Разработка маршрутной технологии сборки, сварки и контроля изделия.
По системе международных стандартов версии ISO 9000 сварка относится к процессам, качество которых не может быть однозначно установлено методами контроля и испытаниями на завершающих стадиях изготовления. Качество сварки выявляется лишь в процессе эксплуатации. Следовательно, судить о качестве сварной конструкции можно только по схеме, приведенной на рисунке 4.1.
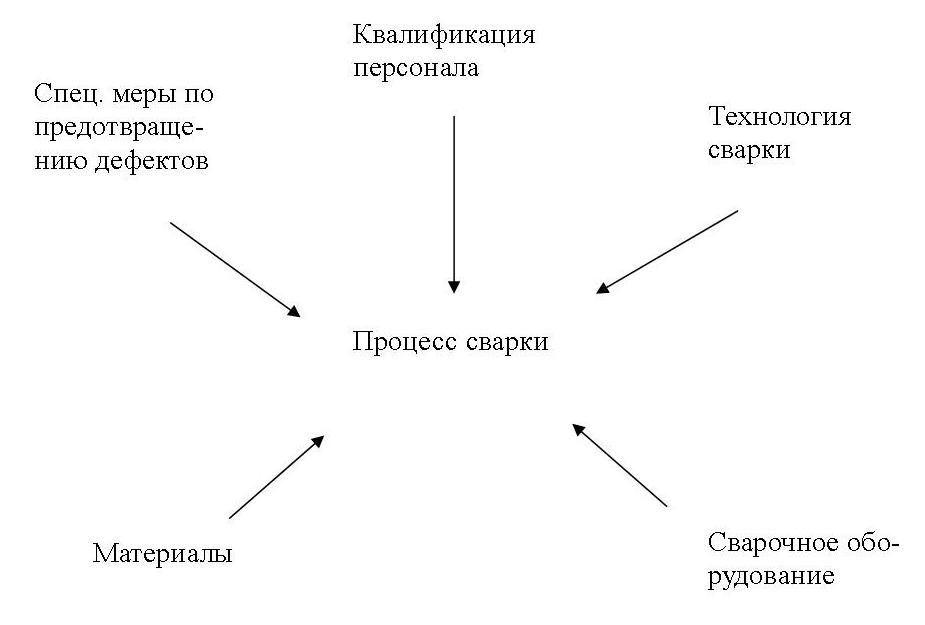
Рисунок 4.1
Таким образом стандартные требования к качеству сварки должны охватывать все аспекты процесса сварочного производства, влияющие на качество готовой продукции.
Расчет норм времени сборочно-сварочных операций
Затраты времени на сварочную операцию для сварки изделия (приблизительно 100 точек) определяется по формуле

где машинное или основное технологическое время, зависящее от
режима сварки;
вспомогательное время, расходуемое на установку, зажатие и съем
детали, ее перемещение, зачистку и т. п.; доля tв достигает
70-80 % tм;
прибавочное время на техническое обслуживание оборудования
составляет 10…15% (tм + tв);
продолжительность естественных перерывов в работе и отдыха.
Описание методов контроля процесса сварки и качества готового
Изделия
Для получения качественного соединения целесообразно производить следующие виды контроля:
1) Технологический контроль чертежей
2) Контроль операций сопутствующих сварке
3) Контроль оборудования и квалификации сварщика
4) Контроль процесса сварки
5) Контроль сварных соединений и узлов
- контроль разрушением
- контроль без разрушения
Для контроля данной детали применяем ультразвуковой контроль, который заключается в прозвучивании изделия короткими импульсами ультразвуковых колебаний и регистрации эхосигналов, отраженных от дефекта и идущих к приемнику.
Признаком дефекта является появление эхосигнала на экран дефектоскопа, что означает отсутствие сварной точки. Этот метод наиболее широко распространен из-за простоты реализации, возможности одностороннего доступа к изделию, независимости результатов контроля от конфигурации и состояния противоположной (донной) поверхности, а также из-за высокой точности в определении координат дефектной.
Разработка карт технологического процесса сборки, сварки и контроля изделия.
