Электромагнитный кристаллизатор
Раздел 2. Материаловедение . Технология конструкционных материалов
Вопрос.
Литьё — технологический процесс изготовления заготовок (реже — готовых деталей), заключающийся в заполнении предварительно изготовленной литейной формы жидким материалом (металлом, сплавом, пластмассой и т. п.) с последующим его затвердеванием.
Известно множество разновидностей литья:
· в песчаные формы (ручная или машинная формовка);
· в многократные (цементные, графитовые, асбестовые формы);
· в оболочковые формы;
· по выплавляемым моделям;
· по замораживаемым ртутным моделям;
· центробежное литьё;
· в кокиль;
· литьё под давлением;
· по газифицируемым (выжигаемым) моделям;
· вакуумное литьё;
· электрошлаковое литьё;
· литьё с утеплением.
Непрерывное литьё металлов и сплавов, процесс получения слитков и заготовок, основанный на равномерном перемещении металла относительно зон заливки и кристаллизации. При этом литейная форма может быть неподвижной или закономерно перемещаться (возвратно-поступательное движение с небольшой амплитудой, вращение, движение по замкнутой кривой ограниченной длины).
Горизонтальное непрерывное литье
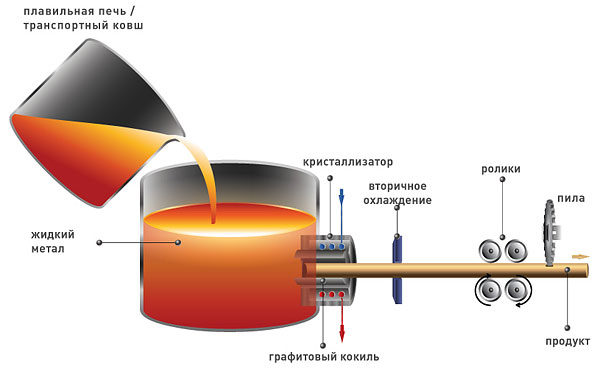
Иллюстрация изображает процесс горизонтального непрерывного литья. Главные компоненты: плавильная печь или транспортный ковш, тигель, кристаллизатор с системой охлаждения и вставленным кокилем, устройство повторного охлаждения, транспортировочные ролики и пила.
Литейное оборудование функционирует следующим образом: сначала в плавильной печи расплавляется металл, потом плавка подается в транспортный ковш для транспортировки в литейное устройство или подается прямо в плавильный тигель, из которого жидкий металл под воздействием гравитационных сил течет через графитовый кокиль, вставленный в кристаллизатор горизонтально, где металл охлаждается и обретает форму. Транспортировочные ролики улавливают сформированный продукт и регулируют скорость литья. Заготовка выходит из литейной машины в горизонтальном положении. Заготовка разрезается пилой на заданную длину и потом подается на дальнейшую обработку.
Вертикальное литье
· вверх
· вниз

Электромагнитный кристаллизатор
Изобретение относится к металлургии, а именно к устройствам для полунепрерывного или непрерывного литья металлов и сплавов. Цель изобретения - сокращение энергозатрат за счет повышения равномерности распределения напряженного электромагнитного поля. Устройство содержит индуктор, изготовленный из мерной ленты, стенки которой образуют охлаждающий канал, затравки, дозирующей воронки, экрана, введенного в индуктор, и тангенциально расположенных токопроводящих шин.
Элетрошлаковое литьё(ЭШЛ) — вид электрошлакового процесса (ЭШП), литейная технология с защитой металлической ванны от взаимодействия с воздухом находящейся сверху шлаковой ванной, подогреваемой проходящим через неё электрическим током. Используется, например, при изготовлении биметаллических прокатных валков.
