МЕТОДИКА ПРОВЕДЕНИЯ ЭКСПЕРИМЕНТОВ И ОБРАБОТКА РЕЗУЛЬТАТОВ ОПЫТОВ
Федеральное агентство по образованию
Волгоградский государственный технический университет
Кафедра «Материаловедение и композиционные материалы»
МЕТОДЫ И ТЕХНИКА КОНТРОЛЯ МАТЕРИАЛОВ И ПРОЦЕССОВ
Методические указания к лабораторным работам, часть 2-я
РПК
«Политехник»
Волгоград
УДК 621.791
Методы и техника контроля материалов и процессов: метод. указ. к лабораторным работам, часть 2-я / сост. С. П. Писарев; Волгоград. гос. техн. ун-т.-Волгоград, 2007.– 24 с.
Рассматриваются технологические приёмы нанесения защитных эмалевых покрытий на металлические поверхности. Приводятся физические основы магнитно-порошкового метода выявления поверхностных и подповерхностных дефектов стальных изделий. Рассматривается также применение магнитно-отрывного метода для контроля толщины покрытий на стальных изделиях.
Предназначены для студентов, обучающихся по направлению 5518А «Технологические машины и оборудование».
Ил. 4. Табл. 3. Библиогр.: 7 назв.
Рецензент доцент, канд. техн. наук Л. Б. Воеводин
Печатается по решению редакционно-издательского совета
Волгоградского государственного технического университета
© Волгоградский
государственный
технический
университет, 2007
ЛАБОРАТОРНАЯ РАБОТА 1
КОНТРОЛЬ КАЧЕСТВА ЭМАЛЕВЫХ ПОКРЫТИЙ
1. ЦЕЛЬ РАБОТЫ
Ознакомление с методами нанесения эмалевых покрытий на металлические поверхности и контроля их качества. Получение практических навыков по применению методов контроля технологических параметров процесса для определения оптимальных режимов нанесения покрытия.
2. СОДЕРЖАНИЕ РАБОТЫ
2.1. Ознакомление с методическими указаниями к лабораторной работе, применяемым оборудованием и поставленной задачей.
2.2. Подготовка исследуемых материалов и оборудования к проведению
опытов.
2.3. Проведение экспериментальных исследований по нанесению эмалевого покрытия на поверхность стальной пластины с контролем его толщины и качества.
2.4. Обработка результатов опытов, составление отчета по лабораторной
работе.
3. ТЕОРЕТИЧЕСКАЯ ЧАСТЬ
При производстве точных стальных заготовок методами штамповки, прессования происходит образование дефектного окисленного слоя, что требует назначения припусков на механическую обработку, а это, в свою очередь, увеличивает трудоемкость изготовления изделий и долю металла, идущего в отходы. Окисление при высоких температурах, обезуглероживание и загрязнение газами поверхности металлов и сплавов существенно влияет на коэффициент использования металла, который является важнейшим показателем технического прогресса и культуры производства в металлообрабатывающих отраслях промышленности.
Для защиты поверхности металлов от окисления в условиях нагрева и при обычных температурах широко применяют защитные эмалевые покрытия. Эмали обычно представляют собой стекловидный твердый раствор кремнезёма, глинозёма и других оксидов. Некоторые из них: оксид свинца, оксид калия, оксид натрия - увеличивают легкоплавкость эмалей, но в то же время делают их менее стойкими против внешних воздействий. Другие соединения: оксид кремния, оксид алюминия, оксид магния, наоборот, увеличивают прочность эмалей и их тугоплавкость. Для получения цветных эмалей добавляют оксиды металлов (свинца, кобальта, никеля и др.), которые называются пигментами. Технологическая схема получения эмалевых покрытий включает следующие основные операции: подготовка сырьевых материалов (сушка, измельчение, просеивание, прокаливание и др.), приготовление шихты, плавка и грануляция полученной фритты, подготовка мельничных добавок (прокаливание, дробление, отбор фракций и др.), приготовление шликера (отвешивание компонентов шликера, мелющих тел, загрузка барабана шаровой мельницы, помол и др.), контроль свойств шликера, подготовка поверхностей деталей к нанесению шликера, сушка шликерного слоя покрытия, контроль качества нанесения шликерного слоя, обжиг эмали и контроль качества эмалевого покрытия.