Технологический процесс изготовления конструкций и узлов включает ряд операций: предварительную сборку, подготовку поверхности, окончательную сборку, прихватку, сварку, антикоррозионную защиту, правку, механическую доработку.
В зависимости от масштаба производства, степени взаимозаменяемости деталей, металла, размеров и формы узла, его ответственности, а также конкретных условий производства отдельные сопутствующие операции могут быть исключены. Может изменяться последовательность их выполнения.
Сборка должна обеспечивать точную установку свариваемых деталей в соответствии с чертежом, а также наилучшие условия для последующей прихватки и сварки. При невысокой точности изготовления деталей сборка резко затрудняется подгоночными операциями. Поверхность деталей загрязняется. Поэтому вначале выполняют предварительную сборку, а затем узел разбирают и подготавливают поверхность. При хорошей взаимозаменяемости свариваемых деталей сборку ведут после подготовки поверхности (т.е. окончательную сборку). Во избежание загрязнения никаких подгоночных операций при этом не допускают.
Карты тех. процесса представлены в приложении Б.
Планировка рабочего места и его описание
Расположение на площади участка всех элементов производства в последовательности технологического процесса называется планировкой участка. В основе планировки участка лежат следующие принципы:
1) исключение возвратных движений, создающих встречные потоки;
2) выбор кратчайших путей передачи продуктов труда с одного рабочего места на другое.

Рисунок 4.2 – Планировка участка
1- тара с заготовками;
2- рабочий стол;
3- контактная машина;
4- тара с готовыми изделиями;
5- электрощит;
6- рабочее место оператора;
7-подвод воды, сжатого воздуха и слив воды
Охрана труда
При установке, монтаже и эксплуатации контактных сварочных машин должны соблюдаться все нормы и правила, необходимые для безопасной работы сварщика и наладчика. При невыполнении этих правил возможны различные случаи травматизма: поражение электрическим током; повреждения рук механизмами сжатия и зажимными устройствами; поражение органов дыхания газами, парами и пылью; ожоги брызгами металла и нагретыми деталями; ушибы тяжелыми деталями и порезы острыми краями металла. Сварочный контур машины не опасен в смысле возможности поражения электрическим током, так как напряжение на концах вторичного витка трансформатора не превышает 36 В. Такое напряжение недостаточно для того, чтобы через тело человека прошел опасный ток, величина которого превышает 0,1А. Ток, который может вызвать травму, появляется в сварочном контуре только при повреждении (пробое) первичной обмотки, когда вторичный виток или корпус машины (электрически соединенный со сварочным контуром) оказываются под напряжением питающей сети (127, 220,380В). Для исключения поражения электрическим током сварщику и наладчику необходимо: 1) систематически проверять надежность заземления станины и одного конца вторичного витка сварочного трансформатора; 2) не допускать попадания воды, масла, грязи, пыли и металлических предметов на обмотки трансформатора и вспомогательных электрических устройств; 3) запрещается производить проверку, наладку и ремонт электрических устройств, находящихся под напряжением питающей сети; эти работы выполняет только цеховой электрик; 4) ступени мощности переключать только при отключенной сети; запрещается открывать дверки машины при включенном напряжении; 5) следить за тем, чтобы изоляция питающих проводов и рукояток не было повреждена; 6) пользоваться резиновым ковриком или сухой деревянной решеткой, находящимися перед машиной; 7) ключи от регулятора времени и прерывателя должны находиться у наладчика или цехового электрика. Следует помнить, что в шовных машинах, а также в стыковых с моторным приводом особую опасность представляют электродвигатели, питающиеся от сети с напряжением 220 или 380 В, поэтому их необходимо тщательно защищать от попадания воды, масла и брызг расплавленного металла. Усилие сжатия электродов точечных и шовных машин достигает большой величины (несколько сот килограммов, а иногда и несколько тонн). Значительные усилия развивают и зажимные механизмы стыковых машин. При случайном нажатии кнопки или педали рука сварщика или наладчика может быть зажата между электродами, что вызовет тяжелую травму. Особую опасность представляют пневматические и гидравлические механизмы