Дайте определение ударной вязкости (KCV). Опишите методику измерения этой характеристики механических свойств металла.
КОНТРОЛЬНАЯ РАБОТА
по дисциплине
«Металловедение (включая сварку)»
Вариант № 25
Выполнил
| студент Кольцова О.И.
| Гр. 1042 – 03С
| Проверил
| Преподаватель Суханов Л.А.
|
Псков
1. Что такое ликвация? Причины её возникновения и способы устранения.тан
Ликвация (от лат. liquatio - разжижение, плавление) называют химическую неоднородность металлов, возникающую при их кристаллизации.
Неоднородность по составу приводит к различию в свойствах и общему ухудшению качества сплава.
Различают ликвацию макроскопическую, когда неоднородность видна глазом и микроскопическую, которая видна под микроскопом и может быть выявлена химическим анализом.
Ликвация в пределах слитка называется зональной ликвацией (макроскопический уровень), а ликвация в пределах дендрита - дендритной ликвацией (микроскопический уровень).
Дендритная ликвация проявляется в микрообъёмах сплава, близких к размеру зёрен. Дендритная ликвация выражается в том, что оси дендритных кристаллов отличаются по химическому составу от межосных пространств.
Этот вид ликвации может быть в значительной степени устранён при длительном отжиге металла (так называемая гомогенизация) в результате диффузии примесей.
Внутри дендрита различают состав сплава в осях, в межосных пространствах и по его границам.
Макроскопическая ликвация выражается в том, что по сечению всего слитка или отдельных его частей наблюдаются невооруженным глазом области, обогащенные примесями. Зональная ликвация, наблюдаемую во всём объёме слитка. Зональная ликвация выражается в наличии в слитке нескольких зон с различным химическим составом, которые в зависимости от характера отклонений от среднего состава сплава называются зонами положитель
Для уменьшения зональной ликвации ограничивают размеры слитков, а также применяют специальные металлургические процессы: непрерывную разливку, переплав в водоохлаждаемом кристаллизаторе (электрошлаковый или вакуумный) и т.п.
Ликвация относится к категории явлений расслоения, приводящих к колебаниям состава, возникающим в результате затвердевания в макро- и микрообластях; ликвация прямо связана с негомогенностью структуры.
Ликвацию классифицируют следующим образом:
) Ликвация в пределах кристалла (в микрообъёмах).
2) Ликвация в слитке, или зональная ликвация (в макрообъёмах), которая подразделяется на:
ликвацию, связанную с направлением теплового потока (с направленным теплоотводом); может быть обычной (нормальной) и обратной;
ликвацию, связанную с действием силового поля; может быть графитационной (по весу) и возникающей при центрифугировании.
Для зональной макроликвации возможна ещё классификация:
. Общая, которая может быть положительной ликвацией в слитке или отливке (прямой) и отрицательной (обратной).
. Местная (кайма по кромке затвердевания; V-образная ликвация; ликвационные шнуры; обратная V-образная ликвация, или теневые полосы; пятнистая ликвация; ликвация, связанная с газовыми пузырями).
Ликвация усиливается при:
а) увеличении скорости охлаждения (особенно дендритная ликвация);
б) уменьшении скорости диффузии.
Ликвация уменьшается (в редких случаях дендритная ликвация устраняется) в результате гомогенизационного или диффузионного отжига. Количественная оценка ликвации в кристалле осуществляется с помощью коэффициента ликвации Kликв. На величину ликвации в кристалле влияет сочетание количеств легирующих добавок.
Причиной ликвации является образование разного состава кристалла. Ликвация возникает в результате того, что сплавы, в отличие от чистых металлов, кристаллизуются не при одной температуре, а в интервале температур. При этом состав кристаллов, образующихся в начале затвердевания, может существенно отличаться от состава последних порций кристаллизующегося маточного раствора. Чем шире температурный интервал кристаллизации сплава, тем большее развитие получает ликвация, причём наибольшую склонность к ней проявляют те компоненты сплава, которые наиболее сильно влияют на ширину интервала кристаллизации (для стали, это например, сера, кислород, фосфор, углерод).
Для уменьшения степени ликвации необходимо весьма медленное охлаждение сплава в интервале температур кристаллизации и ниже, для полного протекания выравнивающей диффузии.
Дайте определение ударной вязкости (KCV). Опишите методику измерения этой характеристики механических свойств металла.
