Технологии обработки художественного стекла
Компоненты стекла
Большое влияние на свойства стекла оказывает и его химический состав, который определяется составом смеси сырьевых материалов (шихты).
Сырьевые материалыдля производства стеклоизделий делят на две группы: основные и вспомогательные.
Основные материалы содержат вещества, образующие основу стекла и определяющие его свойства, вспомогательные представляют собой вещества, которые вводятся для изменения характеристик стекла и ускорения процесса стекловарения (красители, обесцвечиватели, глушители, окислители и восстановители, ускорители варки или плавни и модификаторы свойств).
К основным веществам относят стеклообразователи. Стекло может содержать один или несколько стеклообразователей. Идентификация стекла осуществляется на основе родового названия таких компонентов. Например, если главным стеклообразователем является Si02, то стекло называют силикатным. Если в дополнение к нему в стекле присутствует значительное количество В2О3, то стекло называют боросиликатным.
Красители вводят в шихту для окраски стекла: в зеленый цвет – соединения хрома, железа; в синий и голубой цвет – соединения кобальта, меди; в фиолетовый цвет – соединения марганца, никеля, ниодима; в желтый цвет – соединения кадмия, серебра, церия, титана, урана; в красный и розовый цвета – соединения меди, селена, золота, эрбия, элементарные селен и золото.
Обесцвечиватели, наоборот, вводят для нейтрализации нежелательной окраски. Обесцвечивание стекла основано на ослаблении цветового оттенка (химическое обесцвечивание) и нейтрализации цветового оттенка с помощью дополнительных цветов (физическое обесцвечивание).
Глушение стекла создается за счет образования в стекле частиц, рассеивающих свет. Различают слабое (опалесцентное стекло), среднее (опаловые стекла) и интенсивное глушение (молочные стекла). Глушение вызывают кристаллы (фторидные стекла), области расслоения (фосфатные и специальные стекла), нерастворимые частицы, пузырьки газов.
При варке стекла могут протекать окислительно-восстановительные реакции. И характер химической реакции зависит от количества кислорода. При избытке кислорода в зоне реакции наблюдается окислительная среда. Возможны два источника кислорода: 1) наличие в шихте веществ, которые, разлагаясь при варке стекла, выделяют кислород; эти вещества называются окислителями; 2) избыток воздуха (содержащего, как известно, 21% кислорода) сверх количества, необходимого для поддержания горения топлива.
В качестве окислителей применяют натриевую и калиевую селитры: NaN03 и KN03. В тех же случаях, когда избыток кислорода в среде нежелателен вводят восстановители, поглощающие его (кокс, уголь и др.).
Для снижения температуры варки, а, следовательно, ее ускорения, в шихту вводят плавни (Na2O, K2O, PbO). Их добавление снижает стоимость производства стекла, но ухудшает его свойства (в частности снижает химическую стойкость). Отрицательное влияние плавней устраняют путем добавления модификаторов (например, оксид алюминия или глинозем). И хотя модификаторы и несколько повышают температуру плавления, но они улучшают многие свойства стекла. По сравнению с плавнями модификаторы вводят в меньших количествах, поэтому их применение не приводит к существенному повышению температуры стекловарения.
Для изготовления художественных изделий часто используют натриево-кальциево-силикатное стекло. Главным компонентом такого стекла является оксид кремния Si02, или кремнезем.
История стекла.
Естественным образом произведённое стекло, в особенности вулканическое стекло (обсидиан) использовалось ещё в каменном веке для обработки режущих инструментов. Так как такое стекло было редким, оно стало частым торговым товаром. Археологические источники свидетельствуют, что искусственное стекло впервые было произведено н сирийском побережье, в Месопотамии или в древнем Египте[1]. Большая часть древнейших изделий из стекла была найдена в Египте, благодаря благоприятным для сохранения стекла климатическим условиям, но возможно, что некоторые из этих изделий были ввезены в Египет. Древнейший стеклянные объекты датируются третьим тысячелетием до н. э. Это стеклянные шарики, которые могли случайно получиться в процессе изготовления металла или керамики.
