Наряду с производством основных типов бутадиен-стирольных и бутадиен- метилстирольных каучуков, выпускаются другие специальные типы этих каучуков.
Наполненные каучуки: свойства и применение, типы наполнителей: масло, цели и способы введения наполнителей.
Для улучшения перерабатываемости резиновых смесей и снижения стоимости часть каучука выпускают с наполнителями.
Наряду с производством основных типов бутадиен-стирольных и бутадиен- метилстирольных каучуков, выпускаются другие специальные типы этих каучуков.
Большое количество каучуков вырабатывается в виде маслонаполненных, саженаполненных и сажемаслонаполненных. Выпускаются также каучуки, наполненные в стадии латекса другими наполнителями (силикатные, силикатно-маслолигнинные, смоляные), в другие специальные — карбоксилатные и структурированные. В относительно небольших количествах вырабатываются бутадиен-стирольные и бутадиен-метилстирольные каучуки следующих специальных типов:
с меньшим содержанием второго мономера (марок СКС-10 и СКМС-10), обладающие повышенной морозостойкостью;
с большим содержанием второго мономера (марок СКС-50 и СКМС-50), характеризующиеся хорошей обрабатываемостью;
сополимеры с преобладанием второго мономера (примерно 70—90%), являющиеся фактически не каучуками, а пластиками.
Наблюдается тенденция преимущественного роста производства сажемаслонаполненных каучуков, что объясняется тем, что в этих каучуках удачно сочетаются преимущества сажевых и масляных каучуков.
Введение в каучук масла имеет большое экономическое значение. Благодаря введению масла значительно удешевляется стоимость каучука, поскольку стоимость масла в 3—4 раза ниже стоимости мономеров; при этом качество каучука не ухудшается.
Для того чтобы получить смеси с оптимальными физическими свойствами и в то же время отличающиеся достаточно хорошей обрабатываемостью, необходимо вводить масло в количествах, зависящих от исходной пластичности каучука.
Для правильного выбора масел важно знать их химический состав, поскольку они оказывают значительное влияние на свойства получаемых маслонаполненных каучуков.
Для получения маслонаполненных каучуков применяют нефтяные масла как с высоким, так и средним содержанием ароматических соединений. Применяются также нафтеновые масла, например высокоароматизированное масло ПН-б.
Количество масла в маслонаполненных каучуках (в зависимости от типа каучуков) может колебаться в значительных пределах—от 15 до 50 вес.ч. масла (15, 30, 37 и 50 вес.ч.) на I00 вес.ч. каучука.
Масло вводят в латекс также и непосредственно, минуя стадию приготовления эмульсии масла. В этом случае латекс в трубопроводе или в первом аппарате коагуляционного каскада непрерывно смешивается с раствором хлористого натрия и маслом (без предварительного эмульгирования последнего). Эмульгирование масла происходит под действием эмульгатора, частично освобождающегося при флокуляции латекса. Образуется смесь масла с флокулированным латексом, которая остается однородной при любых температурных условиях. Выходящую из первого аппарата каскада смесь обрабатывают на всех дальнейших стадиях (коагуляция, формирование ленты, ее промывка и сушка) обычными способами.
Сажи, как известно, являются наиболее распространенными усилителями для каучуков. При введении их в натуральный каучук повышаются напряжение при удлинении вулканизатов, предел прочности при разрыве и износостойкость резиновых изделий.
При использовании метода сухого смешения каучука с сажей не всегда достигается однородное распределение сажи в каучуке и не полностью используются усиливающие свойства саж.
При производстве саженаполненных и сажемаслонаполненных каучуков сажа вводится в каучук на стадии коагуляции латекса, что улучшает распределение сажи в каучуке и тем самым повышает качество резиновых изделий.
Саже- и маслосаженаполненные каучуки обладают рядом существенных преимуществ перед каучуками, в которые сажу вводят на обычно применяемом смесительном оборудовании резиновых производств.
Процесс получения саженаполненных бутадиен-стирольных (а-бутадиен-метилстирольных) каучуков заключается в смешении различными способами и на различном оборудовании водных дисперсий сажи с дегазированным латексом с последующей коагуляцией, промывкой и сушкой каучука обычными способами.
Способы получения саже- и сажемаслонаполненных бутадиен-стирольных каучуков можно разделить на две основные группы;
1. с использованием поверхностно-активных веществ (диспергаторов) для стабилизации водных сажевых дисперсий;
2. с приготовлением сажевых дисперсий без применения поверхностно-активных веществ.
Получение саженаполненных и сажемаслонаполненных каучуков с применением поверхностно-активных веществ. Непосредственное введение сажи в латекс трудно осуществить по ряду причин, главными из которых являются частичная коагуляция латекса и агломерация сажи. Для преодоления этих трудностей было предложено применять специальные химические вещества — диспергирующие агенты (диспергаторы).
