Балансировка коленчатого вала.
Простейшая, но вполне удовлетворительная балансировка коленчатого вала производится по эмпирической формуле:
Х = А(0,45 ÷ 0,6) + В(0,45÷0,6) - В,
Где, А = вес поршня + вес пальца + вес поршневых колец + вес стопорных колец + вес шайб + вес подшипника;
В — 0,336 от веса головки шатуна (рис. 50).
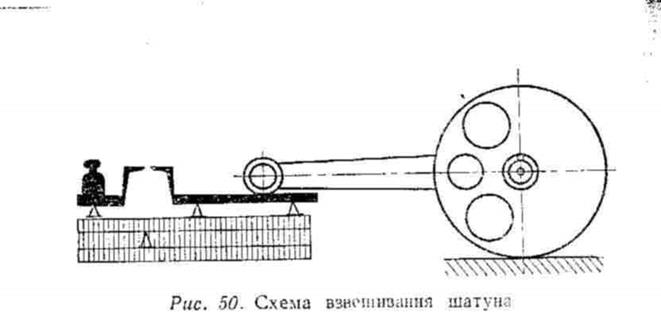
Производя простейшие вычисления, получим чистый вес балансировочного груза X. Например:
Вес поршня =140 г
Вес пальца = 30 г
Вес колец =5 г;
Вес стопорных колец =1 г;
В = 168 : 0,336 = 50 г;
X = 176 • 0,5 + 50 • 0,5 — 50 = 53 г.
Получив нужный балансировочный вес, установить коленчатый вал на балансировочные ножи или призмы, или во вращающиеся центры. Подвесить балансировочный груз
к головке шатуна (рис. 51).
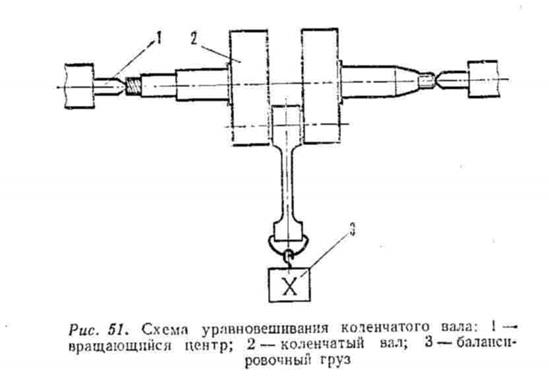
Путем снятия металла (высверливания) из щек коленчатого вала у нижней головки шатуна добиться статического равновесия. Коэффициент балансировки К = (0,45÷0,6) выбирается в зависимости от ожидаемых под нагрузкой оборотов двигателя). Например, для оборотов коленчатого вала 6000—6500 об/мин этот коэффициент берется равным 0,5.
Чем выше обороты коленчатого вала, тем коэффициент балансировки берется большим (для n =8000 об/мин, К = (0,55 — 0,57).
Произведя один раз статическую балансировку коленчатого вала на картере двигателя, записать балансировочный вес, он же вес поршня в сборе. При последующих сменах поршня его вес подгонять под балансировочный вес коленчатого вала.
Выносной маховик балансируется отдельно, а общая балансировка проверяется в сборе. Надев выносной маховик на конус шейки коленчатого вала и хорошо затянув гайку крепления, проверить балансировку. При неправильной балансировке двигателя появляется вибрация.
КАРТЕР ДВИГАТЕЛЯ
Картер двигателя должен быть целым (без трещин, раковин, обрывов ушек крепления, вмятин) с соосными и неразбитыми отверстиями под подшипники валов, с хорошими резьбами под болты затяжки и крепления деталей, с ровными, притертыми плоскостями разъема половинок и горловины.
Уплотнительные прокладки картера рекомендуется смазать тугоплавким солидолом, смазкой I—13 и др. Не оправдано применение для этой цели нитрокраски и бакелитового
лака, так как при разборках спортивного двигателя очистка и подготовка плоскостей разъёма доставляет много хлопот.
Наружную поверхность картера двигателя желательно покрасить в черный цвет для лучшего охлаждения. Все стенки кривошипной камеры полируются, острые кромки
закругляются.