Рабочая поверхность валков холодной прокатки должна быть износостойкой, а для этого — твёрдой. Иначе она быстро сомнётся. Дешёвый, но достаточно твёрдый материал — серый чугун. Но он не достаточно прочен. Весь же валок должен быть прочным, иначе он не выдержит нагрузки и сразу лопнет. Достаточно прочный материал — конструкционная сталь. Но она слишком мягкая. Можно сделать весь валок из инструментальной стали. Но инструментальная сталь дороже, а валок — не резец. У него значительно больше объём и масса, из-за чего такое изделие окажется много дороже большинства инструментов, а служит он всёравно недолго. Выход: сделать поверхность твёрдой, а основное тело валка — прочным. Для этого применяют плазменную наплавку инструментальной стали на конструкционную. Но во-первых, это лишь частично решает проблему дороговизны материала (инструментальной стали), а во-вторых достаточно дорога сама технология. Одна из альтернатив — наворачивание цельно чугунного бандажа на цельно стальное основное тело валка (обе детали должны иметь резьбу). Но при эксплуатации таких валков бандаж сворачивается с основного тела валка. Кроме того, недостаточная прочность чугуна обуславливает формы разрушения бандажа в процессе эксплуатации, отличные от мгновенного хрупкого разрушения, в первую очередь по поверхности контакта бандажа с основным телом валка. Значит нужен прочный белый чугун. Но белый чугун дороже серого. Электрошлаковое же литьё позволяет дешево отбелить серый чугун за счёт экономного легирования серого чугуна хромом. Эта же технология позволяет соединить сплавлением (сварить по всей поверхности контакта) бандаж и основное тело валка. При обычном литье аналогичных изделий диспергирование струи ведёт к избыточному окислению металла, а из-за слишком быстрой кристаллизации чугун шва будет иметь повышенную хрупкость (а не прочность) и не произойдёт сплавление достаточных объёмов стали и чугуна, из-за чего шов будет тонким и в нём не сформируется область плавного перехода по составу от чугуна к стали. Электрошлаковая же технология позволяет решить все эти проблемы. Поверхности кокиля (литейной формы, если она используется) и заготовок(ки) обмазываются фторидами и хлоридами щелочных и щёлочноземельных металлов, термическое разложение этих солей создаёт защитную атмосферу. Струя металла также диспергируется, но теперь это ведёт не к окислению, а к рафинированию металла. Рафинирование металла более интенсивно продолжается также и в шлаке. Остальные проблемы решаются подогревом зоны кристаллизации. Кроме того, элетрошлаковая технология позволяет создать переходный слой (шов) с рельефом двух встречных псевдорезьб. Этот рельеф и работает аналогично двум встречным резьбам (как у талрепа — резьбового приспособления для натяжения тросов), дополнительно скрепляя части изделия, но при этом, не допуская сворачивания бандажа.
Поддерживается также раздельное легирование зон отливки. При ЭШЛ в шлаковой ванне существует магнитное поле и в ней же протекает электрический ток. Силовые линии магнитного поля ориентированы вертикально, а вектор плотности электрического тока в любой точке имеет горизонтальные проекции. В результате взаимодействия электрического тока с магнитным полем возликает горизонтальная сила Лоренца. Радиальная компонента плотности тока обуславливает азимутальную составляющую этой силы, причём, во внешней и внтуренней, относительно электрода, зонах знак радиальной проекции плотности тока противоположен, а направление магнитного поля совпадает. В результате направление азимутальной составляющей силы Лоренца в этих областях противоположно. А это ведёт к возбуждению двух встречных тороидальных потоков шлака. Причём, характер течения ламинарный. Поэтому оба потока не смешиваются. Материал электрода делится между ними ровно пополам, но даже его концентрация в различных зонах шлаковой ванны может быть не одинакова. Если эти зоны имеют различный объём, то в них концентрация материала электрода обратно пропорциональна объёмам зон. В металлической ванне (которая находится под шлаковой) имеет место диффузия, но состав до конца всё равно не выравнивается. Таким образом, электрод из порошковой проволоки можно использовать для раздельного легирования зон отливки. Кроме того, подача легирующих сверху непосредственно во внутреннюю, или во внешнюю зону шлаковой ванны позволяет добиться раздельного легирования, независимого от соотношения объёмов зон, так как присадки в одну зону вообще не попадают в другую.
