Расчёт проточной части колеса
2.1Определение основных параметров:
1. Подача колеса
Q1 = Q/k, (2.1.1)
где Q- подача насоса, k- число потоков.
Q1 = 
2. Напор колеса
H1=H/i, (2.1.2)
где Н- напор насоса, i- число ступеней насоса.

3. Коэффициент быстроходности ступени
, (2.1.3)

где n- частота вращения колеса в об/мин.
4. Гидравлический к.п.д. ступени
(2.1.4)
где D1пр- приведенный диаметр колеса (мм), определяемый по формуле:
(2.1.5)


5. Объёмный к.п.д. ступени (учитывающий потери только в переднем уплотнении колеса)
(2.1.6)

Внутренний механический к.п.д. ступени (учитывающий только потери дискового трения) в первом приближении может быть определен :

(2.1.7)
Механический к.п.д. насоса с учетом потерь в сальниках и подшипниках можно принять на (1-3)% меньше, чем ηiм, т.е. ηм=0,911.
6. Общий к.п.д. насоса.
(2.1.8)
=0,858*0,972*0,911=0,759
9. Мощность на валу насоса (кВт)
(2.1.9)

10. Максимальная расчетная мощность на валу насоса ,
=1,3*1,25=1,625кВт (2.1.10)
11. Определение диаметра вала и втулки
(2.1.11)
Выбираем из стандартного ряда размеров d0= 16 мм

Принимаем =22мм (2.1.12)
3.2 Определение основных размеров колеса:
12. Определение размеров входа в колесо.
Расчетная подача насоса:
(2.2.1)
Скорость потока во входном отверстии колеса:
(2.2.2)
Диаметр входного отверстия колеса:
(2.2.3)
Радиус средней точки входной кромки лопасти:
; (2.2.4)
Ширина канала в меридианном сечении на входе колеса:
; (2.2.5)
Меридианная составляющая скорости с учетом стеснения:
1; ; (2.2.6)
Переносная скорость средней точки входной кромки лопасти:
; (2.2.7)
Угол, соответствующий безударному поступлению потока на лопасть:
; (2.2.8)
Принимая , имеем угол наклона лопасти на входе:
(2.2.9)
13. Определение размеров выхода из колеса.
Теоретический напор:
(2.2.10)
Полагая имеем в 1-м приближении значение переносной скорости на выходе:
; (2.2.11)
И радиус наружной окружности колеса:
(2.2.12)
Ширина канала на выходе:
(2.2.13)
Меридианная составляющая абсолютной скорости без учета стеснения:
(2.2.14)
Меридианная составляющая с учетом стеснения:
(2.2.15)

Выходной угол лопасти берут в пределах β2=20-30˚.
; zK=8.
Коэффициент снижения напора из-за конечного числа лопастей:
(2.2.16)
Теоретический напор при бесконечном числе лопастей:
(2.2.17)
Во 2-м приближении
(2.2.18)
; Δ=0,4%. (2.2.19)
Δ=0,93%. (2.2.20)
Δ=0,94%. (2.2.21)
Относительные скорости:
(2.2.22)
(2.2.23)
Получив, таким образом, элементы входа и выхода колеса, строим соответствующие планы скоростей при входе в колесо (рис. 2,а) и выходе из колеса с учетом конечного числа лопастей (рис. 2,б).