Перепускные каналы. Рабочая смесь, попав через впускное окно в картер двигателя после предварительного сжатия, направляется в перепускные каналы.
На спортивных высокофорсированных двигателях последних лет широкое применение нашла новая схема трех-четырех - и пятиканальной продувки.
Скорость газа, проходящего через перепускные каналы, очень высока, и важно, чтобы продувочные каналы оказывали минимальное сопротивление по всей длине.
Основное правило для любого перепускного канала — сечение входа в перепускной канал должно быть примерно в два раза больше, чем сечение выхода из перепускного канала (рис. 52).
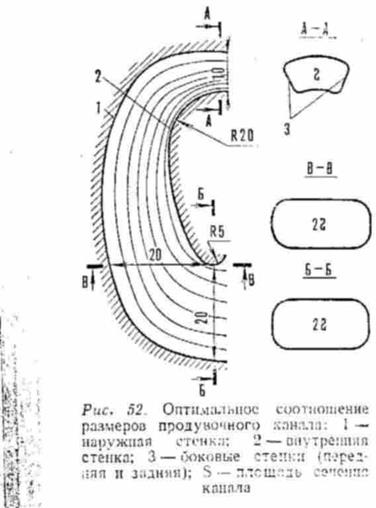
Все радиусы закруглений в перепускных каналах желательно делать плавными, особенно на выходе в цилиндр. Внутренний радиус поворота колен устанавливается примерно равным 20 мм, это лучший минимальный радиус. Наружный радиус колен делают равным 80 % от суммы внутреннего радиуса и высоты сечения выхода. Это обеспечивает минимальное сопротивление потока при изменении направления. В нижнем колене сечение входа равно сечению выхода, но можно делать большим сечение входа.
Полное совпадение продувочных каналов в цилиндре и картере обязательно. Нужно также следить, чтобы продувочные каналы были на одном уровне с наружным диаметром щек коленчатого вала.
Если каналы в картере стандартного исполнения оказываются ниже щек коленчатого вала, то, во избежание нежелательных завихрений, каналы нужно поднять до нужного уровня путем наварки или заполнения эпоксидной смолой с алюминиевым порошком или зачеканки медью, свинцом. Для гарантии накладки нужно закрепить дополнительно двумя-тремя винтами М3 х 0,5 к картеру. Все тщательно зачистить и заполировать.
Большое влияние на работу двигателя, на его мощность оказывает направление потока смеси на выходе из перепускного канала.
При продувке цилиндра рабочей смесью продувочный поток должен отвечать двум основным требованиям:
а) максимально очищать цилиндр от остатков продуктов сгорания;
б) обеспечивать минимальные потери свежего заряда в выпускную систему.
Картина продувки выглядит следующим образом: продувочные струи из продувочных каналов входят в цилиндр и направляются обычно в сторону, противоположную выпускному окну, соединяются между собой, образуя восходящий поток вдоль задней стенки цилиндра, продувочный поток достигает головки цилиндра, протекает вдоль
нее и опускается по передней стенке цилиндра к выпускному окну. Для хорошей очистки цилиндра от отработавших газов необходимо, чтобы восходящая часть потока составляла половину цилиндра, тогда его нисходящая часть будет продувать вторую половину. Но такую картину продувки получить очень трудно, так как продувочный поток при различных оборотах двигателя имеет различные плотности и скорости по своему сечению. Максимальные плотность и скорость продувочного потока имеются у задней стенки цилиндра и снижаются в слоях, лежащих ближе к центру цилиндра. В большинстве случаев при плохой продувке в центральной части цилиндра остаются не продутые, застойные и вихревые зоны. Из-за них часто наблюдаются прогары поршня и недобор максимальной мощности.
При двухканальной продувке получить правильный восходящий поток довольно трудно. Даже небольшие погрешности в геометрии каналов сразу же отражаются на правильности продувки. Продувочная струя должна быть компактной и обладать достаточной энергией для того, чтобы вытеснить отработавшие газы и не смешаться с ними. Поэтому, что очень важно, гидравлические потери в продувочных каналах должны быть сведены к минимуму.