Заданные свойства эмалевых покрытий получают за счет применения в составе шликера эмалевых фритт, являющихся сложным сплавом окислов со структурой силикатного стекла.
Для обеспечения седиментационной устойчивости эмалевых шликеров в их состав вводят глину. В смеси с водой и тонкодисперсными частицами фритты глина образует вязкую, но хорошо текучую массу. При взаимодействии с водой глина образует коллоидный раствор, оседание частичек фритты в котором сильно замедляется.
Тугоплавкость покрытий повышают введением в шликер керамических материалов. Используют чистые окислы (окись алюминия, двуокись циркония, окись хрома), химически стойкие с высокой температурой плавления, и соединения тугоплавких окислов типа шпинели, циркона.
Бескислородные керамические материалы и соединения — бориды, нитриды, силициды, карбиды, тонкодисперсные порошки металлов вводят в шликер с целью придания покрытиям специальных технологических и эксплуатационных свойств (адгезии, коэффициента линейного термического расширения, теплоизолирующих, смазывающих и т. п. свойств), а также для обеспечения процессов реакционного спекания, отверждения покрытий.
Контролируют гранулометрический состав исходных компонентов и отбирают фракцию, просеивая порошки через сито с ячейкой заданного размера. Для размола используют обычно гранулы фритты, частички стекла, керамики, просеянные через сито со стороной ячейки <2,5 мм.
Для приготовления шликера используют также сухой способ размола. Этот способ оказывается необходимым и эффективным в тех случаях, когда шликер обладает низкой седиментационной устойчивостью и склонностью цементироваться при оседании. Размол производят в шаровых мельницах периодического действия. Барабан мельницы из стали футеруют керамическими плитками. Фарфоровые барабаны применяют для приготовления шликера на валковых мельницах.
В качестве мелющих тел используют алундовые, фарфоровые дроты и шары, кремниевую гальку, кварцевые дроты. Соотношение масс мелющих тел и размалываемой сухой смеси должно выдерживаться в пределах 1,2. Барабан мельницы загружают не более чем на 3/4 его объема.
В зависимости от размеров и твердости размалываемых частиц изменяется продолжительность размола. Фритты и стекла с частицами размером ~2,5 мм размалывают в течение 48 ч. При загрузке в барабан частиц размером 50—100 мкм продолжительность размола обычно не превышает 15 ч. Если же в составе порошка доля частиц указанного размера не превышает 20—30 %, то вместо размола осуществляют перемешивание смеси из частиц фритты, специальных добавок, воды для получения суспензии (шликера) заданной вязкости.
Крупные гранулы, кусочки фритты, стекла измельчают на прессах в металлических пресс-формах с последующим отбором мелких фракций просеиванием через сито. Порошки с частицами размером ~ 50 мкм получают дроблением кусков стекла на вибрационных мельницах, что сопряжено с возможным загрязнением фритт и стекол железом.
Приготовлению шликера тугоплавких эмалей, реакционноспекаемых и реакционноотверждаемых покрытий нередко предшествуют специальная обработка исходных материалов и тщательный контроль их химического состава. В частности, стекло подвергают химической обработке в кислоте для удаления частичек железа. Металлические, интерметаллидные, силицидные, боридные порошки подвергают химической, термической, магнитной обработке с целью очистки от примесей или оставшихся исходных компонентов, не связанных в основное соединение. Для приготовления шликера указанных покрытий используют валковые мельницы с барабанами, футерованными не загрязняющими шликер материалами и соответствующие мелющие тела.
Исходные материалы (фритты, металлические порошки, окислы) для технологических покрытий на органосиликатной основе необходимо просушивать перед введением в лаки типа КО-08 и растворители. Например, окись хрома следует нагреть в печи до 900 °С и выдерживать при этой температуре 2 ч. Тонкодисперсные порошки стекол и фритт, хрома, титана необходимо просушить при повышенной (100—300 °С) температуре 3—5 ч, чтобы получить однородный шликер и обеспечить стабильные свойства покрытий.
