История создания винтовых забойных двигателей
Начиная с40-х годов в б. СССР основным техническим средством для бурения нефтяных и газовых скважин являлся многоступенчатый турбобур.
Широкое распространение турбинного способа бурения обеспечило ускоренное разбуривание нефтегазоносных площадей Урало-Поволжья и Западной Сибири и, тем самым, позволило получать высокие темпы роста добычи нефти и газа.
Однако с увеличением средних глубин скважин и по мере совершенствования породоразрушающего инструмента и технологии роторного способа бурения в отечественной нефтяной промышленности с каждым годом росла тенденция отставания проходки за рейс долота – показателя, определяющего технико-экономические показатели бурения.
Несмотря на определенные усовершенствования техники и технологии турбинного бурения показатели работы долот на протяжении ряда лет улучшались весьма незначительно. Хотя в 70-е годы началось разбуривание месторождений Западной Сибири, отличающихся благоприятными условиями бурения (мягкие породы, относительно неглубокие скважины), средняя проходка за рейс по эксплуатационному бурению существенно отставала от аналогичного показателя в нефтяной промышленности США (в 3– 4 раза). Так, в 1981–1982 гг. средняя проходка за долбление в США составила350 м, в то время как в б. СССР этот показатель не превышал 90 м.
Серьезное отставание в проходке за долбление было связано с тем, что в те годы отечественная практика бурения базировалась на высокоскоростном режиме бурения с применением многоступенчатых безредукторных турбобуров, характеристики которых не позволяли получать частоты вращения менее 400–500 об/мин с обеспечением необходимых крутящих моментов и приемлемого уровня давления насосов,и как следствие эффективно использовать революционные усовершенствования шарошечных долот (с прецизионными маслонаполненными опорами и твердосплавным вооружением). В связи с этим перед специалистами и организаторами бурения в нашей стране встал вопрос о создании техники для низкооборотного бурения.
Перед советской нефтяной промышленностью встала дилемма: либо переходить к роторному бурению, либо создать низкооборотный забойный двигатель.
К этому времени в б. СССР имелись определенные успехи роторного бурения глубоких скважин в ряде районов (Северный Кавказ, Западная Украина и др.). Однако технически, экономически и психологически нефтяная промышленность не была готова к развитию роторного бурения. За многие годы государственной поддержки турбинного бурения существенно отстала от мирового уровня техника роторного бурения: не имелось бурильных труб и буровых установок высокого технического уровня.
Переход на роторный способ бурения в основных регионах страны снизил бы темпы развития отрасли, так как промышленность не располагала необходимыми средствами для строительства новых заводов и эксплуатационных баз или закупки за рубежом новых технологий.
Таким образом, определился доминирующий способ бурения на базе низкооборотных забойных двигателей.
Решение проблемы создания забойного гидравлического двигателя с характеристиками, отвечающими требованиям новых конструкций долот, было найдено в переходе от динамических машин, каким являются турбобуры, к объемным.
Первым работоспособным, нашедшим промышленное применение, оказался гидродвигатель, представляющий собой обращенный насос Муано (R. Moineau (1887–1948) – французский инженер, изобретатель одновинтовых гидравлических и пневматических машин), относящийся к планетарно-роторному типу гидромашин.
Работы по созданию опытных образцов винтовых забойных двигателей (ВЗД) начались в США и б. СССР в середине 60-х годов. Американские специалисты фирмы «Smith Tool» разработали ВЗД (на западе их называют РDМ – positive displacement motors) для наклонно направленного бурения как альтернативу турбобурам,а в нашей стране, родине турбинного бурения – они служат техническим средством для привода низкооборотных долот.
Многолетние поисковые научно-исследовательские работы во ВНИИБТ по совершенствованию забойных гидравлических двигателей привели в 1966 г. к появлению предложенного М.Т. Гусманом, С.С. Никомаровым, Н.Д. Деркачем, Ю.В. Захаровым и В.Н. Меньшениным нового типа ВЗД, рабочие органы которого впервые в мировой практике выполнены на базе многозаходного винтового героторного механизма, исполняющего функцию планетарного редуктора. В последующие годы во ВНИИБТ и Пермском филиале Д.Ф. Балденко, М.Т. Гусманом, Ю.В. Захаровым, А.М. Кочневым, С.С. Никомаровым и другими исследователями были созданы основы теории рабочего процесса, конструирования и технологии изготовления, разработана технология бурения винтовыми двигателями.
В результате многолетнего опыта бурения с использованием гидравлических забойных двигателей (турбобуров и ВЗД) сложился комплекс технических требований к современному забойному двигателю.
