Графический метод определения профиля фасонного резца.
При определении профиля фасонного резца графическим методом принимается масштаб 4:1.
См.приложение [1].
Аналитический метод расчета профиля резца.
1. Определение габаритных размеров фасонного резца:
Максимальный диаметр фасонного резца D = 2 ∙ R = 2 ∙ 25 = 50 мм
Значения заднего и переднего угла a = 10°; g = 20°. [1]
Рисунок 3. Схема расчета круглого фасонного резца для наружной обточки.
r1, мм
| r2 = r3= r7, мм
| R4, мм
| r5 = r6, мм
| 12,5
|
| 16,5
|
|
Определение размеров А1, А2, А3, А4, А5, А6, А7 и С1, С2, С3, С4, С5, С6, С7
(1.2)
Для 1 точки:
(1.3)
Для 2, 3 и 7 точек:
(1.4)
(1.5)
Для 4 точки:
Для 5 и 6 точек:

мм

Определение размеров В1, В2, В3, В4, В5, В6, В7 и R1, R2, R3, R4, R5, R6, R7.
, R1= 17мм
(1.6)
Для 1 точки:
(1.7)
Для 2, 3 и 7 точек:

(1.8)

Для 4 точки:



Для 5 и 6 точек:



Результаты графического и аналитического методов расчета профиля фасонного резца и их сравнительный анализ приведены в таблице 1.
Таблица 1.Сравнение результатов графического и аналитического методов:
Соответствующие точки профиля детали
|
| 2,3,7
|
| 5,6
|
| R1,мм
| R2,мм
| R4,мм
| R5,мм
| | Графический метод
|
| 14,5
| 13,5
|
| | Аналитический метод
|
| 14,78
| 13,54
| 12,34
| | Погрешность, мм
|
| 0.28
| 0.04
| 0,34
| | | | | | | | |
Близкие значения диаметров фасонного резца при расчете аналитическим методом подтверждают правильность выполнения графического метода .
По рассчитанным конструктивным параметрам оформляют рабочий чертеж фасонного резца (см. Приложение).
Расчет профиля фасонной затылованной фрезы .
Исходные данные для расчета профиля фрезы: обрабатываемый материал – ВМЛ-1(ГОСТ 2856-79) и профиль детали (рис.3). 3D модель обрабатываемой детали показана на рис.4.
Передний и задний углы задаются в зависимости от физико-механических свойств обрабатываемого материала: a = 10°; g = 15°. [5].

Рис.3.Профиль фасонной детали , получаемой фрезерованием.
R = 11 мм . H = 10 мм .B = 32 мм
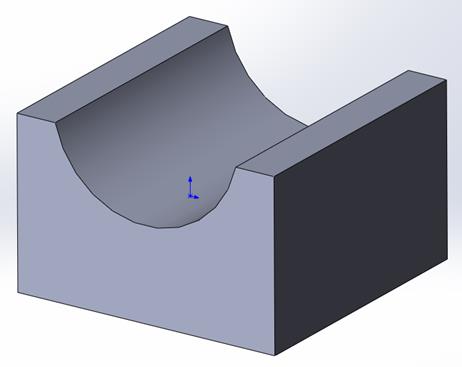
Рис.4 3D модель фасонной детали, получаемой фрезерованием .
Конструктивные параметры дисковой фрезы с затылованными зубьями
Диаметр посадочного отверстия определяется из условия обеспечения достаточной прочности и жесткости оправки фрезы:
, где h и b -соответственно глубина и ширина профиля обрабатываемой канавки детали. Полученный результат округляем до ближайшего значения из нормального ряда диаметров, принимаем d0 = 27 мм [2]
Приближенное значение наружного диаметра:
D ≈ 2.5 ∙ d0 = 2.5 ∙ 27 = 67.5 мм, принимаем D = 70 мм
Высота профиля зуба фрезы :

Число зубьев фрезы :
где А – коэффициент, определяющий прочность зуба и равный 1.8 .. 2.5 для черновых фрез 1.4 .. 1.8 для чистовых.
Геометрические параметры фрезы
Значение переднего угла g=15выбирается положительным в зависимости от обрабатываемого материала детали , что способствует улучшению процесса резания [3]
Значение заднего угла : α = 10 [2]
Величина затылования: , принимаем k = 4 .
Центральный угол канавки, необходимый для выхода затыловочного инструмента:
(при h1 < 15 мм)
Радиус закругления дна впадины между зубьями фрезы:
, принимаем ra = 1 мм
Высота зуба фрезы:
H = h1 + k + r = 11 + 4 + 1 = 16 мм
Толщина фрезы:
m = (0.3…0.5) ∙ d0 = 0.35 ∙ 27 = 9.45, принимаем m = 10 мм
Уточненный наружный диаметр фрезы :
da = d0 + 2∙m + 2∙H = 27 + 2∙10 + 2∙16 = 79 мм, принимаем da = 80 мм
Ширина фрезы :
B = b + (0.5 .. 1)=32 + 1 = 33 мм.
Угол впадины : 
Центральный угол зуба фрезы :
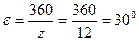
Окончательные значения конструктивных параметров проверяют прочерчиванием фрезы.
Профилирование зубьев фрезы.
Если передний угол γ = 0°, то профиль зубьев в плоскости передней поверхности совпадает с профилем осевого сечения исходной инструментальной поверхности фрезы. При γ≠о° высотные размеры профиля фрезы необходимо корректировать, размеры профиля вдоль оси не изменяются. При этом высотные размеры hiп профиля зуба в плоскости передней поверхности, необходимые для контроля для любой i - ой точки:
N = R∙cos γ = 40∙cos 15 = 41,05 (2.1)
m = R∙sin γ = 40∙sin 15 = 11 (2.2)
Ri = R - hi; (2.3)
(2.4)
ni = Ri∙cos γi (2.5)
hin = N - ni ; (2.6)
; (2.7)
; (2.8)
; (2.9)
Для 1 точки:
R1 = R – h1 = 42,5 – 2.5 = 40 мм;
n1 = R1∙cos γ1 = 40∙cos 15,96 = 38,46 мм
h1n = N – n1 = 41,05 – 38,46 = 2,59 мм
;
;
;
Для 2 точки:
R2 = R – h2 = 42,5 – 5 = 37,5 мм;
n2 = R2∙cos γ2 = 37,5∙cos 17,06 = 35,85 мм
h2n = N – n2 = 41,05 – 35,85 = 5,2 мм
;
;
;
Для 3 точки:
R3 = R – h3 = 42,5 – 7.5 = 35 мм;
n3 = R3∙cos γ3 = 35∙cos 18,32 = 33.22мм
h3n = N – n3 = 41,05 – 33,22 = 7,83 мм
;
;
;
Для 4 точки:
R4 = R – h4 = 42.5 – 10 = 32,5 мм;
n4 = R4∙cos γ4 = 32,5∙cos 19,78 = 30,58 мм
h4n = N – n4 = 41,05 – 30,58 = 10,47 мм
;
;
;
По рассчитанным конструктивным параметрам оформляют рабочий чертеж фасонной фрезы, а также прочерчивают профиль зубьев в осевом сечении (см. Приложение).
Подбор стандартных альтернативных инструментов дли получении фасонных профилей заданных деталей.
Не нашли, что искали? Воспользуйтесь поиском по сайту:
©2015 - 2024 stydopedia.ru Все материалы защищены законодательством РФ.
|