Перед эмалированием детали очищают от жировых и других загрязнений, подвергают пескоструйной обработке для создания шероховатой поверхности. Обезжиривают детали бензином, в щелочных ваннах. В щелочном растворе из смеси кальцинированной технической соды (30 - 40 г/л), жидкого натриевого стекла (30 - 40 г/л) и натра едкого (5 - 10 г/л) при 50-80 0С детали обрабатывают в течение 10 - 30 мин в зависимости от их загрязнённости. Затем их промывают в теплой и холодной воде, сушат до полного удаления влажных пятен. Для пескоструйной обработки используют сухой электрокорунд (ГОСТ 3647-80), который подают на поверхность деталей под давлением 29 – 59 МПа.
На подготовленную поверхность деталей эмалевый шликер наносят: краскораспылителем, окуная детали в шликер, обливая, или заливая их для получения шликерного слоя толщиной 100 - 200 мкм. Сушку нанесённого слоя проводят в сушильном шкафу, на воздухе в течение 30 - 60 мин в зависимости от габаритов, массы и конфигурации деталей. При контроле качества шликерного слоя, выявляют: подтеки, наплывы, непокрытые места, сколы, трещины и т.п. дефекты, которые устраняют затиркой, подкраской повторным нанесением шликера.
Подготовка к обжигу эмалевого покрытия заключается в установке и закреплении деталей в оснастке для обжига, контролировании температуры и чистоты в рабочем пространстве печи. Температура и время обжига устанавливаются в зависимости от массы, габаритов детали, и для эмалей различных марок подбираются, экспериментально. Обычные температуры обжига - 700 - 900 0С, а эмали для жаропрочных сплавов обжигают при 1150 - 1250 0С.
Контроль качества эмалевого покрытия обычно включает визуальный осмотр на соответствие эталону по цвету, сплошности и блеску. Контролируется наличие пузырей, сколов, трещин, непокрытых мест, наплывов, подтёков, разнотонности и т.п. Замеряется также толщина покрытия. Незначительные дефекты устраняют, применяя ремонтные покрытия типа ЭВР, получаемые холодной сушкой. При подготовке к ремонту дефектное место обрабатывают наждачной бумагой и обезжиривают. Ремонтное покрытие наносят мягкой кистью тонким ровным слоем и сушат в течение трёх часов.
Для повышения качества эмалевого покрытия наносят второй и даже третий слой эмали на имеющийся обожженный слой, либо первый слой удаляют пескоструйной очисткой, а затем деталь эмалируют повторно.
4. ЛАБОРАТОРНОЕ ОБОРУДОВАНИЕ И МАТЕРИАЛЫ ДЛЯ ПРОВЕДЕНИЯ ОПЫТОВ
4.1. Сухой шликер грунтовой эмали следующего состава в весовых процентах:
SiO2 – 54,2%, CaF2 – 7,8%, NiO – 1,1%, TiO2 – 0,8%, Al2O3 – 3,8%,
CaO – 0,5%, BaO – 9,7%, Na2O – 20,5%, MnO2 – 0,4%, B2O3 – 1,2%..
4.2. Пластины из стали Ст 3 размером 100х (50-100)х (2-4) мм.
4.3. Стеклянная посуда для приготовления шликерной массы.
4.4. Обезжиривающий раствор.
4.5. Наждачная бумага.
4.6. Электропечь с температурой нагрева до 950 0С и сушильный шкаф (с рабочей температурой до 200 0С);
4.7. Секундомер.
4.8. Наждачный станок.
4.9. Микроскоп МБС-9.
4.10. Микрометр.
4.11. Щипцы для перемещения образцов.
4.12. Защитные очки.
4.13. Милливольтметр с термопарой для измерения температуры.
4.15. Инструменты для нанесения шликера.
МЕТОДИКА ПРОВЕДЕНИЯ ЭКСПЕРИМЕНТОВ И ОБРАБОТКА РЕЗУЛЬТАТОВ ОПЫТОВ
5.1. Определить цель и задачу исследования, ознакомиться с
методическими указаниями, применяемым оборудованием и инструментами.
5.2. Подготовить поверхность стальной пластины для нанесения шликера, измерить толщину заготовки.
5.3. Приготовить эмалевый шликер и нанести его на подготовленную поверхность пластины, просушить в течение 10 – 15 мин при 80 – 100 0С.
5.4. Осуществить промежуточный контроль качества шликерного слоя визуально и с помощью микроскопа марки МБС-9, устранить дефекты. Измерить суммарную толщину заготовки с покрытием на всей её длине, определить распределение толщины покрытия по длине стальной пластины. Результаты занести в таблицы I-2.
