|
ВОССТАНОВЛЕНИЕ ДЕТАЛЕЙ СВАРКОЙ И НАПЛАВКОЙ
Общие сведения
На сварку и наплавку приходится от 40 до 80% всех восстановленных деталей. Такое широкое распространение этих способов обусловлено: простотой технологического процесса и применяемого оборудования; возможностью восстановления деталей из любых металлов и сплавов; высокой производительностью и низкой себестоимостью; получением на рабочих поверхностях деталей наращиваемых слоев практически любой толщины и химического состава (антифрикционные, кислотно-стойкие, жаропрочные и т.д.).
Нагрев до температуры плавления материалов, участвующих при сварке и наплавке, приводит к возникновению вредных процессов, которые оказывают негативное влияние на качество восстанавливаемых деталей. К ним относятся металлургические процессы, структурные изменения, образование внутренних напряжений и деформаций в основном металле деталей.
В процессе сварки и наплавки происходит окисление металла, выгорание легирующих элементов, насыщение наплавленного металла азотом и водородом, разбрызгивание металла.
Соединение наплавленного металла с кислородом воздуха является причиной его окисления и выгорания легирующих элементов (углерода, марганца, кремния и др.). Кроме этого, из воздуха в наплавленный металл проникает азот, который является источником снижения его пластичности и повышения предела прочности. Для защиты от этих отрицательных явлений при сварке и наплавке используют электродные обмазки, флюсы, которые при плавлении образуют шлак, предохраняющий возможный контакт металла с окружающей средой. С этой же целью применяют и защитные газы.
Влага, которая всегда содержится в гигроскопичных электродных обмазках и флюсах, является источником насыщения металла водородом, который способствует повышению пористости наплавленного металла и возникновению в нем значительных внутренних напряжений. Исключить воздействие влаги можно тщательной сушкой электродных обмазок и флюсов.
При сварке и наплавке выделяются углекислый и угарный газы, которые бурно расширяются и являются источником разбрызгивания жидкого металла. Эти потери металла можно уменьшить, если использовать электроды с пониженным содержанием углерода, тщательно очищать детали от окислов или вводить в состав электродных обмазок и флюсов вещества, содержащие раскисляющие элементы (марганец, кремний).
Неравномерный нагрев детали в околошовной зоне (зоне термического влияния) приводит к структурным изменениям в основном металле детали. Механические свойства металла в этой зоне снижаются. Размеры зоны термического влияния зависят от химического состава свариваемого металла, способа сварки и ее режима. Размеры зоны термического влияния для газовой сварки составляют 25... 30 мм, а при электродуговой сварке — 3...5 мм. Увеличение сварочного тока и мощности сварочной горелки приводит к расширению зоны термического влияния, а скорости сварки (выбором рационального режима) — к уменьшению.
Из-за неравномерного (местного) нагрева и структурных превращений, происходящих в зоне термического влияния, возникают внутренние напряжения деформации в деталях. Если внутренние Напряжения превышают предел текучести материала детали, то возникают деформации. Они могут быть значительно снижены путем нагрева деталей перед сваркой и медленного охлаждения после сварки, применения специальных приемов сварки и наплавки. В технологический процесс восстановления деталей сваркой и наплавкой входят следующие операции — это подготовка деталей к сварке или наплавке; выполнение сварочных или наплавочных работ; обработка деталей после выполнения сварочных или наплавочных работ. Порядок выполнения сварочных и наплавочных работ зависит от выбранного способа.
Сварка и наплавка
Ручная сварка и наплавка плавящимися электродами (рис. 13.1). Параметры режима — это сила тока, напряжение и скорость наплавки. Для получения минимальной глубины проплавления основного металла электрод наклоняют в сторону, обратную направлению наплавки.
Общие потери при наплавке покрытыми электродами с учетом потерь на угар, разбрызгивание и огарки составляют до 30%.
Напряжение дуги составляет 22...40 В. Диаметр электрода равен (табл. 13.1) dM — 0,56 + (1...2) мм. Длина дуги не должна превышать диаметра электрода.
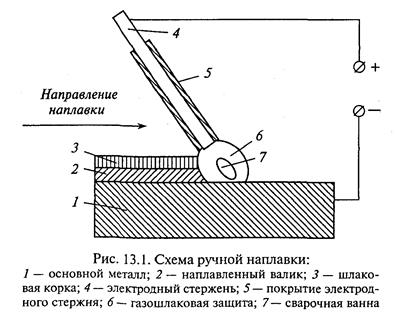
Таблица 13.1
Зависимость коэффициента k от толщины материала изделия
5, мм
| 1...2
| 3...4
| 5. ..6
| k
| 25. ..30
| 30. ..45
| 45. ..60
| 4л
| 2...3
| 3...4
| 4... 5
|
Ручная сварка и наплавка используются для устранения трещин, вмятин, пробоин, изломов и т. д. В табл. 13.2 приведены способы подготовки поврежденного участка изделия.
Для уменьшения вредного последствия рассмотренных в разд. 13.1 явлений сварку и наплавку ведут электродами с обмазкой — тонкой или толстой.