В позднем Бронзовом веке в Египте и в Передней Азии технология изготовления стекла сделала резкий скачок. Археологические находки этого периода включают слитки из цветного стекла и сосуды, иногда с инкрустацией из полудрагоценных камней. Для изготовления египетского и сирийского стекла использовалась сода, которая легко получается из углей многих видов древесины, в особенности растений-галофилов, произрастающих на берегу моря. Самые ранние сосуды производили, вращая пластичные стеклянные волокна вокруг формы из песка и глины, насаженной на металлический стержень. После этого, многократно нагревая стекло, добивались того, что оно сплавлялось в единый сосуд. Затем полосы цветного стекла можно было нанести поверх первоначальной формы, создавая таким образом орнаменты. Затем форму разрушали, а стержень вынимали из получившегося сосуда.
В средние века, после развала Римской империи, перемещение технологий и секретов мастерства стеклодувов сильно замедлилось, поэтому восточная и западная стеклянная посуда постепенно приобретали все больше и больше индивидуальных отличий. Александрия так и оставалась центром производства стекла на Востоке, где делалась изящная стеклянная посуда.
К концу первого тысячелетия, существенно изменились методы производства стекла в Европе. В первую очередь это коснулось состава сырья для производства. Учитывая трудности с доставкой такого компонента смеси как сода, его заменили на поташ, полученный в следствии сжигания дерева. Поэтому стекло, сделанное к северу от Альпийских гор, стало отличаться от изделий, произведенных в средиземноморских странах, например в Италии.
В XI веке немецкие мастера, а в XIII веке – итальянские, освоили производство листового стекла. Они сначала выдували полый цилиндр, затем обрезали его дно, разрезали его и раскатывали в прямоугольный лист. Качество такого листа было не высоким, но практически полностью повторяло химический состав современных оконных стекол. Этими стеклами стеклили окна церквей и замков знатных вельмож. На этот же период приходится и расцвет изготовления витражных окон, в которых использовались кусочки цветного стекла.
В конце Средневековья, центром европейского стекловарения становится Венеция. В тот исторический период венецианский торговый флот бороздил воды всего Средиземноморья, что способствовало быстрому перенесению новейших технологий (особенно с Востока) на венецианскую землю. Производство стеклянных изделий было важнейшим ремеслом в Венеции, о чем свидетельствует количество стеклодувов в этом городе - более 8000 человек. В 1271 году вышел специальный указ, которым узаконивались некоторые протекционистские меры по защите интересов стекловарения, запрещался импорт иностранного стекла, прием на работу иностранных мастеров и вывоз за границу сырья для изготовления стекла.
В XVII веке лидерство в развитии технологии производства стекла постепенно перешло к английским мастерам, в частности благодаря изобретению Джорджем Равенкрофтом в 1674 г. нового способа производства хрусталя. Он сумел получить более качественный состав стекломассы, чем итальянские мастера. Равенкрофт заменил поташ оксидом свинца высокой концентрации и получил стекло с высокими светоотражающими свойствами, которое очень хорошо поддавалось глубокой резке и гравировке.
Но только в конце XIX века стеклоделие из ремесленного стало перерастать в массовое промышленное производство. Одним из «отцов» современного стекольного производства называют немецкого ученого Отто Шотта (1851 – 1935), который активно использовал научные методы для изучения влияния различных химических элементов на оптические и термальные свойства стекла. В области изучения оптических свойств стекла Шотт объединился с Эрнстом Эбби (1840 – 1905), профессором в Университете Йены и совладельцем фирмы Карла Цейса. Другой значительной фигурой, внесшей вклад в массовое производство стекла был Фридрих Симменс. Он изобрел новую печь, которая позволяла непрерывно производить намного большее количество стекломассы.
В конце XIX века, американский инженер Майкл Оуэнс (1859 –1923) изобрел автоматическую машину для производства бутылки. К 1920 году в Соединенных Штатах уже работало примерно 200 машин Оуэнса. Вскоре эти машины распространились по всей Европе. В 1905 году, бельгиец Фурко совершил еще один переворот в стекольной индустрии. Он изобрел метод вертикального вытягивания из печи стеклянного полотна постоянной ширины. В 1914 году, его метод усовершенствовал другой бельгиец – Эмиль Бишеруа, который предложил вытягивать стеклянное полотно между двух роликов, что значительно упрощало процесс дальнейшей обработки стекла.
В Америке подобный процесс вытягивания стеклянного полотна был разработан несколько позже. Затем технология была усовершенствована при поддержке американской фирмы "Либбей - Оуэнс" и начала использоваться для коммерческого производства в 1917 году. Флоат - метод был разработан в 1959 году фирмой "Пилкингтон". При этом процессе стекло поступает из печи плавления в горизонтальной плоскости в виде плоской ленты через ванну с расплавленным оловом на дальнейшее охлаждение и отжиг.
