СПОСОБЫ ХРАНЕНИЯ И ДОСТАВКИ ЧУГУНА В СТАЛЕПЛАВИЛЬНЫЕ ЦЕХИ
Способы хранения и доставка чугуна в сталеплавильные цехи. В практике сталеплавильного производства применяются два способа хранения и транспортировки жидкого чугуна в сталеплавильные цехи:
- чугуновозами небольшой емкости (до 140 т) от доменного в сталеплавильные цехи на небольшие расстояния к миксерам различной емкости;
- передвижными миксерами большой емкости в отделения перелива чугуна (в конвертерный пролет).
Ранее многие заводы работали с применением стационарных миксеров. В последующем вновь вводимые сталеплавильные цехи используют передвижные миксера большой емкости.
В примерном расчете рассматриваются обе схемы подачи жидкого
чугуна к конвертерам.
• Выбор емкости и определение количества миксеров. В настоящее время в отечественной практике эксплуатации сталеплавильных цехов используются типовые миксеры емкостью 600, 1300 и 2500 тонн.
В целом рекомендуется стремиться к установке в миксерном отделении возможно меньшего количества миксеров. Чаще всего, исходя из условий здания независимой отхода доменных печей работы конвертеров, устанавливают не менее двух (но не более трех) миксеров.
Необходимая общая (суммарная) емкость миксеров (ΣGмикс) может быть определена из следующего выражения:

где
А - 16597,09 - суточная производительность проектируемого цеха в годных слитках, т;
= 6 - принятое в проекте среднее время пребывания чугуна в миксере, необходимое для выравнивания его химического состава и температуры, час (обычно принимается в пределах 6...9 час, но не менее 6 час);
η = 0,85 - коэффициент заполнения миксера (обычно зависит от неравномерности заливки чугуна в миксер и выдаче его из миксера; колеблется в пределах 0,65...0,77, реже эта величина принимается в пределах
0,75...0,85);
1,01 - коэффициент, учитывающий потери чугуна в миксере;
Кчуг - расход чугуна на тонну годных слитков, т/т;
24 - количество часов в сутках.
Расход чугуна на тонну годных слитков определяется из выражения:

где 77 - содержание жидкого чугуна в металлошихте, % (берется по расчету шихты конвертерной плавки после исправления операции).
Подставляя известные и определенные расчетом величины в формул)- общей (суммарной) емкости миксеров, получим необходимую суммарную емкость миксеров в проектируемом цехе:

При емкости миксера 2500т, количество миксеров будет равно

Если принять к установке два миксера по 2500т, то среднее фактическое время пребывания жидкого чугуна в миксере составляет:

• Оборудование миксерного отделения. Основное оборудование мнксерного отделения состоит из мостовых заливочных кранов, чугуновозных и шлаковозных тележек с ковшами (чашами), стендов для шлаковых ковшей (чаш), весов железнодорожного типа для взвешивания чугуна, самоходных тележек и тепловозов (электровозов) для подачи чугуна к конвертерам.
Емкость чугуновозных ковшей для подачи чугуна из доменного цеха в миксерное отделение в современных сталеплавильных цехах обычно составляет 100 или 140 т, при грузоподъемности заливочных кранов 125/30
или 180/50 т.
Количество чугуновозных ковшей (тележек) в составе обычно 2...4 единиц. Последнее зависит от емкости ковшей, мощности тепловоза (электровоза) и принятой системы организации подачи чугуна к конвертерам.
Для взвешивания чугуна используются весы железнодорожного типа, по одному на каждый миксер, грузоподъемность которых зависит от емкости применяемых чугуновозных ковшей.
В проектируемом цехе (рассматриваемый примерный расчет) принята транспортировка жидкого чугуна из доменного цеха в миксерное отделение в ковшах емкостью 140 т. Заливка чугуна в миксеры производится заливочными кранами грузоподъемностью 180/50 т.
Рекомендуемый коэффициент загрузки заливочных кранов в миксерном отделении принимается равным 0,87. Определим их необходимое количество:

где - суммарная загруженность крана на одну тонну чугуна, сливаемого в миксер, мин;
А - суточная производительность цеха в годных слитках, тыс.тонн;
Кчуг - коэффициент расхода чугуна на тонну годных слитков, т/т. Суммарная загруженность крана на заливке одной тонны чугуна в миксер ) зависит от продолжительности заливки одного ковша чугуна в миксер, емкости чугуновозного ковша и степени (коэффициента) его заполнения, а также загруженности крана на вспомогательных работах (обычно 15 % от основных работ) и может быть определена по формуле:
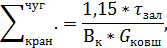
Где – продолжительность операции заливки в миксер одного ковша чугуна, мин (по данным практики, в зависимости от емкости ковша и других конкретных условий работы в отделении, может быть принята в пределах 12…19 мин);
Вк – коэффициент заполнения ковша (0,8…0,9);
Gковш – емкость чугуновозного ковша, т.
Принимаемая для условий проектируемого цеха продолжительность операции заливки одного ковша чугуна в миксер (Gковш=140 т) равной 12…14 мин ( ), коэффициент заполнения ковша Вк = 0,9, суммарная загружаемость заливочного крана на одну тонну чугуна составит:

Подставляя выбранные и принятые величины в формулу определения числа заливочных кранов для заливки чугуна в миксер вычислим необходимое количество заливочных кранов в миксерном отделении проектируемого цеха:

Прнимаем два заливочных крана грузоподъемностью 180/50 т каждый, тогда фактическая загруженность заливочных кранов в миксерном отделении проектируемого цеха составляет:
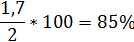
Таким образом, подтверждаются данные практики об установке на каждый миксер свой заливочный кран.
Для обеспечения заливки чугуна в конвертер в один прием емкость чугуновозных ковшей для подачи чугуна из миксерного отделения к конверторам должна быть на 20...30 % больше номинальной емкости конвертера и равной емкости сталеразливочного коша.
В соответствии с этим грузоподъемность заливочных кранов должна быть равной Грузоподъемности разливочных кранов, как это следует из следующей таблицы (рекомендуемые емкости сталеразливочных (и заливочных) ковшей и грузоподъемности разливочных (заливочных) кранов для сталеплавильных агрегатов (конвертеров) различной емкости).
Техническая характеристика
| Емкость стали
| Емкость разливочного (заливочного) ковша, т
|
|
|
|
|
|
|
|
|
|
|
|
|
|
|
|
|
|
|
|
|
Грузоподъемность разливочного (заливочного) ковша, т
| 140/30
| 180/50
| 205/63
| 280/100/16
| 300/100/16
| 400/100/16
| 450/100/20
| 500/100/16
| 560/100/16
| 630/100/16
| Грузоподъемность кранов в
ковшевом пролете
| 50/10
| 20/10
| 80/16
| 125/30
| 125/30
| 125/30
| 125/30
| 125/30
| 140/32
| 140/32
|
В проектируемом цехе для конвертеров с фактической садкой 300 т (вес жидкой стали 264,195 т) для подачи чугуна к конвертерам приняты чугуновозные ковши емкостью 350 т, а грузоподъемность заливочных кранов загрузочного пролета 450/100/20 тонн.
Однако следует иметь ввиду, что (в данном случае) современному кислородно-конвертерному цеху с производительностью около 27000 тонн стали в сутки нецелесообразно иметь три стационарных миксера. Во-первых, они теряют роль усреднителя чугуна по температуре и составу; во-вторых, - становится весьма напряженным грузопоток чугуна; и, в-третьих, - строительство их экономически нецелесообразно.
Рассмотрим второй вариант снабжения конвертерного цеха чугуном.
• Выбор емкости и определение количества передвижных миксеров. Использование передвижных миксеров, помимо решения чисто транспортных проблем, дает значительный эффект благодаря сокращению капиталовложений в основные сооружения, так как отпадает необходимость постройки миксерных отделений. Кроме того, значительно улучшается организация производства, сокращается потребность в подвижном составе, снижаются потери тепла при перевозке чугуна в открытых ковшах, сокращается количество переливов. Пользуясь таблицей приведенной ниже, выбирается для рассматриваемого случая передвижной миксер емкостью 420 т.
Таблица 5,1 – технические характеристики передвижных миксеров
параметры
| Емкость, т
| 135…150
|
|
| Скорость передвижения (в груженном состоянии), км/ч
|
|
|
| Частота поворота, об/мин:
Максимальная
| 0,5
| 0,5
| 0,5
| Минимальная
| 0,2
| 0,2
| 0,2
| Габаритные размеры, мм:
Диаметр корпуса (наружный)
|
|
|
| Диаметр по осям автосцепок
|
|
|
| Общая масса миксера в груженном состоянии, т
|
|
|
| Стойкость футеровки, наливов
| 400-800
| 400-800
| 400-800
|
Количество передвижных миксеров, находящихся в обороте определяется следующим образом:
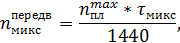
Где – максимально возможное количество плавок в чехе за сутки;
τмикс – время оборота одного миксера, мин;
1440 – количество минут в сутках.
Принимается τмикс – 5 часов (180…300 мин). Время оборотов передвижных миксеров выбирается в зависимости от системы организации грузопотока чугуна от доменного цеха до сталеплавильных агрегатов, особенностей и структуры металлургического производства и колеблется в значительных пределах (от 3 до 5 часов). Уместно напомнить, что миксера сверхбольшой грузоподъемности предназначены только для внутризаводских перевозок.
При = 69 и τмикс = 5 часов (300 мин)