Важное значение имеют радиусы каналов, особенно у внутренней и наружных стенок. С этой целью на многих двигателях выполнена отдаленная продувка. Для получения правильного восходящего потока в последнее время с большим успехом изготовляются цилиндры с 3- и 4-канальной продувкой. Продувочные струи этих каналов отжимают продувочный поток от задней стенки цилиндра, стабилизируют его, улучшают очистку центральных не продутых зон. Погрешности основных каналов выравниваются, продувка цилиндров улучшается, как следствие, повышается мощность двигателя.
Дополнительные продувочные каналы располагаются на задней стенке цилиндра со стороны впускного канала. Их размещение в цилиндре связано с определенными конструктивными изменениями.
У некоторых моделей мотоциклов поступление продувочной смеси в третий канал производится через отверстие в поршне, ниже поршневого кольца. Дополнительный
канал может быть выполнен на рабочей поверхности цилиндра в виде углубления клинообразной формы (ИЖ - «Юпитер»). В этом случае впускной канал смещен книзу,
юбка поршня удлинена. Третий и четвертый каналы можно выводить рядом с основными каналами, они должны огибать впускной канал и выходить на заднюю стенку цилиндра.
Основным правилом здесь является отдаление струи продуваемой смеси от выпускного окна, чтобы утечки были наименьшими, образование правильного восходящего потока (петли), собранность его, нерастекаемость и неомывание задней стенки цилиндра. И самое главное — полное вытеснение отработавших газов из цилиндра и полное
заполнение цилиндра свежей рабочей смесью.
Струя свежей смеси должна иметь возможно большее сечение и только тогда она не будет смешиваться с отработавшими газами, она должна быть компактной и правильно направленной.
Струя свежей смеси не должна встречать никакого препятствия, которое тормозило бы или отклоняло ее. В противном случае компактная струя разбивается. Хорошо
помогает дополнительная струя из третьего продувочного канала (а при 4-х и 5-ти еще лучше). Для получения компактной струн в продувочном канале колено перед продувочным окном должно быть тщательно изготовлено. Важнейшей частью канала является отводящая наружная стенка.
Направление струи после отклонения от стенки должно быть как можно более перпендикулярным по отношению к ней, и при входе в цилиндр должна быть еще небольшая направляющая часть, иначе у верхней кромки продувочного окна поток слегка расширяется. Обе боковые стенки препятствуют растеканию струи при ее повороте в колене.
Отводящая наружная стенка сама по себе также является препятствием, которое вызывает расширение потока. Если желаемое направление струи не перпендикулярно
к наружной стенке, то одна из боковых стенок должна ещё немного загибаться.
Задняя боковая стенка должна расширять струю в цилиндре, а передняя боковая стенка должна препятствовать расширению струи и движению ее к выпускному окну, дополнительно вытеснять струю в желаемом направлении.
На большинстве серийных двигателей угол выхода продувки равен 15 градусам. Лучшие результаты достигнуты при постепенном развороте продувки па выходе, начиная с 0 градусов у передней боковой стенки до 25 градусов у задней стенки продувочного окна.
Высота продувочного окна обычно берется равной примерно 20 – 25% хода поршня, выбирается в зависимости от первичной степени сжатии и требуемых максимальных
оборотов двигателя.
Чем выше давление продувки, тем больше высота продувочного окна. Оптимальная высота продувочного окна обычно подбирается на испытательном стенде. Ширина
перепускного окна берется примерно в два раза больше его высоты. Лучшая форма перепускного канала и окна— эллипсовидная с плавными радиусами.
Важным фактором, влияющим на работу двигателя, является использование полного сечения продувочного окна. С этой целью в цилиндре с продувкой по гильзе нижнюю кромку окна необходимо опустить на 2—4 мм ниже мертвой точки поршня с тем, чтобы окно работало полным своим сечением (рис. 53,а). В некоторой степени в этом случае облегчается работа верхнего поршневого кольца, так как нет удара о кромку окна в н. м. т.
Наиболее распространенные углы выхода продувки для малых классов мотоциклов приведены на рис. 53, б.