Малоответственные детали сваривают электродами с тонкой обмазкой, которые изготовляют из проволоки Св-08. Проволоку рубят на куски длиной 300...500 мм и покрывают обмазкой, состоящей из 3/4 мела и 1/4 жидкого стекла, разведенного в воде д0 сметанообразного состояния.
Определяющим при выборе толстых электродов является процесс — сварка или наплавка. Для сварки используют электроды обозначаемые буквой «Э» с двузначной цифрой через дефис, например Э-42. Цифра показывает прочность сварочного шва на разрыв.
Наплавочные электроды обозначают двумя буквами «ЭН» ц цифрами, которые показывают гарантированную твердость наплавленного данным электродом слоя.
Каждому типу электрода соответствует несколько марок составов обмазок. По входящим в них веществам все электродные покрытия разделяют на следующие группы: рудно-кислое — Р, рути-ловое — Т, фтористо-кальциевое — Ф, органическое — О и др. Наиболее распространены рудно-кислое (ОММ-5, ЦМ-7, ЦМ-8 и др.), рутиловое (АНО-1, АНО-3, АНО-4, АНО-12, ОЗС-3, ОЗС-4, ОЗС-6 и др.) и фтористо-кальциевое покрытия (УОНИ-13/45, УОНИ-13/55, ЦЛ-9, ОЗС-2, АНО-7 и др).
Таблица 13.2
Способы подготовки деталей перед сваркой
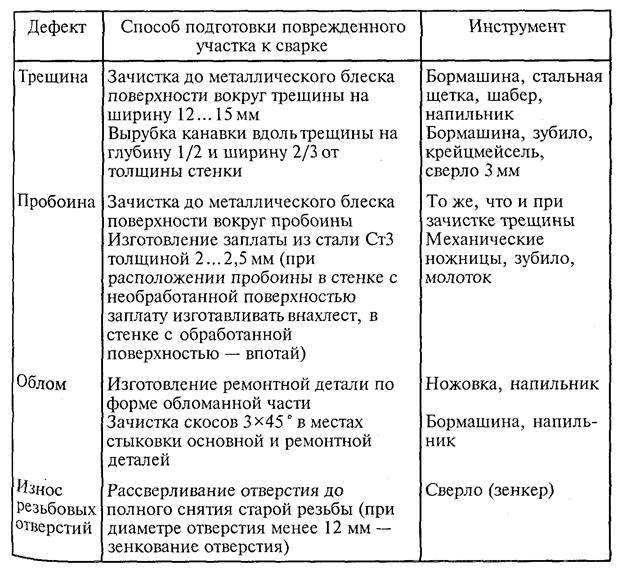
Газовая сварка и наплавка. Сущность процесса — это расплавление свариваемого и присадочного металла пламенем, которое образуется при сгорании горючего газа в смеси с кислородом. В качестве горючего газа используют ацетилен, что позволяет обеспечить температуру пламени 3100... 3300 °С. Ацетилен получают с помощью ацетиленовых генераторов, а кислород сохраняют и транспортируют в стальных баллонах вместимостью 40 л под давлением 15 МПа.
Сварку и наплавку осуществляют сварочными горелками. Мощность пламени характеризуется массовым расходом ацетилена, зависящим от номера наконечника горелки (табл. 13.3). Расход ацетилена можно определить по формуле
А = SR',
где S — толщина детали, мм;
R' — коэффициент, характеризующий удельный расход ацетилена на 1 мм толщины детали, м3/(ч-мм) (для чугуна R' — О,И...0,14; для стали — 0,10...0,12; для латуни — 0,12...0,13; для алюминия — 0,06...0,10).
Расход кислорода на 10...20% больше, чем ацетилена.
При ручной сварке пламя направляют на свариваемые кромки так, чтобы они находились в восстановительной зоне на расстоянии 2... 6 мм от конца ядра. Конец присадочной проволоки также держат в восстановительной зоне или в сварочной ванне.
Угол наклона ее мундштука горелки к поверхности свариваемого металла зависит:
от толщины соединяемых кромок изделия. Углы наклона мундштука горелки в зависимости от толщины металла при сварке низкоуглеродистой стали приведены в табл. 13.4;
17П
Таблица 13.3
Мундштуки наконечников горелок
Номер наконечника
| Расход ацетилена,
ДМ3/Ч
| Диаметр канала сопла, мм
|
|
| 1,0
|
|
| 1,3
|
|
| 1,6
|
|
| 2,0
|
|
| 2,5
|
|
| 3,0
| 7 '
|
| 3,5
|
Таблица 13.4
Угол наклона мундштука горелки в зависимости от толщины свариваемого материала
Толщина материала, мм
| До1
| 1...3
| 3...5
| 5... 7
| 7. ..10
| 10. ..12
| 12. ..15
| Свыше
| Угол наклона, град.
|
|
|
|
|
|
|
|
|
от теплопроводности металла (чем толще металл и чем больше его теплопроводность, тем угол наклона мундштука горелки должен быть больше, что способствует более концентрированному нагреву металла вследствие подведения большего количества теплоты).