Преимуществами этого метода по сравнению со всеми предыдущими являются стабильная толщина стекла, высокое качество поверхности стекла, не требующее дальнейшей полировки, отсутствие оптических дефектов в стекле, высокая производительность процесса. Наибольший размер получаемого стекла, как правило, составляет 6 м. на 3.21 м., а толщина листа может быть от 2 мм до 25 мм.
В настоящее время в мире производится около 16 500 миллионов тонн листового стекла в год.
Основу научного подхода к исследованию и варке стёкол положил Михаил Васильевич Ломоносов. Учёным были проведены первые, технологически систематизированные, исследования варки более 4 тысяч стёкол. Лабораторная практика и методические принципы, которые он применял, мало чем отличаются от считающихся в настоящее время традиционными, классическими. Ломоносов писал:
Теория строения стекла имеет значение не только для понимания свойств изделий из чистого стекла, но и для всех силикатных изделий, которые в процессе производства находились при температуре выше 800°. Можно считать, что все силикатные материалы, рассматриваемые силикатной технологией, содержат стекло.
В «Письме о пользе стекла» (1752 г.) М. В. Ломоносова, пишет: «Имеет от стекла часть крепости фарфор». Не только фарфор, но и фаянс, керамические изделия, огнеупоры, цемент — все они содержат то или иное количество стекла. Поэтому значение изучения стекла чрезвычайно расширяется и выводы, делаемые в исследованиях, посвящённых строению стекла, важны для понимания свойств самых различных технических силикатных продуктов.
Силикаты - минералы, такие как ПОЛЕВОЙ ШПАТ, ГРАНАТ и СЛЮДА, образуют 95% вещества земной коры. СТЕКЛО представляет собой смесь силикатов с небольшими количествами других веществ
В твёрдом состоянии силикатные стёкла весьма устойчивы к обычным реагентам (за исключением плавиковой кислоты), и к действию атмосферных факторов. На этом свойстве основано их широчайшее применение: для изготовления предметов быта, оконных стёкол, стёкол для транспорта, стеклоблоков и многих других строительных материалов, предметов медицинского, лабораторного, научно-исследовательского назначения, и во многих других областях.
Стеклообразование.
Стёкла образуются в результате переохлаждения расплавов со скоростью, достаточной для предотвращения кристаллизации. Благодаря этому стёкла обычно длительное время сохраняют аморфное состояние. Неорганические расплавы, способные образовать стеклофазу, переходят в стеклообразное состояние при температурах ниже температуры стеклования Tg.
Стекло может быть получено путём охлаждения расплавов без кристаллизации. Практически любое вещество из расплавленного состояния может быть переведено в стеклообразное состояние. Некоторые расплавы (как то — отдельных стеклообразующих веществ) не требуют для этого быстрого охлаждения. Однако некоторые вещества (такие как металлосодержащие расплавы) требуют очень быстрого охлаждения, чтобы избежать кристаллизации.
Стекло может быть получено также путём аморфизации кристаллических веществ, например бомбардировкой пучком ионов, или при осаждении паров на охлаждаемые подложки.
Стёкла, в частности благодаря полимерному строению обладают способностью к гетерогенности. Гетерогенность – разнородность, употребляется для обозначения веществ, имеющих несколько фазовых состояний. Полимерность стёкол в стеклообразном состоянии придаёт им индивидуальные качества, определяющие, в зависимости от характера этих структурных образований, степень прозрачности и других свойств стёкол. Присутствие в составе стекла соединений того или иного химического элемента, оксида металла, может влиять его окраску, степень электропроводности, и другие физические и химические свойства.
Улучшение свойств стекла
Основной недостаток обычных стёкол — хрупкость. Для того, чтобы расширить сферу применения стекла, его подвергают закалке (закалённое стекло), создают многослойные композиты (триплекс). Армирование, вопреки распространенному мнению, ослабляет стекло, делает его более хрупким по сравнению с таким же монолитным стеклом.
Классификация стекла
По типу неорганических соединений различают следующие классы стекол: элементарные, металлические, оксидные, галогенидные, халькогенидные, сульфатные, нитратные, карбонатные, фосфатные и др.
Элементарные стекла, их способны образовывать небольшое число элементов - сера (S), селен (Sе), мышьяк (Аs), фосфор (Р), углерод (С). Промышленное значение находит стеклоуглерод, он способен оставаться в твердом состоянии до 3700°С, имеет низкую плотность 1500 кг/м3, обладает высокой прочностью, электропроводностью, химически стоек.