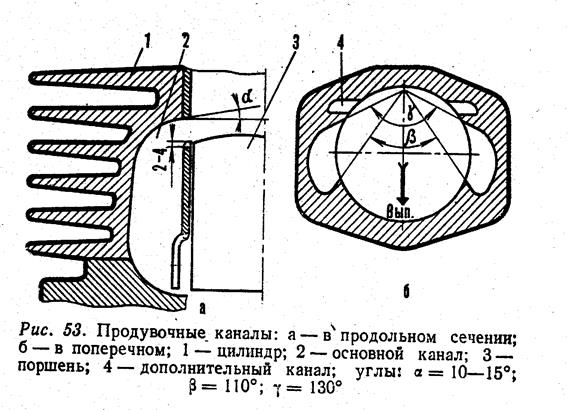
Для больших классов они могут быть другими. При работе двигателя происходит отклонение и расширение потоков к выпускному окну, так что всеми силами их нужно направить в противоположную от выпускного окна сторону.
Очень важно симметрично направить потоки, чтобы они могли опереться один на другой и образовать правильную петлю продувки.
При 3-канальной продувке угол выхода из третьего канала 45° для короткоходных двигателей и 60º для длинноходовых. Ширина третьего канала такая же, как и у любого из двух продувочных. При исполнении 4- и 5- канальной продувки дополнительные каналы обычно имеют небольшую ширину. Фаза открытия дополнительных каналов может быть равна фазе открытия основных, но лучше, когда их открытие немного
запаздывает на 1—2 мм. Углы выхода из дополнительных каналов подбираются с таким расчетом, чтобы выводящие из них потоки газа могли очистить непродуваемую центральную часть цилиндра (рис. 54). Это улучшает продувку цилиндра и увеличивает наполнение его свежей рабочей смесью.

ГОЛОВКА ЦИЛИНДРА
Конструкция головки цилиндров сильно влияет на работу двигателя, его мощность, охлаждение. Она должна иметь герметичную камеру сгорания, большую площадь охлаждения, выраженную в сильно развитом оребрении, хорошо отводить тепло от камеры сгорания, должна быть достаточно жесткой и легкой, не деформироваться при нагревах. Головка обрабатывается под посадочный буртик, нарезается полная резьба под свечи. Головка по посадочному буртику притирается к посадочной плоскости цилиндра.
Для уплотнения между цилиндром и головкой на буртик устанавливается прокладка из отожженной меди или алюминия толщиной 0,4—0,5 мм. Широкая расстановка шпилек часто не обеспечивает хорошей затяжки головки и ее герметичности по посадочному месту. Для достижения хорошей равномерной затяжки головки рекомендуется устанавливать одну-две дополнительные шпильки. В первую очередь—со стороны выпуска, так как при нагреве головки чаще всего пропуски газов бывают именно в этом месте (рис. 55).

Для лучшей передачи тепла от цилиндра к головке посадочный буртик на гильзе цилиндра и выточка под него в головке делаются обычно шириной 5—6 мм, а иногда до 10 мм, но обязательно с последующей притиркой и установкой прокладки.
Для хорошего охлаждения и отвода тепла от камеры сгорания и цилиндра головка выполняется из алюминиевого сплава с большим и хорошо развитым оребрением. Обычно размер головки больше размера ребер цилиндра. Ребра охлаждения на головке цилиндра располагаются веерообразно (см. рис. 55) для того, чтобы иметь направленный
поток холодного воздуха для охлаждения свечей и задних ребер головки.
Толщина металла в головке цилиндра над камерой сгорания должна быть не менее 10-12 мм. Для лучшего охлаждения головку цилиндра так же, как и весь двигатель, желательно покрасить в черный цвет (можно нитрокраской).
Различные формы камер сгорания позволяют доводить геометрическую степень сжатия до 15, не опасаясь детонации на бензине с октановым числом 90—98.
Чтобы головка цилиндра не коробилась при работе в напряженных тепловых режимах, в нижней части ее делаются ребра жесткости (рис. 56), а также предусматривается достаточная масса металла вокруг камеры сгорания.