5.5. Произвести обжиг покрытия в электропечи при 850 0С в течение
10 мин.
5.6. Провести контроль качества полученного покрытия и его толщины как в п. 5.4. Результаты занести в таблицы I-2.
5.7. Произвести повторный обжиг покрытия в электропечи при 850 0С в течение 20 мин, проконтролировать его качество как в п. 5.6. Выбрать оптимальный временной режим обжига эмали.
5.8 В качестве второго варианта исследований может быть варьирование температуры обжига в пределах 700-900 0С при фиксированном времени выдержки (I0 - 20 мин). Здесь по результатам контроля качества покрытия требуется определить оптимальную температуру обжига.
Таблица I - Свойства эмалевых покрытий в зависимости от режимов
термообработки.
N0
оп.
| Температура обжига, 0С
| Время обжига, мин
| Результаты контроля качества эмалевых
Покрытий
|
|
|
|
|
|
|
|
|
|
|
|
|
|
|
|
|
Таблица 2 – Изменение толщины эмалевого покрытия при обжиге
№ оп.
| Х, мм
| И+П1, мм
| П1, мм
| И+П2, мм
| П2, мм
| И+П3, мм
| П3, мм
|
|
|
|
|
|
|
|
|
|
|
|
|
|
|
|
|
|
|
|
|
|
|
|
|
|
|
|
|
|
|
|
|
|
|
|
|
|
|
|
|
|
|
|
|
|
|
|
|
|
|
|
|
|
|
|
|
|
|
|
|
|
|
|
|
|
|
|
|
|
|
|
|
|
|
|
|
|
|
|
|
|
|
|
|
|
|
|
|
|
|
|
|
|
|
|
|
|
|
|
|
|
|
|
|
|
|
|
|
|
|
|
| Примечание: И – толщина изделия, П1 – толщина покрытия до обжига, П2 – после обжига при температуре 850 оС в течение t=10 мин, П3 – после обжига при 850 оС, t=20 мин.
|
5.9 Сделать общие выводы о влиянии режимов термообработки на качество эмалевого покрытия. Построить графики распределения толщины покрытий по длине изделия для использованных режимов их получения.
6. СОДЕРЖАНИЕ ОТЧЁТА
Отчет по данной работе должен содержать описание методики нанесения эмалевых покрытий, результаты контроля качества покрытия, методику контроля, зарисовки поверхности образцов, выводы о влиянии, режимов обжига на качестве покрытий графики распределения толщины покрытий по длине стальной пластины.
7. КОНТРОЛЬНЫЕ ВОПРОСЫ
7.1. Расскажите о назначении эмалевых покрытий.
7.2. Как производится подготовка поверхности изделий для нанесения эмалевых покрытий?
7.3. Какие компоненты могут входить в состав эмалевого шликера?
7.4. Расскажите о методах подготовки порошковых составляющих при получении шликера.
7.5 Каким требованиям должен удовлетворять шликер перед его нанесением на поверхность заготовки?
7.6. Рассказать о способах нанесения шликера на поверхность детали и методах контроля качества.
7.7. С какой целью проводится обжиг покрытия? Что происходит в шликере во время обжига?
7.8. Как осуществляется контроль качества эмалевых покрытий?
ЛАБОРАТОРНАЯ РАБОТА 2
МАГНИТНЫЕ МЕТОДЫ КОНТРОЛЯ
1. ЦЕЛЬ РАБОТЫ
Освоить методики выявления дефектов магнитно-порошковым методом, а также методы контроля толщины покрытий магнитно-отрывным методом.
2.СОДЕРЖАНИЕ РАБОТЫ
2.1. Ознакомление с методическими указаниями к лабораторной работе и поставленной задачей.
2.2. Ознакомление с лабораторным оборудованием и коллекцией исследуемых материалов.
2.3. Проведение экспериментов по выявлению дефектов в стальных изделиях магнитно-порошковым методом.
2.4. Проведение опытов по контролю толщины покрытий магнитно-отрывным методом.
2.5. Обработка полученных результатов, составление отчёта по лабораторной работе.
