Порядок выполнения работы
Лабораторная работа №1
ПРОВЕРКА ГЕОМЕТРИЧЕСКОЙ ТОЧНОСТИ ТОКАРНО-ВИНТОРЕЗНОГО СТАНКА 16К20
Задание
1. Ознакомиться с наиболее распространенными средствами и приемами проверки геометрической точности станка 16К20.
2. Составить отчет о проделанной работе.
Цель и задачи лабораторной работы
1.1. Ознакомиться с контрольно-измерительными устройствами и приемами работы при проверке геометрической точности станка и взаимного расположения механизмов на станке.
1.2. Ознакомиться с существующими нормами точности станков.
1.3. Научиться самостоятельно составлять схему проверки и производить необходимые измерения геометрических погрешностей токарно-винторезного станка.
1.4. Научиться анализировать результаты производственных проверок путем сравнения их с установленными в станкостроении нормами точности.
1.5. Составить отчет о проделанной работе.
Общие методические указания
В процессе создания станка новой конструкции и после изготовления серийного станка, а также после ремонта, перед пуском станка в эксплуатацию, проводятся разные по целям и объему экспериментальные исследования, испытания и проверки станка и его отдельных частей.
Геометрическая точность станка зависит от точности деталей, узлов и качества их сборки. Она должна контролироваться для каждого станка.
Влияние геометрической погрешности станка оценивается по взаимному расположению инструмента и обрабатываемой детали в статическом состоянии без воздействия на станок силы резания. Допустимые нормы точности станков и методы их проверки определяются ГОСТ 18097-88 в зависимости от их типов.
Оборудование, приспособления, инструмент
3.1. Проверка геометрической точности определяется на токарно-винторезном станке
3.2. Индикатор (с ценой деления 0,001 мм) на стойке с магнитным основанием.
3.3. Проверочная линейка с ценой деления, 1 мм
3.4. Проверочный уровень.
3.5. Щуп.
3.6. Контрольные оправки:
- цилиндрическая с конусом Морзе 5;
- торцовая с конусом Морзе 5;
- цилиндрическая с конусом Морзе 4;
- цилиндрическая с центровыми отверстиями;
3.7. Универсальный мостик.
3.8. Набор плоскопараллельных мер.
Порядок выполнения работы
Перед выполнением измерений геометрических погрешностей токарного станка необходимо изучить паспортные данные станка, измерительные приборы и оправки, а также последовательность выполнения замеров. Измерения проводить в следующей последовательности:
4.1. Отклонение от прямолинейности направляющих суппорта станка (станины) в вертикальной плоскости (рис. 1.1).
4.1.1. Установить мостик на передней направляющей суппорта станка.
4.1.2. Параллельно к направляющей установить на мостике уровень.
4.1.3. Перемещая мостик по всей длине направляющей, снять показания уровня через каждые L= 300 мм.
4.1.4. Установить мостик с уровнем на задней направляющей и повторить замеры.
Отклонение определяют как наибольшую алгебраическую разность показаний шкалы уровня. Допустимые отклонения передней и задней направляющих 0..0,02 мм на длине 1000 мм. Вогнутость не допускается.
4.2. Отклонение от прямолинейности продольного перемещения суппорта в вертикальной плоскости (рис. 1.2).
4.2.1. Установить уровень на суппорте около резцедержателя, параллельно направлению перемещения суппорта. Резцедержатель должен быть расположен как можно ближе к оси центров станка.
4.2.2. Перемещая суппорт в продольном направлении на всю длину хода, произвести измерение не более чем через 200 мм. Допустимое отклонение 0,025 мм на длине 800 мм. Вогнутость не допускается.

4.3. Отклонение от параллельности направляющих суппорта станка (станины) на отсутствие короблений (рис. 1.3).
4.3.1. Установить мостик на станине на направляющих суппорта станка.
4.3.2. Установить на мостике уровень перпендикулярно к продольным направляющим.
4.3.3. Перемещая мостик по всей длине станины, снять показания уровня через каждые 300 мм. Допускаемое отклонение 0,02 мм на длине 1000 мм.

4.4. Отклонение от прямолинейности продольного перемещения суппорта станка в горизонтальной плоскости (рис. 1.4).
4.4.1. Контрольную оправку, длиной отвечающей расстоянию между центрами, с цилиндрической измерительной поверхностью установить в центрах передней 4 и задней 5 бабок. Резцедержатель должен быть расположен как можно ближе к оси центров станка.
