Грузозахватные приспособления
Для захвата грузов при выполнении погрузочно –разгрузочных работ применяют различные грузозахватные устройства. На кранах, предназначенных для работы с различными грузами, в качестве универсального грузозахватного устройства используют крюки или петли, к которым груз подвешивают непосредственно или с помощью гибких строп (канатных или цепных) или с помощью специальных грузозахватных устройств.
1.1.4 ВЫБОР ТИПА КРЮКА
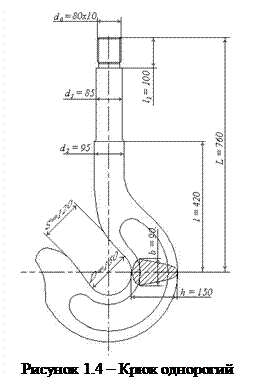
В мостовых кранах общего назначения применяются кованные однорогие крюки по ГОСТ 6627-74. По номинальной грузоподъемности Q = 15т, выбираем крюк однорогий, тип Б (с удлиненным хвостовиком) - №19.
Для принятого крюка (Рисунок 1.4) основными параметрами являются:
Диаметр резьбы хвостовика крюка d0 = 80 мм (Трап. 80х10);
Диаметр шейки хвостовика d1 = 85 мм;
d2 = 95 мм;
Диаметр зева D = 150 мм;
S = 120 мм;
Длина хвостовика крюка l1 = 100 мм;
l = 420 мм;
L = 760 мм;
h = 150 мм;
b = 90мм;
1.1.3 ВЫБОР ТИПА ПОДВЕСКИ И ЕЕ СХЕМА
По типу крюка подвески могут быть с однорогим и с двурогим крюком.
При выборе типоразмера крюковой подвески необходимо соблюдать ряд условий. Первое условие – грузоподъемность крюковой подвески не должна быть меньше заданной грузоподъемности: Qп ≥Q. Второе условие – режим работы крюковой подвески должен соответствовать режиму работы механизма.
Принимаем строительную подвеску (Рисунок 1.3).
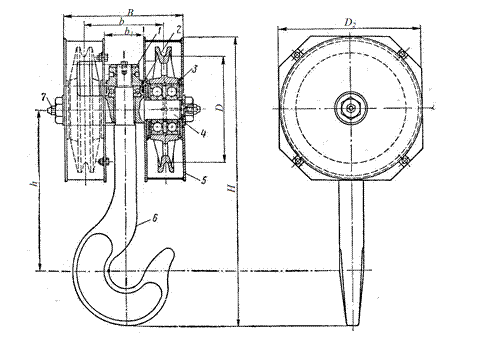
.
Всегд
На рисунке 1.3 приведен чертеж подвески крана рассчитываемого крана. Она состоит из крюка 6, на нарезную часть которого навинчивается гайка 1, опирающаяся на упорный шариковый подшипник 2, который опирается на траверсу 4, на цапфах которой вращаются блоки полиспаста, установленные на шарикоподшипниках. Для безопасности работы и предохранения канатов от выпадения из блоков, последние закрыты специальными сварными кожухами 5. Смазка подшипников блоков – консистентная при помощи масленок 7, войлочные уплотнительные кольца 3 предохраняют подшипники от вытекания смазки.
Кроме этого необходимо выписать условное обозначение ее типоразмера и основные параметры: грузоподъемность Qп; режим работы; число блоков Zп; диаметр блоков по дну канавок Dбл 0; расстояние между осями крайних наружных блоков Внар; расстояние между осями крайнего наружного и соседнего с ним внутреннего блоков бс; массу подвески mп .
1.1.5 РАСЧЕТ И ВЫБОР УПОРНОГО ПОДШИПНИКА ПОД ГАЙКУ КРЮКА
Гайка крюка выполняется с уширением нижней части, которая охватывает упорный подшипник. Наружный диаметр гайки определяется по формуле:
, (1.3)

Поскольку вращение крюка является только установочным, то расчет подшипника ведется по статической грузоподъемности, которая может быть определена по формуле:
, (1.4)
где: Q – грузоподъемность крана,
Q = 15000кг,
kд - динамический коэффициент,
kд = 1,2.

