Технические средства обеспечения монтажа
Для монтажа конструкций и деталей зданий применяют следующие виды оборудования:
• такелажные приспособления, предназначенные для строповки конструкций, — стропы, траверсы, захваты, карабины;
• оборудование для перемещения конструкций — лебедки, блоки и полиспасты, домкраты, тали, монтажные мачты, шевры;
• оборудование для закрепления и заделки монтажных стыков — сварочные аппараты, трансформаторы, компрессоры, аппараты для нанесения противокоррозионных покрытий, герметизации стыков и т. п.;
• монтажные приспособления для временного закрепления и выверки конструкций — кондукторы, распорки, подкосы, струбцины;
• оборудование для изменения рабочего места монтажников — лестницы и стремянки, подмости, люльки, подвесные площадки.
Подготовка мест установки сборных элементов
Перед монтажом фундаментов проверяют готовность основания, а именно, контролируют отметку основания, его горизонтальность, при необходимости осуществляют планировку основания. Подготовка фундаментов перед монтажом колонн и фундаментных балок состоит в проверке правильности размеров конструкций и установки анкерных болтов в фундаментах под стальные колонны. Правильность положения осей фундаментов, уровня стаканов в железобетонных башмаках, горизонтальных отметок и уровней проверяют геодезическими инструментами.
При установке колонн одноэтажных промышленных зданий особо контролируют горизонтальный уровень консолей колонн, на которые будут укладывать подкрановые балки. Этого достигают за счет подливки бетонной смеси в стакан фундамента или укладки в него армоцементных подкладок толщиной 1 и 2 см.
Подготовка мест установки сборных конструкций заключается в очистке основания, разметке места установки, для большинства железобетонных элементов в устройстве растворной постели. Наилучшее качество шва получается при точной установке конструкции, когда она сразу займет проектное положение. Если по условиям выверки устанавливаемый элемент необходимо снимать с постели, то раствор убирают и заменяют новым, который хорошо разравнивают, выполняют одинаковой толщины, распределяя по всей площади основания.
Подготовка элементов к подъему заключается в определении пригодности изделия по внешнему виду, ее очистке, проверке размеров и нанесении разметочных рисок. При внешнем осмотре проверяют наличие сколов бетона и трещин, исправность монтажных петель, нет ли наплыва бетона на закладных металлических деталях, в штрабах, в гнездах для монтажных петель. Детали с трещинами и другими дефектами, превышающие допуски, отбраковывают. Риски наносят на бетонные поверхности мягким черным карандашом, на металлических закладных деталях — зубилом и молотком.
Строповка конструкций
Грузозахватные приспособления предназначены для захвата надежного удерживания различных строительных грузов и изделий при перемещении кранами, обеспечения из сохранности при транспортировании, простой расстроповки при опускании на рабочее место.
В зависимости от назначения и конструктивного исполнения грузозахватные приспособления разделяют на следующие группы: канатные стропы, строповые устройства с дистанционным управлением, траверсы, захваты.
Для строповки сборных элементов используют универсальные и специальные канатные стропы с крюками, а также пальцевые, рамочные, вилочные, фрикционные захваты и петли-подхваты. Наибольшее применение нашли универсальные канатные стропы, оснащенные чалочными крюками для подъема сборных элементов за монтажные петли. По числу ветвей стропы подразделяют на одно-, двух-, трех- и четырехветвевые и кольцевые. Строп — съемное приспособление, выполненное в виде обрезка стального каната с соединительными элементами — кольца, крюки, коуши, карабины, канатная петля.
Траверсы состоят из металлической балки или фермы с устройствами для захвата монтируемых элементов, число которых зависит от количества точек захвата элементов — для колонн обычно одна или две точки, для ферм и балок — две или четыре, для плит — четыре или шесть. В качестве захватных устройств используют облегченные стропы с крюками или карабинами на концах, а также захваты из двух металлических щек, которые, охватывая монтируемые элементы, удерживают их с помощью продетого в них штыря — клещевые и другие захваты.