Ударная вязкость - это способность материала поглощать механическую энергию в процессе деформации и разрушения под действием ударной нагрузки. Ударная вязкость характеризует надежность материала, его способность сопротивляться хрупкому разрушению.
Испытания на ударную вязкостьотносятся к динамическим видам испытаний. Для определения ударной вязкости используют стандартные образцы с надрезом U- или V-образной формы, который служит концентратором напряжений. В зависимости от формы надреза ударная вязкость обозначается KCU или KCV.
Образец квадратного или прямоугольного сечения с концентраторами вида U, V и Т (рисунок 1) устанавливают на опорах маятникового копра надрезом в сторону, противоположную удару ножа маятника, который поднимают на определенную высоту. Удар наносят посередине образца со стороны, противоположной надрезу. За окончательный результат испытания принимают работу удара или ударную вязкость для образцов с концентраторами видов U и V и ударную вязкость для образцов с концентратором вида Т (усталостная трещина, получаемая в вершине начального надреза при циклическом изгибе образца в одной плоскости). Работу (KU, KV или КТ) разрушения образца определяют обычно по специальной шкале маятникового копра. После определения работы разрушения образца вычисляют ударную вязкость KCU (KCV, КСТ):
КС= = K/S0,
где S0 - площадь поперечного сечения образца в месте надреза, см2.
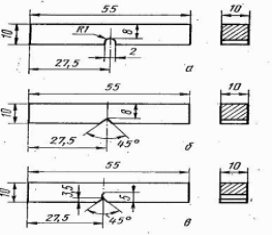
Рисунок 1 - Образцы для испытаний на ударную вязкость:
а-в-соответственно с концентраторами вида U, V и T (усталостная трещина).
Работу удара обозначают двумя буквами (KU, KV или КТ) и цифрами. Первая буква (К) - символ работы удара, вторая буква (U, V или Т) - вид концентратора. Последующие цифры обозначают максимальную энергию удара маятника, глубину концентратора и ширину образца. Цифры не указывают при определении работы удара на копре с максимальной энергией удара маятника 30 кгс•м, при глубине концентратора 2 мм для концентраторов видов U и V и 3 мм для концентратора типа Т и ширине образца 10 мм.
Ударную вязкость также обозначают сочетанием букв и цифр. Первые две буквы КС обозначают символ ударной вязкости, третья буква - вид концентратора; первая цифра - максимальную энергию удара маятника, вторая - глубину концентратора и третья - ширину образца. Цифры не указывают в тех же случаях, что и для работы удара. Применяют 10 типов образцов с надрезом вида U, А - с надрезом вида V и 6 - с надрезом вида Т.
Для определения ударной вязкости хрупких материалов (чугунов, сталей с твердостью HRC 55 и выше) допускается применение призматических образцов с размерами 10х10х55 мм без надреза. Ударную вязкость, полученную при испытании таких образцов, обозначают символом КС без индекса.
Для более точной оценки вязкости материалов иногда ударную вязкость как интегральную характеристику делят на две составляющие - удельную работу зарождения а3 и удельную работу развития ар трещины: aH = a3 + aр. При хрупком разрушении работа распространения трещины близка к нулю, а при полухрупком она снижается пропорционально проценту вязкой составляющей в изломе, поэтому целесообразно определять ар только при полностью вязком изломе.
Существует несколько методов определения а3 и ар. Наиболее распространены метод Б.А. Дроздовского (предварительное нанесение на образец усталостной трещины) и метод А.П. Гуляева (испытание образцов с разными надрезами и построение зависимости ударной вязкости от радиуса надреза); экстраполяция прямой до нулевого значения радиуса надреза дает возможность получить величину ар.
Таким образом, ударная вязкость показывает, какой стойкостью обладает материал к ударному излому.
3. Вычертите диаграмму состояния железо-карбид железа, укажите структурные составляющие во всех областях диаграммы, опишите превращения для сплава, содержащего 3,6% С. Какова структура этого сплава при комнатной температуре, и как такой сплав называется?