Без диспергатора можно приготовить дисперсию, содержащую до 5 вес.% сажи. По мере дальнейшего увеличения содержания сажи дисперсия загустевает. Применение диспергатор а позволяет получать сажевые дисперсии с более высокой концентрацией (например, 19%).
В качесве диспергаторов для сажи было предложено применять продукты конденсации нафталинсульфокислоты или ее солей с формальдегидом.
Количество применяемого диспергатора стремятся свести к минимуму, так как его присутствие в каучуке увеличивает содержание примесей и ухудшает взаимодействие сажи с каучуком. Последнее обстоятельство связано с тем, что диспергатор, адсорбируясь на поверхности сажи, блокирует некоторые активные центры на ее поверхности.
Способ получения саже- и сажемаслонаполненных каучуков с применением диспергаторов считается нерентабельным; в виду этого его не считают перспективным для широкого промышленного использования.
Получение саже- и сажемаслонаполненных каучуков без применения поверхностно-активных веществ.
Был разработан способ получения маточных смесей из каучука, сажи и масла под действием гидравлического удара с приложением силы сдвига, полностью устраняющего растирание сажи с водой и уменьшающего повреждение частиц сажи.
Наиболее распространенным является метод диспергирования саж с помощью перегретого пара в струйно-вибрационной мельнице непрерывного действия. Методы производства саже- и сажемаслон аполневных каучуков без применения поверхностно-активных веществ являются наиболее перспективными.
Каучуки выпускают с различными сажами в дозировках от 40 до 80 вес.ч. Большинство каучуков содержит также и масло (типа ароматического, высокоароматического или нафтенового) в количестве от 5 до 60 вес. ч.
Основным потребителем саже и сажемаслонаполненных каучуков является шинная промышленность, где эти каучуки используются для производства протекторов.
В последнее время стали выпускать модифицированные каучуки марки СКН. Модификация состоит во введении в СКН различных добавок, например таких, как поливинилхлорид. Смешение производят в резиносмесителях или на вальцах.
Можно модифицировать каучуки путем смешения латексов. Последний способ более экономичен. Каучуки СКН, модифицированные поливинилхлоридом, выпускаются двух типов. Они различаются соотношением каучука и поливинилхлорида: 70 : 30 и 50: 50. Модифицированный каучук получают обычно периодическим способом. Латекс СКН после дегазации смешивается с латексом поливинилхлорида в аппарате с мешалкой, при этом вводят стабилизатор для двух латексов. Выделение модифицированного каучука производится раствором хлорида натрия при 40—45 °С. Полученная крошка промывается водой в аппарате с мешалкой и направляется в агрегат для сушки. Преимуществами таких модифицированных каучуков являются отличные озоностойкость, сопротивление раздиру, стойкость к агрессивным средам и тепловому старению, а также огнестойкость.
Кроме поливинилхлоридов бутадиен-нитрильные каучуки модифицируют хлоропреновым каучуком, тиоколом, бутадиен-стирольным, полибутадиеновым, натуральным каучуками и фенолоформальдегидными смолами.
Выпускают так называемые структурированные бутадиен-нитрильные каучуки — продукты тройной сополимеризации бутадиена, НАК и дивинилбензола, маркированные СКН-26СШ и СКН-40СШ. Большое значение имеет тройной сополимер бутадиена, НАКа и стирола, выпускаемый в виде смолы.
Разработаны бутадиен-нитрильные каучуки, наполненные пластификатором на стадии латекса, характеризующиеся особо легкой перерабатываемостью; карбоксилированные каучуки (СКН-26-5—сополимер бутадиена, НАК и метакриловой кислоты); большой ассортимент жидких бутадиен-нитрильных полимеров. Начато производство порошкообразных каучуков, каучуков со связанным антиоксидантом, вводимым на стадии полимеризации.
Поликонденсация: определения, классификация, способы проведения. Полисульфидные и силоксановые каучуки: структура, исходные вещества, условия синтеза, свойства, области их использования, особенности технологии
Поликонденсацией называют процесс получения высокомолекулярных соединений путем взаимодействия полифункциональных мономеров, сопровождающийся чаще всего выделением низкомолекулярного вещества (воды, спирта, аммиака). Поликонденсация может осуществляться в растворе, расплаве, твердой фазе, а также на границе раздела фаз.
При поликонденсации в отличие от полимеризации нарастание молекулярной массы происходит ступенчато. Скорость поликонденсации является суммой скоростей реакций между молекулами различных размеров. В результате каждой элементарной реакции конденсации образуются устойчивые соединения. Характерной особенностью поликонденсации является то, что наращивание цепи может происходить как путем взаимодействия молекул мономера с молекулой полимера или олигомера, так и в результате взаимодействия последних друг с другом. По мере израсходования мономера второй процесс становится преобладающим.
Процесс поликонденсации, в котором участвуют однородные молекулы, называется гомополиконденсацией. В общем виде этот процесс может быть изображен следующим уравнением:

где Х и У — функциональные группы исходного вещества; Z — группа, связывающая остатки реагирующих молекул; А молекула выделяющегося простого вещества.
Процесс поликонденсации, в котором участвуют разнородные молекулы, называется гетерополиконденсацией. Эта реакция в общем виде может быть выражена следующим уравнением:

При эквимолярном соотношений исходных веществ процесс гетерополиконденсации протекает аналогично гомополиконденсации. Реакция поликонденсации бифункциональных соединений приводит к образованию линейных полимеров. При поликонденсации соединений, содержащих в молекуле больше двух функциональных групп, образуются полимеры разветвленного и пространственного строения.
В результате реакций поликонденсации элементный состав продукта реакции (полимера) отличается от суммарного элементного состава реагирующих веществ. Процессы поликонденсации в промышленности СК применяются при получении полисульфидных (тиоколов) и уретановых каучуков.
В промышленности полисульфидные эластомеры выпускаются в виде жидких тиоколов, объем производства которых составляет 70—80% от общего выпуска. В полимерной цепи тиоколов содержится от 20 до 85% атомов серы. Поскольку это предельные полимеры, они вулканизуются путем присоединения вулканизующих агентов к концевым группам полимера.
В общем виде тиоколы описывают формулой

В зависимости от числа атомов серы в составе элементарного звена различают тетрасульфидные и дисульфидные полимеры. Физико-механические свойства полимер а определяются как строением органического радикала, так и числом атомов серы в полисульфидном звене. Все тетрасульфидные полимеры, независимо от строения органического радикала, — эластичные материалы. Дисульфидные полимеры обладают эластическими свойствами, если в органическом радикале содержится четыре и более атомов углерода.
В промышленности выпускают тиоколы в виде твердых каучуков и жидких полимеров. Полисульфидные каучуки получают поликонденсацией алифатических дигалогенопроизводных с полисульфидами щелочных металлов.
В качестве галогенпроизводных применяют следующие соединения:
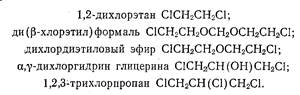
Основной мономер для получения тиоколов — ди-(3-хлор-этил)формаль. Его получают взаимодействием этиленхлоргидрина и формальдегида в присутствии соединений, способных удалять образующуюся при реакции воду в виде азеотропа (например, дихлорэтана, нитрометана и др.):

Реакцию проводят при 90—95 °С и избытке этиленхлоргида
Образование полисульфидного полимера происходит в результате поликонденсации на границе раздела фаз путем замещения хлора полисульфидными анионами:

На концах цепи могут чередоваться атомы хлора и полисульфидные группы. поликонденсацию проводят при 80—90 °С в водной дисперсии в присутствии диспергаторов в аппаратах с мешалкой. В качестве диспергаторов применяют гидроксиды магния, кальция или бария, а в качестве эмульгатора — канифольное мыло или алкиларилсульфонаты. Процесс может быть периодическим или непрерывным.
Полимеры с молекулярной массой 200—500 тыс, получают в присутствии значительного избытка полисульфида натрия. При этом образуется полимер с концевыми группами , которые вступают в дальнейшие реакции, приводящие к увеличению молекулярной массы полимера:

Наряду с основной реакцией диконденсации протекают также побочные реакции. При синтезе тиоколов на основе дихлорэтана или дихлордиэтилового эфира в результате их взаимодействия с сульфидом натрия образуются низкомолекулярные дитиолы, а также циклические соединения — тиофен, тиоксан и другие, которые обладают резким неприятным запахом. Тиоколы, синтезированные на основе формаля, не имеют неприятного запаха.
По окончании процесса поликонденсации дисперсию полимера отмывают от избытка полисульфида натрия многократной промывкой водой. После промывки дисперсию подкисляют минеральной кислотой, в результате чего полимер выделяется в виде крошки. Для отделения полимера от водной фазы применяют вибросита или центрифуги. Крошку каучука отмывают от кислоты и сушат под вакуумом в колонных или полочных сушилках.
Жидкие низкомолекулярные полимеры получают в результате регулируемой химической деструкции дисульфидных связей высокомолекулярного полимера гидросульфидом натрия в присутствии сульфита натрия:

В процессе расщепления принимают участие только S—S- связи, связь СS не затрагивается.
Реакция расщепления дисульфидных связей высокомолекулярного полимера осуществляется в водной дисперсии на границе раздела фаз. Молекулярная масса образующегося жидкого полимера зависит от количества гидросульфида натрия.
Выделение жидкого полимера из водной дисперсии осуществляется, как и выделение эластомеров, разрушением диспергатора (гидроксида магния) минеральными кислотами. Выделенный полимер отмывают водой от кислоты и минеральных солей. Удаление воды должно тщательно контролироваться, так как эта стадия процесса оказывает существенное влияние на свойства жидкого тиокола и его вулканизатов.
Свойства полисульфидных каучуков зависят в значительной мере от природы применяемых галогенпроизводных и их соотношения с полисульфидом натрия.
Наличие серы в основной цепи придает вулканизатам тиоколов стойкость к действию многих агрессивных сред (масел, нефтяных топлив, кислот, щелочей), озона, света, радиации, высокую газонепроницаемость, устойчивость при длительном хранении и эксплуатации. Для ряда полимеров эти свойства сочетаются с высокой морозостойкостью.
Вулканизаты твердых тиоколов имеют сравнительно низкие физико-механические свойства. Хорошие бензо- и влагостойкость, а также газонепроницаемость позволяют использовать твердые тиоколы для изготовления шлангов и прокладок, работающих в среде растворителей и топлив. Эластичные тиоколы применяют также в качестве вулканизующих агентов для каучуков общего назначения.
Тиоколы легко смешиваются с техническим углеродом, мелом, каолином, диоксидом титана и другими минеральными наполнителями, совмещаются с бутадиен-нитрильными, хлоропреновыми и другими каучуками, вулканизуются оксидами металлов (цинка, магния и др.) при 135—145 0 С и некоторыми органическими пероксидами.
Твердые тиоколы производят также в виде водных дисперсий с массовым содержанием сухого вещества около 50% Водные тиоколовые дисперсии можно применять для получения антикоррозионных и изоляционных покрытий для металла, железобетона и других материалов. Дисперсии наносят на поверхность кистью или пульверизатором. После высыхания образуются пленки с хорошей бензо- и маслостойкостью, влаго- и газонепроницаемостью.
Жидкие полимеры составляют основную долю в общем объеме производства тиоколов. Основным их преимуществом по сравнению с твердыми является способность вулканизоваться при комнатной температуре с образованием эластичных газонепроницаемых покрытий, способных устойчиво работать в интервале температур от —40 до 130° С в среде масел и растворителей, и условиях вибрации, при повышенной влажности среды.
Отверждение жидких тиоколов осуществляется окислением концевых тиокольных групп до дисульфидных. Наиболее доступным окислителем является кислород воздуха. Отверждение легко протекает в присутствии щелочных активаторов, например дифенилгуанидина или солей тяжелых металлов. Широкое применение в качестве вулканизующих агентов получили диоксиды свинца, марганца и теллура. Все неорганические окислители требуют присутствия следов влаги для инициирования процесса.
Жидкие тиоколы предназначаются для изготовления масло- и бензостойких герметизирующих паст и замазок, отверждающихся при умеренных температурах.
По внешнему виду жидкие тиоколы предствляют собой вязкую однородную жидкость темного цвета с зеленоватым или коричневатым оттенком.
Выпускают пять марок жидких тиоколов, различающихся содержанием серы и вязкостью.
Жидкие тиоколы нашли широкое применение при строительстве ирригационных сооружений, жилых домов, получении антикоррозионных покрытий в качестве герметиков.
Силоксановые каучуки, полимерная цепь которых состоит из чередующихся атомов кислорода и кремния, связанного с заместителями различной химической природы, получают полимеризацией в блоке циклических силоксанов. Разработаны также методы получения этих каучуков методом гидролитической поликонденсации. Существует два метода получения силоксановых каучуков: полимеризационный и поликонденсационный. Наибольшее распространение в промышленности получил полимеризационный метод, основанный на использовании реакций перегруппировки 5i—О-связей в циклосилоксанах по схеме:

Полимеризационным методом получают силоксановые каучуки основных марок СКТ, СКТВ и др. В значительно меньшей степени в промышленности используют поликонденсационные методы (для получения ариленсилоксанов, блоксополимеров и др.), которые протекают по схеме:

Технологический процесс получения силоксановых каучуков состоит из следующих стадий: подготовка исходного мономера или смеси мономеров; гидролиз диалкил(или алкилалкенил-, или алкиларил) хлорсиланов и нейтрализация гидролизата; деполимеризация гидролизата; полимеризация циклосилоксанов; дегазация, сушка и упаковка каучука. Основным мономером при производстве силоксановых каучуков является диметилдихлорсилан , который должен содержать не менее 99,96% основного вещества, для получения диметилдихлорсилана-ректификата требуемой чистоты его выделяют в высокоэффективных ректификационных колоннах. Гидролиз диметилдихлорсилана осуществляется фильтрованной водой при соотношении вода: диметилдихлорсилан = (1,5- 1,9): 1, при этом примерно в равных количествах образуются линейные и циклические полисилоксаны:
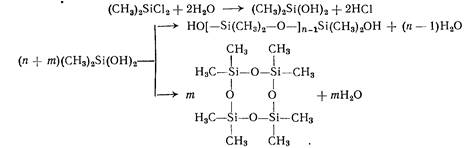
Деполимеризация гидролизата происходит под действием 50%-ного водного раствора едкого кали в вакууме при 150—160 0 С. Процесс циклизации описывается следующей схемой:
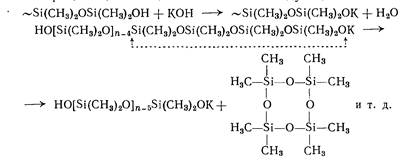
Полимеризация индивидуальных циклосилоксанов или их смесей в промышленности осуществляется под влиянием катализатора на основе сульфата алюминия и серной кислоты. Катализатор готовится в виде пасты, получаемой при смешении силоксанового масла, обезвоженного сульфата алюминия и серной кислоты в массовом соотношении 10 : 5 : 0,2 . Можно применять и щелочные катализаторы. Полимеризация протекает по следующей схеме:
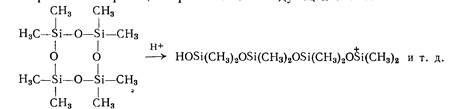
Промышленные марки силоксановых каучуков имеют следующую структуру:


Каучук марки СКТ имеет диметилсилоксановые звенья . Другие типы силоксановых каучуков содержат небольшое количество звеньев другой природы.
Силоксановые каучуки представляют собой прозрачную бесцветную легко растекающуюся массу. Силоксановые каучуки обладают высокой термостойкостью (до 250 °С), газонепроницемостью, термоокислительной стабильностью, стойкостью к действию озона и УФ-излучения, имеют хорошие диэлектрические свойства. Так, силоксановые каучуки практически не окисляются кислородом воздуха при температуре ниже 150 0 С. При более высоких температурах окисляются боковые метильные группы, что приводит к деструкции и структурированию полимера. Силоксановые каучуки применяют для электроизоляции проводов, кабелей, машин, электронных приборов. Из них изготовляют прокладки, теплостойкие воздуховоды и другие изделия, применяемые в авиационной промышленности. Резина из силоксановых каучуков превосходит резины из всех других каучуков по морозостойкости, поэтому ее можно использовать для изготовления изделий, работающих при температуре до —100 ° С.
Не нашли, что искали? Воспользуйтесь поиском по сайту:
©2015 - 2025 stydopedia.ru Все материалы защищены законодательством РФ.
|