Описание технологического процесса
РЕГЕНЕРАЦИЯ АММИАКА В ПРОИЗВОДСТВЕ КАЛЬЦИНИРОВАННОЙ СОДЫ
Методические указания
к лабораторной работе по курсу «Промышленная экология» для студентов специальности 280201 «Охрана окружающей среды и рациональное использование природных ресурсов»
дневной и заочной формы обучения
Барнаул 2010
УДК 66.02
Горелова, О.М., Сомин, В.А. Регенерация аммиака в производстве кальцинированной содыМетодические указания к лабораторной работе по курсу «Промышленная экология» для студентов специальности 280201 «Охрана окружающей среды и рациональное использование природных ресурсов» / Алт. гос. техн. ун-т им. И.И.Ползунова. – Барнаул: Изд-во АлтГТУ, 2010. – 23 с.
В методических указаниях приводится теоретическая часть, в которой изложены основы технологического процесса производства кальцинированной соды, пути снижения отходов и энергозатрат в содовом производстве, описана методика выполнения работы.
Рассмотрены и одобрены на
заседании кафедры
«Химической техники и
инженерной экологии» АлтГТУ
Протокол № 2 от 27.09.2010
- ТЕОРЕТИЧЕСКАЯ ЧАСТЬ
Кальцинированная сода - угленатриевая соль – Na2CO3. Около половины производимой кальцинированной соды идет на изготовление стекла, около четверти – химикатов, 13% - мыла и моющих средств, 11% употребляется на такие цели, как изготовление целлюлозы и бумаги, рафинирование металлов и нефти, дубление кожи и очистку воды, а остальное поступает в продажу.
Основной промышленный способ производства кальцинированной соды – метод Сольве.Сущность этого метода состоит в насыщении соляных растворов аммиаком и углекислым газом и переработке получающегося при этом осадка бикарбоната на кальцинированную соду посредством прокаливания.
Сырье для производства кальцинированной соды
Хлорид натрия (рассол)
В аммиачном способе производства соды применяют не твердую соль, а рассол, что является большим преимуществом, так как добыча рассола путем подземного выщелачивания соли водой значительно дешевле добычи твердой соли обычным шахтным способом. Использование для приготовления рассола твердой соли, поднятой на поверхность земли, допустимо только в тех случаях, когда поваренная соль является отходом производства.
Рассол при подземном выщелачивании соли имеет температуру порядка 15ºС. При этой температуре он содержит около 317 г/л NaCl. Однако получать насыщенный раствор довольно трудно. Для этого требуется длительное время, так как с приближением к состоянию насыщения скорость растворения NaCl сильно уменьшается. Практически можно получать рассол с концентрацией 305 – 310 г/л.
Различают рассолы естественные и искусственные. Первые получаются в результате растворения пластов каменной соли подпочвенными водами. Соль залегает обычно на глубине 200 – 300 м. Наличие грунтовых вод приводит иногда к тому, что размывание соляных пластов происходит под землей естественным образом, в результате чего под землей образуются большие озера с насыщенным рассолом.
Искусственный рассол добывается из подземных глубин с помощью буровых скважин (рисунок 1). Скважину сверлят до основания соляного пласта. Для защиты ее от обвалов осадочных пород вставляют так называемую обсадную трубу. Внутри обсадной трубы вставляют центральную трубу почти до основания соляного пласта. Когда в пласте соли образуется достаточно большая размытая камера, приступают к нормальной эксплуатации скважины. Воду подают по кольцевому пространству в верхнюю часть камеры, а концентрированный рассол поднимается по центральной трубе. В процессе эксплуатации скважины, камера увеличивается и достигает расположенных сверху осадочных пород, которые намокают, падают на дно камеры и приводят к забивке скважины.