Существуют два основных способа газовой сварки.
Правый (рис. 13.2, а). Процесс сварки ведется слева направо, горелка перемещается впереди присадочного прутка, а пламя направлено на формирующийся шов. В результате происходит хорошая защита сварочной ванны от воздействия атмосферного воздуха и замедленное охлаждение сварного шва. Такой способ позволяет получить швы высокого качества. Применяют при сварке металла толщиной более 5 мм. Пламя горелки ограничено с двух сторон кромками изделия, а позади — наплавленным валиком, что значительно уменьшает рассеивание теплоты и повышает степень ее Использования. Этим способом легче сваривать потолочные швы, так как в этом случае газовый поток пламени направлен непосред-ственно на шов и тем самым препятствует вытеканию металла из сварочной ванны.
Левый (рис. 13.2, б). Процесс сварки выполняют справа налево, горелка перемещается за присадочным прутком, а пламя направляется на несваренные кромки и подогревает их, подготавливая к сварке. Пламя свободно растекается по поверхности металла что снижает опасность его пережога. Способ позволяет получить внешний вид шва лучше, так как сварщик отчетливо видит шов ц может получить его равномерным по высоте и ширине, что особенно важно при сварке тонких листов. Этим способом осуществляют сварку: вертикальных швов снизу вверх; на вертикальных поверхностях горизонтальными швами выполняют сварку, направляя пламя горелки на заваренный шов.
Для получения сварного шва с высокими механическими свойствами необходимо качественно произвести подготовку свариваемых кромок, которая состоит в очистке их от масла, окалины и других загрязнений на ширину 20...30 мм с каждой стороны шва; разделку под сварку, которая зависит от типа сварного соединения; прихватки короткими швами, длина, количество и расстояние между ними зависит от толщины металла, длины и конфигурации шва.
При толщине металла до 6... 8 мм применяют однослойные швы, до 10 мм — двухслойные, более 10 мм — трехслойные и более. Перед наложением очередного слоя поверхность предыдущего слоя необходимо хорошо очистить металлической щеткой. Сварку выполняют короткими участками, стыки валиков в слоях не должны совпадать. При однослойной сварке зона нагрева больше, чем при многослойной. При наплавке очередного слоя проводят отжиг нижележащих слоев.
Диаметр присадочной проволоки при сварке левым способом металла толщиной до 15 мм равен d ~ S/2 + 1, где S — толщина свариваемой стали (мм), при правом способе — половине толщины свариваемого металла. При сварке металла толщиной более 15 мм применяют проволоку диаметром 6...8 мм.
После сварки, чтобы металл приобрел достаточную пластичность и мелкозернистую структуру, необходимо провести проковку металла шва в горячем состоянии и последующую нормализацию при температуре 800...900"С.
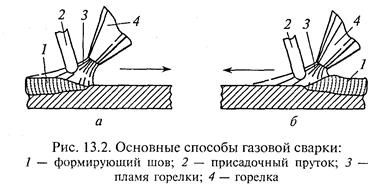
Дуговая наплавка под флюсом. Способ широко применяется для восстановления цилиндрических и плоских поверхностей деталей. Это механизированный способ наплавки, при котором совмещены два основных движения электрода — это его подача по мере оплавления к детали и перемещение вдоль сварочного шва.
Сущность способа наплавки под флюсом (рис. 13.3) заключается в том, что в зону горения дуги автоматически подаются сыпучий флюс и электродная проволока. Под действием высокой температуры образуется газовый пузырь, в котором существует дуга, расплавляющая металл. Часть флюса плавится, образуя вокруг дуги эластичную оболочку из жидкого флюса, которая защищает расплавленный металл от окисления, уменьшает разбрызгивание и угар. При кристаллизации расплавленного металла образуется сварочный шов.
Преимущества способа:
возможность получения покрытия заданного состава, т. е. легирования металла через проволоку и флюс и равномерного по химическому составу и свойствам;
защита сварочной дуги и ванны жидкого металла от вредного влияния кислорода и азота воздуха;
выделение растворенных газов и шлаковых включений из сварочной ванны в результате медленной кристаллизации жидкого металла под флюсом;
возможность использования повышенных сварочных токов, которые позволяют увеличить скорость сварки, что способствует повышению производительности труда в 6...8 раз;
экономичность в отношении расхода электроэнергии и электродного металла;
отсутствие разбрызгивания металла благодаря статическому давлению флюса; возможность получения слоя наплавленного металла большой толщины (1,5 ...5 мм и более);
независимость качества наплавленного металла от квалификации исполнителя;
лучшие условия труда сварщиков ввиду отсутствия ультрафиолетового излучения; возможность автоматизации технологического процесса.