4.4.2. Установить и закрепить индикатор на суппорте 1 станка в резцедержателе, коснувшись измерительным наконечником боковой образующей контрольной оправки перпендикулярно к ее оси. Перемещая суппорт 1 станка в продольном направлении по длине оправки, сиять показания индикатора в точках А и Б.
Отклонение определяют как наибольшую алгебраическую разность показаний индикатора. Допускаемое отклонение 0,015 мм на длине 1000 мм.

4.5. Отклонение, от параллельности линии центров по отношению к направляющим станины в вертикальной плоскости (рис. 1.5).
4.5.1. Установить в центрах передней 1 и задней 5 бабок контрольную оправку 2 с цилиндрической поверхностью.
4.5.2. Закрепить индикатор 3 на суппорте 4 станка и, коснувшись его измерительным наконечником верхней образующей контрольной оправки в вертикальной плоскости перпендикулярно к ее оси в точке А, переместить суппорт на длину 700 мм и произвести измерение в точке Б.
4.5.3. Повернуть шпиндель на 180° и повторить измерения в точках А и Б. Отклонение определяют как среднюю арифметическую величину двух указанных измерений, каждая из которых определяется алгебраической разностью показаний индикатора на концах контрольной оправки. Допустимое отклонение О..0,03 мм.
4.6. Отклонение от параллельности перемещения задней бабки; по отношению к перемещению суппорта станка (рис. 1.6): а в вертикальной плоскости; б-в горизонтальной плоскости.
4.6.1. Установить суппорт 1 и заднюю бабку 4 в крайнее положение на направляющих станины (правое или левое). Пиноль 3 вдвинуть в заднюю бабку на 0,8 хода и закрепить.
4.6.2. Установить и закрепить индикатор 2 на суппорте станка, коснувшись измерительным наконечником образующую пиноли задней бабки перпендикулярно к ее оси.
4.6.3. Перемещая суппорт и заднюю бабку станка одновременно (при этом расстояние между суппортом и задней бабкой должно быть постоянным) на всю длину ее хода, снять показания индикатора не более чем через 0,3 длины хода с остановками для измерения и закрепления задней бабки.
Отклонение определяют как наибольшую алгебраическую разность показаний индикатора при первоначальном и последующем положениях задней бабки и суппорта.
Допустимое отклонение в вертикальной плоскости 0,04 мм, в горизонтальной плоскости 0,025 мм.
4.7. Отклонение параллельности направляющих задней бабки по отношению к перемещению суппорта станка (рис. 1.7).
4.7.1. Установить и закрепить индикатор на суппорте станка, коснувшись измерительным наконечником перпендикулярно поверхности направляющей задней бабки.
4.7.2. Перемещая суппорт станка по всей длине направляющих, снять показания индикатора.
4.7.3. Произвести замеры всех поверхностей направляющих задней бабки поочередно. Допустимое, отклонение по всей длине точения 0,015 мм.
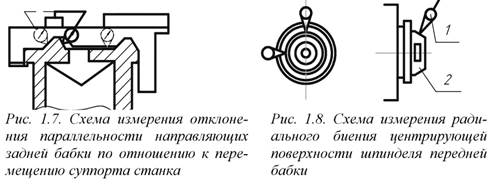
4.8. Радиальное биение центрирующей поверхности шпинделя передней бабки (рис. 8).
4.8.1. Установить и закрепить индикатор 1 на неподвижной части станка, коснувшись измерительным наконечником перпендикулярно образующей конической поверхности шпинделя 2.
4.8.2. Вращая шпиндель станка в рабочем направлении, снять показания индикатора. При измерении шпиндель должен сделать не менее двух оборотов. Отклонение определяют как наибольшую алгебраическую разность показаний индикатора. Допустимое отклонение 0,008 мм.
4.9. Осевое биение шпинделя передней бабки (рис. 1.9).
4.9.1. Установить контрольную оправку 2 в конусное отверстие 1 передней бабки станка.
4.9.2. Установись и закрепить на неподвижной части станка индикатор 3, коснувшись измерительным наконечником центра поверхности оправки 2 вдоль оси шпинделя станка.
4.9.3. Вращая шпиндель в рабочем направлении, произвести измерения по показаниям индикатора. При измерении шпиндель должен сделать не менее двух оборотов. Отклонение определяют как наибольшую алгебраическую разность результатов измерений. Допустимое отклонение 0,008 мм.
