КОНСТРУИРОВАНИЕ КОРПУСНЫХ ДЕТАЛЕЙ
Корпус редуктора обычно образован двумя деталями: основанием корпуса и крышкой корпуса. Исключение составляют планетарные редукторы и червячные редукторы малых размеров, у которых корпус состоит из основной детали (собственно корпуса) и двух торцевых крышек с расточками под подшипники.
Размеры корпуса редуктора определяются числом и размерами размещённых в нём деталей, относительным их расположением, величинами зазоров между ними. Ориентировочные размеры корпуса и зазоров определяют при составлении компоновочной схемы редуктора и конструировании валов, теперь же следует их уточнить.
Корпуса современных серийных редукторов очерчивают плоскими поверхностями, все выступающие элементы вводят внутрь корпуса, проушины для транспортировки редуктора выполняют заодно с корпусом. Для удобства сборки плоскость разъёма проходит через оси валов. Плоскость разъёма и верхнюю поверхность крышки корпуса, как правило, выполняют параллельными установочной плоскости.
Для редукторов общего назначения, когда неизвестны тип и мощность двигателя, рекомендуются следующие формулы для нахождения толщины основания и крышки корпуса, а также диаметра стяжного болта:
толщину стенки основания корпуса определяют по эмпирической формуле
(8.1)
с округлением до целого числа;
толщину стенки крышки корпуса - по формуле
(8.2)
диаметр стяжного болта (винта) крепления крышки корпуса редуктора к основанию - по формуле
(8.3)
Используют болты по ГОСТ 7798-70 или ГОСТ 7808-70.
Диаметр фундаментного болта
(8.4)
с округлением до ближайшего стандартного значения.
Число фундаментных болтов Zф принимают в зависимости от межосевого расстояния: при aw≤250 мм Zф=4, при aw > 250 мм Zф=6.
Диаметр установочных штифтов dшт = (0,7...0,8) dст с округлением до ближайшего стандартного значения по ГОСТ 3129-70 или ГОСТ 9464-70.
При размещении отверстий под болты (винты) крепления крышки к корпусу:
—отверстия располагают преимущественно по продольным сторонам;
—у бобышек стараются максимально приблизить их к отверстию под подшипник, то есть оставляют стенку минимальной толщиной, равной радиусу отверстия под стяжной болт (для увеличения жёсткости соединения);
—минимальное расстояние между стенками близко расположенных отверстий должно составлять не менее 5 мм;
—на длинных боковых сторонах помимо болтов у подшипниковых гнёзд устанавливают дополнительно болты на фланцах на расстоянии один от другого с шагом (10 ...12)d.
Диаметры отверстий под стяжные и фундаментные болты назначают по табл.8.1.
Таблица 8.1 - Диаметры отверстий под стяжные и фланцевые болты
Размер
| Диаметр болта
|
| М10
| М12
| М14
| М16
| M18
| М20
| М22
| М24
| Диаметр отверстия под стяжной болт
|
|
|
|
|
|
|
|
| Диаметр отверстия под фундаментный болт
|
|
|
|
|
|
|
|
|
Толщина фланца разъема корпуса и фундаментной лапы
(8.6)
Ширина фланца разъема корпуса и фундаментной лапы (от наружной поверхности корпуса)
(8.8)
Толщина ребер жесткости и проушин
(8.9)
Размеры и конфигурацию прочих конструктивных элементов корпусных деталей редукторов (сливных отверстий, люков, и т.д.) выполняют согласно рекомендациям [2].
КОНСТРУИРОВАНИЕ ЗУБЧАТЫХ И ЧЕРВЯЧНЫХ КОЛЕС
Зубчатые колеса
Форма зубчатого колеса может быть плоской или со ступицей, выступающей с одной стороны. Значительно реже (в одноступенчатых редукторах) колеса делают со ступицей, выступающей в обе стороны.
При небольших диаметрах колес их изготовляют из прутка, а при больших получают заготовки свободной ковкой с последующей токарной обработкой.
Ширину ступицы lСТ колеса желательно принимать равной или больше ширины b2 зубчатого венца (lСТ≥ b2). Принятую длину ступицы согласуют с расчетной и с диаметром посадочного отверстия d: lСТ=(0,8... l,5)d, обычно lСТ=(1,0...1,2)d
Диаметр dСТ назначают в зависимости от материала ступицы: для стали - dСТ=(l,5...1,55)d; для чугуна - dСТ=(1,55...1,6)d; для легких сплавов - dСТ =(1,6... 1,7)d. Меньшие значения - для шлицевого соединения колеса с валом, большие - для шпоночного соединения и соединения с натягом.
Толщину обода колеса S принимают:
(9.1)
где m - модуль зацепления, мм.
На торцах зубчатого венца (зубьях и кромках обода) выполняют фаски, величину которых находят по соотношению
(9.2)
с округлением до стандартного значения.
На прямозубых зубчатых колесах фаску выполняют под углом аф=45°, на косозубых колесах при твердости рабочих поверхностей менее 350НВ — под углом аф= 45°, а при более высокой твердости - аф= 15...20º.
Острые кромки торцов ступицы также притупляют фасками, размеры которых принимают по табл. 9.1.
При серийном производстве заготовки колес получают из прутка свободной ковкой, а также ковкой в штампах. При годовом объеме выпуска колес более 50 шт. экономически оправдана ковка в простейших односторонних подкладных штампах.