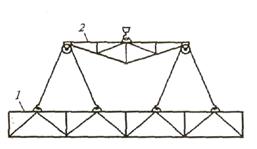
1 — ферма; 2 — траверса а — фрикционный; б — траверса
Рисунок 4 – Строповка металлических со штыревым креплением; 1-
ферм колонна; 2 — монтажный строп;
3 — полуавтоматический замок; 4 — канат для расстроповки; 5 — выдвигаемый штырь; 6— траверса; 7— чека
Рисунок 5 – Захваты для монтажа колонн
Временное закрепление элементов
Подъем сборного элемента рекомендуется производить в том же положении, в каком монтируемый элемент будет работать в возводимой конструкции. Поднимать монтируемые конструкции необходимо плавно, без рывков, раскачивания и вращения. Подъем изделий осуществляют способами, исключающими возникновение опасных напряжений в процессе их подъема и установки, а также гарантирующими безопасные условия ведения работ. При необходимости производят временное усиление поднимаемых элементов. Тяжелые элементы и конструкции поднимают в два приема: сначала на высоту 0,2...0,3 м с задержкой на весу для дополнительной проверки надежности строповки и правильного положения, затем продолжают поднимать на проектную отметку.
В строительстве для временного закрепления монтируемых элементов применяют различные монтажные приспособления и устройства. Они могут быть индивидуальными и групповыми (рисунок 6). К индивидуальным средствам относятся клинья, расчалки, подкосы, распорки, кондукторы, фиксаторы и т. п. Групповые средства предусматривают закрепление нескольких статически неустойчивых монтажных элементов.
Для металлических конструкций временное закрепление осуществляют монтажными болтами.
Для железобетонных конструкций:
• колонны, устанавливаемые в стаканы фундаментов, крепятся деревянными, бетонными, железобетонными и металлическими клиньями, по одному — два клина с каждой стороны в зависимости от сечения и высоты колонны; растяжками и металлическими кондукторами, оснащенными регулировочными винтами. Выверку осуществляют путем погружения клиньев в полость между боковой гранью колонны и стакана фундамента с последующим инструментальным контролем. После замоноличивания стыков и набора бетоном определенной прочности деревянные и металлические клинья извлекают, что требует больших затрат ручного труда. Широкое распространение получили инвентарные клиновые вкладыши с винтовыми домкратами.
Выверка элементов
Выверка обеспечивает точное соответствие монтируемых конструкций проектному положению. В зависимости от вида монтируемых конструкдий, их оснастки, стыков и условий обеспечения устойчивости, выверку производят визуально или инструментально в процессе установки, когда конструкция удерживается монтажным механизмом или после установки при ее закреплении.
Визуальную выверку производят при достаточной точности опорных поверхностей и стыков конструкций. При этом могут использоваться стальные рулетки, калибры, шаблоны и т. п.
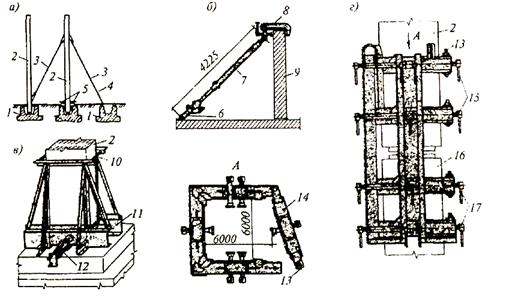
а — расчалка; б — подкос; в — кондуктор для установки колонны в стакан фундамента; г — кондуктор для установки колонн на оголовки ранее смонтированных колонн; 1 — фундамент; 2 — колонна; 3 — расчалка; 4 — винтовая стяжка; 5 — клиновой вкладыш; 6 — крюк с надвижной муфтой; 7 — телескопическая штанга; 8 — струбцина; 9 — панель; 10 — стяжные болты; 11 — рама; 12 — распорный домкрат; 13 — запорный шкворень; 14 — поворотная балка; 15 — винты для выверки колонны; 16 — оголовок колонны; 17 — винты для закрепления кондуктора на оголовке колонны
Рисунок 6 – Приспособления для временного закрепления и выверки конструкций
Инструментальную выверку выполняют при сложности обеспечения точности установки монтажных элементов и конструкций проверкой только опорных поверхностей, торцовых оснований или стыков смонтированных конструкций. Ее производят при установке специальных монтажных приспособлений (кондукторов, рамно-шарнирных индикаторов и т. п.). Инструментальная выверка является наиболее распространенным видом проверки положения смонтированных конструкций в плане, высотном и вертикальном положениях. В процессе такой выверки применяют теодолиты, нивелиры, лазерные приборы и устройства.