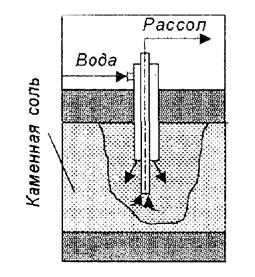
Рисунок 1 – Подземное выщелачивание хлорида натрия
Более совершенным способом добычи рассола является так называемый метод гидровруба, при котором у основания соляного пласта при помощи воды создают вруб, т.е. размыв пласта в ширину до диаметра 100 – 110 м и высотой 1,5 – 2 м. Чтобы обеспечить растворение пласта соли вширь и предохранить от растворения потолок образующейся камеры, в скважину вводят воздух или нефтяные продукты, например мазут, которые, всплывая, образуют между потолком камеры и водой изолирующий слой, препятствующий растворению соли. Слой мазута или нефти поддерживают около 1 см. Таким образом, соль будет растворяться только с боков камеры. Такая предварительная подготовка камеры длится 1,5 – 2 года, после чего начинается нормальная ее эксплуатация.
На заводе рассол хранят в стальных резервуарах емкостью 2000 – 3000 м3. Для защиты от коррозии эти резервуары внутри футеруют слоем бетона, армированного стальной сеткой. Рассол хранят также в бревенчатых срубах, которые могут служить многие годы.
Известняк и мел
Более предпочтительным сырьем является известняк, т.к. мел - пористая порода, он легко впитывает влагу, нарушая нормальный ход обжига его в известковых печах.
Обычно считается, что наилучшим сырьем является известняк с содержанием от 92% CaCO3, влаги от 1 до 5% и минимальным количеством силикатов. Размер кусков извести, поступающей на обжиг - около 60 - 150 мм. Содержание CaCO3 не должно быть ниже 80 % масс., влаги - не выше 5%, чтобы печной газ не разбавлялся водяным паром.
Добыча известняка и мела ведется в карьерах методом открытых разработок.
Куски, имеющие размер меньше 40 мм, составляют отход, который может быть использован, например, на строительных работах, в производстве цемента, в металлургической промышленности или же для получения извести в специально выделенных для обжига мелочи печах.
Аммиак.
В производстве соды аммиак после регенерации в отделении дистилляции возвращают обратно в производственный цикл. Неизбежные при этом потери компенсируются введением аммиачной воды. Аммиачная вода поступает с заводов синтетического аммиака, а также с коксохимических заводов.
Аммиак хорошо растворяется в воде и рассоле. При этом плотность раствора понижается, а объем его увеличивается.
Топливо.
В производстве кальцинированной соды топливо применяют в известковых печах при получении извести и в содовых печах при кальцинации бикарбоната натрия (NaHCO3).
В содовом производстве чаще всего используется кокс второго сорта в смеси с коксом третьего сорта.
Также возможно применение в качестве топлива для обжига карбонатного сырья природного газа. Это наиболее дешевое беззольное высококалорийное топливо.
Вода
На содовых заводах воду расходуют в основном для охлаждения жидкостей и газов. Сравнительно меньше ее расходуют на чисто технологические нужды, например на приготовление рассола, известкового молока и т.д. Воду расходуют также на питание паровых котлов, производящих пар для отгонки аммиака в отделении дистилляции, для паровых машин, если они имеются на заводе, и для отопления помещений.
Качество воды характеризуется содержанием растворенных в ней солей и газов. Особое внимание уделяется «солям жесткости».
Описание технологического процесса
Производство кальцинированной соды по аммиачному способу включает 8 основных стадий:
1) получение карбонатного сырья: вскрыша, взрывные работы, добыча, дробление, сортировка сырья и транспортирование;
2) переработка карбонатного сырья: обжиг, охлаждение и очистка диоксида углерода, гашение извести с получением известковой суспензии;
3) очистка рассола: взаимодействие сырого рассола с реагентами в реакторах и отстой рассола;
4) абсорбция: отмывка в промывателях газов, выделяющихся на других стадиях, от аммиака, двухстадийное насыщение раствора хлорида натрия аммиаком и частично диоксидом углерода, поступающим со стадии дистилляции, охлаждение аммонизированного рассола;
5) карбонизация: отмывка от аммиака газа, покидающего стадию карбонизации (сопровождается улавливанием диоксида углерода), предварительная карбонизация, карбонизация с выделением гидрокарбоната натрия в осадительных колоннах, компримирование (перед подачей в карбонизационные колонны) диоксид углерода, поступающего со стадий переработки сырья и кальцинации;
6) фильтрация: отделение гидрокарбоната натрия на вакуум – фильтрах;
7) кальцинация: обезвоживание и разложение гидрокарбоната натрия в содовых печах, охлаждение и очистка диоксида углерода после содовых печей;
8) регенерация аммиака (дистилляция): предварительный подогрев и диссоциация содержащихся в фильтровой жидкости карбонатов и гидрокарбонатов аммония в конденсаторе и теплообменнике дистилляции, смешение и взаимодействие нагретой жидкости с известковой суспензией в смесителе и отгонка аммиака в дистиллере.