При стойкости футеровки миксера 400 наливов (400…800) в ремонте за сутки побывает:
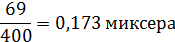
Что составляет = 1,2% от количества находящихся в работе миксеров.
При продолжительности ремонта одного миксера 6 суток (5…8) количество одновременно находящихся в ремонте миксеров составит
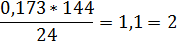
Принимается количество находящихся в ремонте передвижных миксеров равное 2. С учетом на непредвиденные задержки принимается, что 10% рабочего парка передвижных миксеров находится в резерве, то есть
(14 + 2) * 0,1 = 1,6 = 2 (миксера)
Таким образом, общее количество передвижных миксеров в рассматриваемом случае (примерный расчет) составит
14 + 2 + 2 = 18 (миксеров)
• Определение количества необходимого оборудования. Если в цехе одновременно работают 2 конвертера, причем из каждого из них выпускают плавку с интервалом 42 минут (продолжительность плавки), то при помощи чугуновозной тележки, обслуживающей оба конвертера, подают чугун через каждые 42 : 2 = 21 мин (то же при заливке краном).
Количество чугуновозных ковшей, находящихся в обороте, определяется по формуле:

Где – максимально возможное количество плавок в цехе за сутки;
– время оборота одного ковша, минут;
1440 – количество минут в сутках.
Принимается (исходя из практических данных 8…24) .
Тогда количество одновременно находящихся в обороте чугуновозных ковшей в цехе составит:
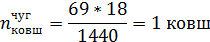
При стойке футеровки ковша 100... 150 наливов в ремонте за сутки
побывает (принимается 100 наливов)
69/ 100 = 0,69 (ковшей).
При продолжительности ремонта одного ковша (6...8) часов, будет
находиться в ремонте
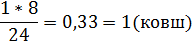
С учетом времени на непредвиденные задержки по смене футеровки,
механическому ремонту ковшей и необходимого резерва общее количество
чугуновозных ковшей в цехе составит
1 + 1 + 1 + 1 = 4 (ковша).
Для нормальной работы цеха по обеспечению сталеплавильных агрегатов чугуном, поступающим из отделения перелива чугуна в загрузочный пролет конвертерного отделения, может быть принято (с учетом резерва, текущей профилактики и ремонта) 2 чугуновозных тележки.
Число чугуновозных ковшей для транспортировки необходимого количества чугуна из доменного цеха в миксерное отделение сталеплавильного цеха можно определить по формуле:
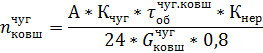
Где – необходимое число чугуновозных ковшей в сутки;
А – суточная производительность конвертерного цеха, т;
- длительность цикла оборота ковша (5…7 час);
– коэффициент неравномерности выпуска чугуна (1,25);
0,8 – коэффициент заполнения ковша чугуном;
- номинальная емкость ковша, т.