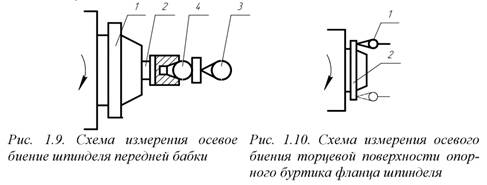
4.10. Осевое биение торцевой поверхности опорного буртика фланца шпинделя передней бабки (рис. 1.10).
4.10.1. Установить и закрепить на неподвижной части станка индикатор 1, коснувшись измерительным наконечником перпендикулярно торцевой поверхности опорного буртика шпинделя 2 на возможно большем расстоянии от его центра.
4.10.2. Вращая шпиндель в рабочем направлении, снять показания индикатора в двух взаимно перпендикулярных плоскостях диаметрально противоположных точках поочередно (в 4-х точках на поверхности фланца через каждые 90°). При каждом измерении шпиндель должен сделать не менее двух оборотов. Отклонение определяют как наибольшую алгебраическую разность показаний индикатора в каждом его положении. Допустимое отклонение - 0,015 мм.
4.11. Радиальное биение конического отверстия шпинделя передней бабки (рис. 1.11): а) -у торца; б) - на длине L=300 мм.
4.11.1. В коническое отверстие шпинделя (Морзе 5) установить контрольную оправку 3 с цилиндрической измерительной поверхностью.
4.11.2. На неподвижной части станка установить и закрепить индикатор 2, касаясь измерительным наконечником поверхности контрольной оправки в точке А в направлении ее оси, перпендикулярно образующей.
4.11.3. Вращая шпиндель в рабочем направлении, произвести замеры по показаниям индикатора. При измерении шпиндель должен сделать не менее двух оборотов.
4.11.4. Повторить измерения в точке Б. Замеры произвести 4-х кратно, меняя каждый раз положение оправки в конусном отверстии шпинделя через каждые 90° в 2-х взаимно перпендикулярных плоскостях. Отклонение определяют как наибольшую алгебраическую разность показаний индикатора в каждом его положении. Допустимые отклонения: у торца - 0,008 мм, на длине L = 300 мм - 0,025 мм.
4.12. Отклонение от параллельности оси вращения шпинделя передней бабки по отношению к продольному перемещению суппорта станка в плоскостях: а - вертикальной, б - горизонтальной (рис. 1.12).
4.12.1. Установить контрольную оправку 3 с цилиндрической измерительной поверхностью в конусное отверстие шпинделя 1.

4.12.2. Установить на суппорте 4 и закрепить в резцедержателе индикатор 2, касаясь измерительным наконечником в вертикальной плоскости перпендикулярно к образующей поверхности оправки в направлении к ее оси.
4.12.3. Перемещая суппорт в продольном направлении вдоль станины станка на всю длину хода L , снять показания индикатора.
4.12.4. Повернуть шпиндель на 180° и повторить замер.
4.12.5. Повторить измерение в горизонтальной плоскости.
Отклонение определяют как среднеарифметическую величину нескольких измерений в каждой плоскости, каждый из которых определяют как наибольшую алгебраическую разность показаний индикатора при перемещении суппорта.
Допустимое отклонение на расстоянии L = 300 мм:
а) в вертикальной плоскости 0..0,02 мм;
б) в горизонтальной плоскости 0..0,01, мм.
Свободный конец оправки может отклоняться вверх и в направлении к резцу.
4.13. Отклонение от параллельности продольного перемещения верхних салазок суппорта по отношению к оси вращения шпинделя передней бабки в вертикальной плоскости (рис. 1.13).
4.13.1. Установить контрольную оправку 3 с цилиндрической измерительной поверхностью в конусное отверстие шпинделя 1.
4.13.2. Установить в верхних салазках суппорта 4 и закрепить в резцедержателе индикаторный прибор 2, коснувшись измерительным наконечником перпендикулярно образующей измерительной поверхности оправки в направлении к ее оси в вертикальной плоскости.
4.13.3. Салазки верхнего суппорта установить таким образом, чтобы они в горизонтальной плоскости были отдалены на одинаковом расстоянии от концов оправки.
4.13.4. Перемещая верхние салазки суппорта вдоль оси шпинделя, произвести измерения не менее чем в трех поперечных сечениях оправки крайних и средних.