Варианты ЭШЛ
· Литьё переходного слоя На запорную плиту ставят две заготовки основного тела и бандажа валка и льют переходный слой между ними
· Литьё основного тела валка На запорную приту ставят заготовку бандажа и внутрь льют основное тело валка
· Литьё бандажа в Кокиль Внутри литейной формы (кокиля) ставят заготовку основного тела валка и льют бандаж между кокилем и заготовкой
Используемый метал может переплавляться электрошлаковым способом и сразу заливаться в форму, так и подогреваться в промежуточном ковше, после быстрого слива в него готового расплава, полученного любым другим способом. Общей является электрошлаковая защита металла в ковше как от взаимодействия с воздухом, так и от преждевременной кристаллизации в процессе литья.

схема получения отливки электрошлаковым литьем: 1 – электроды (стрелками показано направление их движения); 2 – кристаллизатор; 3 – стержень (наружной стрелкой показано направление его движения вверх; фигурной стрелкой – направление потока охлаждающей воды); 4 – шлаковая ванна; 5 – расплав; 6 – отливка; 7 – затравка
Сферы применения изделий, полученных при помощи ЭШЛ:
1 Стальное литье - заглушки (водоканал, теплоцентрали, нефтегазовая промышленность) - шары для шаровых мельниц (ТЭЦ, цементные заводы и прочие) - фланцы (водоканал, теплоцентрали, нефтегазовая промышленность) - переходы (нефтегазотрубопроводы) - штампы (машиностроительные заводы и ремонтные мастерские) и т.д. 2. Наплавка твердым сплавом - ножи (грейдер, бульдозер и скрепер) - дробящие плиты (цементные заводы) - конуса для дробилок (карьеры, цементные заводы, горнодобывающая промышленность) - плиты для дробилок (карьеры, цементные заводы, горнодобывающая промышленность) - клыки для экскаваторов (карьеры, цементные заводы, прочие) - било (ТЭЦ) - молотки (ТЭЦ, цементные заводы) - наплавка для драг (золотодобывающая промышленность) - башмаки для гусеничных тракторов (сельское хозяйство, горнодобывающая промышленность) - почвообрабатывающие детали машин (сельское хозяйство) - прочее. 3. Вытяжка (непрерывная кристаллизация) - уголок и металлоконструкции (строительные организации) - пруток (катанка от 5 до 25 мм) - прочие профиля 4. Цветной металл - контактный провод (железная дорога, троллейбусы, трамваи) - катанка медная (кабельное производство, эмаль производство) - шестигранник (бронза, латунь для производства метизов) - прочее 5. Керамика - керамические плиты - облицовочные плиты - кирпич 6. Каменное литье. - камни (в т.ч. декоративные) - теплоизолирующие плиты - трубы - бордюрные камни
7. Прямое восстановление - циркония - редких земель 8. Высокотемпературная керамика - кирпич из оксида алюминия - кирпич из циркония - кирпич из магнезита - высокотемпературные теплоизоляционные плиты.
Вопрос.
Обработка металлов давлением основана на их способности при определенных условиях пластически деформироваться в результате воздействия на деформируемое тело (заготовку) внешних сил.
Если при упругих деформациях деформируемое тело полностью восстанавливает исходные форму и размеры после снятия внешних сил, то при пластических деформациях изменение формы и размеров, вызванное действием внешних сил, сохраняется и после прекращения действия этих сил. Упругая деформация характеризуется смещением атомов относительно друг друга на величину, меньшую межатомных расстояний, и после снятия внешних сил атомы возвращаются в исходное положение. При пластических деформациях атомы смещаются относительно друг друга на величины, большие межатомных расстояний, и после снятия внешних сил не возвращаются в свое исходное положение, а занимают новые положения равновесия.
Для начала перехода атомов в новые положения равновесия необходима определенная величина действующих напряжений, зависящая от межатомных сил и характера взаимного расположения атомов (типа кристаллической решетки, наличия и расположения примесей, формы и размеров зерен поликристалла и т. п.).
Так как сопротивление смещению атомов в новые положения изменяется не пропорционально смещению, то при пластических деформациях линейная связь между напряжениями и деформациями обычно отсутствует.