Для крюка с диаметром шейки d1 = 85 мм, выбираем упорный однорядный подшипник легкой серии 8217 (ГОСТ 6874-54) с коэффициентом работоспособности Сс = 235кН, что в несколько раз превосходит расчетный.
1.1.6 РАСЧЕТ И ВЫБОР КАНАТА
На грузоподъемных машинах общего назначения при однослойной навивке на барабан рекомендуется применять следующие два типа шестипрядных стальных канатов двойной свивки с одним органическим сердечником: 1)ЛК-Р6х19(1+6+6/6)+1 о.с. ГОСТ2688-80; 2)ЛК-Р0 6х36 (1+7+7/7 +14)+1
2)
При расчете и выборе каната сводится к нахождению максимального усилия в канате Smax в точке набегания его на барабан (Рисунок 1.5), которое определяется по формуле:
, (1.5)
где: - КПД полиспаста,
,
- КПД подвижного блока,
= 0,99,
- КПД уравнительного блока,
= 1,
,
.
Канат выбираем по разрывному усилию, согласно Правилам Госгортехнадзора:
, (1.6)
где: - минимальный коэффициент запаса прочности каната,
= 6,0 [2, таблица 11].
.
Выбираем тип каната ЛК-Р6х19(1+6+6+6/6)+1о.с, ГОСТ 2688-80, имеющий линейное касание проволок и разные диаметры проволок в верхнем слое пряди.

По условию , из таблицы ГОСТа выбираем типоразмер каната.
Канат 21,0-Г-В-С-О-Н-1666 ГОСТ 2688-80 имеет параметры: Sразр = 236000 Н; dк = 21 мм; Fк = 167,03 мм2.
Назначение каната – грузовое;
Марка проволоки – высшая;
Маркировочная группа – 1666 МПа;
Вид покрытия проволоки – оцинкованная для среднеагрессивных условий работы;
Сочетание направлений свивки элементов – одностороннее;
Способ свивки каната – нераскручивающийся;
Направление свивки каната – для одной половины полиспаста – правое, для другой – левое.
1.1.7 ОПРЕДЕЛЕНИЕ ДИАМЕТРА БЛОКОВ
Допускаемый диаметр блока по центру каната определяется по формуле Госгортехнадзора:
(1.7)
где: е – коэффициент, учитывающий допустимый перегиб каната,
е = 30 [2, таблица 12].

С целью унификации окончательного диаметра блока (по канавке) принимается по ряду. Так как по расчету , и в ряде такой диаметр существует, то оставляем расчетное значение, а именно .
Профиль канавок блоков (Рисунок 1.6) выполняется по нормалям в зависимости от диаметра каната:
(1.8)
(1.9)
(1.10)

Принимаем 12мм.

Принимаем 35мм.

Остальные параметры выбираем из таблицы [2. приложение 5]:
B = 65 мм,
В1 = 45 мм.
1.1.8 РАСЧЕТ ЭЛЕМЕНТОВ ПОДВЕСКИ НА ПРОЧНОСТЬ
Расчет траверсы крюка
Траверса подвески (Рисунок 1.7) работает на изгиб. Расчет траверсы ведется по двум опасным сечениям: в середине (А-А) и в месте изменения сечения (В-В).
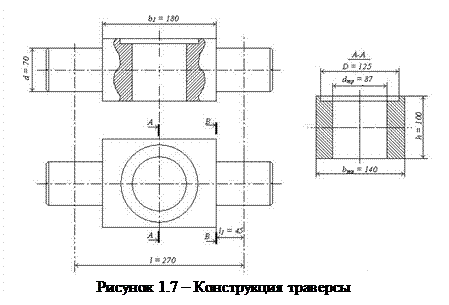
Максимальный изгибающий момент в сечении А-А (Рисунок 1.8) определяется по формуле:
(1.11)
где: l –расчетная длина траверсы [см],
Поскольку величина l неизвестна, то для предварительного расчета ее можно принять по аналогичным типовым подвескам. Для двухблочной подвески l=27см [1.таблица5].

Ширину траверсы можно принять:
(1.12)
где: - наружный диаметр упорного подшипника.
= 125 мм, (выбранный упорный однорядный подшипник легкой серии 8217).