Таблица 9.1 - Размеры фасок на торцах ступицы колеса
d, мм
| 20...30
| 30...40
| 40...50
| 50... 80
| 80... 120
| 120... ...150
| 150... ...250
| 250... ...500
| f,мм
| 1,0
| 1,2
| 1,6
| 2,0
| 2,5
| 3,0
| 4,0
| 5,0
|
При готовом объеме выпуска более 100 шт. применяют двусторонние штампы. Для свободной выемки заготовок из штампа принимают значения штамповочных уклонов γ≥7° и радиусов закруглений R ≥6 мм.
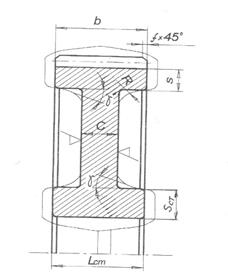
Конструкция колеса показана на рис. 9.1.
где Sст=0,5(dст-d).
В диске обычно выполняют 4...6 технологических отверстий диаметром 18...22 мм.
Для уменьшения влияния термической обработки на точность геометрической формы зубчатые колеса при НВ >350 делают массивными:
(9.4)
Нормализованные и улучшенные колеса делают с более тонким диском (С = 0,25b2).
Зубчатые колеса, вращающиеся с относительно высокой частотой (n≥1000 мин-1), обрабатывают кругом и балансируют путем высверливания отверстий на торцах обода.
Базовыми поверхностями при нарезании зубьев являются поверхность центрального отверстия и торцы зубчатого венца. Производительность возрастает при нарезании зубьев в «пакете» из двух колес и более.
Червячные колеса
Червячные колеса, как правило, выполняют составными: центр колеса (ступицу с диском) - из стали, реже из серого чугуна, а зубчатый венец (обод) — из антифрикционного материала.
В единичном и мелкосерийном производстве зубчатые венцы соединяют с центром посадкой с натягом. Для обеспечения точной сборки колеса на наружной поверхности центра предусматривают буртик, в который упирается обод при его запрессовке, и эта форма является традиционной.
Центр колеса представляет собой деталь, подобную по своей форме зубчатому колесу, но с гладкой наружной цилиндрической поверхностью, и рекомендуемые соотношения размеров ступицы и диска те же, что и в п. 9.1. Единственное отличие состоит в том, что размер S (см. рис. 9.1) определяют в зависимости от делительного диаметра червячного колеса d2: S= 0,06d2.
Характерным размером обода является его толщина
(9.5)
где dн - диаметр посадочной цилиндрической поверхности центра.
Пользуясь этим соотношением, находят S0 и dH.
На зубьях обода выполняют такие же фаски, что и на зубьях цилиндрических зубчатых колес (см. п. 9.1).
СМАЗКА РЕДУКТОРОВ
Для снижения трения, шума и вибрации, защиты от коррозии, уменьшения интенсивности износа, отвода тепла и продуктов износа в редукторе необходимо предусмотреть надежную смазку.
Зубчатые и червячные передачи смазывают жидкими маслами картерным непроточным способом (окунанием). Сорт масла выбирают в зависимости от контактного напряжения в передаче и характерной скорости. В зубчатых передачах такой скоростью является окружная скорость шестерни (или колеса), в червячной - окружная скорость червяка. Масло для зубчатой передачи следует выбирать по табл. 10.1. Для червячных передач при σН £200МПа и n£5 м/с принимают масло И-Г-С-320, а при n > 5 м/с - масло И-Г-С-220.
Обозначение индустриальных масел состоит из четырёх знаков, каждый из которых обозначает: первый (И) - индустриальное, второй - принадлежность к группе по назначению (Г - для гидравлических систем, Т - для тяжелонагруженных узлов), третий - принадлежность к группе по эксплуатационным свойствам (А - масло без присадок, С — масло с антиокислительными, антикоррозионными противоизносными и противозадирными присадками), четвёртый (число) - класс кинематической вязкости.
Таблица 10.1 - Рекомендуемые сорта масла по ГОСТ 20799-88 для зубчатых передач
Контактное напряжение, МПа
| Окружная скорость, м/с
|
<2
| 2...5
| >5
| <600
| И-Г-А-32
| И-Г-А-32
| И-Л-А-22
| 600... 1000
| И-Г-А-68
| И-Г-А-46
| И-Г-А-32
| 1000... 1200
| И-Г-А-68
| И-Г-А-68
| И-Г-А-46
|
Колесо цилиндрической зубчатой передачи должно окунаться в масляную ванну на глубину h (2m...0,25d2), где m - модуль зацепления. Колесо конической передачи - до половины зуба (до среднего диаметра зубчатого венца). В червячной передаче с нижним расположением червяка следует обеспечить погружение червяка на глубину не менее 2,2m.
При картерном смазывании передачи и окружных скоростях более 1 м/с масло разбрызгивается зубьями колёс, а при скоростях более 3 м/с внутри корпуса образуется масляный туман. И в том, и другом случае нет необходимости предусматривать специальную смазку подшипников, т.к. они будут смазываться тем же маслом, что и передачи. Именно такие скорости характерны для большинства редукторов общего назначения.
Особое значение имеет смазка для червячных передач, т.к. без интенсивной смазки возможен перегрев редуктора. Следует обеспечить объём масла в картере V, дм³, равный
где РдвТ – требуемая мощность двигателя, кВт.
Устройства для заливки масла в корпус редуктора и слива масла для замены, отдушины, маслоуказатели, а также различные типы уплотнений см. [1,2,4].
ТРЕБОВАНИЯ К РАСЧЕТНО-КОНСТРУКТОРСКОЙ ДОКУМЕНТАЦИИ
Не нашли, что искали? Воспользуйтесь поиском по сайту:
©2015 - 2025 stydopedia.ru Все материалы защищены законодательством РФ.
|