Напряжения, вызывающие смещение атомов в новые положения равновесия, могут уравновешиваться только силами межатомных взаимодействий. Поэтому под нагрузкой при пластическом деформировании деформация состоит из упругой и пластической составляющих, причем упругая составляющая исчезает при разгрузке (при снятии деформирующих сил), а пластическая составляющая приводит к остаточному изменению формы и размеров тела. В новые положения равновесия атомы могут переходить в результате смещения в определенных параллельных плоскостях, без существенного изменения расстояний между этими плоскостями. При этом атомы не выходят из зоны силового взаимодействия и деформация происходит без нарушения сплошности металла, плотность которого практически не изменяется. Скольжение одной части кристаллической решетки относительно другой происходит по плоскостям наиболее плотного размещения атомов (плоскостям скольжения). В реальных металлах кристаллическая решетка имеет линейные дефекты (дислокации), перемещение которых облегчает скольжение.
Величина пластической деформации не безгранична, при определенных ее значениях может начаться разрушение металла.
На величину пластической деформации, которую можно достичь без разрушения (предельная деформация), оказывают влияние многие факторы, основные из которых - механические свойства металла (сплава), температурно-скоростные условия деформирования и схема напряженного состояния. Последний фактор оказывает большое влияние на значение предельной деформации. Наибольшая предельная деформация достигается при отсутствии растягивающих напряжений и увеличении сжимающих. В этих условиях (схема неравномерного всестороннего сжатия) даже хрупкие материалы-типа мрамора могут получать пластические деформации. Схемы напряженного состояния в различных процессах и операциях обработки давлением различны, вследствие чего для каждой операции, металла и температурно-скоростных условий существуют свои определенные предельные деформации.
Существенные преимущества обработки металлов давлением по сравнению с обработкой резанием - возможность значительного уменьшения отхода металла, а также повышения производительности труда, поскольку в результате однократного приложения усилия можно значительно изменить форму и размеры деформируемой заготовки. Кроме того, пластическая деформация сопровождается изменением физико-механических свойств металла заготовки, что можно использовать для получения деталей с наилучшими эксплуатационными свойствами (прочностью, жесткостью, высокой износостойкостью и т. д.) при наименьшей их массе. Эти и другие преимущества обработки металлов давлением (отмеченные ниже) способствуют неуклонному росту ее удельного веса в металлообработке. Совершенствование технологических процессов обработки металлов давлением, а также применяемого оборудования позволяет расширять номенклатуру деталей, изготовляемых обработкой давлением, увеличивать диапазон деталей по массе и размерам, а также повышать точность размеров полуфабрикатов, получаемых обработкой металлов давлением.
Если обработка металлов давлением выполняется при температуре ниже температуры рекристаллизации, то такая обработка называется холодной.
Если обработка металлов давлением происходит при нагреве металлического тела выше температуры рекристаллизации, то она называется горячей.
Основными законами обработки металлов давлением являются:
· Закон постоянства объемов - объем металла до деформации практически равен объему металла после деформации.
· Закон наименьшего сопротивления - частицы деформируемого металла всегда перемещаются в направлении наименьшего сопротивления.
Холодная объёмная штамповка.
Штамповка без предварительного нагрева заготовки – для металлов и сплавов такой процесс деформирования соответствует условиям холодной деформации. Отсутствие окисленного слоя на заготовках (окалины) при холодной штамповке обеспечивает хорошее качество поверхности детали и достаточно высокую точность размеров, это уменьшает объём обработки резанием или даже исключает её. Основные разновидности холодной объёмной штамповки – холодное выдавливание, холодная высадка, холодная штамповка в открытом штампе.
Холодное выдавливание.
Заготовку помещают в полость, из которой металл выдавливают в отверстия, имеющиеся в рабочем инструменте. Выдавливание обычно выполняют на кривошипных или гидравлических прессах в штампах, рабочими частями которых являются пуансон и матрица.
Основной положительной особенностью выдавливания является возможность получения без разрушения заготовки весьма больших степеней деформации, которые можно характеризовать показателем k=F0/F1 (F0 и F1 - площади поперечного сечения исходной заготовки и выдавленной части детали). Для весьма мягких, пластичных металлов k>100 (алюминиевые трубы со стенкой толщиной 0,1-0,2 мм при диаметре трубы 20-40 мм). Пластическое деформирование при выдавливании происходит в условиях всестороннего неравномерного сжатия.