Загрузочный пролет
Выбор типа и определение необходимого количества основного оборудования в загрузочном пролете. Основные грузопотоки загрузочного пролета связаны с подачей скрапа и чугуна и последующей загрузкой их в конвертер.
Кроме того, в пролете осуществляется прием и хранение ферросплавов и огнеупоров. Для обеспечения быстрой завалки и устранения простоев конвертеров, транспортировка и загрузка необходимого вида материалов в агрегат производится отдельными механизмами и машинами.
Так, при емкости конвертеров до 130/160 т и наличии шихтового двора в направлении загрузочного пролета подача совков с ломом производится по железнодорожному пути нормальной колеи, ближайшему к конвертерам. В случае расположения шихтового пролета параллельно конвертерному - подача лома производится на уровне пола цеха по поперечным путям и в загрузочном пролете имеются только два пути для подачи чугуна.
При емкости конвертеров более 250 т подача ковшей с чудном осуществляется по путям широкой колеи (3,0...4,5 м). Соосно с этими путями прокладываются пути нормальной колеи для подачи в пролет железнодорожных вагонов.
Для подачи огнеупоров по полу цеха (пролета) уложен тупиковый железнодорожный путь.
Завалка лома и заливка жидкою чугуна в конвертер производится установленными в пролете специальными завалочными и заливочными кранами, 1рузоподьемность которых определяется емкостью совков и чугуновозных ковшей.
Планировкой конвертерного отделения (случаи раооты цеха на литую заготовку) предусмотрены подача чугуна и лома в загрузочный пролет с разных торцов на отметке ±0,00 м (хотя возможны и другие варианты), завалка лома и заливка чугуна на плавку одной порцией литейными кранами, выдача стали и шлака от конвертеров в разные стороны.
В проектируемом цехе, с классической системой организации работ по схеме работы цеха на слиток (то же и на литую заготовку), для обеспечения заливки чугуна в один прием с учетом увеличения массы плавки вследствие разгара футеровки конвертера, а также в случае работы с повышенным расходом чугуна в металлошихте приняты чугуновозные ковши емкостью 350 т, а грузоподъемность заливочных кранов 450/100/20 т (см табл. выше).
Количество заливочных кранов в загрузочном пролете может быть определено из выражения:

Где – суточный расход чугуна, тыс. тонн;
1,13 – коэффициент неравномерности;
- суммарная загруженность крана на 1 тонну чугуна, мин.
В зависимости от емкости чугуновозных ковшей, коэффициент расхода чугуна на тонну слитков (литых заготовок) и других условий суммарная загруженность заливочных кранов ( ) по практическим данным колеблется в довольно широких пределах 0,1…0,25 мин/т чугуна. В данном расчете , тогда:

Где А – 16597,09 – максимальная суточная производительность цеха в годных слитках, тыс. тонн;
Кчуг=0,92 – коэффициент расхода чугуна на тонну годных слитков, т/т.
Используя известные величины в ранее приведенном выражении, определяется необходимое количество заливочных кранов в загрузочном пролете:

Принимается в расчете два заливочных крана грузоподъемностью 450/100/20т, одновременно определяется загруженность их в загрузочном пролете:

Для завалки лома в конвертер чаще всего используются полупортальные краны, имеющие по два подъема для завалки двух лотков (совков) лома. 13 пролете предусматривается по одному полупорталу на каждый непрерывно работающий конвертер, но не менее двух.
При рабою цеха на литую заготовку возможен вариант подачи металлолома из шихтового отделения скрапоразделочного цеха, в случае расположения последнего в близи конвертерного цеха, в совках емкостью 110 м3, установленных на самоходном скраповозе (скраповоз оборудуется тензометрическими весами для взвешивания массы лома в совке). Лом загрузочным краном грузоподъемностью 450/100/20 т заваливается в конвертер.
Число ( ) заливочных кранов и мостовых кранов для загрузки лома ( ) можно определить также и по формуле:
Где – число плавок в цехе за сутки, пл/сут;
Σ – загруженность крана на одну плавку (на заливку одного ковша или загрузку одного совка), мин/пл;
К – коэффициент, учитывающий выполнение вспомогательных работ
b – коэффициент использования крана (0,8);
1440 – число минут в сутках, мин/сут.
Загруженность крана на заливку чугуна складывается из опускания траверсы, захвата ковша и его подъема, переезда к конвертеру, заливка чугуна (2…3 мин) и выполнения обратных работ. При доставке заливочных ковшей по рабочей площадке загруженность крана £ составит 6...8 мин, при доставке в торец загрузочного пролета на нулевой отметке 10... 12 мин.
При загрузке лома одним совком кран выполняет те же операции, что и при работе с чугуновозным ковшом, собственно загрузка длится 1...1,5 мин. Загруженность крана Σ при доставке совков в пролет по полу цеха также составит 10...12 мин. Часть снятых со скраповоза совков ставят на пол цеха, где они ожидают начала загрузки. Такая дополнительная перестановка увеличивает загруженность крана на 3.. .4 мин.
4.3 РАЗЛИВОЧНЫЕ ПРОЛЕТЫ
Разливочные пролеты. Назначение, планировка и оборудование. Объемно - планировочное решение кислородно-конвертерных цехов классической системы организации работ (при работе на слиток) предполагает наличие (как в случае конвертерного цеха «Миттал Стил Темиртау» до модернизации) двух примыкающих друг другу разливочных пролета, расположенных в главном здании цеха параллельно конвертерному пролету. Основное назначение этих пролетов - прием и разливка стали по изложницам, а также прием и уборка шлака и выполнение других вспомогательных робот.
Пролеты снабжаются сквозными и тупиковыми железнодорожными путями, а также оборудованием необходимые для разливки стали и уборки мусора и шлака.
К основному оборудованию разливочных пролетов относятся разливочные краны, сталеразливочные ковши и шлаковые чаши, изложницы и тележки, разливочные площадки; к вспомогательному - устройства для сушки стопоров шиберных затворов), стенды для размещения сталеразливочных ковшей и таковых чаш и т.д.
Для механизации работ по подготовке ковшей в разливочных пролетах используются консольные краны (по одному в пролете). Основные характеристики оборудования и его количество (грузоподъемность кранов, емкость ковша и т.д.) определяются производительностью проектируемого или модернизируемого цеха, емкостью установленных в цехе конвертеров, принятым способом разливки и т.п.
• Грузоподъемность разливочных кранов определяется максимально возможным весом (массой) металла и шлака в сталеразливочном ковше и массой самого ковша.
Рекомендуемые грузоподъемности разливочных (как и заливочных) кранов для сталеплавильных агрегатов различной емкости приведены в таблице (см. выше), а также в справочной литературе. Гам же приведены их основные габаритные размеры (характеристики). В проектируемом цехе для конвертеров емкостью 300 тонн грузоподъемность разливочных кранов, как и завалочных (см. выше), принята равной 450/100/20 т.
• Необходимое количество разливочных кранов (без учета резервных) определяется их занятостью на операциях по разливке стали и на вспомогательных работах (смена шлаковых чаш, уборка мусора и т.п.), то есть загруженностью крана на тонну слитков ( ) и суточной производительностью цеха. С учетом коэффициента неравномерности выпуска плавок, равном 1,13, необходимое количество разливочных кранов можно определить из выражения:

Где А – максимальная суточная производительность цеха в годных слитках, тыс. т;
- общая загруженность крана на разливке и вспомогательных работах, мин/т слитков.
В зависимости от емкости сталеразливочных ковшей (массы плавки), принятой скорости и других условий разливки, а также занятости разливочных кранов на вспомогательных работах, общую загруженность разливочного крана на тонну годных слитков ( ), можно принять равной 0,25...0,5 мин (исходя из практических данных).
В рассматриваемом случае, при разливке стали сверху в крупные слитки (массой 22 т, например) с повышенной скоростью наполнения одновременно двух слитков (через два стопора), принимаем = 0,28 мин/т. В этом случае количество разливочных кранов в цехе составит:

Отсюда следует, что необходимо принять 6 разливочных кранов грузоподъемностью 450/100/20 т; четыре разливочных крана в первом разливочном пролете и два крана во втором. Фактическая загруженность разливочных кранов в цехе при этом составит:
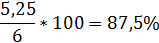
· Количество сталеразливочных ковшей, находящихся в обороте, может быть определено из выражения:

Где – максимальное количество плавок в сутки;
– время оборота одного ковша, мин;
1440 – количество минут в сутах.
В рассматриваемом расчете принято равным 8 (практическое значение 6...9 часов). Количество одновременно находящихся в обороте сталеразливочных ковшей будет равно:

При стойкости футеровки ковша, например, 12 плавок (практические значения колеблются в широких пределах 10...20 плавок) в ремонте в течение
суток побывает 69:12=5,8 ковша, что составляет от количества
находящихся в обороте ковшей. При продолжительности ремонта одного ковша 7 часов, одновременно будет находиться в ремонте%
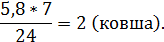
Таким образом, для ремонта ковшей в ковшевом отделении должно быть не менее двух одноместных ремонтных ям. С учетом на непредвиденные задержки следует принять, что 10 % рабочего парка ковшей находится в резерве (23*0,1 =2 ковша).
Следовательно, общее количество сталеразливочных ковшей в рассматриваемом случае составит 23+2 + 2 =27 (ковшей).
5.4 тянущее устройство
• Тянущее устройство. В зависимости от типа МНЛЗ (вертикальная, вертикальная с изгибом, радиальная, криволинейная, горизонтальная) тянущее устройство представляет собой клеть с балками, обеспечивающими необходимую скорость вытягивания слитка (заготовки), причем равномерно и с заданной скоростью.
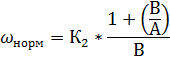
Где К2 - коэффициент, зависящий от ранее отмеченных параметров со значениями (0,14 и 0,11).
Для заготовок квадратного сечения
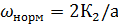
В условиях реальной практики работы сталеплавильным агрегатом и МНЛЗ, а также совершенствования технологии разливки и конструкции МНЛЗ возможны изменения расчетных скоростей разливки до 20%.
В рассматриваемом случае при К=340 и К,=0,30 нормативная скорость разливки слябов:

(с возможным максимальным увеличением до )
Металлургическая длина в рассматриваемом случае будет равна:

Где 1,15 – коэффициент, учитывающий величину резерва металлургической длины МНЛЗ.
Для определения металлургической длины рассчитываем протяженность жидкой фазы (м) согласно выражению:

Где – скорость разливки, рассчитанная из времени разливки, равного или кратного ритму поступления плавок из конвертерного отделения, м/мин;
А – толщина заготовки, мм.

Тогда металлургическая длина будет равна:

Следует отметить, что для оценки общей длины МНЛЗ (/-общ) необходимо учитывать протяженность участка от конца металлургической длины до конца приемного рольганга (рольганг перед газорезкой, устройства отцепления затравки и порезки заготовок на мерные длины, клеймитель, устройство хранения затравки, приемные и транспортные рольганги, устройства поперечной передачи заготовок), которая порой составляет от 25 до 50 м и зависит от типоразмера и мерной длины отливаемых заготовок.
• Определение параметров разливки. Ранее уже отмечалось, что параметры разливки стали на МНЛЗ определяются размерным и марочным сортаментом в сочетании с учетом максимально допустимой продолжительности разливки металла из сталеразливочных (и естественно, из промежуточных) ковшей необходимой вместимости.
Руководствуясь приведенными ниже данными, сочетающими максимально возможную продолжительность разливки стали из сталеразливочных ковшей (Треал, мин) различной емкости и рекомендуемую для расчетов реальную продолжительность разливки (Тмах, мин) можно выбрать наиболее оптимальные значения параметров с учетом возможностей согласования «плавильный аппарат - МНЛЗ»
Емкость ковша, м3
|
|
|
|
|
| Тмах, мин (углеродистых и низколегированных сталей)
|
|
|
|
|
| Треал, мин (легированных сталей)
|
|
|
|
|
|
Расчет параметров разливки возможно осуществить после определения количества ручьев МНЛЗ
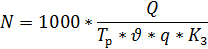
Где Q – масса разливаемой стали, т;
– нормативная скорость разливки, м/мин;
q – масса погонного метра литых заготовок, кг;
K3 = 0,9 – коэффициент, учитывающий непредвиденные потери времени во время разливки.
Масса погонного метра литой заготовки:
Тогда

Время разливки Тр (мин), при нормальной скорости для каждого сечения размерного сортамента обратно количеству ручьев:


Скорость разливки, м/мин:
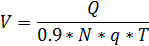
Где Т – время разливки, равное или кратное ритму поступления сталеразливочных ковшей в отделение.