Галогенидные стекла получают на основе стеклообразующего компонента ВеF2 Многокомпонентные составы фторобериллатных стекол содержат также фториды алюминия, кальция, магния, стронция и бария. Фторобериллатные стекла находят практическое применение благодаря высокой стойкости к действию жестких излучений, включая рентгеновские и γ-лучи, агрессивных сред - фтор, фтористый водород.
Халькогенидные стекла Они прозрачны в ИК-области спектра, обладают полупроводниковой проводимостью электронного типа, обнаруживают внутренний фотоэффект. Стекла применяются в телевизионных высокочувствительных камерах, в ЭВМ в качестве переключателей или элементов запоминающих устройств.
Оксидные стекла. Наибольшее значение в технике, строительстве и художественном проектировании имеют оксидные стекла, которые представляют собой обширный класс соединений.
В зависимости от основных стеклообразующих компонентов (стеклообразователей) различают оксидные стекла:
силикатные – SiO2;
алюмосиликатные - Аl2O3, SiO2;
боросиликатные - В2O3, SiO2;
бороалюмосиликатные - В2O3, Аl2O3, SiO2;
алюмофосфатные - Аl2O3, Р2O5;
бороалюмофосфатные - В2O3, Аl2O3, Р2O3;
алюмосиликофосфатные - Аl2O3, SiO2, Р2O5;
фосфорванадатные - Р2O5, V2O5;
силикотитанатные - SiO2, TiO2;
силикоцирконатные - SiO2, ZrО2.
Промышленные составы стекол содержат, как правило, не менее 5 компонентов, а специальные и оптические стекла могут содержать более 10 компонентов.
Однокомпонентное кварцевое стекло на основе диоксида кремния SiO2, широко использующееся в технике и быту, наиболее простое по составу.
Двухкомпонентные - бинарные щелочно-силикатные стекла (состава Ме2O-nSiO2, где Me-Na, К; n=2...4), так называемые растворимые (жидкие) стекла, имеют большое промышленное значение, широко применяются в строительстве для получения кислотостойкого цемента, а также для реставрационных работах.
Многокомпонентные оксидные стекла - промышленные стекла - оконного, архитектурно-строительного, сортового, автомобильного, тарного и других производств. их основу - составляют композиции тройной системы Na2O(К2O)-СаО- SiO2, при массовых содержаниях (%):SiO2 - 60...80, СаО - 0...10, Na2O - 10...25.
Промышленные составы силикатных стекол кроме SiO2, Na2O, СаО содержат МgO, который способствует снижению склонности к кристаллизации, и оксид алюминия Аl2O3, повышающий химическую стойкость стекол. Сортовые стекла содержат K2O, РbО, ZnО
Важно отметить, что физико-механические свойства стекла зависят от входящих в него оксидов. В общем виде можно отметить влияние главных составляющих стекла.
Кремнезем SiO2 - главная составная часть всех силикатных стекол; в обычных стеклах его концентрация составляет 70...73% по массе. Он повышает вязкость и тугоплавкость стекломассы, улучшает химические и физические свойства стекла, повышает прочность, химическую и термическую стойкость, снижает плотность, температурный коэффициент линейного расширения (ТКЛР), показатель светопреломления.
Оксид алюминия Аl2O3 повышает тугоплавкость, вязкость и температуру размягчения, поверхностное натяжение расплава стекла, улучшает механические свойства, теплопроводность, химическую стойкость, снижает ТКЛР.
Оксид бора В2O3 снижает температуру плавления, вязкость, поверхностное натяжение и склонность расплава стекла к кристаллизации и ТКЛР, увеличивает термо- и химическую стойкость, улучшает химические свойства.
Оксиды щелочных металлов (Na2O, К2O, Li2O) играют роль плавней, снижая температуру плавления стекольной шихты и вязкость расплава. В обычных стеклах концентрация их не превышает 14...15 %. Они повышают плотность, ТКЛР, диэлектрическую проницаемость и снижают химическую стойкость, электросопротивление стекла.
Поташ К2СO3 придает стеклу чистоту, блеск, прозрачность, увеличивая его светопреломление и применяется для производства лучших сортов стекла, в частности хрусталя - одного из видов стекла, используемого для высокохудожественных светильников.
Оксиды СаО, МgO, ZnО и РbО повышают механическую прочность, химическую стойкость, показатель светопреломления стекла и улучшают внешний вид стеклоизделий.
