Метод оценки согласованности работы приводов (для станков с ЧПУ)
Диагностика станка с ЧПУ проводится при помощи электронно-механического прибора точностью +-0,5 мкм и программы для расшифровки и анализа полученных данных. В процессе испытания проводится контроль круговой траектории, выполняемой согласованными действиями приводов станка. Метод позволяет определить неисправности станка по 17 параметрам. Среди них люфты по каждой координате, боковые люфты, рассогласование скорости приводов, не перпенди-
кулярность осей, непрямолинейность по каждой оси. Результаты диагностики предоставляются заказчику в форме отчета, включающего графики, таблицы расшифровки и анализа неисправностей и рекомендации по их устранению. Время проведения испытаний одного станка, обработки информации и выдачи рекомендаций 2-3 часа.
Метод вибрационной диагностики
Диагностика любого типа металлообрабатывающего оборудования проводится при помощи датчика съема показаний вибрации (акселерометра), накопителя-
преобразователя сигнала (виброанализатора) и программы расшифровки и анализа полученных данных. В процессе испытания производится съем вибрационных характеристик с определенных точек станка, преобразование и трансляция их в программу для расшифровки данных. Метод позволяет определить 23 параметра механического износа и неисправностей узлов и деталей станка. Определяются дефекты каждого подшипника, в том числе износ наружного или внутреннего кольца, перекос наружного кольца, износ шариков или роликов, биение или перекос валов и шпинделей, износ каждой шестерни, погрешность зацепления каждой передачи, а также износ и дефекты деталей шариковинтовой пары: гаек, винта, шариков, перекос винта ШВП. Время подготовки и написания рабочей программы 1 день. Время для проведения диагностики одного станка в цехе и выдача рекомендаций 2-3 часа. По результатам испытаний оформляется отчет.ме
Применяемость методов безразборной диагностики
Данные методы диагностики и оценки технического состояния станочного парка внедрены на передовых отечественных и большинстве зарубежных предприятиях с 90-х годов.
Автомобильные, авиационные, ракетно-космические и машиностроительные заводы США, Японии, Англии и Франции проводят обслуживание станков только по их фактическому состоянию, когда ремонтируются/заменяются только те узлы и агрегаты, дефекты которых были выявлены в ходе безразборной диагностики.
Такой подход к организации технического обслуживания станочного парка обеспечивает стабильность работы производства, на 40% — 50% снижает затраты на ремонт и обслуживание станков, позволяет прогнозировать время безаварийной работы, планировать заказ запасных частей и замену оборудования. Техническое обслуживание оборудования с применением комплексных методов диагностики получило название предупредительное обслуживание или обслуживание по фактическому состоянию.
Второй вариант ответа
Различают следующие группы методов определения коэффициента физического износа при оценке машин и оборудования:
- экспертные;
- экономико-статистические;
- экспериментально-аналитические.
Экспертная группа методов основана на заключении специалистов-экспертов или оценщиков о фактическом техническом состоянии машин и технологического оборудования исходя из следующих факторов:
- внешнего вида;
- режима эксплуатации;
- состояния окружающей среды;
- периодичности технического обслуживания и ремонтов.
При использовании экспертных методов требуется высокий уровень знаний о конструкции и эксплуатационных характеристиках оцениваемых машин и технологического оборудования. К данным методам относятся:
- метод эффективного возраста;
- метод экспертизы состояния.
Экономико-статистические методы используются, когда имеется достоверная информация об эксплуатационных характеристиках и экономических показателях оборудования. К данной группе методов относятся:
– метод снижения доходности;
– метод стадии ремонтного цикла.
При использовании экспериментально-аналитической группы методов требуется проведение испытаний оборудования на точность, правильность функционирования, а также наличие нормативно-технической документации. К данной группе методов относятся:
- метод снижения потребительских свойств;
- метод поэлементного расчета;
- прямой метод.