Холодная высадка.
Высадка – уменьшение длины части заготовки с получением местного увеличения поперечных размеров. Штамповкой на холодновысадочных автоматах обеспечиваются достаточно высокая точность размеров и хорошее качество поверхности, вследствие чего некоторые детали не требуют последующей обработки резанием. Штамповка на холодновысадочных автоматах высокопроизводительна: 20-400 деталей в минуту. Штамповка на холодновысадочных автоматах характеризуется высоким коэффициентом использования металла. Средний коэффициент использования металла 95% (только 5% идёт в отход).
На холодновысадочных автоматах штампуют заготовки диаметром 0,5 - 40 мм из чёрных и цветных металлов, а также детали с местными утолщениями сплошные и с отверстиями.
Холодная штамповка в открытых штампах.
Холодная штамповка в открытых штампах заключается в придании заготовке формы детали путём заполнения полости штампа металлом заготовки (см. схему штамповки в открытых штампах). Холодная объёмная штамповка требует значительных удельных усилий вследствие высокого сопротивления металла деформированию в условиях холодной деформации и упрочнения металла в процессе деформирования. Упрочнение сопровождается и уменьшением пластичности. Для уменьшения вредного влияния упрочнения и облегчения процесса деформирования при холодной штамповке оформление детали обычно расчленяют на переходы, между которыми заготовку подвергают рекристаллизационному отжигу. В закрытых штампах в условиях холодной деформации штампуют реже и главным образом из цветных металлов. Холодной штамповкой можно изготовлять пространственные детали сложных форм (сплошные и с отверстиями). Холодная объёмная штамповка обеспечивает получение деталей со сравнительно большой точностью размеров и качеством поверхности. Это уменьшает объём обработки резанием или даже исключает её. Однако, учитывая, что изготовление штампов трудоёмко и дороже изготовления инструмента, используемого при обработке резанием, холодную штамповку следует применять лишь при достаточно большой серийности производства.
Чем выше температура нагрева, тем больше размер образующихся новых зерен.
Вначале с увеличением степени деформации размер зерна при рекристаллизации сильно возрастает, затем с дальнейшим увеличением степени деформации уменьшается.
Степень деформации, дающая максимальный размер зерна при нагреве, называется критической. При ковке, прокатке и других видах обработки нужно следить за тем, чтобы металл не приобретал критической степени деформации, иначе при последующем нагреве получается крупнозернистый металл с плохими свойствами.
Вопрос.
Прокатка — процесс пластического деформирования тел на прокатном стане между вращающимися приводными валками (часть валков может быть неприводными). Слова "приводными валками" означают, что энергия, необходимая для осуществления деформации, передается через валки, соединённые с двигателем прокатного стана. Деформируемое тело можно протягивать и через неприводные (холостые) валки, но это будет не процесс прокатки, а процесс волочения.
Прокатка относится к числу основных способов обработки металлов давлением. Прокаткой получают изделия (прокат) разнообразной формы и размеров. Как и любой другой способ обработки металлов давлением прокатка служит не только для получения нужной формы изделия, но и для формирования у него определенной структуры и свойств.
схема прокатки
Процессы прокатки классифицируют по следующим признакам:
· по температуре проведения процесса прокатку делят на горячую (температура металла при реализации процесса выше температуры рекристаллизации) и холодную (температура металла ниже температуры рекристаллизации). Также имеет место так называемая теплая прокатка - обработка в области промежуточных температур;
· по взаимному расположению осей валков и полосы различают продольную (ось прокатываемой полосы перпендикулярная осям валков), поперечную (ось прокатываемой полосы параллельна осям валков) и поперечно-винтовую или "косую" прокатку (оси валков находятся под некоторым углом друг к другу и к оси прокатываемой полосы;
· по характеру воздействия валков на полосу и условиям деформации прокатка бывает симметричной и несимметричной. Симметричной прокаткой называют процесс при котором воздействие каждого из валков на прокатываемую полосу является идентичным. Если это условие нарушается процесс следует отнести к несимметричному;
· по наличию или отсутствию внешних сил, приложенных к концам полосы, выделяют свободную и несвободную прокатку. Прокатка называется свободной если на полосу действуют только силы, приложенные со стороны валков. Несвободная прокатка осуществляется с натяжением или подпором концов полосы.