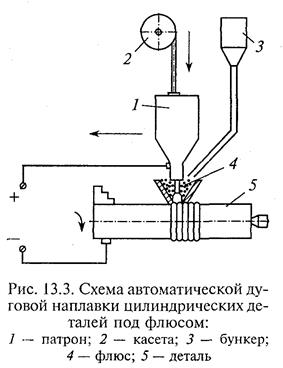
Недостатки способа:
значительныи нагрев детали;
невозможность наплавки в верхнем положении шва и деталей диаметром менее 40 мм
При наплавке могут возникнуть дефекты: неравномерность ширины и высоты наплавленного валика из-за износа мундштука или подающих роликов, чрезмерного вылета электрода; наплыв металла вследствие чрезмерной силы сварочного тока или недостаточного смещения электродов от зенита; поры в наплавленном металле из-за повышенной влажности флюса (его необходимо просушить в течение 1... 1,5 ч при температуре 250...300°С).
В ремонтном производстве наплавку под флюсом применяют для восстановления шеек коленчатых валов, шлицевых поверхностей на различных валах и других деталей автомобиля.
Наплавка в среде углекислого газа. Этот способ восстановления деталей отличается от наплавки под флюсом тем, что в качестве защитной среды используется углекислый газ.
Сущность способа наплавки в среде углекислого газа (рис. 13.5) заключается в том, что электродная проволока из кассеты непрерывно подается в зону сварки. Ток к электродной проволоке подводится через мундштук и наконечник, расположенные внутри газоэлектрической горелки. При наплавке металл электрода и детали перемешивается. В зону горения дуги под давлением 0,05...0,2 МПа по трубке подается углекислый газ, который, вытесняя воздух, защищает расплавленный металл от вредного действия кислорода и азота воздуха.
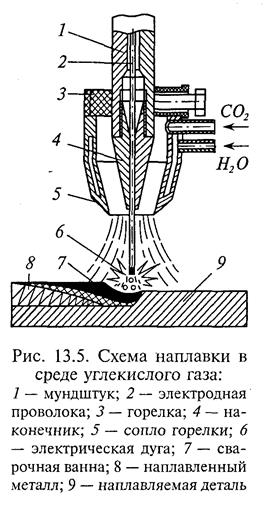
При наплавке используют токарный станок, в патроне которого устанавливают деталь 8, на суппорте крепят наплавочный аппарат 2 (рис. 13.6). Углекислый газ из баллона 7 подается в зону горения. При выходе из баллона 7 газ резко расширяется и переохлаждается. Для подогрева его пропускают через электрический подогреватель 6. Содержащуюся в углекислом газе воду удаляют с помощью осушителя 5, который представляет собой патрон, наполненный обезвоженным медным купоросом или силикагелем. Давление газа понижают с помощью кислородного редуктора 4, а расход его контролируют расходомером 3.
К достоинствам способа относятся — меньший нагрев деталей; возможность наплавки при любом пространственном положении детали; более высокую по площади покрытия производительность процесса (на 20... 30 %); возможность наплавки деталей диаметром менее 40 мм; отсутствие трудоемкой операции по отделению шлаковой корки, а к недостаткам — повышенное разбрызгивание металла (5... 10%), необходимость применения легированной проволоки для получения наплавленного металла с требуемыми свойствами, открытое световое излучение дуги.
Для наплавки применяют следующее оборудование: наплавочные головки АБС, А-384, А-409, А-580, ОКС-1252М; источники питания ВС-200, ВСУ-300, ВС-400, ПСГ-350, АЗД-7,5/30; подогреватели газа; осушитель, заполненный силикагелем КСМ крупностью 2,8—7 мм; редукторы-расходомеры ДРЗ-1-5-7 или рота-Метры РС-3, РС-ЗА, РКС-65, или кислородный редуктор РК-53Б.
При наплавке используют материалы: электродную проволоку Св-12ГС, Св-0,8ГС, Св-0,8Г2С, Св-12Х13, Св-06Х19Н9Т, Св-18ХМА, Нп-ЗОХГСА; порошковую проволоку ПП-Р18Т, ПП-Р19Т, ПП-4Х28Г и др.
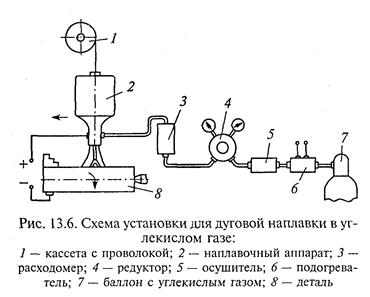
Режимы наплавки, выполняемой на цилиндрических деталях, приведены в табл. 13.7.