Весь содовый процесс полностью может быть изображен следующими химическими уравнениями:
NH3+H2O= NH4OH (1.1)
CO2+ H2O=H2CO3 (1.2)
H2CO3+ NH4OH= NH4HCO3+ H2O (1.3)
NH4HCO3+ NaCl=NaHCO3+ NH4Cl (1.4)
2 NaHCO3→Na2CO3+ H2O+ CO2 (1.5)
Сущность процесса может быть выражена следующим образом: при обработке насыщенного аммиаком рассола углекислым газом сперва происходит как – бы нейтрализация этого раствора углекислотой, сопровождающаяся значительным выделением тепла, а в дальнейшем, по мере повышения в растворе концентрации углеаммониевой соли, начинается ее обменное разложение с поваренной солью с образованием соды, которая при дальнейшем действии на раствор углекислоты образует наименее растворимое соединение – бикарбонат.
Степень конверсии хлорида натрия в бикарбонат натрия по данной технологии не превышает 70 %.
1.2.1 Очистка рассола поваренной соли
На содовых заводах сырой рассол очищают от примесей известково – содовым способом. В этом случае для осаждения солей кальция используют соду, для осаждения солей магния – известковую суспензию.
В основе известково-содового способа лежат реакции ионного обмена, приводящие к образованию труднорастворимых карбоната кальция и гидроксида магния:
Ca2++CO32-↔CaCO3; (1.7)
Mg2++2OH-↔Mg(OH)2 (1.8)
Полнота выделения ионов магния и кальция в осадок, а следовательно, степень очистки, определяется растворимостью СаСО3 и Mg(OH)2 в растворе хлорида натрия. Косвенным параметром, характеризующим полноту выделения Са2+ и Mg2+ в осадок, может служить величина pH, что важно при создании автоматической системы управления процессом очистки.
Процесс очистки рассола происходит при температуре 17±3 °С. Осаждение взвеси осуществляется в отстойнике, образовавшийся шлам разбавляется и направляется в шламопроводы дистиллерной жидкости.
1.2.2 Обжиг извести и получение углекислого газа
Углекислый газ добывается путем обжига известняка, при чем параллельно, кроме углекислого газа, получается известь, которая также необходима для аммиачно – содового процесса в виде известкового молока, как щелочь при дистилляции для разложения аммония, содержащихся в маточной жидкости. Известковое отделение является вспомогательным, вырабатывающим полупродукты для главного процесса. Процесс, происходящий в известковом отделении, разделяется на три операции:
1) обжиг известняка или мела в печах;
2) гашение извести с получением известкового молока;
3) промывка и очистка выходящего из печей углекислого газа.
Реакцию, происходящую при обжиге мела или известняка, можно изобразить так:
CaCO3=CaO+CO2 (1.9)
1.2.3 Приготовление известкового молока
Известковое молоко, необходимое в содовом производстве для регенерации аммиака из хлористого аммония по реакции
2NH4C1 + Са(ОН)2 → CaCl2 + 2NН3 + 2Н2О (1.10)
получают гашением извести избытком воды:
СаО+ Н2О → Са(ОН)2 (1.11)
В воде Са(ОН)2 растворяется плохо, причем с повышением температуры растворимость уменьшается. При 0°С растворяется 0,185 г на 100 г Н2О, а при 100°С всего лишь 0,077 г па 100 г Н2О. Поэтому для разложения хлористого аммония применяют не гомогенный раствор, а суспензию Са(ОН)2 в воде, называемую известковым молоком. Концентрация взвешенной гидроокиси кальция в известковом молоке должна быть по возможности высокой, так как чем меньше воды поступит с известковым молоком в отделение дистилляции, где регенерируется аммиак, тем меньше тепла (пара) будет израсходовано на нагревание этой воды в процессе регенерации. Максимально возможная концентрация известкового молока ограничивается его вязкостью: слишком вязкую суспензию трудно транспортировать, очищать от примесей и дозировать. При получении суспензии известкового молока производят его сгущение в отстойнике, отделенный верхний слой воды является сточной водой.