Архитектурно-строительные стекла классифицируются
- по виду: листовое строительное и декоративное стекло;
- по назначению
облицовочное стекло (цветные коврово-мозаичные плитки, стемалит и др.), стекло для санитарно-технических устройств и оборудования внутренних помещений; стеклянная осветительная арматура; конструктивно-строительные элементы из стекла (блоки, профильное стекло, панели и пр.); тепло- и звукоизоляционные материалы (пеностекло, стекловолокнистые материалы, стеклоткани).
Технологии обработки художественного стекла
Варка стекла
Варка художественного стекла происходит по тем же технологиям, что и для обычных типов стекла, главное отличие - очень широкий спектр применяемых компонентов: для получения разноцветного стекла, для матового (глушёного), стекла с повышенным коэффициентом преломления, авантюринового и т.д.
Выдувание и формовка
Выдувание — операция, позволяющая из вязкого расплава получить различные формы — шары, вазы, бокалы. Стеклодувные стёкла делятся на «короткие» (тугоплавкие и термостойкие, например — «пирекс»), пластичные в весьма узком диапазоне температур и «длинные» (легкоплавкие, например — молибденовое) — имеющие этот интервал значительно более широким.
При помощью выдувания изготовляют широкий ассортимент изделий различных конфигураций. Выдувание бывает ручным и механизированным.
Ручным способом изделия выдувают с помощью стеклодувной трубки. Для этого на конец стеклодувной трубки набирают стекломассу, закатывают ее на плитке и затем раздувают в небольшой пузырек «баночку». На «баночку» набирают еще порцию стекломассы и, раздувая и вращая трубку, придают стекломассе определенную форму. Эту заготовку изделия (пульку) опускают в форму, где при, одновременном вращении окончательно выдувают изделие.
При механизированном способе изделия выдувают сжатым воздухом на стеклоформующих машинах. На этих машинах выполняют такие операции, как формование головки (горла) изделия и предварительное выдувание «баночки» в черновой форме (рис. 16, а—б), передачу «баночки» с помощью горлового кольца в чистовую форму (рис. 16, в—д) и окончательное выдувание изделия (рис. 16, е—ж).
Большинство стеклоформующих машин работают но принципу автомата. В зависимости от характера питания они подразделяются на машины с капельным питанием, машины фидерного типа (полуавтоматы ВШМ, ВВ-2, автоматы 2ЛАМ, Л-10, АВ-4, АВ-4-2, АВ-6 АВ-6-2, ВВ-7) и машины с вакуумным питанием (автоматы ВВ-6, ВВМ-10, ВР-24, ВС-24, ВК-18).
Способом ручного и механизированного выдувания вырабатывают полые изделия различной конфигурации. Это прежде всего узкогорлые (диаметр горла до 30 мм) толстостенные полые изделия диаметром от 15 до 160 мм, высотой от 25 до 370 мм, емкостью от 15 до 4500 мл — пищевая, медицинская, парфюмерная, химическая и прочая тара. Этим же способом вырабатывают большинство изделий бытовой посуды и художественного стекла (стаканы, чайные и винные, блюдца для чая и варенья, рюмки, фужеры, вазы, графины).
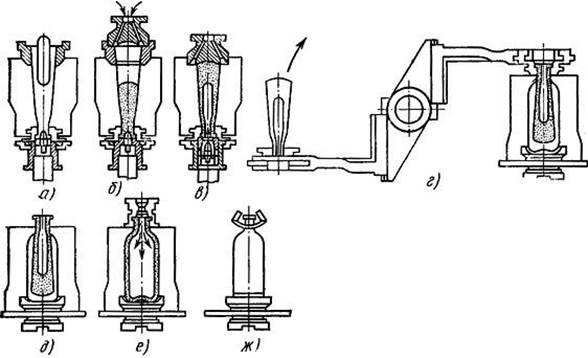
Рис. 16. Технологическая схема выдувания изделий на автомате АВ-4: а — ж — последовательность операций
формование головки (горла) изделия и предварительное выдувание «баночки» в черновой форме (рис. 16, а—б), передача «баночки» с помощью горлового кольца в чистовую форму (рис. 16, в—д) и окончательное выдувание изделия (рис. 16, е—ж).