Таблица 13.5
Режим наплавки цилиндрических поверхностей
Диаметр детали, мм
| Сила тока, А
| Скорость, м/ч
| Смещение электрода е, мм
|
подачи проволоки
| наплавки
|
40. ..50
| 110. ..130
| 70. ..100
| 14. ..18
| 4... 5
| 60. ..70
| 170. ..180
| 70. ..120
| 20. ..24
| 5. ..6
| 80. ..90
| 170. ..200
| 120. ..150
| 20. ..24
| 6. ..7
| 90. ..100
| 170. ..200
| 120. ..150
| 20. ..24
| 7... 8
|
Таблица 13.6
Основные параметры наплавки плоских поверхностей
Износ, мм
| Сила тока, А
| Проволока
|
Скорость подачи, м/ч
| Диаметр, мм
| 2...3
| 160. ..220
| 100. ..125
| 1,6. ..2,0
| 2... 4
| 320. ..350
| 150. ..200
| 1,6. ..2,0
| 4... 5
| 350. ..460
| 180. ..210
| 2,0. ..3,0
| 5... 6
| 650. ..750
| 200. ..250
| 4,0. ..5,0
| Таблица 13.7
Режим наплавки цилиндрических поверхностей
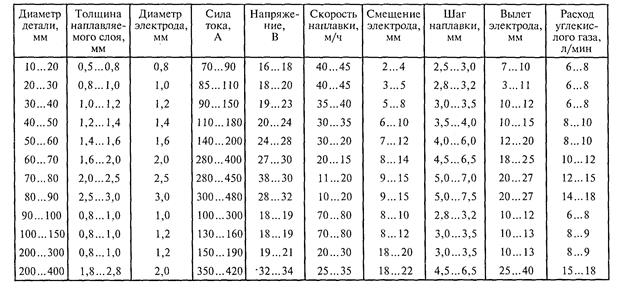
Наплавку в среде углекислого газа производят на постоянном токе обратной полярности. Тип и марку электрода выбирают в зависимости от материала восстанавливаемой детали и требуемых физико-механических свойств наплавленного металла. Скорость подачи проволоки зависит от силы тока, устанавливаемой с таким расчетом, чтобы в процессе наплавки не было коротких замыканий и обрывов дуги. Скорость наплавки зависит от толщины наплавляемого металла и качества формирования наплавленного слоя. Наплавку валиков осуществляют с шагом 2,5... 3,5 мм. Каждый последующий валик должен перекрывать предыдущий не менее чем на 1/3 его ширины.
Твердость наплавленного металла в зависимости от марки и типа электродной проволоки 200...300 НВ.
Расход углекислого газа зависит от диаметра электродной проволоки. На расход газа оказывают также влияние скорость наплавки, конфигурация изделия и наличие движения воздуха.
Механизированную сварку в углекислом газе применяют при ремонте кабин, кузовов и других деталей, изготовленных из листовой стали небольшой толщины, а также для устранения дефектов резьбы, осей, зубьев, пальцев, шеек валов и т.д.
Электродуговая наплавка неплавящимся электродом (вольфрамовым) в среде аргона. Этот способ наплавки широко используется для восстановления алюминиевых сплавов и титана. Сущность способа — электрическая дуга горит между неплавящимся вольфрамовым электродом и деталью. В зону сварки подается защитный газ -~ аргон, а присадочный материал — проволока (так же, как при газовой сварке). Аргон надежно защищает расплавленный металл от окисления кислородом воздуха. Наплавленный металл получается плотным, без пор и раковин. Добавление к аргону 10... 12% углекислого газа и 2... 3 % кислорода способствует повышению устойчивости горения дуги и улучшению формирования наплавленного металла. Благодаря защите дуги струями аргона (внутренняя) и углекислого газа (наружная) в 3...4 раза сокращается расход аргона при сохранении качества защиты дуги.
К преимуществам способа относятся — высокая производительность процесса (в 3...4 раза выше, чем при газовой сварке); высокая механическая прочность сварного шва; небольшая зона термического влияния; снижение потерь энергии дуги на световое излучение, так как аргон задерживает ультрафиолетовые лучи, а к недостаткам — высокая стоимость процесса (в 3 раза выше, чем при газовой сварке) и использование аргона.
Режим сварки определяется двумя основными параметрами: силой тока и диаметром электрода. Силу сварочного тока выбирают исходя из толщины стенки свариваемой детали (чем тоньше стенка, тем меньше сила сварочного тока) и составляет 100...500 А. Диаметр вольфрамового электрода составляет 4... 10 мм.
Устойчивость процесса наплавки и хорошее формирование наплавленного металла позволяют вести процесс на высоких скоростях — до 150 м/ч и выше.
Для наплавки в среде защитных газов применяют специальные автоматы и установки АГП-2, АДСП-2, УДАР-300, УДГ-501; полуавтоматы А-547Р, Л-537, ПШП-10; преобразователи ПСГ-350, ПСГ-500.
Вибродуговая наплавка. Этот способ наплавки является разновидностью дуговой наплавки металлическим электродом. Процесс наплавки осуществляется при вибрации электрода с подачей охлаждающей жидкости на наплавленную поверхность.
На рис. 13.7 дана принципиальная схема вибродуговой установки с электромеханическим вибратором. Деталь 3, подлежащая наплавке, устанавливается в патроне или в центрах токарного станка. На суппорте станка монтируется наплавочная головка, состоящая из механизма 5 подачи проволоки с кассетой 6, электромагнитного вибратора 7с мундштуком 4. Вибратор создает колебания конца электрода с частотой 110 Гц и амплитудой колебания до 4 мм (практически 1,8...3,2 мм), обеспечивая размыкание и замыкание сварочной цепи. При периодическом замыкании электродной проволоки и детали происходит перенос металла с электрода на деталь. Вибрация электрода во время наплавки обеспечивает стабильность процесса за счет частых возбуждений дуговых разрядов и способствует подаче электродной проволоки небольшими порциями, что обеспечивает лучшее формирование наплавленных валиков.