Применяют прокатный стан.
Прока́тный стан — комплекс оборудования, в котором происходит пластическая деформация металла между вращающимися валками. В более широком значении — система машин, выполняющая не только прокатку, но и вспомогательные операции:
· транспортирование исходной заготовки со склада к нагревательным печам и к валкам стана,
· передачу прокатываемого материала от одного калибра к другому,
· кантовку,
· транспортирование металла после прокатки,
· резку на части,
· маркировку или клеймение,
· правку,
· упаковку,
· передачу на склад готовой продукции и др.
Главный признак, определяющий устройство — его назначение в зависимости от сортамента продукции или выполняемого технологического процесса.
По сортаменту продукции станы разделяют на:
· заготовочные, в том числе станы для прокатки слябов и блюмов,
· листовые и полосовые,
· сортовые, в том числе балочные и проволочные,
· трубопрокатные
· деталепрокатные (бандажи, колёса, оси и т.д.).
Волочение — обработка металлов давлением, при которой изделия (заготовки) круглого или фасонного профиля (поперечного сечения) протягиваются через отверстие, сечение которого меньше сечения заготовки.
В результате поперечные размеры изделия уменьшаются, а длина увеличивается. Волочение широко применяется в производстве пруткового металла, проволоки, труб и другого. Производится на волочильных станах, основными частями которых являются волоки и устройство, тянущее через них металл.
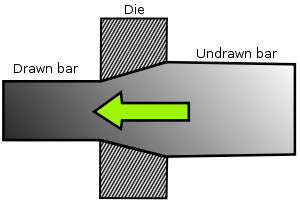
Виды волочения
По типу волочения
· сухое (волочение через ванночку с мыльным порошком)
· мокрое (через мыльную эмульсию)
По чистоте обработки:
· черновое (заготовительное)
· чистовое (заключительная операция, для придания готовому изделию требуемых формы, размеров и качества);
По кратности переходов:
· однократное
· многократное (с несколькими последовательными переходами волочения одной заготовки);
По параллельности обработки:
· однониточное
· многониточное (с количеством одновременно протягиваемых заготовок 2, 4, 8);
По подвижности волоки:
· через неподвижную волоку
· через вращающуюся относительно продольной оси волоку;
По нагреву заготовки:
· холодное волочение
· горячее волочение
Волочильный стан — машина для обработки металлов волочением.
Волочильный стан состоит из двух основных элементов:
· рабочего инструмента — волоки
· тянущего устройства, сообщающего обрабатываемому металлу движение через волоку.
Вращение от двигателя к тянущему устройству передаётся через редуктор. При волочильном стане имеется ряд вспомогательных устройств для механизации и автоматизации производства.
В зависимости от принципа работы тянущего устройства волочильные станы подразделяются на:
· станы с прямолинейным движением обрабатываемого металла
· станы с наматыванием обрабатываемого металла (барабанные).
Волочильные станы с прямолинейным движением обрабатываемого металла применяются для получения прутков и труб, барабанные — для волочения проволоки и металла других профилей, сматываемого на бунты.
Барабанные волочильные станы подразделяются на:
· однократные — с одним ведущим (тянущим) барабаном, в которых волочение металла производится через одну волоку
· многократные — с несколькими барабанами, в которых металл одновременно подвергается волочению через ряд последовательно установленных волок.
получение пустотелого профиля
Производство труб – это изготовление бесшовных металлических труб методом прокатки на специальных станах, которые называют трубопрокатными агрегатами. Трубопрокатное производство подразумевает изготовление горячекатаных (прокатанных в горячем состоянии) и холоднокатаных труб (трубы, подвергающиеся после горячей прокатки прокатке в холодном состоянии).
Чаще всего производство труб состоит из 2 главных и нескольких вспомогательных операций.
· Прошивка Происходит образование продольного отверстия в слитке или в заготовке, из-за чего получается толстостенная труба, которая называется гильзой.