Протяженность жидкой фазы равно, как и металлургическая длина МНЛЗ была найдена ранее и составляет соответственно 16,6 и 19,1 м.
Результаты расчетов сводятся в таблицу для анализа полученных результатов и проверки следующих условий:
V≤Vнорм+20%
| 2,17≤2,1+20%
| Тр≤Т<Тмах
| 39,1≤39,1<60
|
Расчет параметров вакуумной камеры циркуляционного типа для обработки металла в 290-тонном сталеразливочном ковше.
Основные параметры циркуляционного вакууматора и их расчеты
Как показывает опыт эксплуатации вакуумных установок циркуляционного типа, скорость циркуляции металла или расход металла через вакуумную камеру могут быть определены из соотношения:

Где
Qm – расход металла т/мин;
М – масса металла в сталеразливочном ковше, т;
К – кратность циркуляции;
τ – время, необходимое для вакуумирования металла.
Принимая размеры подъемного и сливного патрубков одинаковыми площадь поперечного сечения патрубков можно оценить из условия минимальной мощности перемешивания маталла в ковше за счет истечения расплава из сливного патрубка. Для определения мощности струи металла, используем выражение:

Где
W – мощность струи, Вт;
S – площадь поперечного сечения патрубка, м2;
р – плотность металла, т/м3;
u – скорость истечения металла, м/с.
Исследования, проведенные сотрудниками МИСиС, позволили получить соотношение, связывающее между собой поперечные сечения рукавом, скорость истечения металла, расхода и уровень ввода газа:
Где
Qr – расход несущего газа при фактических значениях температуры и давления, м3/с;
g – ускорение силы тяжести, м/с2;
h – уровень ввода несущего газа, м;
µ - коэффициент расхода;
– скорость движения газового пузыря относительно жидкости.
Величина 

Используя выражение для мощности истекающей струи металла, можно получить

Дифференцируя W по u и приравнивая производную нулю, можно получить уравнение для определения оптимальной скорости металла в сливном патрубке

Это уравнение может быть решено численно, например, методом последовательных приближений.
При м/с и это уравнение может быть записано в виде

Это значит, что если выбран уровень ввода газа h, то соответствующая ему скорость истечения металла в сливном рукаве является оптимальной, то есть поддержание этой скорости в патрубке за счет регулирования расхода газа, подводимого к подъемному рукаву, обеспечивает максимальную мощность перемешивания в ковше.
Так как расход металла через вакуумную камеру определен в зависимости от решения технологической задачи коэффициентом кратности циркуляции, то площадь поперечного сечения камеры может быть определена из соотношения:
или , м2.
По уравнению вычисляется расход несущего Qr газа при фактических значениях температуры и давления. Остальные параметры вакуумной камеры выбираются из конструктивных соображений.
Согласно заданию на курсовое проектирование, необходимо рассчитать и спроектировать вакуумкамеру циркуляционного типа для обработки металла в 290-тонном сталеразливочном ковше. Принимаем кратность циркуляции К=4, время вакуумной обработки 16 минут.
Применяя формулу (000), находим скорость циркуляции металла через вакуумную камеру:
т/мин.
Приняв уровень ввода аргона и подъемный патрубок h=1,15 м, получим скорость истечения металла в сливочном патрубке:

м/с
Применяя формулу (000) находим площадь поперечного сечения рукава и его диаметр
м2;
мм.
Принимаем D=600 мм.
При помощи формулы (000) находим расход несущего газа:
м3/с.
Для нахождения расхода газа при нормальных условиях необходимо определить уровень металла в вакууматоре. Для этого необходимо определить поперечное сечение камеры. Диаметр камеры можно найти из условия, что в днище должны разместиться два патрубка:
,
Где
l1 – расстояние между внутренними стенками патрубков,
l2 – расстояние от внутренней стенки патрубка до цилиндрической части.
Расстояние между патрубками l1(рис. 000) зависят от их конструкции и включает толщину внутренней футеровки патрубков, толщину металлической арматуры патрубков и фланцев для их крепления, если они разъемные, или толщину наружной футеровки:
,
Где
– расстояние между кожухами патрубков (300…400 мм)
– толщина рабочего слоя внутренней футеровки патрубка (периклазохомитовые изделия толщиной 125мм);
– толщина набивной массы между рабочим слоем и металлическим кожухом (40мм);
– толщина металлического кожуха (20…30мм);
м

Не нашли, что искали? Воспользуйтесь поиском по сайту:
©2015 - 2024 stydopedia.ru Все материалы защищены законодательством РФ.
|