3. ТЕОРЕТИЧЕСКАЯ ЧАСТЬ
3.1. Магнитная порошковая дефектоскопия
Магнитная порошковая дефектоскопия основана на выявлении магнитного поля рассеяния, возникающего около дефекта, ферромагнитными частицами. В намагниченном изделии магнитные силовые линии, встречая трещины, флокены, волосовины и другие несплошности, огибают их, как препятствия с малой магнитной проницаемостью. Образующиеся поля рассеяния неоднородны. Поэтому ферромагнитные частицы затягиваются полем и оседают на контролируемой поверхности. Форма скоплений частиц порошка соответствует очертаниям выявляемых дефектов (рис. 1).
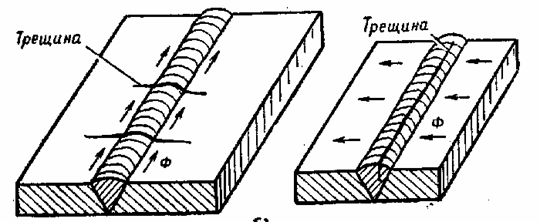
Рис. 1. Осаждение магнитного порошка на сварных соединениях:
а-на поперечных трещинах, б-на сварном шве.
В магнитопорошковой дефектоскопии наиболее часто используются железные порошки, получаемые или термическим разложением соединений железа, например Fе02 СО5, или распылением железа в керосине с помощью электрической дуги, а также порошки из окалины железа, отходов стали, магнетита, ферромагнитной окиси железа, из феррита.
Для увеличения контрастности изображения применяют порошки желтого, красного и светло-желтого цвета. Разрабатываются и применяются люминесцирующие порошки. Обычно порошок применяют в виде суспензии. Магнитная суспензия - это взвесь ферромагнитных частиц в жидкости (воде, минеральных маслах, керосине). Применение порошков из никеля и кобальта весьма ограничено из-за их высокой стоимости.
При контроле детали намагничивают в поле постоянного или переменного тока, пропуская через деталь или медный стержень ток большой силы. Деталь намагничивается циркулярным магнитным полем в плоскости, перпендикулярной к направлению тока. Если деталь поместить в поле соленоида или электромагнита, то создается продольное или поперечное намагничивание. Применяют также комбинированное намагничивание одновременно продольным постоянным и поперечным циркулярным полем и более сложное намагничивание, например, трехфазным током. Некоторые примеры приведены на рис. 2-3.
Метод магнитного порошка применяют для контроля деталей, прошедших окончательную механическую и термическую обработку. Чувствительность метода в значительной степени зависит от размера частиц применяемого порошка и его магнитных свойств, напряжённости приложенного намагничивающего поля, формы и величины дефектов, а также их расположения по отношению к поверхности изделия и направлению намагничивания, состояния и формы поверхности контролируемого изделия.
Размеры частиц порошка во много раз сильнее влияют на чувствительность метода, чем магнитные свойства. С увеличением напряжённости приложенного поля (до достижения индукции насыщения) возрастает чувствительность метода, проявляющаяся в увеличении количества обнаруживаемых дефектов. При соблюдении оптимальных условий ведения контроля магнитно-порошковый метод имеет высокую чувствительность к тонким и мелким трещинам. Он позволяет выявлять поверхностные и подповерхностные дефекты с раскрытием от 0,01 мм и глубиной (высотой дефекта) от 0,05 мм и более. Дефекты округлой формы (например поры) выявляются значительно хуже.
Методом магнитно-порошкового контроля хорошо выявляются поверхностные и подповерхностные дефекты типа трещин, непроваров, несплавлений, волосовин, закатов, включений. Могут также выявляться сравнительно крупные дефекты, расположенные на глубине до 6 мм от поверхности. Наиболее чётко выявляются дефекты, наибольший размер которых ориентирован под прямым или близким к нему углом относительно направления магнитного потока.
Если на поверхности контролируемого изделия, кроме полей от дефектов, имеются значительные градиенты магнитных полей структурного или геометрического происхождения (например, наличие усилительного валика сварного шва, чешуйчатость на его поверхности, резкое изменение сечения детали и т.п.), то магнитный порошок интенсивнее скапливается не над дефектами, а в местах со значительными градиентами магнитного поля. Следовательно, по осаждению магнитного порошка на поверхности детали нельзя однозначно судить о наличии дефектов сплошности. Поэтому при контроле изделий с грубой поверхностью чувствительность магнитно-порошкового метода невысока, особенно к внутренним дефектам.
