Специальные способы литья
В современном литейном производстве все более широкое применение получают специальные способы литья: в оболочковые формы, по выплавляемым моделям, кокильное, под давлением, центробежное и другие.
Эти способы позволяют получать отливки повышенной точности, с малой шероховатостью поверхности, минимальными припусками на механическую обработку, а иногда полностью исключают ее, что обеспечивает высокую производительность труда. Каждый специальный способ литья имеет свои особенности, определяющие области применения.
Литье в оболочковые формы
Литье в оболочковые формы - процесс получения отливок из расплавленного металла в формах, изготовленных по горячей модельной оснастке из специальных песчано-смоляных смесей.
Формовочную смесь приготовляют из мелкого кварцевого песка с добавлением термореактивных связующих материалов.
Технологические операции формовки при литье в оболочковые формы представлены на рис.6.1.
Металлическую модельную плиту 1 с моделью нагревают в печи до 200…250 0C.
Затем плиту 1 закрепляют на опрокидывающемся бункере 2 с формовочной смесью 3 (рис. 2.17. а) и поворачивают на 180 0 (рис. 2.17.б). Формовочную смесь выдерживают на плите 10…30 секунд. Под действием теплоты, исходящей от модельной плиты, термореактивная смола в приграничном слое расплавляется, склеивает песчинки и отвердевает с образованием песчано-смоляной оболочки 4, толщиной 5…15 мм. Бункер возвращается в исходное положение (рис. 2.17. в), излишки формовочной смеси осыпаются с оболочки. Модельная плита с полутвердой оболочкой 4 снимается с бункера и прокаливается в печи при температуре 300…350 ?C, при этом смола переходит в твердое необратимое состояние. Твердая оболочка снимается с модели с помощью выталкивателей 5 (рис.2.17.г). Аналогичным образом получают вторую полуформу.
Для получения формы полуформы склеивают или соединяют другими способами (при помощи скоб).
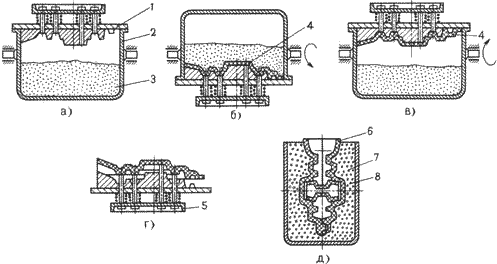
Рис 2.17. Технологические операции формовки при литье в оболочковые формы
Собранные формы небольших размеров с горизонтальной плоскостью разъема укладывают на слой песка. Формы с вертикальной плоскостью разъема 6 и крупные формы для предохранения от коробления и преждевременного разрушения устанавливают в контейнеры 7 и засыпают чугунной дробью 8 (рис.2.17.д).
Литье в оболочковые формы обеспечивает высокую геометрическую точность отливок, малую шероховатость поверхностей, снижает расход формовочных материалов (высокая прочность оболочек позволяет изготавливать формы тонкостенными) и объем механической обработки, является высокопроизводительным процессом.
В оболочковых формах изготавливают отливки массой 0,2…100 кг с толщиной стенки 3…15 мм из всех литейных сплавов для приборов, автомобилей, металлорежущих станков.
Литье по выплавляемым моделям
Литье по выплавляемым моделям – процесс получения отливок из расплавленного металла в формах, рабочая полость которых образуется благодаря удалению (вытеканию) легкоплавкого материала модели при ее предварительном нагревании.
Технологические операции процесса литья по выплавляемым моделям представлены на рис. 6.2.
Выплавляемые модели изготавливают в пресс-формах 1 (рис. 2.18.а) из модельных составов, включающих парафин, воск, стеарин, жирные кислоты. Состав хорошо заполняет полость пресс-формы, дает четкий отпечаток. После затвердевания модельного состава пресс-форма раскрывается и модель 2 (рис. 2.18.б) выталкивается в холодную воду.
Затем модели собираются в модельные блоки 3 (рис. 2.18.в) с общей литниковой системой припаиванием, приклеиванием или механическим креплением. В один блок объединяют 2…100 моделей.
Формы изготавливают многократным погружением модельного блока 3 в специальную жидкую огнеупорную смесь 5, налитую в емкость 4 (рис.2.18.г) с последующей обсыпкой кварцевым песком. Затем модельные блоки сушат на воздухе или в среде аммиака. Обычно наносят 3…5 слоев огнеупорного покрытия с последующей сушкой каждого слоя.