Принимаем = 140 мм.
Диаметр отверстия принимается на 2…5 мм больше диаметра хвостовика крюка. Так как диаметр шейки хвостовика d1 = 85 мм, то диаметр отверстия траверсы dтр = 87 мм.
Длину средней части траверсы для предварительного расчета можно принять [1. таблица 5].
Момент сечения В-В будет равен:
(1.13)

Траверса обычно изготавливается из стали 45 с пределом выносливости .
Параметры траверсы определяются проектным расчетом из условия прочности при изгибе
,
где: М – момент, действующий в расчетном сечении [ ],
W – момент сопротивления расчетного сечения [см3],
- допускаемое напряжение изгиба [МПа].
Поскольку траверса работает в пульсирующем цикле, то допускаемое напряжение для предварительного расчета может быть определено по упрощенной формуле:
(1.15)
где: - коэффициент, учитывающий конструкцию детали, = 2,2,
- допускаемые коэффициент запаса прочности, = 1,7,
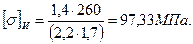
Определим моменты сопротивления, действующие в расчетных сечениях:


Момент сопротивления среднего сечения траверсы А-А, ослабленном отверстием:
(1.16)
где: h – высота траверсы,
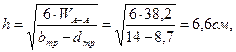
Принимаем h = 100 мм.
Момент сопротивления сечения траверсы В-В:
(1.17)
где: d – минимальный диаметр цапфы под подшипник,
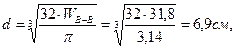
Принимаем d = 70 мм
1.1.9 ПОДБОР ПОДШИПНИКОВ БЛОКА
Подшипники качения для блоков выбираем по коэффициенту работоспособности С, вычисленному с учетом эквивалентной нагрузки на подшипник.
Каждый блок устанавливается на двух радиальных подшипниках. Нагрузка на один подшипник при максимальном грузе:
(1.18)
где: - динамический коэффициент, =1,2;
- коэффициент вращения, =1,35 (при вращении наружного кольца подшипника);
- число блоков в подвеске, = 2.

Однако в связи с тем, что кран работает с разными грузами, расчет следует вести по эквивалентной нагрузке, которую с достаточной точностью можно определить по следующей формуле:
(1.19)
где: - коэффициент приведения, = 0,75.

Требуемая долговечность подшипника L определяется по формуле:
(1.20)
где: - долговечность подшипника, = 5000 ч = мин,
n - частота вращения блока,
об/мин.
млн. оборотов.
Тогда расчетная динамическая грузоподъемность шарикового подшипника будет равна:
(1.21)

Для данного диаметра цапфы по расчетному коэффициенту работоспособности выбираем шарикоподшипник радиальный однорядный средней серии 314 (ГОСТ 8338-57), внутренний диаметр d = 70 мм, наружный диаметр D = 150 мм, ширина подшипника В = 35 мм, коэффициент работоспособности С = 104,0 кН.
1.1.10 ОПРЕДЕЛЕНИЕ ДИАМЕТРА УРАВНИТЕЛЬНОГО БЛОКА
Диаметр уравнительного блока:
(1.22)

С целью унификации окончательного диаметра блока (по канавке) принимается по ряду. Так как по расчету , принимаем .
Профиль канавок блоков (Рисунок 1.9) выбираем [2. приложение 5]:
12мм.
35мм.
B = 65 мм,
В1 = 45 мм,

1.1.11 ОПРЕДЕЛЕНИЕ ДИАМЕТРА И ДЛИНЫ БАРАБАНА
Допускаемый диаметр блока по центру каната также определяется по формуле Госгортехнадзора:


С целью унификации окончательного диаметра блока (по канавке) принимается по ряду. Так как по расчету , и в ряде такой диаметр существует, то оставляем расчетное значение, а именно .
Длина каната, наматываемого на одну половину барабана:
(1.23)
где: Н – высота подъема, Н = 15,5м,

Для равномерной укладки каната на поверхности барабана наносятся винтовые канавки нормализованного профиля (Рисунок 1.10). Шаг канавок принимается равным:
(1.24)

Принимаем
Толщина стенки проектируемого стального барабана, из условий технологии толщина стенки их должна быть не менее 12 мм и может быть определена по формуле:
(1.25)

Принимаем .
Длина барабана при использовании сдвоенного полиспаста (на барабан наматываются две ветви каната) определяется по следующей формуле:
, (1.26)
где - участок для закрепления конца каната,
, (1.27)