Первичная кристаллизация сплавов системы железо-углерод начинается по достижении температур, соответствующих линии ABCD (линии ликвидус), и заканчивается при температурах, образующих линию AHJECF (линию солидус). При кристаллизации сплавов по линии АВ из жидкого раствора выделяются кристаллы твердого раствора углерода в б-железе (д-раствор). Процесс кристаллизации сплавов с содержанием углерода до 0,1% заканчивается по линии АН с образованием б (д) - твердого раствора. На линии HJB протекает перитектическое превращение, в результате которого образуется твердый раствор углерода в г-железе, т.е. аустенит. Процесс первичной кристаллизации сталей заканчивается по линии AHJE. При температурах, соответствующих линии ВС, из жидкого раствора кристаллизуется аустенит. В сплавах, содержащих от 4,3% до 6,67% углерода, при температурах, соответствующих линии CD, начинают выделяться кристаллы цементита первичного. Цементит, кристаллизующийся из жидкой фазы, называется первичным цементитом. B точке С при температуре 1147°С и концентрации углерода в жидком растворе 4,3% образуется эвтектика, которая называется ледебуритом. Эвтектическое превращение с образованием ледебурита можно записать формулой ЖР4,3 Л [А2,14+Ц6,67]. Процесс первичной кристаллизации чугунов заканчивается по линии ECF образованием ледебурита. Таким образом, структура чугунов ниже 1147°С будет: доэвтектических - аустенит + ледебурит, эвтектических - ледебурит и заэвтектических - цементит (первичный) + ледебурит. Превращения, происходящие в твердом состоянии, называются вторичной кристаллизацией. Они связаны с переходом при охлаждении г-железа в б-железо и распадом аустенита. Линия GS соответствует температурам начала превращения аустенита в феррит. Ниже линии GS сплавы состоят из феррита и аустенита. Линия ЕS показывает температуры начала выделения цементита из аустенита вследствие уменьшения растворимости углерода в аустените с понижением температуры. Цементит, выделяющийся из аустенита, называется вторичным цементитом. В точке S при температуре 727°С и концентрации углерода в аустените 0,8% образуется эвтектоидная смесь состоящая из феррита и цементита, которая называется перлитом. Перлит получается в результате одновременного выпадения из аустенита частиц феррита и цементита. Процесс превращения аустенита в перлит можно записать формулой А0,8→П [Ф0,03+Ц6,67]. Линия PQ показывает на уменьшение растворимости углерода в феррите при охлаждении и выделении цементита, который называется третичным цементитом.
Следовательно, сплавы, содержащие менее 0,008% углерода (точкаQ), являются однофазными и имеют структуру чистого феррита, а сплавы, содержащие углерод от 0,008 до 0,03% - структуру феррит + цементит третичный и называются техническим железом.
Доэвтектоидные стали при температуре ниже 727єС имеют структуру феррит+перлит и заэвтектоидные - перлит+цементит вторичный в виде сетки по границам зерен. В доэвтектических чугунах в интервале температур 1147-727єС при охлаждении из аустенита выделяется цементит вторичный, вследствие уменьшения растворимости углерода (линия ES). По достижении температуры 727єС (линия PSK) аустенит, обедненный углеродом до 0,8% (точка S), превращаясь в перлит. Таким образом, после окончательного охлаждения структура доэвтектических чугунов состоит из перлита, цементита вторичного и ледебурита превращенного (перлит+цементит).
Структура эвтектических чугунов при температурах ниже 727єС состоит из ледебурита превращенного. Заэвтектический чугун при температурах ниже 727єС состоит из ледебурита превращенного и цементита первичного.
Правило фаз устанавливает зависимость между числом степеней свободы, числом компонентов и числом фаз и выражается уравнением:
С= K + 1 - Ф,
где С - число степеней свободы системы; К - число компонентов, образующих систему; 1 - число внешних факторов (внешним фактором считаем только температуру, так как давление за исключением очень высокого мало влияет на фазовое равновесие сплавов в твердом и жидком состояниях); Ф - число фаз, находящихся в равновесии.
Сплав железа с углеродом, содержащий 3,6% С, называется доэвтектическим чугуном. Его структура при комнатной температуре - перлит + цементит + ледебурит.