Рис. 2(а)
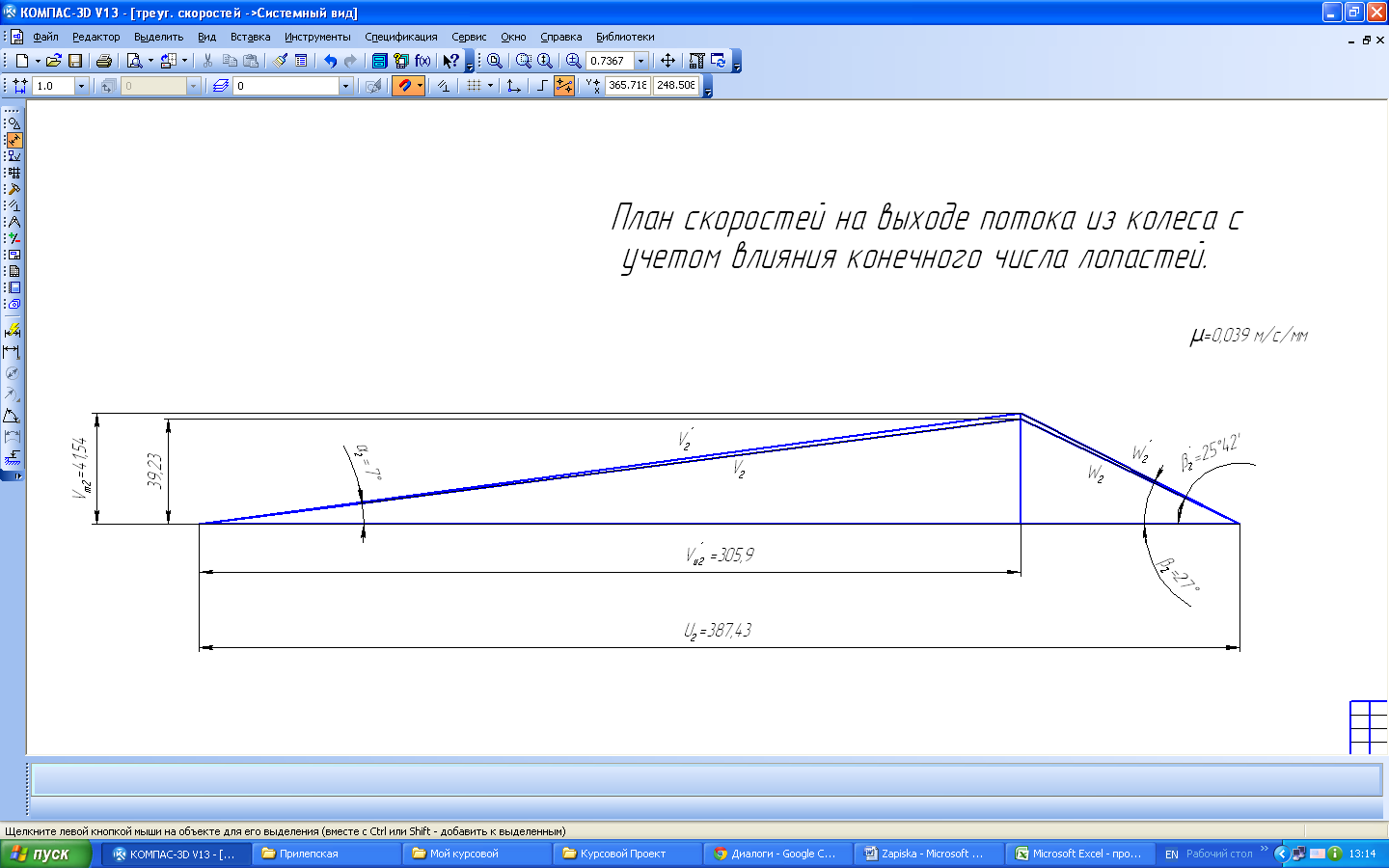
Рис. 2(б)
Профилирование канала колеса в меридианном сечении
Исходным положением профилирования канала в меридианном сечении для получения высоких энергетических и кавитационных качеств колеса является обеспечение плавности изменения скоростей от входного отверстия колеса и до выхода из него. С этой целью задаются графиком изменения скоростей в функции от радиуса r или длины средней линии канала s.
Рабочие колёса с имеют цилиндрические лопасти, расположенные в радиальной части канала. Профилирование канала колеса в меридианном сечении производят в следующей последовательности. На ось вращения OZ (рис. 3) наносим перпендикулярно к ней линию. На расстоянии R2 откладываем отрезок, равный b2.

Рис. 3
Затем наносим линии параллельные оси OZ, отстоящие от последней на расстоянии R1 и R0. Справа строят эпюру скоростей , изменяющейся по радиусу прямолинейно от до . При этом в соответствии с указанным выше принимаем = . Имея для любой точки произвольного радиуса r величину из графика, по уравнению неразрывности получают значение ширины канала
(3.1)
Результаты приведены в таблице 1.
Получив, таким образом, для различных точек ширину канала, проводим окружности с радиусом b/2 касательно к линии АБ. Проводим огибающую к этим окружностям, не доводя до линии R0 . Затем проводим окружность с радиусом R, плавно сопрягающуюся с линией R0. В дальнейшем окружности с радиусами b/2 проводим касательно к дуге окружности радиуса R.
Таким же образом проводим справа (по контуру, соответствующему ведущему диску) огибающую до сопряжения с линией OZ. В случае необходимости контуры канала корректируют по конструктивно-технологическим соображениям и определяют окончательное положение средней линии тока.
Таблица 1.
Не нашли, что искали? Воспользуйтесь поиском по сайту:
©2015 - 2025 stydopedia.ru Все материалы защищены законодательством РФ.
|