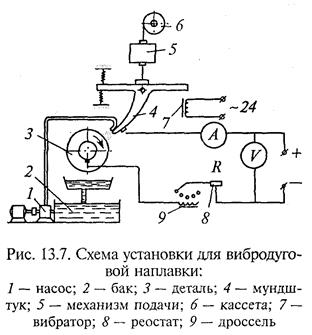
Электроснабжение установки осуществляется от источника тока напряжением 24 В. Последовательно с ним включен дроссель 9 низкой частоты, который стабилизирует силу сварочного тока. Реостат 8 служит для регулировки силы тока в цепи. В Зону наплавки при помощи насоса 1 из бака 2 подается охлаждающая жидкость (4...6%-ный раствор кальцинированной соды в воде), которая защищает металл от окисления.
К преимуществам способа относятся: небольшой нагрев деталей, не влияющий на нагрев деталей; небольшая зона термического влияния; высокая производительность процесса; возможность получать наплавленный слой без пор и трещин; минимальная деформация детали, которая не превышает полей допусков посадочных мест. К недостаткам способа относят снижение усталостной прочности деталей после наплавки на 30...40%.
Качество соединения наплавленного металла с основным зависит от полярности тока, шага наплавки (подача суппорта станка на один оборот детали), угла подвода электрода к детали, качества очистки и подготовки поверхности, подлежащей наплавлению, толщины слоя наплавки и др.
Высокое качество наплавки получают при токе обратной полярности («+» на электроде, «—» на детали), шаге наплавки 2,3...2,8 мм/об и угле подвода проволоки к детали 15... 30°. Скорость подачи электродной проволоки не должна превышать 1,65 м/мин, а скорость наплавки — 0,5...0,65 м/мин. Наибольшая скорость наплавки
К„ = (0,4...0,7)КПР, (13.4)
где Vnp — скорость подачи электродной проволоки, м/мин.
Knp = nsDh/(250d2i\), (13.5)
где я — частота вращения детали, мин;
s — шаг наплавки, мм/об;
D — диаметр детали, мм;
h — толщина наплавляемого слоя, мм;
d — диаметр электродной проволоки, мм;
г\ — коэффициент наплавки (г) = 0,85...0,90).
Надежное сплавление обеспечивается при толщине наплавленного слоя, равной 2,5 мм.
Структура и твердость наплавленного слоя зависят от химического состава электродной проволоки и количества охлаждающей Жидкости. Если при наплавке используется проволока Нп-80 (содержание углерода 0,75...0,85 %), то валик в охлаждающей жидкости закаляется до высокой твердости (26...55 HRC3). При использовании при наплавке низкоуглеродистой проволоки Св-08 твердость поверхности наплавки равна 14... 19 HRG,.
Вибродуговой наплавкой восстанавливают детали с цилиндрическими, коническими наружными и внутренними поверхностями, а также с плоскими поверхностями (рис. 13.8).

При однослойной наплавке толщина слоя колеблется от 0,5 до 3 мм, а при многослойной наплавке ее можно получить любой толщины.
Рациональный режим наплавки: напряжение — 28...30 В; сила тока — 70...75 А (диаметр проволоки 1,6 мм); скорость подачи проволоки — 1,3 м/мин; скорость наплавки — 0,5...0,6 м/мин; амплитуда вибрации — 1,82 мм.
Широкослойная наплавка. Сущность способа — это наплавка тел вращения за один оборот детали с поперечным колебанием электрода, а не по винтовой линии.
Режимы наплавки: ток — 250...420 А; напряжение — 26...28 В; скорость подачи проволоки — 240...400 м/ч; скорость наплавки — 5,0...6,0 м/ч; вылет, смещение и размах колебаний электрода соответственно — 18...20, 6...7 и 27...57 мм.
Внутренние цилиндрические и конические поверхности наплавляются с использованием специальных удлиненных мундштуков. Тела сложной формы наплавляют самозащитной порошковой проволокой на специализированных станках, позволяющих придать оси вращения горизонтальное положение.
Плоские поверхности целесообразно наплавлять колебательными движениями электрода или с использованием электродной ленты. Параметры наплавки: ширина ленты — 20...30 мм; ток — 600... 1000 А; рациональная скорость наплавки для ленты шириной не более 30 мм — 15...60 м/ч. Процесс наплавки осуществляют отдельными участками во избежание коробления деталей.
Плазменно-дуговая сварка и наплавка. Плазменная струя представляет собой частично или полностью ионизированный газ, обладающая свойствами электропроводности и имеющая высокую температуру. Она создается дуговым разрядом, размещенным в узком канале специального устройства, при обдуве электрической дуги потоком плазмообразующего газа. Устройства для получения плазменной струи получили название плазмотронов или плазменных горелок (рис. 13.9). Плазменную струю получают путем нагрева плазмообразующего газа в электрической дуге, горящей в закрытом пространстве. Температура струи достигает 10000... 30 000 "С, а скорость в 2... 3 раза превышает скорость звука.