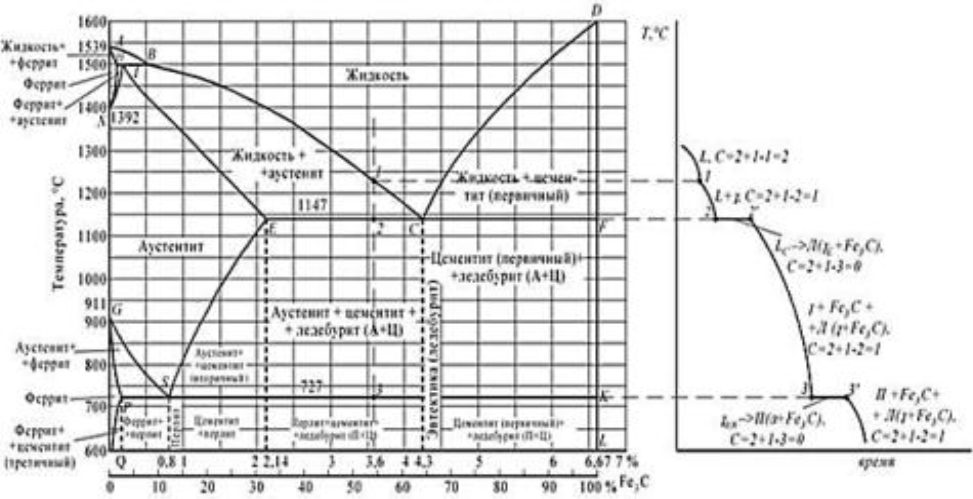
Рисунок 2 - диаграмма железо-цементит и кривая охлаждения для сплава, содержащего 3,6% углерода
4. Вычертите диаграмму изотермического превращения аустенита для стали У8, нанесите на нее кривую режима изотермической обработки, обеспечивающей получение твердости 45-50 НRC. Укажите, как этот режим называется, опишите сущность превращений и структуру, получаемую в этом случае.
Сталь У8 содержит 0,8% углерода, т.е. это эвтектоидная сталь.
Изотермической обработкой, необходимой для получения твердости 45…50 HRC, является изотермическая закалка - вид термической обработки, заключающийся в нагреве стали до температуры выше критической точки, выдержке и последующем быстром охлаждении со скоростью не ниже критической.
Нагрев при закалке производится для перевода всей исходной структуры или определенной ее части в аустенит, который является исходной фазой для получения конечной структуры закаленной стали.
Выдержка необходима для выравнивания температуры по сечению детали и для полного установления необходимого фазового состояния.
Охлаждение при закалке должно производиться со скоростью не меньше критической для того, чтобы предотвратить протекание диффузионных процессов и переохладить весь исходный аустенит до температурного интервала мартенситного превращения.
Критическая скорость охлаждения (закалки) - это минимальная скорость охлаждения, при которой предотвращается диффузионный распад переохлажденного аустенита.
Температура закалки определяется исходя из массовой доли углерода в стали и соответствующего ей значения критической точки. Практически критические точки выбирают по справочникам или по диаграмме состояния «железо - цементит». Продолжительность нагрева и выдержки определяется размерами и конфигурацией деталей и способом их укладки в печи. Она должна быть такой, чтобы прошло выравнивание концентрации углерода в аустените. Обычно общее время нагрева и изотермической выдержки составляет 1-1,5 мин на мм наибольшего поперечного сечения.
Закалочное охлаждение эвтектоидной и доэвтектоидных сталей происходит из однофазной аустенитной области, поэтому структура этих сталей после закалки будет представлять мартенсит с небольшим количеством остаточного аустенита.
Диаграмма изотермического превращения аустенита для этой стали приведена на рисунке 3.
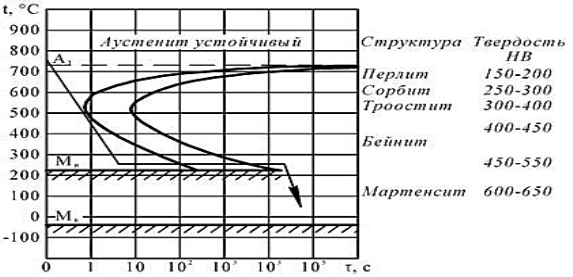
Рисунок 3 - Диаграмма изотермического превращения аустенита стали У8
При изотермической закалке сталь У8 нагревают до температуры на 30-50°С выше точки Ас1 (Ас1 = 730°С) и после выдержки охлаждают до температуры 250-350°С, что несколько превышает температуру начала мартенситного превращения. Выдержка деталей в закалочной среде должна быть достаточной для полного превращения аустенита в нижний бейнит, имеющий твердость 45…50 HRC. Нижний бейнит представляет собой структуру, состоящая из б-твердого раствора, претерпевшего мартенситное превращение и несколько пересыщенного углеродом, и частиц карбидов. В качестве охлаждающей среды при изотермической закалке применяют расплавленные соли или расплавленные щелочи.
Не нашли, что искали? Воспользуйтесь поиском по сайту:
©2015 - 2025 stydopedia.ru Все материалы защищены законодательством РФ.
|