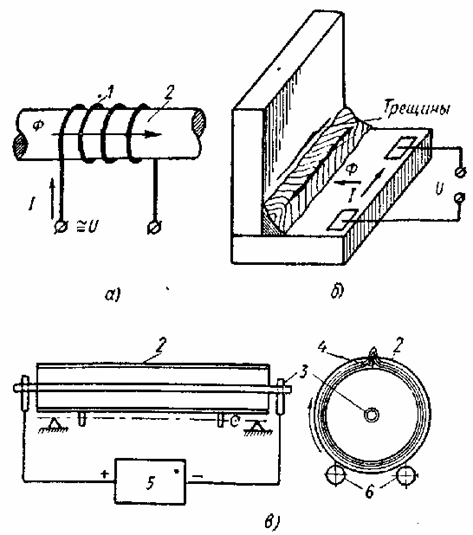
Рис. 2. Схемы намагничивания изделий в магнитно-порошковом контроле:
а-соленоидом, б-пропусканием тока через изделие, в-пропусканием тока через стержень; 1- соленоид, 2-контролируемое изделие, 3-стержень с током, 4- дефект, 5-источник тока, 6-опорные ролики.
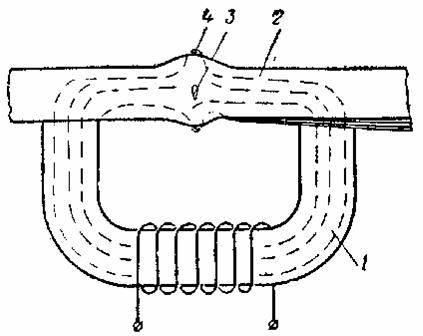
Рис. 3. Намагничивание приставным электромагнитом: 1-магнитопровод, 2-контролируемое изделие, 3-дефект, 4-осаждённый порошок.
Контроль можно проводить, покрывая поверхность изделия порошком в процессе намагничивания (в приложенном поле; или нанося магнитный порошок на поверхность предварительно намагниченного до насыщения изделия, то есть используя остаточную намагниченность.
Первым из указанных способов обычно контролируют изделия из магнитно-мягких материалов с коэрцитивной силой Нсдо 8—10 А/см, а вторым - изделия из сравнительно магнитно-твердых материалов с коэрцитивной силой свыше 10—15 А/см.
Контролируемые изделия намагничивают постоянным, пульсирующим (импульсным), или переменным полем. При намагничивании постоянным полем внутренние дефекты выявляются лучше, чем при намагничивании переменным. Однако в ряде случаев (например, в цеховых условиях) отдают предпочтение намагничиванию переменным полем. Это объясняется тем, что от сети переменного тока через понижающий трансформатор можно непосредственно получить достаточно большую силу намагничивающего тока и создать большую напряженность магнитного поля Н. Однако при использовании переменного поля основной магнитный поток под влиянием скин-эффекта, вызываемого вихревыми токами, вытесняется на поверхность металла, вследствие чего сильнее намагничиваются его поверхностные слои и лучше выявляются наружные и подповерхностные дефекты (например, закалочные или усталостные трещины и др.). Это особенно важно учитывать при контроле крупных и толстостенных деталей.
Импульсное униполярное намагничивание наиболее предпочтительно при контроле в режимах остаточной намагниченности изделия. При контроле на остаточной намагниченности применяют следующие четыре режима:
1. Режим отбраковки деталей по грубым дефектам, при котором поле на поверхности деталей около 30 А/см. Этим режимом пользуются для контроля деталей с грубой обработанной поверхностью, а также при междуоперационном контроле перед последующей обработкой поверхности деталей.
2. Режим пониженной жесткости, при котором на поверхности детали должно быть около 60 А/см.
3. Стандартный режим, при котором на поверхности контролируемой детали должна быть обеспечена напряженность магнитного поля около 100 А/см.
4. Режим повышенной жесткости, при котором на поверхности детали обеспечивается напряженность поля около 180—200 А/см.
После контроля намагниченные детали часто должны быть размагничены. Если деталь при контроле намагничивалась переменным током, то ее размагничивают в специальных камерах или с помощью специальных электромагнитов (размагничивающих устройств), питаемых переменным током.