принимаем 
- участок для неприкосновенных витков трения (для уменьшения нагрузки на элементы крепления каната),
, (1.28)

принимаем 
участок для навивки рабочей ветви каната
, (1.29)
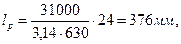
- длина концевой части барабана,
, (1.30)

принимаем 
Максимальная длина среднего участка принимается из условия обеспечения нормального набегания каната при максимальном подъеме подвески (Рисунок 1.11).
- средний участок барабана, разделяющий левую и правую нарезки.
(1.31)
где: минимальное расстояние между осью барабана и осью подвески, 
- расстояние между осями ручьев крайних блоков, 
- допустимый угол отклонения набегающей на барабан ветви каната от вертикального положения, 

принимаем 

1.1.12 РАСЧЕТ БАРАБАНА НА ПРОЧНОСТЬ
Барабан выполнен из стали 35Л, с пределом текучести .
Принятое значение толщины стенки следует проверить на сжатие по формуле:
(1.32)
где:
(1.33)
k – коэффициент запаса прочности для крюковых кранов,
k = 1,5 [2. приложение15],
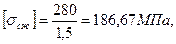

Кроме сжатия стенки барабана испытывает деформацию изгиба и кручения (Рисунок 1.12).
Крутящий момент, передаваемый барабаном:
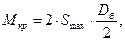

Изгибающий момент определяется для случая, когда крюковая подвеска находится в самом верхнем положении (расстояние между навиваемыми канатами ). После конструктивной проработки расстояние от точки приложения усилия Smax до середины ступицы оказалось равным 376 мм. Тогда:

Сложное напряжение от изгиба и кручения:
(1.35)
где: W – экваториальный момент сопротивления поперечного сечения барабана при кручении:

- коэффициент приведения напряжения, 

Напряжения от изгиба и кручения в стенке барабана незначительны; при длине барабана менее трех диаметров они обычно не превышают 15% от напряжения сжатия.
1.1.13 ВЫБОР СИСТЕМЫ КРЕПЛЕНИЯ КАНАТА НА БАРАБАНЕ. ПОДБОР И РАСЧЕТ ДЕТАЛЕЙ ДАННОГО КРЕПЛЕНИЯ
Принята конструкция крепления каната к барабану прижимной планкой, имеющей трапециидальные канавки (Рисунок 1.13). Канат удерживается от перемещения силой трения, возникающей от зажатия его между планкой и барабаном двумя болтами. Начиная от планки предусматривают дополнительные витки (1,5…2), способствующие уменьшению усилия в точке закрепления каната.
С учетом влияния этих витков усилие в канате перед прижимной планкой можно определить по формуле Эйлера:
(1.36)
где: – основание натурального логарифма, 
- коэффициент трения каната о барабан, 
угол обхвата барабана витками трения, 

С учетом всех сил трения, которые удерживают канат на барабане в одном болте может быть найдено по формуле:
(1.37)
где: число болтов; 
коэффициент трения каната о планку, ,

Обычно при диаметре каната 21 мм принимают болты (шпильки) М22. Принятый болт проверяют на растяжение:
, (1.38)
где: 1,3 – коэффициент, учитывающий кручение и изгиб болта,
– коэффициент запаса надежности крепления каната к барабану, 
площадь сечения болта, см2,
– допускаемое напряжение растяжения, 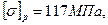

где: - внутренний диаметр болта М22, изготовленного из стали Ст3, 

1.1.14 РАСЧЕТ УСТАНОВКИ БАРАБАНА, РАСЧЕТНАЯ СХЕМА НАГРУЗОК НА ВАЛ БАРАБАНА И РАСЧЕТ ВАЛА НА ПРОЧНОСТЬ
Соединение вала барабана с входным валом редуктора может производиться при помощи зубчатых муфт, допускающих значительную на соосность соединяемых валов. Эти муфты характеризуются высокой надежностью, но имеют большие габариты. Поэтому в современных конструкциях механизмов подъема мостовых кранов для обеспечения компактности широко применяется специальное зубчатое зацепление (Рисунок 1.14).
В этом случае конец тихоходного вала редуктора выполняется в виде зубчатого венца, входящего в зацепление с другим венцом, укрепленным непосредственно на барабане. При таком соединении крутящий момент передается через болты, соединяющие венец-ступицу с обечайкой барабана, и следовательно, вал барабана работает только на изгиб.
Для предварительного расчета длину оси барабана можно принять равной:
(1.39)