Модели из форм удаляют, погружая в горячую воду или с помощью нагретого пара. После удаления модельного состава тонкостенные литейные формы устанавливаются в опоке, засыпаются кварцевым песком, а затем прокаливают в печи в течение 6…8 часов при температуре 850…950 0C для удаления остатков модельного состава, испарения воды (рис. 6.2.д)
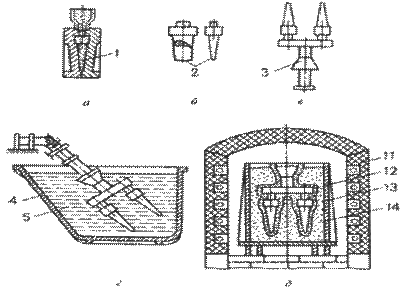
Рис.2.18. Технологические операции процесса литья по выплавляемым моделям
Заливку форм по выплавляемым моделям производят сразу же после прокалки в нагретом состоянии. Заливка может быть свободной, под действием центробежных сил, в вакууме и т.д.
После затвердевания залитого металла и охлаждения отливок форма разрушается, отливки отделяют от литников механическими методами, направляют на химическую очистку, промывают и подвергают термической обработке.
Литье по выплавляемым моделям обеспечивает получение точных и сложных отливок из различных сплавов массой 0,02…15 кг с толщиной стенки 0,5…5 мм.
Недостатком является сложность и длительность процесса производства отливок, применение специальной дорогостоящей оснастки.
Литьем по выплавляемым моделям изготавливают детали для приборостроительной, авиационной и другой отраслевой промышленности. Используют при литье жаропрочных труднообрабатываемых сплавов (лопатки турбин), коррозионно-стойких сталей, углеродистых сталей в массовом производстве (автомобильная промышленность).
Технологический процесс автоматизирован и механизирован.
Литье в металлические формы
Литье в металлические формы (кокили) получило большое распространение. Этим способом получают более 40% всех отливок из алюминиевых и магниевых сплавов, отливки из чугуна и стали.
Литье в кокиль – изготовление отливок из расплавленного металла в металлических формах-кокилях.
Формирование отливки происходит при интенсивном отводе теплоты от расплавленного металла, от затвердевающей и охлаждающейся отливки к массивному металлическому кокилю, что обеспечивает более высокие плотность металла и механические свойства, чем у отливок, полученных в песчаных формах.
Схема получения отливок в кокиле представлена на рис. 6.3.
Рабочую поверхность кокиля с вертикальной плоскостью разъема, состоящую из поддона 1, двух симметричных полуформ 2 и 3 и металлического стержня 4, предварительно нагретую до 150…180 ?C покрывают из пульверизатора 5 слоем огнеупорного покрытия (рис. 2.19.а) толщиной 0,3…0,8 мм. Покрытие предохраняет рабочую поверхность кокиля от резкого нагрева и схватывания с отливкой.
Покрытия приготовляют из огнеупорных материалов (тальк, мел, графит), связующего материала (жидкое стекло) и воды.

Рис. 2.19 Технологические операции изготовления отливки в кокиль
Затем с помощью манипулятора устанавливают песчаный стержень 6, с помощью которого в отливке выполняется полость (рис.2.19.б).
Половинки кокиля соединяют и заливают расплав. После затвердевания отливки 7 (рис. 2.19.в) и охлаждения ее до температуры выбивки кокиль раскрывают (рис.2.19.г) и протягивают вниз металлический стержень 4. Отливка 7 удаляется манипулятором из кокиля (рис.2.19.д).
Отливки простой конфигурации изготовляют в неразъемных кокилях, несложные отливки с небольшими выступами и впадинами на наружной поверхности – в кокилях с вертикальным разъемом. Крупные, простые по конфигурации отливки получают в кокилях с горизонтальным разъемом. При изготовлении сложных отливок применяют кокили с комбинированным разъемом.
Расплавленный металл в форму подводят сверху, снизу (сифоном), сбоку. Для удаления воздуха и газов по плоскости разъема прорезают вентиляционные каналы.
Все операции технологического процесса литья в кокиль механизированы и автоматизированы. Используют однопозиционные и многопозиционные автоматические кокильные машины.
Литье в кокиль применяют в массовом и серийном производствах для изготовления отливок из чугуна, стали и сплавов цветных металлов с толщиной стенки 3…100 мм, массой от нескольких граммов до нескольких сотен килограммов.
Литье в кокиль позволяет сократить или избежать расхода формовочных и стержневых смесей, трудоемких операций формовки и выбивки форм, повысить точность размеров и снизить шероховатость поверхности, улучшить механические свойства.
Недостатки кокильного литья: высокая трудоемкость изготовления кокилей, их ограниченная стойкость, трудность изготовления сложных по конфигурации отливок.