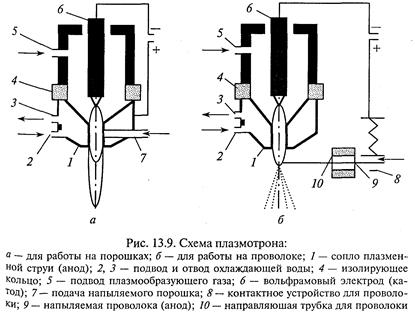
Плазмотрон состоит из охлаждаемых водой катода и анода, смонтированных в рукоятке. Катод обычно изготовляют из вольфрама или лантанированного вольфрама (вольфрамовые стержни с присадкой 1...2% окиси лантана), анод (сопло) — из меди (водоохлаждаемое сопло). Катод и анод изолированы друг от друга прокладкой из изоляционного материала (асбеста). Технические характеристики плазматронов для сварки и наплавки приведены в табл. 13.8 и 13.9.
Для получения плазменной струи между катодом и анодом возбуждают электрическую дугу от источника постоянного напряжения 80... 100 В. Электрическая дуга, горящая между катодом и анодом, нагревает подаваемый в плазмотрон газ до температуры плазмы, т. е. до состояния электропроводности. В поток нагретого газа вводится материал для сварки и наплавки. Образующиеся расплавленные частицы материала выносятся потоком горячего газа из сопла и наносятся на поверхность изделия.
В качестве плазмообразующих газов используют аргон и азот. Ар-гонная плазма имеет более высокую температуру —15 000... 30 000 °С, температура азотной плазмы ниже — 10 000... 15 000 "С. Применение нейтральных газов способствуют предотвращению окисления материалов.
Таблица 13.1
Технические характеристики плазмотронов для наплавки
Параметры
| Плазмотроны для наплавки
|
наружных
| внутренних
| Унивесаль-
|
| поверхностей
| поверхностей
| ного типа
| Допустимая сила тока, А
|
|
|
| Производительность наплавки, кг/ч
| 0,5. ,5,2
| 0,3. ..3,0
| 0,5. ..3,8
| Диаметр, мм: плазмообразующего сопла выходного отверстия защит-
| 4 12. ..13
| 4 10. ..12
| 3...4 10... 12
| ного сопла
|
|
|
| Высота плазмотрона, мм
|
|
|
|
Таблица 13.9
Технические характеристики плазмотронов для сварки
| Максимальная
| Толщи-
| Максимальный
| Масса,
|
| сварочная сила
| на сва-
| расход, л/мин
| кг
| Тип
| тока, А
| ривае-
|
|
| плазмотрона
| прямая
| обратная
| мого металла,
| газов
| охлаж-
|
|
| поляр-
| поляр-
| мм
| (суммар-
| дающей
|
|
| ность
| ность
|
| ный)
| воды
|
| ПРС-0201
|
|
| 0,05. ..1,5
| 6,6
| 2,0
| 0,1
| ПРС-0401
|
|
| 0,1. ,2,5
| 6,6
| 2,0
| 0,3
| ПРС-0301
|
| —
| 0,5
| 17,0
| 4,0
| 1,0
| ПМС-501
|
| —
| —
| —
| —
| —
| ПМС-804
|
| —
| 6. ,12
| —
| —
| —
| Многодуговой
|
|
| 1...60
| 45,0
| 8,4
| з.о
|
В зависимости от подключения плазматрона к источнику питания плазменная дута может быть открытой, закрытой и комбинированной.
При открытой плазменной дуге (рис. 13.10, б) ток течет между вольфрамовым электродом и деталью. Плазмообразующий газ совпадает с дуговым разрядом на всем пути его следования от катода до анода. Такой процесс сопровождается передачей большого количества тепла детали. Открытая плазменная дуга применяется при резке металлов.
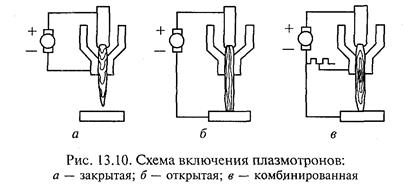
При закрытой плазменной дуге (рис. 13.10, а) плазмообразую-щий газ проходит соосно с дугой лишь часть пути и, отделяясь от нее, выходит из сопла плазмотрона в виде факела плазмы. Температура закрытой плазменной дуги (светлой ее части) на 25...30% выше, чем открытой. Эта дуга применяется для плавления тугоплавких порошков, подаваемых в сжатую часть дуги.
При комбинированной схеме горят две дуги (рис. 13.10, в): между вольфрамовым электродом и деталью; между вольфрамовым электродом и водоохлаждаемым соплом. Плазмотрон с комбинированной дугой позволяет раздельно регулировать плавление присадочного и основного материала изменением величины соответствующих сопротивлений.
Исходный материал покрытия подается в плазматрон в виде порошка, проволоки, прутка. Режимы плазменной наплавки порошковыми материалами приведены в табл. 13.10.