Безвыверочная установка получила наибольшее распространение при монтаже сборных металлических конструкций (в отдельных случаях и железобетонных конструкций). Основным ее условием является применение конструкций с повышенным классом точности геометрических размеров в монтажных стыках. Это позволяет при монтаже устанавливать, например, стальные колонны, опоры и другие элементы каркаса с фрезерованными опорными торцами в проектное положение, исключая выверку по высоте и вертикали.
Автоматическая выверка предусматривает установку конструкций с параллельной выверкой при помощи автоматических устройств.
Выверка элементов
Выверка обеспечивает точное соответствие монтируемых конструкций проектному положению. В зависимости от вида монтируемых конструкдий, их оснастки, стыков и условий обеспечения устойчивости, выверку производят визуально или инструментально в процессе установки, когда конструкция удерживается монтажным механизмом или после установки при ее закреплении.
Визуальную выверку производят при достаточной точности опорных поверхностей и стыков конструкций. При этом могут использоваться стальные рулетки, калибры, шаблоны и т. п.
Инструментальную выверку выполняют при сложности обеспечения точности установки монтажных элементов и конструкций проверкой только опорных поверхностей, торцовых оснований или стыков смонтированных конструкций. Ее производят при установке специальных монтажных приспособлений (кондукторов, рамно-шарнирных индикаторов и т. п.). Инструментальная выверка является наиболее распространенным видом проверки положения смонтированных конструкций в плане, высотном и вертикальном положениях. В процессе такой выверки применяют теодолиты, нивелиры, лазерные приборы и устройства.
Безвыверочная установка получила наибольшее распространение при монтаже сборных металлических конструкций (в отдельных случаях и железобетонных конструкций). Основным ее условием является применение конструкций с повышенным классом точности геометрических размеров в монтажных стыках. Это позволяет при монтаже устанавливать, например, стальные колонны, опоры и другие элементы каркаса с фрезерованными опорными торцами в проектное положение, исключая выверку по высоте и вертикали.
Автоматическая выверка предусматривает установку конструкций с параллельной выверкой при помощи автоматических устройств.
При выверке элементов:
• вертикальность установки элементов проверяют по отвесу или при помощи теодолита;
• горизонтальность установки проверяют уровнем или нивелиром;
• перед установкой колонн в стаканы фундаментов контролируют их фактические размеры, по этим размерам подготавливают фундаменты — осуществляют углубление гнезда стакана фундамента или проводят подливку бетонной смеси в стакан, чаще укладывают армоцементные прокладки толщиной 1 и 2 см.
В период выверки конструкция должна быть устойчивой под действием собственной массы, монтажных и ветровых нагрузок благодаря правильной последовательности монтажа, соблюдению проектных размеров опорных площадок и сопряжений, своевременной установке предусмотренных в проекте постоянных или временных связей или креплений, а также обеспечению мероприятий по безопасному ведению строительных процессов.
Возможные предельные отклонения от проектного положения элементов и конструкций при монтаже должны быть установлены в проекте производства работ в зависимости от конструктивных решений, применяемых приспособлений и оснастки, порядка сварки и других условий в пределах, предусмотренных СНиПом. Результаты проверки оформляют актами промежуточной приемки смонтированных ответственных конструкций и актами освидетельствования скрытых работ с приложением исполнительной схемы геодезического контроля.
Постоянное закрепление конструкций
Долговечность полносборных зданий в значительной степени зависит от качества закладных деталей и сварных соединений между ними. Стальные закладные детали и сварные швы под действием проникающей через щели и поры агрессивной среды подвергаются коррозии, что ведет к ослаблению и разрушению стального соединения между конструкциями. Постоянным закреплением конструкций в большей степени предотвращают негативное влияние окружающей среды.
Одной из основных задач при возведении зданий является надежное соединение отдельных конструкций между собой, так как качество такого соединения в определенной степени предопределяет качество и надежность смонтированного сооружения. Соединения элементов имеют три разновидности: швы, стыки и узлы.
Швы — наиболее часто встречаемое соединение элементов; это все горизонтальные и вертикальные плоскости, полости между рядом расположенными элементами. Полость между рядом лежащими панелями перекрытий, панелью перекрытия и стенкой ригеля, на котором она лежит, плоскость соединения панели перекрытия и установленной на ней стеновой панели — это швы соединяемых конструкций.
Стык — более ответственное сочленение двух элементов каркаса, это место соединения, а в большей степени зона передачи нагрузки от одного элемента каркаса другому. Стыком является место соединения двух колонн между собой по вертикали, место опирания и передачи нагрузки от подкрановой балки на консоль колонны, аналогичный стык фермы и колонны.