При намагничивании деталей постоянным током их размагничивают в постоянном поле с переменным изменением его направления и плавным уменьшением напряженности до нуля. Начальная напряженность размагничивающего поля соленоида устанавливается несколько больше напряженности поля, при котором деталь намагничивалась для контроля.
Ввиду сложности расчетов и невозможности учесть все существенно влияющие факторы, для определения режимов контроля применяют образцы с эталонными дефектами и специальные «свидетели» намагниченности, которые представляют собой плоские пластинки из материала контролируемых деталей, прикладываемые к поверхности последних во время намагничивания.
Методика магнитопорошкового метода сводится к следующим основным операциям:
1. Подготовка поверхностей перед контролем. Очистка от загрязнений, окалины, следов шлака после сварки;
2. Подготовка суспензии, заключающаяся в интенсивном перемешивании магнитного порошка с транспортирующей жидкостью;
3. Намагничивание контролируемого изделия;
4. Нанесение суспензии на поверхность контролируемого изделия;
5. Осмотр поверхности изделия и выявление мест, покрытых отложением порошка.
В сомнительных случаях валик порошка удаляют и повторяют операции 3, 4 и 5. После контроля изделие размагничивают.
Магнитопорошковый метод получил весьма широкое распространение. Это обусловлено его основными преимуществами: высокой чувствительностью к тонким и мелким трещинам, простотой методики, оперативностью получения результатов контроля и их наглядностью.
В отечественной и зарубежной практике этот метод применяется для контроля продольных сварных швов труб, выполненных стыковой электроконтактной сваркой, а также для выявления трещин и узких (стянутых) непроваров в стыковых швах трубопроводов, сваренных электродуговыми способами. В обоих этих случаях усиления швов перед контролем снимают.
В магнитно-люминесцентном методе, в отличие от магнитно-порошкового метода дефектоскопии, к магнитному порошку добавляют люминофор, окрашивающий частицы магнитного порошка и вызывающий яркое свечение их в ультрафиолетовых лучах. Для приготовления суспензии применяют магнитный порошок люмагпор-1, порошок с люмогеном или антраценом, а также пасты МЛ-1 и МЛ-2 (смеси магнитных порошков с люмогеном, антивспенивающей, антикоррозионной и смачивающей добавками). В качестве жидкой среды используют воду, водные растворы с антикоррозионными, антивспенивающими и смачивающими добавками, керосин и очищенные нелюминисцирующие масла типа РМ. Концентрация магнитного порошка в суспензии 4 ± 1 г/л, концентрация пасты 32 г/л. По магнитно-люминесцентному методу контролируемые изделия вначале тщательно обезжиривают, а затем намагничивают и покрывают суспензией. Наличие дефектов устанавливают по яркому свечению .магнитного порошка в местах его скоплений. Методом магнитно-люминесцентной дефектоскопии выявляют поверхностные и близкие к поверхности дефекты с шириной раскрытия 0,1-0,01 мкм.
3.2. Магнитно-отрывной метод контроля
Этот метод основан на измерении силы притяжения подвижного магнита или сердечника электромагнита к поверхности контролируемой детали, либо на измерении тока, протекающего через катушку электромагнита в момент его отрыва от изделия. Метод используется для измерения толщины немагнитных или слабомагнитных покрытий на ферромагнитных деталях, для определения процентного содержания α-фазы в аустенитных сталях и др.
4. ЛАБОРАТОРНОЕ ОБОРУДОВАНИЕ И МАТЕРИАЛЫ ДЛЯ ПРОВЕДЕНИЯ ОПЫТОВ
4.1. Коллекция исследуемых материалов с поверхностными и внутренними дефектами.
4.2. Магнитные порошки для выявления дефектов.
4.3. Постоянный магнит и электромагнит.
4.5. Жидкость для приготовления магнитной суспензии.
4.6. Установка для определения толщины покрытий магнитно-отрывным методом (рис. 1)
5. МЕТОДИКА ПРОВЕДЕНИЯ ЭКСПЕРИМЕНТОВ И ОБРАБОТКА РЕЗУЛЬТАТОВ ОПЫТОВ
5.1. Ознакомиться с методическими указаниями и применяемым оборудованием.
5.2. Подготовить поверхности контролируемых изделий, произвести их очистку от загрязнений.
5.3. Подготовить магнитную суспензию и нанести её на поверхность контролируемого изделия.
5.4. Намагнитить контролируемое изделие приставным магнитом или электромагнитом.