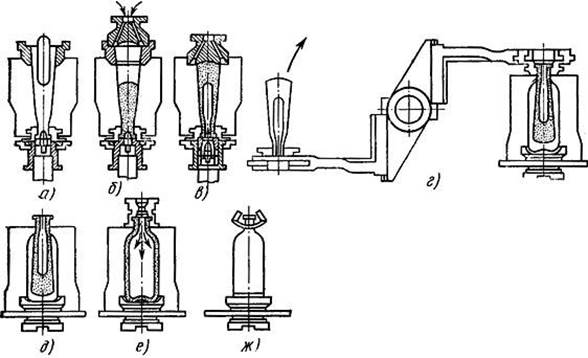
Рис. 16. Технологическая схема выдувания изделий на автомате АВ-4: а — ж — последовательность операций
формование головки (горла) изделия и предварительное выдувание «баночки» в черновой форме (рис. 16, а—б), передача «баночки» с помощью горлового кольца в чистовую форму (рис. 16, в—д) и окончательное выдувание изделия (рис. 16, е—ж).
Формовка стекла
Для вытягивания и формования стеклянной массы, образования тиснёных украшений и т.д. используют длинные пинцетообразные клещи из металла, для отсекания всего изделия от трубки используют сечку или ножницы, деревянной ложкой (скалка, долок — в форме коклюшки) разравнивают набранную стекломассу. Предварительно отформованное с помощью этих инструментов стекло («баночку») стеклодув вкладывает в форму из дерева или железа.
Готовое изделие отшибают от трубки на вилы и несут в отжигательную печь. Оставшийся от отшибания след (насадок, колпачок) приходится удалять шлифовкой.
Технологии обработки теплого стекла
Спекание стекла — соединение нескольких стеклянных элементов в одно целое за счёт диффузии в расплавленном стекле под действием высокой температуры. При нагреве до определенной температуры стекло размягчается, и детали изделия спекаются между собой, не изменяя или незначительно изменяя свою форму и взаимное расположение. Такое спекание называется приметочным (неполный фьюзинг).Если повысить температуру обработки, то вязкость стекла станет еще меньше. Под воздействием собственного веса верхние элементы начнут постепенно погружаться в нижние и даже частично растворяться в них. Полное растворение верхних элементов в нижнем называется полным спеканием, или полным фьюзингом.При правильном подборе сортов стекла и температурно-временных режимов нагрева (охлаждения) технология спекания позволяет достичь великолепного декоративного эффекта и высокой прочности готового изделия. Фьюзинг – технология спекания листового стекла, а так же листового стекла со стеклом, имеющим иную форму (фритта, дрот и т.д.).
Отекание (моллирование) или свободное формование стекла — изменение формы нагретой стеклянной заготовки под действием силы тяжести. При достижении температуры 750-800°С стекло размягчается настолько, что начинает провисать или отекать, принимая форму поверхности, на которой оно находится. Воспользовавшись этим процессом, готовому изделию можно придать форму чаши, блюда и иную подобную. При этом роль подложки играют формы из глины, гипса или других термостойких материалов.
Огневая полировка — нагрев стекла с целью создания гладкой, блестящей поверхности, а также сглаживания кромки изделия.
Печная отливка — формование изделия путем спекания (плавления) фритты и/или кусков стекла в форме.
Стекольная отливка — формование изделия путем налива расплавленной стекломассы в форму.
Прочесывание стекла — механическое воздействие на размягченное стекло ручным инструментом
Таблица 1 - Температурные режимы различных технологий обработки теплого стекла
№
| Виды обработки теплого стекла
| Описание
| Температура, °С
|
| Приметочное спекание
| Спекание двух или более стеклянных элементов с сохранением формы каждого
| 730-790
|
| Полное спекание
| Спекание двух или более стеклянных элементов до полного вплавления верхних в нижний
| 790 - 840
|
| Моллирование
| Свободное формование стекла под воздействием собственного веса в форме
| 650-700
|
| Огневая полировка
| Нагревание стекла для скругления кромок и придания блеска
| 700 - 760
|
| Печная отливка
| Формование стекла путем спекания фритты и/или мелких фрагментов стекла внутри формы
| 820 - 870
|
| Стекольная отливка
| Формование стекла путем выливания расплавленной стекломассы в форму
| 930 - 980
|
| Прочесывание
| Механическое воздействие на стекло при помощи ручного инструмента
| 900 - 950
|
| Pate de verre
| Обжиг стеклянной пасты в форме
| 700 - 800
|
Не нашли, что искали? Воспользуйтесь поиском по сайту:
©2015 - 2024 stydopedia.ru Все материалы защищены законодательством РФ.
|