Плазменную наплавку выполняют одиночным валиком (при наплавке цилиндрических деталей по винтовой линии), а также с применением колебательных механизмов, на прямой и обратной полярности. Наиболее простой способ наплавки — это наплавка по заранее насыпанному на наплавляемую поверхность порошку.
В ремонтной практике для получения износостойких покрытий применяют хромборникелевые порошки СНГН и ПГ-ХН80СР4, твердосплавные порошки на железной основе ФБХ-б-2, КБХ, УС-25 и другие, а также смеси порошков.
Для плазменной наплавки выпускаются установки УМП-303, УПУ-602 и другие и оборудование-комплект КПН-01.23-215 Рем-деталь, пост 01.23-21 Ремдеталь, для сварки УПС-301, УПС-403, УПС-804. Толщина напыляемого материала — 0,1...2 мм.
Лазерная наплавка. Этот способ наплавки представляет собой технологический метод получения покрытий с заданными физико-механическими свойствами путем нанесения наплавочного материала (порошок, фольга, проволока и др.) с последующим оплавлением его лазерным лучем. Наименьших затрат энергии требуют порошковые материалы.
Порошки на поверхность детали могут подаваться непосредственно в зону лазерного луча с помощью дозатора; после предварительной обмазки клеющим составом; в виде коллоидного раствора. Для первого случая характерен увеличенный расход порошка (в 5...7 раз) и ухудшение физико-механических свойств покрытия. Коллоидный раствор — это смесь порошка и раствора целлюлозы.
Таблица 13.10
Режимы плазменной наплавки порошковыми материалами
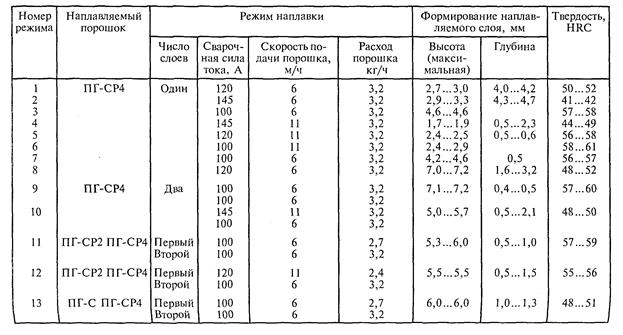
С увеличением толщины обмазки увеличивается поглощение излучения и растет КПД наплавки. Одновременно возрастает твердость нанесенного слоя, которую путем подбора скорости наплавки и материала можно регулировать в пределах 35...65 HRC.
При наплавке порошковых материалов необходимо учитывать грануляцию частиц. Увеличение размеров частиц приводит к росту твердости и износостойкости покрытия. Рациональной является смесь различных фракций: 40...100 мкм — 10%, 100...280 мкм — 80%, 280 мкм и более — 10 %.
Качество покрытий зависит от скорости перемещения лазерного луча, толщины наплавляемого слоя и перекрытия валиков. Покрытия, нанесенные лазерной наплавкой, имеют следующие характеристики: толщина слоя, наплавленного за один проход — до 0,8 мм; толщина дефектного слоя — не более 0,1 мм; прочность сцепления — до 35 кг/мм2; потери наплавляемого материала — не более 1 %; глубина зоны термического влияния — не более 1 мм. Толщина нанесенного слоя может достигает 40...50 мкм.
Оплавление лазерным лучем проводится на установках, которые используют серийные лазеры: ЛГН-702 «Кардамон», ЛТ1-2, «Иглай», «Комета», «Катунь», Латус-31, Юпитер 1,0, и лазерных технологических модулях: 01.03.178 «Ремдеталь» и 01.12.376 «Рем-деталъ». В табл. 13.11 приведены технологические параметры наплавки.
Лазерной наплавкой восстанавливают тарелки клапанов, кулачки распределительных и кулачковых валов и других деталей.
Таблица 13.11
Технологические параметры лазерной наплавки в зависимости от фракции и состава порошка
Порошок
| Фракции
| Скорость наплавки,
см/мин
| Микротвердость -1 03, МПа
| Прочность сцепления с основой, МПа
| ПН73ХСЗРЗ
| 200. ..300
|
| 7,5
|
|
| 6,5
|
| 5,5
|
| 4,5
|
100. ..200
|
| 6,5
|
| 6,0
|
| 5,5
|
| 3,5
|
60. ..100
|
| 3,2
|
| 2,9
|
| 2,5
|
| 2,4
|
ПГФБХ-6-2
| 100. ..200
| 15. ..38
| 8,0. ..10,0
|
|
200. ..400
| 15. ..35
| 8, 5. ..11,0
|
400... 600
| 15. ..30
| 9,0... 11,5
|
Особенности сварки чугунных деталей. Многие корпусные детали изготавливаются из серого, высококачественного и ковкого чугуна, который является трудносвариваемым материалом. У деталей из чугуна сваркой заделывают трещины и отверстия, присоединяют отколотые части детали, наплавляют износостойкие покрытия.
Не нашли, что искали? Воспользуйтесь поиском по сайту:
©2015 - 2025 stydopedia.ru Все материалы защищены законодательством РФ.
|