сжатия. Для предотвращения повреждения рук при работе на контактных машинах сварщику и наладчику необходимо выполнять следующие правила: 1) следить за исправностью механизмов сжатия и зажимных устройств, не допускать самопроизвольного их срабатывания; 2) выполнять зачистку, заправку и смену электродов только при выключенной машине; 3) не смазывать части машины на ходу; 4) не допускать присутствия посторонних лиц около машины во время работы; 5) своевременно устранять утечки сжатого воздуха и масла из пневматической и гидравлической систем; 6) при остановке машины на продолжительное время перекрывать воздушный вентиль. При точечной и шовной сварке хорошо очищенных стальных деталей в окружающую атмосферу не выделяются какие-либо вредные пары или газы. При сварке на правильно подобранном режиме также нет опасности загрязнения воздуха металлической пылью. Поэтому устройств местных отсосов воздуха, как правило, не требуется. Однако на сварку часто подаются детали из горячекатаной стали, арматурный пруток, а также штампованные детали, на поверхности которых имеются масло и эмульсия. Точечная и шовная сварка применяются и для соединения деталей из стали с антикоррозионными покрытиями (свинцом, оловом, цинком и др.) и из цветных металлов. При сварке таких деталей выделяются пары и пыль, имеющие токсические свойства. Стыковая сварка оплавлением неизбежно сопровождается интенсивным искрообразова-нием, а следовательно, выделением металлической пыли. В этих условиях всегда требуются устройства местных воздухоотсосов или увеличение мощности общей приточно-вытяжной вентиляции. Интенсивное искрообразование при стыковой сварке оплавлением особенно опасно при сварке деталей большого сечения. Брызги расплавленного металла могут вызвать ожог рук, лица, глаз или прожечь одежду сварщика. Точечная сварка плохо очищенного металла или сварка на неправильно настроенной машине при сильно изношенных электродах сопровождается большим количеством выплесков, т. е. выбрасыванием частиц расплавленного металла. Это явление также может быть причиной местных ожогов. Температура нагрева места сварки детали настолько высока, что при снятии ее с машины сварщик может получить ожоги рук. При шовной сварке ожог может произойти во время прикосновения к неостывшему шву, а также от горячей воды, стекающей в поддон с охлаждаемого изделия. Для предупреждения получения ожогов сварщик должен пользоваться рукавицами и специальным инструментом (клещами или щипцами) при снятии горячих деталей. От ожогов глаз брызгами металла применяются защитные очки с простыми прозрачными стеклами. В комплект спецодежды должен входить брезентовый, кожаный или дерматиновый фартук — не промасленный и не пропитанный горючими жидкостями. При сварке оплавлением на стыковой машине должен быть предохранительный щиток из прозрачного материала, который откидывается при установке деталей и снятии сваренного изделия. Ушибы тяжелыми деталями или порезы острыми краями их возможны в той же степени, как и при работе на любом металлообрабатывающем станке. Необходимо учитывать, что при сварке сложных крупногабаритных узлов некоторой опасности подвергаются рабочие, выполняющие операции на рядом расположенных станках. Поэтому соседние машины должны быть разделены ограждениями или достаточно широкими проходами. Для складирования и перемещения крупногабаритных изделий и деталей должны быть предусмотрены специальные устройства. Все сварщики и наладчики контактных машин должны обязательно пройти инструктаж по технике безопасности, охватывающий как общие условия работы на данном предприятии (в цехе), так и условия эксплуатации современных контактных машин.
Заключение
В данном курсовой работе разработан технологический процесс изготовления кронштейна при помощи контактной шовной из стали 12Х18Н10Т толщиной 2,5 мм.
В ходе выполнения проекта были решены следующие инженерные задачи:
Произведён расчёт режимов сварки для исходной стали,расчет элементов сварочного контура, для осуществления сварки выбрана сварочная машина МТ-2202,составлены карты технологического процесса сборки, сварки и контроля. Спроектировали рабочее место сварщика. Разработали мероприятия по охране труда и техники безопасности при выполнении сборочно-сварочных работ.
Не нашли, что искали? Воспользуйтесь поиском по сайту:
©2015 - 2025 stydopedia.ru Все материалы защищены законодательством РФ.
|