1.2.4 Абсорбция
Назначение абсорбции состоит в том, чтобы произвести окончательное насыщение рассола аммиаком.
Рассол поваренной соли, содержащий 310 г/л хлорида натрия, предварительно очищенный от примесей других солей, поступает в абсорбер, в который подают аммиак из колонны дистилляции, где протекает регенерация аммиака из маточной жидкости после вакуум – фильтров. Также в абсорбер поступает газ, содержащий аммиак и углекислоту из печи кальцинации бикарбоната.
1.2.5 Карбонизация аммонизированного рассола
Процесс карбонизации (насыщения аммонизированного рассола диоксидом углерода), в результате которого образуется гидрокарбонат натрия, является основным процессом содового производства.
В результате процесса карбонизации из раствора в осадок выпадает гидрокарбонат натрия, образующийся по реакции
NaCl + NH3 + СО2 + Н2О ↔ NaHCO3↓ + NH4C1 (1.12)
Процесс насыщения аммонизированного рассола диоксидом углерода является экзотермическим. Выделяющееся тепло реакции в конечной стадии процесса необходимо отвести, чтобы обеспечить необходимые степени карбонизации раствора и утилизации (использования) натрия.
Температурный режим карбонизационной колонны значительно влияет на процесс образования кристаллов гидрокарбоната натрия. Для получения крупных кристаллов гидрокарбоната натрия правильной формы, которые не забивают фильтрующую поверхность вакуум-фильтров и малорастворимы в процессе фильтрации, необходимо поддерживать сравнительно высокую температуру (60—72 °С) в зоне образования и в начальный период роста кристаллов. В процессе дальнейшего роста кристаллов температура уже не оказывает существенного влияния на их размер.
1.2.6 Фильтрация суспензии бикарбоната натрия
В отделении фильтрации осуществляют процесс разделения выходящей из карбонизационных колонн бикарбонатной суспензии на твердую и жидкую фазы. Твердая фаза-бикарбонат натрия — должен быть не только отделен от маточной жидкости, но и тщательно промыт. При промывке маточная жидкость, задержавшаяся между кристаллами бикарбоната, вытесняется водой, что снижает содержание хлоридов и углеаммонийных солей в отфильтрованном осадке. Для уменьшения влажности отфильтрованный бикарбонат дополнительно отжимают на фильтре.
На содовых заводах для разделения суспензии бикарбоната натрия применяют вращающиеся барабанные вакуум-фильтры, работающие под разрежением.
1.2.7 Кальцинация гидрокарбоната натрия
Кальцинация - термическое разложение гидрокарбоната натрия – является заключительной стадией в производстве кальцинированной соды.
Процесс кальцинации можно показать уравнением:
2 NaHCO3(тв.)=Na2CO3(тв.)+СО2(газ)+Н2О(пар). (1.13)
Кроме этой основной реакции при нагревании технического бикарбоната могут протекать дополнительные реакции:
(NH4)2CO3↔2NH3(газ)+СО2(газ)+Н2О(пар), (1.14)
NH4 HCO3↔2NH3(газ)+СО2(газ)+Н2О(пар). (1.15)
Хлористый аммоний взаимодействует при нагревании с бикарбонатом натрия по реакции
NH4Cl(рас.)+NaHCO3(тв)↔
↔NaCl(тв)+NH3(газ)+СО2(газ)+Н2О (1.16)
Таким образом, в результате кальцинации в твердой фазе остаются Na2CO3 и NaCl, а в газовую фазу переходят NH3, СО2 и Н2О.
Аммиак и углекислый газ будут возвращены в производство. Они улавливаются жидкостью, поступающей в газовый коллектор кальцинатора.
Для обогрева данного аппарата подают водяной пар высокого давления. Перед подачей в кальцинатор, пар проходит редукционную охладительную установку, где его температура снижается до 270°С, а давление — до 3 МПа.
Не нашли, что искали? Воспользуйтесь поиском по сайту:
©2015 - 2025 stydopedia.ru Все материалы защищены законодательством РФ.
|