· Раскатка Происходит удлинение уже прошитой заготовки и сокращении толщины её стенки до необходимых в готовой трубе размеров
Эти две операции происходят с одного нагрева. Первая осуществляется на прошивных станах винтовой прокатки между грибовидными и бочкообразными валками на короткой оправке, вторая операция осуществляется на различных прокатных станах: короткооправочных, непрерывных, трёхвалковых, пилигримовых станах винтовой прокатки. После того, как трубы прошли раскатку, они калибруются на калибровочных станах, потом охлаждаются, правятся, подвергаются контролю. Трубы, которые имеют диаметр меньше 7 см, подвергаются дополнительной, на редукционных станах, горячей прокатке.
Для сокращения диаметра и толщины стенки, и получения высших механических характеристик, точных размеров и гладкой поверхности, после горячей прокатки трубы подвергаются холодной прокатке на специальных станах периодической продольной прокатки роликами или валками, а также волочению.
Трубы – это эффективное решение проблемы замены изношенных теплотрасс и резкого уменьшения сверхнормативных потерь теплоносителя.
Процесс подготовки материалов и сырья, производства труб имеет стадии, в ходе которых создаются трубы. Для теплоизоляции труб с бесканальной прокладкой применяется полиэтиленовая оболочка, для труб с надземной прокладкой – спиралевидная оцинкованная оболочка с диаметрами 9 - 14 см.
Прессова́ние (от лат. presso — давлю, жму) — процесс обработки материалов давлением, производимый с целью увеличения плотности, изменения формы, разделения фаз материала, для изменения механических или иных его свойств.
Как правило, для прессования применяют прессы высокого давления. Прессование используют в различных отраслях промышленности, а также в сельском хозяйстве.
Прессование следует отличать от ковки и штамповки.
Пресс — механизм для производства давления с целью уплотнения вещества, выжимания жидкостей, изменения формы, подъёма и перемещения тяжестей, а также для кузнечно-штамповочных работ. По конструкции прессы бывают:
· Валковые
· Винтовые
· Гидравлические
· Клиновые
· Кривошипные
· Листогибочный пресс
· Магнитно-импульсные
· Рычажные
· Эксцентриковые
· Реечные
Древнейшие прессы, например для выбивания оливкового масла, представляли собой камень с обширной выемкой округлой формы. По заполнении этой ёмкости отжимаемым продуктом, сверху опускали другой камень, который силой своего веса отжимал (выбивал) масло, стекавшее через лоток в заготовленную для него ёмкость
Сущность процесса прессования заключается в том, что металл, помещенный в замкнутый объем — контейнер, подвергается высокому давлению и выдавливается сквозь отверстие, принимая его форму.
Ковка — это высокотемпературная обработка различных металлов (железо, медь и её сплавы, титан, алюминий и его сплавы), нагретых до ковочной температуры. Для каждого металла существует своя ковочная температура, зависящая от физических (температура плавления, кристаллизация) и химических (наличия легирующих элементов) свойств. Для железа температурный интервал 1250–800 °С, для меди 1000–650 °С, для титана 1600—900 °С, для алюминиевых сплавов 480–400 °С.
Различают:
· ковка на молотах (пневматических, паровых и гидравлических)
· ручная ковка
· штамповка
Изделия и полуфабрикаты, получаемые ковкой, называют «поковка».
При ковке в штампах металл ограничен со всех сторон стенками штампа. При деформации он приобретает форму этой полости.
При свободной ковке (ручной и машинной) металл не ограничен совсем или же ограничен с одной стороны. При ручной ковке непосредственно на металл или на инструмент воздействуют кувалдой или молотом.
Свободную ковку применяют также для улучшения качества и структуры металла. При проковке металл упрочняется, завариваются так называемые несплошности и размельчаются крупные кристаллы, в результате чего структура становится мелкозернистой, приобретает волокнистое строение.