Изготовление отливок центробежным литьем
При центробежном литье сплав заливается во вращающиеся формы. Формирование отливки осуществляется под действием центробежных сил, что обеспечивает высокую плотность и механические свойства отливок.
Центробежным литьем изготовляют отливки в металлических, песчаных, оболочковых формах и формах для литья по выплавляемым моделям на центробежных машинах с горизонтальной и вертикальной осью вращения.
Металлические формы изложницы изготовляют из чугуна и стали. Толщина изложницы в 1,5…2 раза больше толщины отливки. В процессе литья изложницы снаружи охлаждают водой или воздухом.
На рабочую поверхность изложницы наносят теплозащитные покрытия для увеличения срока их службы. Перед работой изложницы нагревают до 200 0C.
Схемы процессов изготовления отливок центробежным литьем представлены на рис.2.20.
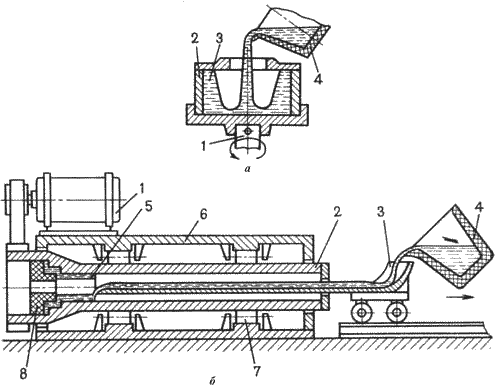
Рис.2.20. Схемы процессов изготовления отливок центробежным литьем
При получении отливок на машинах с вращением формы вокруг вертикальной оси (рис. 2.20.а) металл из ковша 4 заливают во вращающуюся форму 2, укрепленную на шпинделе 1, который вращается от электродвигателя.
Под действием центробежных сил металл прижимается к боковой стенке изложницы. Литейная форма вращается до полного затвердевания отливки. После остановки формы отливка 3 извлекается.
Отливки имеют разностенность по высоте – более толстое сечение в нижней части. Применяют для получения отливок небольшой высоты – коротких втулок, колец, фланцев.
При получении отливок типа тел вращения большой длины (трубы, втулки) на машинах с горизонтальной осью вращения (рис. 2.20.б) изложницу 2 устанавливают на опорные ролики 7 и закрывают кожухом 6. Изложница приводится в движение электродвигателем 1. Расплавленный металл из ковша 4 заливают через желоб 3, который в процессе заливки металла перемещается, что обеспечивает получение равностенной отливки 5. Для образования раструба трубы используют песчаный или оболочковый стержень 8. После затвердевания металла готовую отливку извлекают специальным приспособлением.
Скорость вращения формы зависит от диаметра отливки и плотности сплава, определяется по формуле:
,
где: – плотность сплава; – внутренний радиус отливки.
Центробежным литьем изготавливают отливки из чугуна, стали, сплавов титана, алюминия, магния и цинка (трубы, втулки, кольца, подшипники качения, бандажи железнодорожных и трамвайных вагонов).
Масса отливок от нескольких килограммов до 45 тонн. Толщина стенок от нескольких миллиметров до 350 мм. Центробежным литьем можно получить тонкостенные отливки из сплавов с низкой текучестью, что невозможно сделать при других способах литья.
Недостаток: наличие усадочной пористости, ликватов и неметаллических включений на внутренних поверхностях; возможность появления дефектов в виде продольных и поперечных трещин, газовых пузырей.
Преимущества – получение внутренних полостей трубных заготовок без применения стержней, экономия сплава за счет отсутствия литниковой системы, возможность получения двухслойных заготовок, что получается поочередной заливкой в форму различных сплавов (сталь – чугун, чугун – бронза).
Используют автоматические и многопозиционные карусельные машины с управлением от ЭВМ.
Литье под давлением
Литьем под давлением получают отливки в металлических формах (пресс-формах), при этом заливку металла в форму и формирование отливки осуществляют под давлением.
Отливки получают на машины литья под давлением с холодной или горячей камерой прессования. В машинах с холодной камерой прессования камеры прессования располагаются либо горизонтально, либо вертикально.
На машинах с горизонтальной холодной камерой прессования (рис. 2.21) расплавленный металл заливают в камеру прессования 4 (рис. 2.21.а). Затем металл плунжером 5, под давлением 40…100 МПа, подается в полость пресс-формы (рис.2.21.б), состоящей из неподвижной 3 и подвижной 1 полуформ. Внутреннюю полость в отливке получают стержнем 2. После затвердевания отливки пресс-форма раскрывается, стержень 2 извлекается (рис. 2.21.в) и отливка 7 выталкивателями 6 удаляется из рабочей полости пресс-формы.