Принимаем 
Нагрузка на барабан (пренебрегая собственным весом барабана) создается усилиями двух ветвей каната – 2Smax. Поскольку ступицы находятся на разных расстояниях от опор предварительно можно принять:
l1=120мм, l2=200мм.
Нагрузки на ступицы также не будут одинаковыми (Рисунок 1.15). С достаточной для предварительного расчета точностью их можно принять:
Расчет барабана сводится к определению диаметров цапф dц и ступицы dст из условия работы оси на изгиб в симметричном цикле:
(1.40)
где: М – изгибающий момент в расчетном сечении,
W – момент сопротивления расчетного сечения,
-допускаемое напряжение при симметричном цикле.
Материалом для оси барабана обычно служит сталь 45 с пределом выносливости . Допускаемое напряжение при симметричном цикле можно определить по упрощенной формуле:
(1.41)
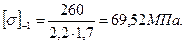
Реакции в опорах:


Наибольший изгибающий момент в сечении под ступицей:

Момент сопротивления этого сечения:
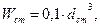

Принимаем: 
Наибольший момент для правой цапфы будет равен:
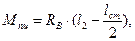
где: - длина ступицы,

Принимаем: 

Момент сопротивления этого сечения:


Принимаем: 
В целях унификации подшипников диаметр левой цапфы может быть принят равным диаметру правой цапфы 
1.1.15 ВЫБОР ПОДШИПНИКА ВАЛА БАРАБАНА
Для компенсации несоосности опор вал барабана помещается на самоустанавливающихся сферических двухрядных шариковых подшипниках.
Эквивалентная нагрузка на правый подшипник может быть определена по упрощенной формуле:
(1.42)
где: - коэффициент вращения, (при вращении внутреннего кольца),
- динамический коэффициент, (для механизмов подъема),

Расчетная динамическая грузоподъемность шарикового подшипника будет равна:


Поскольку в левом подшипнике вращаются оба кольца, (подшипник служит только опорой), то его можно рассчитывать по статической грузоподъемности:
, (1.43)

В целях унификации оба подшипника можно принять одинаковыми.
По вычисленной работоспособности для цапфы , выбираем шарикоподшипник радиальный сферический № 1316 (ГОСТ 5720-75) с коэффициентом работоспособности Такой шарикоподшипник допускает поворот оси в опорах, что благоприятно сказывается на работоспособности подшипникового узла.
1.1.16 РАСЧЕТ МОЩНОСТИ ЭЛЕКТРОДВИГАТЕЛЯ И ЕГО ВЫБОР ПО КАТОЛОГУ
При выборе режима работы электродвигателя и продолжительности включения (ПВ) для крюковых кранов общего назначения, принимаем ПВ = 40% (при тяжелом режиме работы электрооборудования) [3, таблица 5]
Статическая мощность двигателя механизма подъема при установившемся режиме вычисляется при подъеме номинального груза:
(1.44)
где: - КПД механизма подъема,
= 0,85 [2, приложение 33],

В кранах общего назначения расчет двигателя можно с достаточной точности вести по эквивалентной нагрузке. В этом случае потребная мощность двигателя определяется по формуле:
(1.45)

По табл. [2, приложение 34], выбираем электродвигатель переменного тока с фазовым ротором типа МТВ412-8 мощностью N=17кВт, числом оборотов nдв=725об/мин, максимальным моментом Мп.max =824,04Н.м,
1.1.17 ВЫБОР РЕДУКТОРА
Редуктор выбирается по статической мощности, передаточному отношению, частоте вращения вала двигателя и режиму работы.
Мощность редуктора определяется по формуле:
(1.46)
где: - коэффициент запаса,
= 1 (для редуктора типа Ц2),