Для определения наибольшего показания индикатора в каждом из положений суппорта верхнюю часть его перемещают в поперечном направлении вперед и назад.
4.13.5. Повернуть шпиндель на 180° и повторить замер.
Отклонение определяют как среднее арифметическое двух указанных измерений, каждое из которых определяется как наибольшая алгебраическая разность показаний индикатора в указаниях положениях салазок суппорта. Допустимое отклонение от 0 до 0,020 мм на длине L=100 мм. Свободный конец оправки может отклоняться только вверх.

4.14. Отклонение от параллельности перемещений пиноли задней бабки по отношению к продольному перемещению суппорта в вертикальной и в горизонтальной плоскостях (рис. 1.14).
4.14.1. Установить заднюю бабку в положение, предусмотренное для проверки (см. п. 4.6) с учетом обеспечения хода каретки на длину L.
4.14.2. Вдвинуть пиноль 3 в заднюю бабку 4 и зажать.
1.14.1. Установить и закрепить индикатор 2 на верхнем суппорте станка, коснувшись измерительным наконечником в вертикальной плоскости перпендикулярно образующей поверхности в точке А в направлении к ее оси и снять показания.
4.14.1. Отжать пиноль и, выдвинув на длину больше L, снова зажать.
4.14.2. Переместить суппорт станка с индикатором в продольном направлении в сторону передней бабки к той же точке касания А на образующей пиноли задней бабки измерительным наконечником индикатора.
4.14.3. Повторить замеры в горизонтальной плоскости. Отклонение в каждой из плоскостей определяют как наибольшую алгебраическую разность показаний индикатора в двух указанных положениях пиноли и суппорта.
Допустимое отклонение на всей длине выдвижения:
а) в вертикальной плоскости - 0..0,02 мм;
б) в горизонтальной плоскости - 0..0,01 мм.
Свободный конец пиноли может отклоняться вверх и в сторону инструмента.
4.15. Отклонение от параллельности оси конусного отверстия пиноли задней бабки по отношению к перемещению суппорта станка в плоскостях: (рис. 1.15)
а) в вертикальной плоскости;
б) в горизонтальной плоскости.
4.15.1. Установить контрольную оправку 1 с цилиндрической измерительной поверхностью в конусное отверстие вдвинутой и зажатой пиноли 3 задней бабки.
4.15.2. Установить на суппорте 4 индикатор 2 так, чтобы его измерительный наконечник касался измерительной поверхности оправки в вертикальной плоскости перпендикулярно образующей в направлении к ее оси.
4.15.3. Переместить суппорт станка по станине в продольном направлении на длину L и снять показания индикатора. Отклонение определяют как наибольшую алгебраическую разность показаний индикатора в указанных положениях суппорта. Допустимые отклонения на длине L = 200 мм:
а) в вертикальной плоскости - 0..0,020 мм;
б) в горизонтальной плоскости - 0..0,020 мм.
Свободный конец оправки может отклоняться вверх и в сторону инструмента.
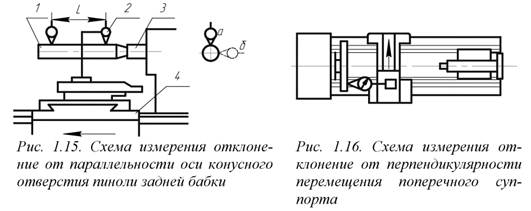
4.16. Отклонение от перпендикулярности перемещения поперечного суппорта по отношению к оси шпинделя станка (рис. 1.16).
4.16.1. Установить в конусное отверстие шпинделя станка специальный контрольный диск (линейку).
4.16.2. Установить и закрепить на поперечном суппорте станка индикатор так, чтобы измерительный наконечник касался перпендикулярно торцевой поверхности контрольного диска (линейки).
4.16.3. Перемещая поперечный суппорт на длину L, снять показания индикатора.
4.16.4. Повернуть шпиндель станка на 180° и повторить замер. Отклонение определяют как среднее арифметическое результатов двух замеров. Допустимое отклонение на длине L = 150 мм - 0..0,20 мм.
Допускается единственное отклонение, при котором обработанная торцевая поверхность будет только вогнутой.