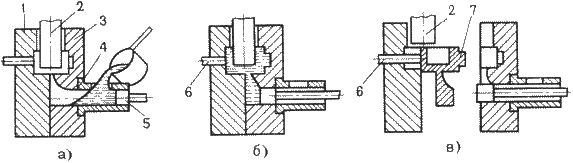
Рис.2.21. Технологические операции изготовления отливок на машинах с горизонтальной холодной камерой прессования
Перед заливкой пресс-форму нагревают до 120…320 0C. После удаления отливки рабочую поверхность пресс-формы обдувают воздухом и смазывают специальными материалами для предупреждения приваривания отливки. Воздух и газы удаляются через каналы, расположенные в плоскости разъема пресс-формы или вакуумированием рабочей полости перед заливкой металла. Такие машины применяют для изготовления отливок из медных, алюминиевых, магниевых и цинковых сплавов массой до 45 кг.
На машинах с горячей камерой прессования (рис. 2.22) камера прессования 2 расположена в обогреваемом тигле 1 с расплавленным металлом. При верхнем положении плунжера 3 металл через отверстие 4 заполняет камеру прессования. При движении плунжера вниз отверстие перекрывается, сплав под давлением 10…30 МПа заполняет полость пресс-формы 5. После затвердевания отливки плунжер возвращается в исходное положение, остатки расплавленного металла сливаются в камеру прессования, а отливка удаляется из пресс-формы выталкивателями 6.
Получают отливки из цинковых и магниевых сплавов массой от нескольких граммов до 25 кг.

Рис.2.22. Схема изготовления отливки на машинах с горячей камерой прессования
При литье под давлением температура заливки сплава выбирается на 10…20 0C выше температуры плавления.
Литье под давлением используют в массовом и крупносерийном производствах отливок с минимальной толщиной стенок 0,8 мм, с высокой точностью размеров и малой шероховатостью поверхности, за счет тщательного полирования рабочей полости пресс-формы, без механической обработки или с минимальными припусками, с высокой производительностью процесса.
Недостатки: высокая стоимость пресс-формы и оборудования, ограниченность габаритных размеров и массы отливок, наличие воздушной пористости в массивных частях отливки.
Изготовление отливок электрошлаковым литьем
Сущность процесса электрошлакового литья заключается в переплаве расходуемого электрода в водоохлаждаемой металлической форме (кристаллизаторе).
При этом операции расплавления металла, его заливка и выдержка отливки в форме совмещены по месту и времени.
Схема изготовления отливок электрошлаковым литьем представлена на рис. 2.23.

Рис.2.23. Схема изготовления отливок электрошлаковым литьем
В качестве расходуемого электрода используется прокат. В кристаллизатор 6 заливают расплавленный шлак 4 (фторид кальция или смесь на его основе), обладающий высоким электро- сопротивлением. При пропускании тока через электрод 7 и затравку 1 выделяется значительное количество теплоты, и шлаковые ванна нагревается до 1700 C, происходит оплавление электрода. Капли расплавленного металла проходят через расплавленный шлак и образуют под ним металлическую ванну 3. Она в водоохлаждаемой форме затвердевает последовательно, образуя плотную без усадочных дефектов отливку 2. Внутренняя полость образуется металлической вставкой 5.
Расплавленный шлак способствует удалению кислорода, снижению содержания серы и неметаллических включений, поэтому получают отливки с высокими механическими и эксплуатационными свойствами.
Изготавливаются отливки ответственного назначения массой до 300 тонн: корпуса клапанов и задвижек атомных и тепловых электростанций, коленчатые валы судовых двигателей, корпуса сосудов сверхвысокого давления, ротора турбогенераторов.
Изготовление отливок непрерывным литьем
При непрерывном литье (рис. 2.24) расплавленный металл из металлоприемника 1 через графитовую насадку 2 поступает в водоохлаждаемый кристаллизатор 3 и затвердевает в виде отливки 4, которая вытягивается специальным устройством 5. Длинные отливки разрезают на заготовки требуемой длины.
Используют при получении отливок с параллельными образующими из чугуна, медных, алюминиевых сплавов. Отливки не имеют неметаллических включений, усадочных раковин и пористости, благодаря созданию направленного затвердевания отливок.

Рис. 2.24. Схема непрерывного литья (а) и разновидности получаемых отливок (б)
Не нашли, что искали? Воспользуйтесь поиском по сайту:
©2015 - 2024 stydopedia.ru Все материалы защищены законодательством РФ.
|