Машинную ковку выполняют на специальном оборудовании — молотах с массой падающих частей от 40 до 5000 кг или гидравлических прессах, развивающих усилия 2–200 МН (200–20000 тс), а также на ковочных машинах. Изготовляют поковки массой 100 т и более. Для манипулирования тяжёлыми заготовками при ковке используют подъёмные краны грузоподъёмностью до 350 т, кантователи и специальные манипуляторы.
Ковка является одним из экономичных способов получения заготовок деталей. В массовом и крупносерийном производствах преимущественное применение имеет ковка в штампах, а в мелкосерийном и единичном — свободная ковка.
При ковке используют набор кузнечного инструмента, с помощью которого заготовкам придают требуемую форму и размеры.
Штамповка — процесс пластической деформации материала с изменением формы и размеров тела. Чаще всего штамповке подвергаются металлы или пластмассы. Существуют два основных вида штамповки — листовая и объёмная. Листовая штамповка подразумевает в исходном виде тело, одно из измерений которого пренебрежимо мало по сравнению с двумя другими (лист до 6 мм). Примером листовой штамповки является процесс пробивания листового металла, в результате которого получают перфорированный металл (перфолист). В противном случае штамповка называется объёмной. Для процесса штамповки используются прессы — устройства, позволяющие деформировать материалы с помощью механического воздействия.
Сущность способа заключается в процессе, где в качестве заготовки используют полученные прокаткой лист, полосу или ленту, свёрнутую в рулон. Листовой штамповкой изготовляют самые разнообразные плоские и пространственные детали массой от долей грамма и размерами, исчисляемыми долями миллиметра (например, секундная стрелка ручных часов), и детали массой в десятки килограммов и размерами, составляющими несколько метров (облицовка автомобиля, самолёта, ракеты).
Для деталей, получаемых листовой штамповкой, характерно то, что толщина их стенок незначительно отличается от толщины исходной заготовки. При изготовлении листовой штамповкой пространственных деталей заготовка обычно испытывает значительные пластические деформации. Это обстоятельство вынуждает предъявлять к материалу заготовки достаточно высокие требования по пластичности.
При листовой штамповке чаще всего используют низкоуглеродистую сталь, пластичные легированные стали, медь, латунь, содержащую более 60 % Cu, алюминий и его сплавы, магниевые сплавы, титан и др. Листовой штамповкой получают плоские и пространственные детали из листовых неметаллических материалов, таких, как кожа, целлулоид, органическое стекло, фетр, текстолит, гетинакс и др.
Листовую штамповку широко применяют в различных отраслях промышленности, особенно в таких, как авто-, тракторо-, самолето-, ракето- и приборостроение, электротехническая промышленность и др.
К преимуществам листовой штамповки относятся:
возможность получения деталей минимальной массы при заданной их прочности и жёсткости;
достаточно высокие точность размеров и качество поверхности, позволяющие до минимума сократить отделочные операции обработки резанием;
сравнительная простота механизации и автоматизации процессов штамповки, обеспечивающая высокую производительность (30—40 тыс. деталей в смену с одной машины);
хорошая приспособляемость к масштабам производства, при которой листовая штамповка может быть экономически целесообразной и в массовом, и в мелкосерийном производстве.
Горячая объёмная штамповка — это вид обработки металлов давлением, при которой формообразование поковки из нагретой заготовки осуществляют с помощью специального инструмента — штампа. Течение металла ограничивается поверхностями полостей (а также выступов), изготовленных в отдельных частях штампа, так что в конечный момент штамповки они образуют единую замкнутую полость (ручей) по конфигурации поковки. В качестве заготовок для горячей штамповки применяют прокат круглого, квадратного, прямоугольного профилей, а также периодический. При этом прутки разрезают на отдельные (мерные) заготовки, хотя иногда штампуют из прутка с последующим отделением поковки непосредственно на штамповочной машине.
Применение объемной штамповки оправдано при серийном и массовом производстве. При использовании этого способа значительно повышается производительность труда, снижаются отходы металла, обеспечиваются высокие точность формы изделия и качество поверхности. Штамповкой можно получать очень сложные по форме изделия, которые невозможно получить приемами свободной ковки.
Не нашли, что искали? Воспользуйтесь поиском по сайту:
©2015 - 2024 stydopedia.ru Все материалы защищены законодательством РФ.
|