Проектирование и расчет роликового стенда.
3.1 Основные требования.
Края обечайки должны выходить за роликовые опоры не менее, чем на 100мм.
Следить, чтобы центр тяжести изделия не располагался вне роликового стенда. Соблюдать требования к грузоподъемности роликов.
Следить, чтобы корпус не приобретал прогиб в результате отсутствия поддерживающего ролика.
Обеспечение заданной последовательности сборки и наложения швов в соответствии с разработанным технологическим процессом.
Обеспечение заданного качества сварного изделия, для чего оно должно быть достаточно прочным и жестким, а закрепляемые детали должны оставаться в требуемом положении без деформирования их при сварке.
Широкое использование типовых унифицированных, нормализованных и стандартных деталей и механизмов, что способствует снижению их себестоимости, сроков проектирования и изготовления, повышению ремонтноспобности и т.п.
Обеспечение сборки всего изделия с одной установки, свободного съема изделия.Обеспечение доступа для осмотра, наладки и контроля изделия при сборке и сварке.
Ремонтоспособность, безопасность в эксплуатации, высокий срок службы. Для повышения ремонтоспособности предусматривать возможность замены быстроизнашивающихся деталей и возможность восстановления требуемой точности приспособления. В нем должны быть устройства для подрегулировки в процессе эксплуатации. В конструкции приспособления следует использовать изнашивающиеся детали с упрочненными рабочими поверхностями; предотвращать проникновение пыли, грязи, влаги, брызг металла на трущиеся и сопряженные поверхности, предупреждать возможность перегрузки приспособления в эксплуатации, вводить предохранительные и предельные устройства; предусматривать возможность удобной очистки базовых поверхностей от шлака, брызг металла. Технологичность приспособления и его отдельных элементов.Специальных ручки или другие устройства управления, должны быть защищены от случайных поворотов.
Смазка устройств без разборки механизмов.
Отсутствие острых кромок и углов, которые могут быть причиной травм.
Исключение каких-либо подгоночных и доделочных работ с изделием, так как они плохо поддаются механизации и сопровождаются большими затратами времени.
3.2 Расчет роликоопор сварочного стенда.

Рис.2 Расчетная схема роликого стенда.
Допустимый диапазон диаметров для данного расстояния L между роликоопорами ограничен двумя крайними (опасными) положениями изделия на стенде: 1) при чрезмерно большом диаметре по сравнению с величиной L и, следовательно, при очень малом центральном угле а, положение вращаемого изделия на стенде может оказаться неустойчивым. 2) При очень малом диаметре вращаемого барабана по сравнению с величиной L, угол а будет чрезмерно велик и может возникнуть явление затяжки [барабана с последующим его заклиниванием и даже поломкой стенда из-за резко возросших распорных усилий на роликах.
Затяжка барабана может происходить в стендах с одним рядом приводных роликов при вращении приводного вала в сторону холостых роликоопор. При обратном направлении вращения опасность затяжки исчезает, остаётся однако возможность статического заклинивания барабана
при очень большом центральном угле α и при некоторых других неблагоприятных обстоятельствах (малый диаметр роликов по сравнению с диаметром подшипников, применение подшипников скольжения, а не качения и проч.).
Для определения необходимых диаметров роликоопор, а так же мощности и электродвигателя, его тип и необходимую передачу вращающих моментов, производим нижеприведённый расчёт. Расчетная схема роликового стенда представлена на рис. 2.
Активная внешняя нагрузка стенда состоит из центральной силы G, равной весу вращаемого изделия(=8816кг), и грузового момента M^G * е.
В статическом состоянии стенда при е=0 сила G создает на роликоопорах опорные реакции Q, е =0 зависящие от центрального угла распора (α=84).
Q=G/n-cos(a/2), где:
n - количество роликоопор.
Q=8816/8-cos(84/2)=1102 кг
Во время вращения изделия на приводных роликах возникает окружное усилие Т.
Величина необходимого окружного усилия Т на приводных и холостых роликоопорах b:


dp- диаметр оси ролика в подшипниках;
f- коэффициент трения в подшипниках роликоопор (для подшипников скольжения ( f=0.1);
µ - коэффициент трения качения (для обрезиненных роликов У = 0,3);
Dp - диаметр роликов.
см
кгс
Суммарные опорные реакции на приводных и холостых роликоопорах:


Окружное усилие на приводных роликах, выраженное в долях веса изделия, представляет собой коэффициент сопротивления вращению изделия

Расчетная нагрузка роликов:
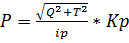
Р - нагрузка на одну ведущую или холостую роликоопору;
ip- число роликоопор в одном ряду;
kp - коэффициент, учитывающий неравномерность распределения
нагрузки на роликоопорах (для обрезиненных роликов при *Р > 4 ко = 1.2 ...1.3)
По величине Р подбираем типовые роликоопоры в соответствии с действующим сортаментом. Колличество роликовых опор равна-8.
Модель роликоопор:
Приводная: РП - 1; номинальная нагрузка на опору 2,5 т; диаметр ролика: 500 мм.
Холостая: РХ - 1; номинальная нагрузка на опору 2,5 т; диаметр ролика: 500 мм.
Определим крутящий момент на приводном валу ведущих роликоопор:
(2.7)
3.3 Расчет привода.
рис. 3 Кинематическая схема привода
(2.8)
-КПД муфты
-КПД прямой передачи
-КПД одной пары подшипников качения