Использование того или иного метода определения коэффициента физического износа при оценке оборудования зависит от цели оценки, стоимости оцениваемого оборудования, полноты информации об оцениваемом оборудовании и т.д. В каждом конкретном случае оценщик сам должен сделать вывод о возможности и необходимости применения того или иного метода.
Вопрос 3
Частота появления неисправностей может быть обусловлена многими факторами. Важнейшим по моему мнению является на сколько качественно и своевременно выполнено тех. Обслуживание. Частота неисправностей будет максимальной на этапе ввода в эксплуатацию оборудования и также на этапе критического износа. Минимальная частота неисправностей будет между этими двумя этапами. Причины возникновения неисправностей на этапе ввода в эксплуатацию обусловлены не качественной сборкой и изготовления бракованных деталей оборудования. Неисправности наблюдаются в определенных узлах и после их устранения при правильном тех. Обслуживании проявятся только на этапе критического износа. В случае с этапом критического износа всё очевидно. Детали узлов оборудования имеют большой износ и постепенно начинают выходить из строя увеличивая частоту появления неисправностей.
Вопрос 4
Можно выделить ряд основных факторов, которые условно делят на две группы:
· субъективные, которые во многом зависят от деятельности человека (выбор схемного и конструктивного решения при проектировании машины, выбор элементов и материалов, организация рациональной системы Р и ТО в период эксплуатации и т.п.);
· объективные (неблагоприятное влияние внешней среды, связанное с климатическими, методологическими, биологическими, физико-химическими и другими воздействиями).
Кроме того, все факторы, влияющие на надежность, делят на факторы, увеличивающие ее и уменьшающие. К первым, повышающим безотказность и долговечность, относятся выбор надежных элементов, резервирование, облегчение режимов эксплуатации, теплозащита, герметизация, виброизоляция, оптимизация схем и конструкций, автоматизация контроля параметров. К параметрам, снижающим надежность оборудования, можно отнести объективные факторы (температуру, давление, радиацию, старение, изнашивание) и субъективные (недоработки схем и конструкций, неоптимальный режим работы, нарушение технологии изготовления, нарушение правил эксплуатации).
Анализ работы оборудования показывает, что потеря работоспособности является следствием одновременного воздействия случайных, внезапных повреждений и постепенных процессов изнашивания и старения деталей оборудования.
Закономерности появления случайных отказов и повреждений определяются методами теории вероятности и математической статистики.
Закономерности, описывающие процессы изменения свойств и состояния материалов в условиях их эксплуатации, изучаются в разделах физики отказов.
Знание физических закономерностей процессов дает возможность прогнозировать надежность деталей и более точно оценивать надежность оборудования.
Физические закономерности процесса изнашивания описываются конкретными законами. Но по причине многообразия и переменности действующих факторов эти зависимости приобретают вероятностный характер, и поэтому при анализе изнашивания используется математический аппарат теории вероятности и математической статистики.
Пусть скорость некоторого процесса разрушения материала зависит от ряда входящих параметров и времени, то есть
(28)
Здесь параметры xi характеризуют условия эксплуатации, состояния материала и другие факторы, влияющие на протекание процесса разрушения, меняющиеся во времени.
При работе машины происходят непредвиденные изменения и колебания нагрузок, поэтому приведенная функциональная зависимость приближенно отражает физическую сущность процесса, но она может предсказать возможный ход процесса при различных сочетаниях параметров.
Существо проблемы надежности заключается, в конечном счете, в изменчивости материалов и элементов во времени при заданных условиях эксплуатации. Поэтому знание проблем надежности связано с изучением представлений о процессах разрушения материалов, их изменчивости во времени при заданных условиях эксплуатации. Любой отказ возникает, как правило, в результате постепенного накопления необратимых изменений в элементах (кроме случаев непредвиденной концентрации нагрузок).