1. Характеристики двигателя должны обеспечивать:
высокий уровень крутящего момента (3 кН∙м и более для долот диаметром 215–243 мм);
частоту вращения выходного вала в диапазоне100–200 об/мин для шарошечных долот и500–800 об/мин для алмазных долот;
высокий КПД двигателя для эффективного использования гидравлической мощности насосов;
пропорциональную зависимость между расходом бурового раствора и частотой вращения, а также между крутящим моментом и перепадом давления с целью эффективного управления режимом бурения.
2. Рабочие элементы и другие узлы двигателя должны быть износо- и термостойкими, что позволяет использовать буровой раствор любой плотности и вязкости, в том числе с содержанием тампонирующих материалов.
3. Конструктивная компоновка двигателя и проектные запасы прочности его узлов должны обеспечить:
стойкость двигателя, достаточную для стабильной работы с современными шарошечными и алмазными долотами;
возможность искривления корпуса двигателя при наклонно направленном бурении;
возможность установки на корпусе двигателя опорно-центрирующих элементов при проводке наклонно направленных и горизонтальных скважин.
4. Диаметральные и осевые размеры двигателя должны обеспечивать:
-проведение буровых работ долотами различного диаметра, включая малогабаритные;
-эффективную проводку наклонно направленных и горизонтальных скважин;
-использование стандартного ловильного инструмента.
Анализ конструкций и характеристик забойных гидравлических двигателей различного типа показывает, что ни один из них не отвечает в полной мере всем перечисленным требованиям; в большей степени указанным требованиям соответствуют ВЗД с многозаходными рабочими элементами.
Принцип действия ВЗД
Винтовые двигатели относятся к объемным роторным гидравлическим машинам. Согласно теории винтовых роторных гидравлических машин элементами рабочих органов (РО) являются:
1) статор двигателя с полостями, примыкающими по концам к камерам высокого и низкого давления;
2) ротор-винт, носящий название ведущего, через который крутящий момент передается исполнительному механизму;
3) замыкатели-винты, носящие название ведомых, назначение которых уплотнять двигатель, т.е.препятствовать перетеканию жидкости из камеры высокого давления в камеру низкого давления.
В одновинтовых гидромашинах используются механизмы, в которых замыкатель образуется лишь двумя деталями, находящимися в постоянном взаимодействии, – статором и ротором.
Упрощенная схема двигателя показана на рис. 4.8.
При циркуляции жидкости через РО в результате действия перепада давления на роторе двигателя вырабатывается крутящий момент, причем винтовые поверхности РО взаимно замыкаясь, разобщают область высокого давления и область низкого давления. Следовательно, по принципу действия винтовые двигатели аналогичны поршневым, у которых имеется винтообразный поршень, непрерывно перемещающийся в цилиндре вдоль оси двигателя.
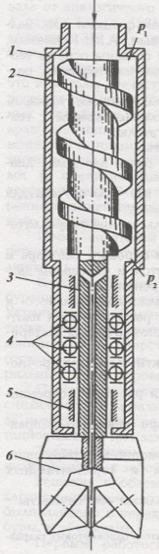
Рис. 1.8.Упрощенная схема двигателя: 1 – корпус,2 – ротор; 3 – вал; 4, 5 подшипники; 6 –долото
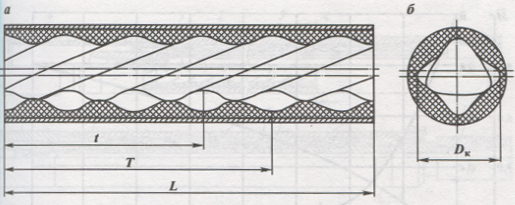
Рис. 1.9. Рабочие органы ВГМ: a – продольный разрез; б – поперечный разрез
Для создания в РО двигателя полостей, теоретически разобщенных от областей высокого и низкого давлений (шлюзов), необходимо и достаточно выполнение четырех условий (рис. 4.9):
1) число зубьев Z1наружного элемента (статора) должно быть на единицу больше числа зубьев Z2 внутреннего элемента (ротора): Z1= Z2+ 1;
2) отношение шагов винтовых поверхностей наружного элемента (статора) O и внутреннего элемента (ротора) t должно быть пропорционально отношению числа зубьев: T/t = Z1/Z2;
3) длина РО L должна быть не менее шага винтовой поверхности наружного элемента: L ≥ T;
4) профили зубьев наружного и внутреннего элементов должны быть взаимоогибаемы и находиться в непрерывном контакте между собой в любой фазе зацепления.
Не нашли, что искали? Воспользуйтесь поиском по сайту:
©2015 - 2025 stydopedia.ru Все материалы защищены законодательством РФ.
|