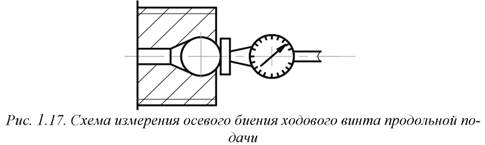
4.17. Осевое биение ходового винта продольной подачи (рис. 1.17).
4.17.1. Установить шарик в центровое отверстие ходового винта.
4.17.2. Установить и закрепить на станине станка индикатор так, чтобы измерительный наконечник индикатора касался шарика через плоскопараллельные плитки по оси ходового винта. Вращая ходовой винт в правую сторону, снять показания индикатора. При этом обеспечить осевую нагрузку, которая может быть создана суппортом станка, перемещающегося после сопряжения ходового винта с ходовой маточной гайкой.
4.17.3. Повторить замер при вращении ходового винта в левую сторону. Допустимое отклонение 0,010 мм.
4.18. Осевое биение ходового винта поперечной подачи (То же, что и в п. 4.17).
5. Контрольные вопросы
5.1. Точность станков и способы ее оценки.
5.2. От чего зависят и что характеризуют геометрические погрешности в металлорежущих станках?
5.3. Какими документами регламентируются нормы точности станков?
5.4. На что влияет геометрическая точность станка?
5.5. Перечислите методы повышения точности станков?
Содержание отчета
1. Перечислить основные паспортные данные станка.
2. Заполнить таблицу 1.1 в виде:
Таблица 1.1
Номер проверки
| Что проверяется
| Схема проверки
| Допустимое отклонение по ГОСТ 18097-72
|
| Отклонение от прямолинейности направляющих суппорта станка (станины) в вертикальной плоскости
| (рис. 1.1)
|
|
| Отклонение от прямолинейности продольного перемещения суппорта в вертикально плоскости
| (рис. 1.2)
|
|
| Отклонение от параллельности направляющих суппорта станка (станины) на отсутствие короблений
|
|
|
| (рис. 1.3)
|
|
| Отклонение от прямолинейности продольного перемещения суппорта станка в горизонтальной плоскости
|
|
|
| (рис. 1.4)
|
|
| Отклонение, от параллельности линии центров по отношению к направляющим станины в вертикальной плоскости (рис. 1.5).
|
|
|
| (рис. 1.5)
|
|
| Отклонение от параллельности перемещения пиноли задней бабки; по отношению к перемещению суппорта станка
| (рис. 1.6)
|
|
|
|
|
| Отклонение параллельности направляющих задней бабки по отношению к перемещению суппорта станка
| (рис. 1.7)
|
|
|
|
|
| Радиальное биение центрирующей поверхности шпинделя передней бабки
под патрон
|
|
|
| (рис. 1.8)
|
|
| Осевое биение шпинделя передней бабки
| (рис. 9)
|
|
| Осевое биение торцевой поверхности опорного буртика фланца шпинделя передней бабки
|
|
|
| (рис. 1.10)
|
|
| Радиальное биение конического отверстия шпинделя передней бабки, проверяемое:
а) у торца; б) на длине L = 300 мм
|
|
|
| (рис. 1.11)
|
|
| Отклонение от параллельности оси вращения шпинделя передней бабки по отношению к продольному перемещению суппорта станка в плоскостях: а - вертикальной, б - горизонтальной
|
|
|
| (рис. 1.12)
|
|
|
|
|
| Отклонение от параллельности продольного перемещения верхних салазок суппорта по отношению к оси вращения шпинделя передней бабки в вертикальной плоскости
|
|
|
| (рис. 1.13)
|
|
| Отклонение от параллельности перемещений пиноли задней бабки по отношению к продольному перемещению суппорта в плоскостях:
а) в вертикально,
б) в горизонтальной.
|
|
|
| (рис. 1.14)
|
|
|
|
|
|
|
|
| Отклонение от параллельности оси конусного отверстия пиноли задней бабки по отношению к перемещению суппорта станка в плоскостях:
а) в вертикальной плоскости;
б) в горизонтальной плоскости
|
|
|
| (рис. 1.15)
|
|
|
|
|
|
|
|
| Отклонение от перпендикулярности перемещения поперечного суппорта по отношению к оси шпинделя станка
|
|
|
| (рис. 1.16)
|
|
| Осевое биение ходового винта продольной подачи
| (рис. 1.17)
|
|
Не нашли, что искали? Воспользуйтесь поиском по сайту:
©2015 - 2025 stydopedia.ru Все материалы защищены законодательством РФ.
|