Передаточное отношение:
(1.47)
где: - число оборотов барабана, об/мин.
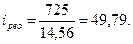
Редуктор механизма подъема выбираем исходя из расчетной мощности числа оборотов вала двигателя nдв=725об/мин, передаточного числа и режима работы – 5М.
По каталогу [2, приложение 38] выбираем редуктор типа Ц2-500-50,94-5М (суммарное межосевое расстояние Ас = 500мм, передаточное число вал тихоходный с концом под зубчатую муфту).
Конструкция выходных валов редуктора показано на рисунке (рисунок 1.16), которые имеют основные размеры:
а) зубчатый конец тихоходного вала: m=8, z=40, D3=336мм, B=40мм, d2=150мм, L2=295мм, L3=330мм, l2=65мм.
б) быстроходный вал: d=60мм, d1=80мм, L1=390мм, l1=108мм.
1.1.18 ВЫБОР МУФТ ДЛЯ СОЕДИНЕНИЯ ВАЛОВ
В принятом способе соединения вала редуктора с барабаном крутящий момент передается через прецизионные болты, установленные в отверстия без зазора (см. рисунок 1.14).
В этом случае болты работают на срез, напряжение которого определяется по формуле:
(1.48)
где: - число болтов, 
- диаметр цилиндрической части прецизионного болта, 
- допустимое напряжение среза,

- усилие, действующее по окружности установки болтов,
(1.49)
где: - крутящий момент на барабане,
- диаметр окружности установки болтов,

Принимаем 

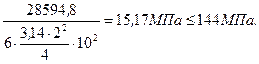
В механизмах подъема необходимо выбрать муфты для соединения вала электродвигателя с валом редуктора. Муфты выбираются по расчетному крутящему моменту:
(1.50)
где: k3 – коэффициент запаса,

где: k1 – коэффициент, учитывающий степень ответственности механизма, k1 = 1,3,
k2 – коэффициент, учитывающий режим работы, k2 = 1,3,
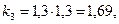

По каталогу [2, приложение 63] выбираем две упруго втулочно-пальцевые муфты типа МУВП-60 (рисунок 1.17) (Допустимый крутящий момент , D=220мм, Lнаиб=286мм, ).
По каталогу [2, приложение 44] выбираем зубчатую муфту с тормозным шкивом Dт = 300мм, имеющую следующую характеристику: наибольший передаваемый крутящий момент 
1.1.1.9. ВЫБОР И РАСЧЕТ ТОРМОЗА
В ГПМ нашли применения большое число разнообразных конструкций колодочных тормозов. В простейшем случае одноколодочного тормоза замыкающая сила Fраб , приложенная к тормозному рычагу, создает усилие нажатия fn колодки на тормозной шкив, вследствие чего возникает сила трения , противодействующая вращению механизма.
Одноколодочные тормоза применяются редко, т.к. создают при торможении усилие, изгибающее тормозной вал
; 
; 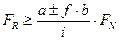
(+), если Т по часовой стрелки, и (-) если против.
В механизмах подъема груза широко используют автоматические нормально замкнутые тормоза с пружинным замыканием и электромагнитным или электрогидравлическим приводом типа ТКТ, ТКП, ТКГ, ТКТГ и ТТ.
В примере применен колодочный тормоз типа
ТТ- 320
Тормоз устанавливается на быстроходном валу редуктора. Расчетный тормозной момент на этом валу равен:
(1.51)
где: kт – коэффициент запаса торможения, kт = 2,

В последнее время в грузоподъемных машинах наибольшее применение получили колодочные тормоза с электрогидротолкателями (рисунок 1.18). По таблице (2, приложение 66) выбираем тормоз типа ТТ-320 с наибольшим тормозным моментом , отрегулированный на расчетный тормозной момент.
ПРОВЕРОЧНЫЙ РАСЧЕТ
1.2.1 ПРОВЕРКА ДВИГАТЕЛЯ МЕХАНИЗМА ПОДЪЕМА НА ВРЕМЯ РАЗГОНА.
Так как тормоз на втором конце быстроходного вала редуктора, необходимо определить момент инерции тормозного шкива, который не входит теперь в состав муфты.
Момент инерции тормозного шкива:
, (1.52)
где: - масса тормозного шкива, = 41кг,
- радиус тормозного шкива, = 0,15м,
Не нашли, что искали? Воспользуйтесь поиском по сайту:
©2015 - 2025 stydopedia.ru Все материалы защищены законодательством РФ.
|