Расчет зажимного механизма.
Разработка конструкции приспособления для механической обработки.
Выбор конструкции установочных элементов и схемы зажимного устройства.
1. Анализ технического задания на проектирование станочного приспособления.
При выполнении операции 010 необходимо фрезеровать плоскость бокового окна, плоскости и фаски верхнего окна, растачивать точное отверстие Æ180H7 детали «Корпус», а также обработать нескольких отверстий (6 отв. М10-7Н, 2 отв. М10х1-7Н). Необходимо выдержать ряд размеров. Среди них нет точных размеров, лимитируемых точностью приспособления. Наиболее сложным в обеспечении является размер 40±0,3, определяющий положения отверстия Æ180H7.
2. Выбор системы приспособления.
В соответствие с заданием была выбрана система неразборные специальные приспособления (НСП).
3. Выбор способа установки приспособления на станке.
Для сверления отверстия используется многоцелевой станок ИС800-ГЛОБУС. Размеры рабочей поверхности стола 800х800 мм. Базовыми элементами являются точное центральное отверстие (D = 50H7) и семь Т-образных пазов (18H7 – центральный паз, 18Н9 – остальные). Таким образом, приспособление на столе станка может быть установлено с помощью цилиндрического пальца и шпонки, закреплено болтами М16.
4. Выбор баз и схемы базирования.
При выполнении операции необходимо обеспечить полное базирование, т.е. лишить заготовку всех 6 степеней свободы. В качестве главной базы удобнее всего использовать нижнюю плоскость детали, т.к. она обладают достаточно площадью и обработана на предшествующей операции.
Кроме этого потребуются еще 2 вспомогательные базы (двойная опорная и опорная базы). Для этого воспользуемся двумя точными отверстиями Æ22H7.
Выбранная схема является классической при обработке корпусных деталей и позволяет выдержать заданную точность всех размеров и обеспечить удобное закрепление.
Описанная схема базирования показана на рис. 3.
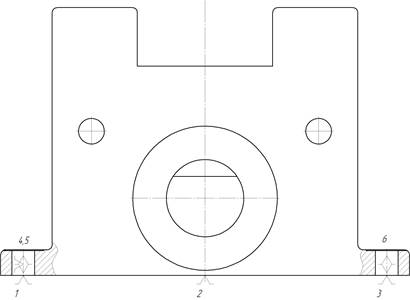
Рис. 3. Схемы базирования.
Расчет зажимного механизма.
1. Точки приложения и направление зажимного усилия.
Закрепление заготовки удобно осуществлять в направлении главной базы (установочная база). Это позволит оказывать наименьшее влияние силы закрепления на точность выполнения большинства размеров, выдерживаемых на операции. В качестве точек для приложения усилий зажима можно использовать верхнюю плоскость платиков с боковых сторон детали.
2. Расчет усилия закрепления заготовки проводим на основе задачи статики – равновесие заготовки под действием приложенных к ней сил в процессе обработки. Составим расчетную схему, на которой изобразим все действующие на заготовку силы и моменты: усилия зажима, силы резания, реакции опор и силы трения в местах контакта заготовки с установочными и зажимными элементами (рис. 4). Наша задача состоит в определении силы зажима, предотвращающей смещение заготовки вдоль установочной базы.
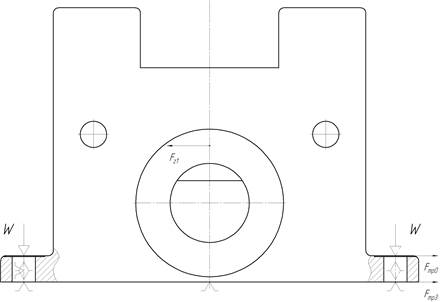
Рис. 4. Схема закрепления.
2. Определяем силы и моменты резания.
Наибольшие силы резания будут наблюдаться при выполнении первого перехода – фрезеровании бокового окна торцевой фрезой с твердосплавными пластинами.
По [33, с. 406] для нашего примера
.
где Ср Кмр – коэффициенты; D – диаметр фрезы, мм; t – глубина резания, мм; s – подача, мм/об; z – число зубьев фрезы; n – частота вращения фрезы, мин-1; q, x, y, n, w – показатели степени.
Принимаем D = 52 мм; z = 4; B = 32,5 мм [32, с. 263]; t = 2 мм; sz = 0,25 мм/зуб.
По данным [32, с. 412, табл. 83] для осевой силы – Cp = 54,5; q = 1,00; x = 0,90; y = 0,74; u = 1,00; w = 0.
Коэффициент 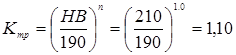

3. Составляем систему уравнений статики, т.е. уравнений сил и моментов из условия равновесия заготовки. Проводим расчеты усилия закрепления W.
Cилы закрепления W должны создавать силу и момент трения, превышающие по величине силу Pz и соответствующий ей момент вращения.

где f – коэффициент трения на зажимных и опорных элементах; k – коэффициент запаса.

где k0 – гарантированный коэффициент запаса надежности закрепления k0 = 1,5 [35, с. 382]; k1 – коэффициент, учитывающий увеличение силы резания из-за случайных неровностей на заготовках k1 = 1,2 [35, с. 382]; k2 – коэффициент, учитывающий увеличение сил резания от прогрессирующего затупления режущего инструмента k2 = 1,3 [35, с. 383, табл. 2]; k3 – коэффициент, учитывающий увеличение сил резания при прерывистом резании k3 = 1,2 [35, с. 383]; k4 – коэффициент, характеризующий зажимное устройство с точки зрения постоянства развиваемых им сил k4 = 1,3 [35, с. 383]; k5 – коэффициент, характеризующий удобство расположения рукояток в ручных зажимных устройствах k5 = 1,2 [35, с. 383]; k6 – коэффициент, учитывающий наличие моментов, стремящихся провернуть заготовку k6 = 1,0 [35, с. 384].

Выбираем материал зажимного и опорного элементов – сталь. Эффективные коэффициенты трения равны [1, с. 67, табл. 12] fз = 0,16 и fо = 0,20.

Принимаем усилие закрепление W = 9кH.
6. Выбор и расчет конструктивных параметров контактных элементов, силового механизма и привода зажимного устройство.
В качестве зажимных элементов в приспособлении будут использованы два винтовых прихвата, собранных из стандартных деталей.
Исходя из рассчитанного значения усилия закрепления W = 9кH по табл. 4 [35, с.386] выбираем размер резьбы винта – M16. По табл. 7 проверяем прочность винта sр = 98 МПа < [sр] = 170-190 МПа (Сталь 40, термообработка – улучшение).
По табл. 56 [35, с.138] выбираем Прихват 7011-0471 ГОСТ 4734-69.
Вычислим момент, который необходимо приложить к винту, чтобы закрепить заготовку.

Определим плечо ключа
L = M / 160 = 13231/160 » 80 мм,
что вполне удовлетворяет требованиям эргономики.
7. Разработка конструкции установочных элементов.
Для реализации установочной базы используем 2 опорные шайбы к установочным пальцам (Шайба 7034-0555 ГОСТ 17777-72) и одну опорную шайбу (Пластина 7034-0458 ГОСТ 17778-72). Площадь контактной поверхности первых составляет S » 995 мм2, а последней – S = 233 мм2. Допустимое давление на опору 40МПа.
,
что не превышает допустимого давления.
Не нашли, что искали? Воспользуйтесь поиском по сайту:
©2015 - 2025 stydopedia.ru Все материалы защищены законодательством РФ.
|