Необходимая мощность на приводном валу роликоопор определяется по формуле:
(2.9)
- частота вращения вала при маршевой скорости =10 об/мин.
Необходимая мощность приводного электродвигателя:
(2.10)
Где - общи КПД приводного механизма:
Проверка запаса сцепления приводных роликов с изделием:
(2.11)
ф- коэффициент сцепления роликов с изделием (для обрезиненных а = 0.35)
4.3 Расчет привода роликового стенда.
По потребной мощности N=1.1 кВт, используя библиотеку программы Компас - 3D V7 plus, выбираем асинхронный электродвигатель АИР 80А4, мощностью N=1,1 кВт, частотой вращения пэл=1500 об/мин. По электродвигателю подбираем электропривод серии ИРБИ 81-1,5 для обеспечения регулирования частоты вращения электродвигателя от 20-40Гц. От которого и будет зависеть скорость в вращения роликов.
Определим передаточное число привода:
(2.12)
=1500 об/мин - частота вращения электродвигателя;
=10 об/мин - частота вращения ролика при маршевой скорости.
Учитывая требуемое передаточное отношение и крутящий момент Мкр=413,3 Н*м (7), используя библиотеку программы Компас - 3D V7 plus, выбираем червячный редуктор Ч - 125, с передаточным отношением и=80 и крутящим моментом Мкр=525 Н*м.
Кинематический расчет привода: Частота вращения валов привода:
Обозначим: nl - частота вращения вала электродвигателя;
п2 - частота вращения входного вала редуктора, она равна n1
пЗ - частота вращения выходного вала редуктора; п4 - частота вращения вала роликоопоры, она равна пЗ;
пэл - частота вращения электродвигателя.
Следовательно:
n1=n2=пэл=1500 об/мин;
n3=n2/u=10 об/мин;
n4=9.375 об/мин.
Мощности на валах:
N1=N=1.1 кВт;
N2=N1* =1.1*.098* 0.98=1.05 кВт;
N3=N2* =1.05*0.75*0.98=0.77 кВт;
N4=N3* =0.77*0.98*0.98=0.74 кВт.
Моменты на валах:
Ml=9550 Nl/nl=9550*1.1/1500=7 Нм;
M2=9550N2/n2=9550*1.05 /1500=6.6 Нм;
M3=9550N3/n3=9550*0.77/10=735.3 Нм;
M4=9550N4/n4=9550*0.74/9.375=759.8 Нм;
Кинематический расчет проводим для нахождения моментов на валах, которые необходимы для подбора муфты.
Подбор муфты:
Подбор муфт осуществляется в зависимости от крутящих моментов которые действуют на валы.
Таблица 2.1 - Моменты на валах
Вал
| Электродвигателя A4
| Редуктора
| Роликоопоры М4
| Входной М2
| Выходной МЗ
| Моменты, Нм
|
| 6.6
| 735.3
| 759.8
| Для соединения вала электродвигателя и входного вала редуктора применяем упругую втулочно - пальцевую муфту 16-24-1.1-УЗ ГОСТ 21424 - 75 Е 1
Эти муфты получили широкое распространение благодаря относительной простоте конструкции и удобства замены упругих элементов. Упругие втулочно - пальцевые муфты общего назначения применяют для
передачи крутящего момента и уменьшения динамических нагрузок на соединяемых соосных валах.
Для соединения валов выходного вала редуктора и роликоопор, а так же роликоопор между собой применим фланцевую муфту 630-56-11 ГОСТ 20761-75 [ ].
Муфты фланцевые (поперечно - разъемные) наиболее распространенные из класса жестких нерасцепляемых муфт из-за удобства монтажа и возможности жесткого соединения валов.
Литература.
1-Конструирование и расчет механического сварочного оборудования П.И.Севбо 1978
2- Основы проектирования и расчета сборочно-сварочных приспособлений Битинская Л.Н., Мочалова Т.Ф. 1789
3-Сварочные конструкции С.А.Куркин, Г.А. Николаев Высшая школа 1991
4-Новые сварные приспособления Е.В.Рыморов 1988.
Заключение
Обозначены основные требования к конструкциям приспособлений. Определен состав ложемента и кантователя.
Ложемент состоит из 5ти ребер, листов толщиной 20мм.
Данный кантователь состоит из 2х секций, состоящие из основания, 4-х роликов, 8 винтов и 8 фиксаторов, для крепления роликов на основание.
Произведен расчет роликовых опор сварочного стенда и его привода.
2ряда роликовых опор, по 4 ролика в каждом ряду, общее количество роликов-8
Модель роликовых опор:
Приводная: РП - 1
Холостая: РХ – 1
Подобрали асинхронный электродвигатель АИР 80А4.
Для соединения вала электродвигателя и входного вала редуктора применяем упругую втулочно - пальцевую муфту 16-24-1.1-УЗ ГОСТ 21424 - 75 Е 1
Аннотация.
Курсовой проект посвящен разработке оснастки для сборки и сварки элемента нижнего пояса НП1 фермы.
Курсовой проект состоит из:
1.Пояснительной записки
-Техническое описание изделия и пояснения к технологическому процессу.
-Проектирование кантователя для сборки и сварки раскосов.
-Проектирование ложемента для сборки и сварки «крестов»
-Проектирование и расчет роликового стенда.
2.Приложения к пояснительной записке, включающего в себя альбом спецификаций.
3.Графической части на 3,5 листах формата А1, включающих
-Ложемент для сварки «Крестов»
-Кантователь
-Роликовый стенд
Не нашли, что искали? Воспользуйтесь поиском по сайту:
©2015 - 2025 stydopedia.ru Все материалы защищены законодательством РФ.
|