Изучение влияния совместного действия силовых и физико-химических факторов, взаимодействия трущихся поверхностей с учетом их геометрических и физических свойств и поверхностных явлений в связи со смазкой и наличием ПАВ позволяет полученные закономерности на субмикроскопическом уровне распространить на всю рабочую поверхность. Полученные в результате такого анализа физические закономерности используются при оценке работоспособности оборудования и разработке мероприятий по повышению его надежности.
Для чистых металлов, сплавов, полимеров, полупроводников и других материалов экспериментально установлены температурно-временные зависимости между напряжением s, температурой t0, временем t от момента приложения постоянной механической нагрузки до разрушения. Как правило, эти зависимости имеют экспоненциальный характер. Металлы и сплавы по-разному разрушаются в зависимости от температуры: в низкотемпературной области, характеризующейся большими напряжениями и сравнительно низкой температурой, механизм разрушения определяется последовательным разрушением атомных связей в кристаллической решетке; в высокотемпературной, характеризуемой малыми напряжениями и высокой температурой, механизм разрушения определяется ростом трещин за счет сосредоточения вакансий.
В процессе дальнейшего нагружения за счет сдвига материала смежные трещины соединяются друг с другом до полного разрушения. Рост трещин может происходить в две стадии: медленный рост с увеличивающейся скоростью, быстрый рост с постоянно предельной скоростью, близкой к скорости звука в материале. На первой стадии разрыв связей происходит за счет избытка кинетической энергии, накопленной вследствие флутаций атомов молекул. Ее вероятность тем больше, чем выше температура и больше напряжения у вершины трещины. Во второй стадии разрыв определяется локальными напряжениями, близкими к молекулярной прочности.
Рассмотрим влияние некоторых факторов на процесс разрушения:
· характер изменения нагрузки и его влияние на трещины. При медленном увеличении нагрузки происходит упругая деформация, пластическое течение материала и затем наступает резкое упрочнение и разрыв (рис. 34);
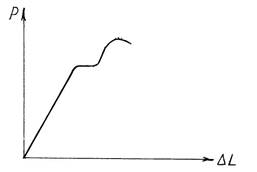
Рис. 34. Диаграмма растяжения стальных деталей (образцов)
· при большой скорости нарастания механического нагружения происходит хрупкое (без удлинения) разрушение большинства материалов;
· поверхностно-активные вещества. Они в большинстве случаев способствуют разрушению материалов. Поверхностный слой металла из-за наличия в нем свободных связей обладает большой активностью. Поэтому любая внешняя поверхность твердого тела покрыта всегда тончайшей пленкой вещества, содержащегося в окружающей среде (газов, паров жидкостей и других адсорбированных веществ). Органические ПАВ имеют значительную по величине дифильную молекулу, которая не может дифундировать в кристаллическую решетку металла. Поэтому их действие чисто поверхностное. Своей карбоксильной группой молекулы ПАВ прочно закрепляются на поверхности металла, образуя монослой из плотно расположенных молекул. Пленка может выдерживать давления до 1·102 МПа. При этом трение в подвижных сопряжениях происходит не между поверхностями металлов, а между поверхностями масляных пленок. В этом состоит защитное действие смазок с ПАВ;
· тепловое разрушение материалов в виде плавления или испарения;
· старение материалов (объясняемое изменением их физико-механических свойств со временем, в условиях длительного хранения и эксплуатации).
Все эти представления о следствиях и причинах образования механических разрушений в материалах необходимы для понимания изнашивания (основного параметра, определяющего работоспособность оборудования). Согласно ГОСТ 23.000-78 изнашивание – процесс разрушения и отделения материала с поверхности детали и (или) накопления его остаточной деформации при трении, проявляющийся в постепенном изменении размеров и (или) формы детали.
Вопрос 5
Не нашли, что искали? Воспользуйтесь поиском по сайту:
©2015 - 2024 stydopedia.ru Все материалы защищены законодательством РФ.
|