5.5. Произвести осмотр поверхности изделия, выявить места скоплений частиц порошка.
5.6. Зарисовать наблюдаемые картины.
5.7. Получить коллекцию стальных образцов с покрытиями различной толщины.
5.8. С помощью установки, показанной на рис. 1 проконтролировать ток в момент отрыва от поверхности изделия. Полученные экспериментальные данные занести в таблицу 1.
5.8. Построить экспериментальную зависимость тока в момент отрыва электромагнита от поверхности изделия от толщины покрытия.
5.9. Проанализировать полученные результаты.
Рис. 1. Установка для контроля толщины покрытий магнитно-отрывным
методом: 1-сердечник электромагнита, 2-обмотка, 3- покрытие, 4-стальное изделие, АТР-автотрансформатор, Тр-понижающий трансформатор, VD1-VD4-диоды, А-амперметр.
Таблица 1-Зависимость тока в момент отрыва электромагнита от поверхности изделия от толщины покрытия
Номер
опыта
| Х
мм
| Ток в момент отрыва, А
| ΔI/Iо
| Примечание
| I1
| I2
| I3
| Iср
| ΔI
|
|
|
|
|
|
|
|
|
|
|
|
|
|
|
|
|
|
|
|
|
|
|
|
|
|
|
|
|
|
|
|
|
|
|
|
|
|
|
|
|
|
|
|
|
|
|
|
|
|
|
|
|
|
|
|
|
|
|
|
|
|
|
|
|
|
|
|
|
|
|
|
|
|
| 6. СОДЕРЖАНИЕ ОТЧЁТА
Отчёт по данной работе должен содержать методику контроля изделий магнитно-порошковым методом, зарисовки изделий с отложениями порошка, методику контроля изделий магнитно-отрывным методом, график зависимости тока в момент отрыва от толщины покрытия.
7. КОНТРОЛЬНЫЕ ВОПРОСЫ
7.1. Расскажите о диамагнетиках, парамагнетиках и ферромагнетиках.
7.2 Расскажите о принципиальных основах магнитно-порошкового метода.
7.3. Какие материалы и оборудование используют при магнитно-порошковом методе?
7.4. Расскажите о возможностях магнитно-отрывного метода.
7.5. Расскажите об устройстве установки для контроля толщины покрытий магнитно-отрывным методом.
СПИСОК РЕКОМЕНДУЕМОЙ ЛИТЕРАТУРЫ
1. Б.Г.Лившиц, В.С.Крапошин, Я.Л.Линецкий. Физические свойства металлов и сплавов. М.; “Металлургия”, 1980, с. 3-5, 133-203.
2. Металловедение и термическая обработка стали (справочник), т.1, под
редакцией М.Л.Бернштейна и А.Г.Рахштадта. М.; “Металлургия”, 1983, с. 275-276, 292-298.
3. С.В.Румянцев, В.А.Добромыслов, О.М.Борисов, Н.Т.Азаров.
Неразрушающие методы контроля сварных соединений. М.;
Машиностроение, 1976, с. 335.
4. Солнцев С.С. Защитные технологические покрытия и тугоплавкие эмали. М.: Машиностроение, 1984. - 256 с.
5. А.А. Аппен. Термоустойчивые неорганические покрытия. Л.: Химия, 1976. - 295 с.
6. Ю.Д. Баринов, Г.И. Беляев, С.М. Пономарчук. Эмалирование металлов. Киев, Гостехиздат, 1962. - 107 с.
7. Контроль качества сварки. Учебное пособие для машиностроительных вузов под ред. В. Н. Волченко. М., «Машиностроение», 1975, 328 с.
Составитель Сергей Петрович Писарев
МЕТОДЫ И ТЕХНИКА КОНТРОЛЯ МАТЕРИАЛОВ И ПРОЦЕССОВ
Методические указания к лабораторным работам, часть 2-я
Темплан 2007г., поз.№ 98 . Подписано в печать 13.02.07 . Формат 60х84 1/16. Бумага газетная. Печать офсетная. Усл. печ. л. 1,4 . Тираж 100 экз.
Заказ 109 .Бесплатно.
Не нашли, что искали? Воспользуйтесь поиском по сайту:
©2015 - 2025 stydopedia.ru Все материалы защищены законодательством РФ.
|