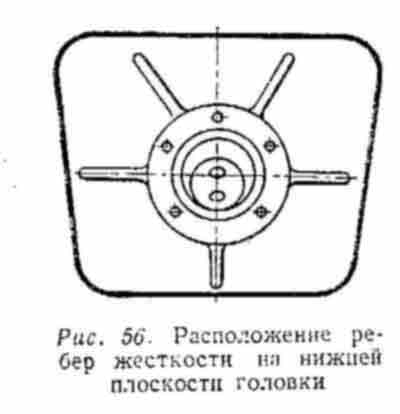
Подбор наилучшей камеры сгорания для любого двигателя лучше всего производить на тормозном испытательном стенде.
На высокофорсированных кроссовых и других двигателях малых рабочих объемов в последнее время широкое применение получила камера сгорания со смещенной сферой — «жокейская шапочка» (рис. 57,а).
Для двигателей классов 250 и выше лучшие результаты даёт форма камеры сгорания полумесяц» (рис. 57,а) с небольшим завихрительным козырьком со стороны выпуска.
Диаметр и высота смещенной сферы камеры сгорания подбираются экспериментально.
Чаще всего диаметр смещенной сферы камеры сгорания равен 2/3 диаметра цилиндра, а при «полумесяце» 3/5 диаметра цилиндра.
Для меньшего нагарообразования внутренняя поверхность камеры сгорания должна быть чисто обработана и отполирована. Все острые кромки в камере сгорания следует скруглить радусом 1—3 мм.

ЦИЛИНДР
Для снижения веса мотоцикла, хорошего отвода тепла, а также легкости обработки цилиндр лучше всего изготовлять из алюминиевого сплава. Для охлаждения цилиндра должно быть сильно развитее оребрение его.
Задние ребра охлаждения делают больше, чем передние; расстояние между ними 12—15 мм. Толщина ребер охлаждения обычно 3—5 мм.
Для установки впускного и выпускного патрубков на рубашке цилиндра предусматриваются специальные приливы, максимальная высота которых 20 мм, а по длине и ширине они равны фланцам крепления впускного и выпускного патрубков плюс 5 мм на каждую сторону для удобства монтажа и демонтажа.
После литья плоскости крепления патрубков фрезеруются, производится разметка под шпильки крепления и окна, сверлятся 4—6 отверстий, и нарезается резьба под установку шпилек крепления патрубка. Размер и диаметр шпилек крепления патрубков выбирается в зависимости от размеров цилиндра и фланцев крепления. Чаще всего применяются шпильки длиной 20—30 мм с резьбой М6 X 1, но возможны и варианты шпилек М5Х0,8, М8 Х1, М8 X 1,25.
При расточке отверстия под гильзу следует учитывать, что запрессовывать гильзу нужно с определенным натягом, который выбирается в зависимости от линейного расширения материала цилиндра и его конструкции. Обычно натяг под запрессовку гильзы для алюминиевых цилиндров берется разным 0,8—0.15 мм от наружного диаметра гильзы.
Больший натяг делать не нужно, так как рубашка цилиндра может лопнуть или деформировать гильзу.
Окончив обработку цилиндра (расточку, подрезку, разметку, фрезеровку, подгонку, распиловку, зачистку), нужно обязательно произвести еще раз контрольный осмотр,
проверку всех размеров и совпадение с гильзой каналов, окон. Это делается при помощи отпечатков окон на тонкой бумаге и совмещения их с окнами в цилиндре. Убедившись в правильности всех размеров, можно приступать к запрессовке гильзы (гильза тоже должна быть полностью готова и окончательно проверена).
Гильза предварительно шлифуется, распиливаются окна в гильзе, затем вставляется в цилиндр и подгоняются все сопряжения каналов — цилиндр— гильза. Это очень удобно, так как можно вынимать гильзу, допиливать до нужного размера, Снова вставлять в цилиндр, проверять совпадение окон гильзы с каналами цилиндра. После окончательной подгонки всех сопряжении гильза меднится на нужный натяг и вставляется в нагретый цилиндр.
В результате лучшая подгонка и теплопередача от гильзы к цилиндру.
Не нашли, что искали? Воспользуйтесь поиском по сайту:
©2015 - 2024 stydopedia.ru Все материалы защищены законодательством РФ.
|