Узел — место конструктивного соединения двух или нескольких элементов между собой. Так, просто узлом называют место соединения двух наружных и одной внутренней панелей крупнопанельного здания, место соединения колонны и фундамента также является узлом, но через колонну передается нагрузка на фундамент, поэтому узел одновременно является и рабочим стыком двух элементов.
Стыки и узлы конструкций могут быть несущими (нагрузку) и ненесущими. Если стык несущий, то он воспринимает нагрузку и поэтому обязан обеспечить соединению прочность, жесткость и неизменяемость. К несущим стыкам можно отнести все соединения каркаса здания. Ненесущий стык по определению не несет нагрузки — это и стык санитарно-технической кабины и перегородки, стык (узел), отмеченный ранее, двух наружных и внутренней стеновых панелей.
Монтаж сборных элементов осуществляется различными методами.
В зависимости от степени укрупнения монтируемых элементов различают следующие методы монтажа: поэлементный и блочный монтаж, монтаж укрупненными модулями и в целом виде.
Поэлементный монтаж осуществляется отдельными элементами и не требует сложных подготовительных работ и наиболее распространен в строительстве.
Блочный монтаж – монтаж блоками из нескольких элементов, позволяет максимально механизировать монтажный процесс, полностью использовать грузоподъемность крана, сократить количество работ на высоте, но при этом требуются краны большой грузоподъемности, площадки и оборудование для сборки.
Монтаж укрупненными модулями и монтаж в целом виде – сборка сооружения осуществляется в нижнем положении, подъем и установка в полностью законченном виде, исключаются работы на высоте, но требуется наличие необходимого оборудования.
Монтаж отдельных конструкций осуществляют следующими способами: наращиванием, подращиванием, поворотом, скольжением, вертикальным подъемом, надвижкой, с перемещением в пространстве.
Наращивание – направление монтажа снизу вверх, наиболее массовый, простой и достаточно надежный метод.
Подращивание – направление монтажа сверху вниз, то есть поднимается и закрепляется верхняя конструкция, затем которая, располагается ниже.
Поворот – метод монтажа, при которой монтируемая конструкция или сооружение собирается на земле, ставится на шарнир, поворачивается. Этот способ технически сложно исполнить, применяется при монтаже вертикальных конструкций.
Способ скольжения отличается от способа поворота тем, что в процессе подъема конструкции за верхнюю часть, ее база перемещается в сторону подготовленного основания с помощью опорной тележки.
При применении способа вертикального подъема конструкцию поднимают на высоту, несколько большую, чем проектная, после чего подставляют или собирают постоянные опоры, на которые опускается конструкция.
Надвижка – способ монтажа конструкций, при котором горизонтальное перемещение конструкций осуществляется с помощью горизонтально работающих домкратов, мостовых кранов.
Подъем перемещением в пространстве состоит из подъема, горизонтального перемещения краном и опускания конструкции в проектное положение.
В зависимости от последовательности установки конструкций различают дифференцированный (раздельный) и комплексный (смешанный) методы монтажа, комбинированный (раздельно-комплексный) метод монтажа, сочетающий элементы первых двух (рисунок 7).
Дифференцированный метод предусматривает предварительную установку всех однотипных конструкций в пределах всего здания или определенного монтажного участка, а затем монтаж конструкций другого типа. Комплексный метод предусматривает последовательный монтаж разнотипных конструкций в пределах одной или нескольких смежных ячеек здания, образующих жесткую устойчивую систему, открывающую фронт для ведения последующих работ.

а – дифференцированным методом; б – комплексным методом; в – комбинированным методом; 1-6 – последовательность установки
Рисунок 7 – Последовательность установки конструкции в проектное положение
В зависимости от направления развития монтажного процесса различают продольный, когда конструкции последовательно монтируют вдоль здания или пролета, и поперечный монтаж, когда конструкции устанавливают последовательно по поперечным осям здания.
Рекомендуемая литература [1-5].
Контрольные задания по СРС [1-5] – 3 часа.
Составить калькуляцию трудовых затрат на монтажные работы. Разработать технологические схемы по установке строительных конструкций в зависимости от конструктивных особенностей зданий и выбранных методов монтажа. Рассчитать рабочие параметры монтажных кранов.
Не нашли, что искали? Воспользуйтесь поиском по сайту:
©2015 - 2024 stydopedia.ru Все материалы защищены законодательством РФ.
|