Приборов и автоматических систем обеспечения безопасности
В соответствии с требованиями [2] производственное оборудование должно обеспечивать безопасность работающих при монтаже (демонтаже), вводе в эксплуатацию и эксплуатации, как в случае автономного использования, так и в составе технологических комплексов при соблюдении требований (условий, правил), предусмотренных эксплуатационной документацией.
При этом безопасность конструкции производственного оборудования обеспечивается:
- выбором принципов действия и конструктивных решений, источников энергии и характеристик энергоносителей, параметров рабочих процессов, системы управления и ее элементов;
- минимизацией потребляемой и накапливаемой энергии при функционировании оборудования;
- выбором комплектующих изделий и материалов для изготовления конструкций, а также применяемых при эксплуатации;
- выбором технологических процессов изготовления;
- применением встроенных в конструкцию средств защиты работающих, а также средств информации, предупреждающих о возникновении опасных (в том числе пожаровзрывоопасных) ситуаций
- надежностью конструкции и ее элементов (в том числе дублированием отдельных систем управления, средств защиты и информации, отказы которых могут привести к созданию опасных ситуаций);
- применением средств механизации, автоматизации (в том числе автоматического регулирования параметров рабочих процессов) дистанционного управления и контроля;
- возможностью использования средств защиты, не входящих в конструкцию;
- выполнением эргономических требований;
- ограничением физических и нервнопсихических нагрузок на работающих.
Все исходные наиболее критичные предпосылки, инициирующие отказы элементов и узлов оборудования должны быть проанализированы на соответствие с требованиями [2, раздел 2].
Пример 1. При токарной обработке заготовок высока вероятность выбрасывания инструмента в результате либо ошибки оператора при его закреплении, либо отказа узла крепления. Это не соответствует требованиям [2, раздел 2, пункт 2.1.4]: «Конструкция производственного оборудования должна исключать падение или выбрасывание предметов (например, инструмента, заготовок, обработанных деталей, стружки), представляющих опасность для работающих, а также выбросов смазывающих, охлаждающих и других рабочих жидкостей».
Обычно конструкцией токарного станка предусмотрено не исключение выбрасывания инструмента, а исключение его попадания в оператора за счет применения защитного щитка, т.е. конструкцией резцедержателя не предусмотрено дополнительных технических решений, исключающих выбрасывание инструмента, рис. 3.

Рис. 3. Обычно используемый вариант крепления резца:
1 – резцедержатель; 2 – резец; 3 – крепежные болты.
Может быть предложено такое решение, путем выполнения прямоугольной канавки на нижней пластине резцедержателя, которой и устанавливается тело резца. Эта канавка исключает выбрасывание резца из резцедержателя при неплотном его закреплении иле отказе элементов крепления, за счет невозможности поперечного смещения резца, а допускает только его продольное смещение, что не приводит к выбрасыванию резца, рис. 4.
Пример 2.В металлорежущих станках должен использоваться защитный щиток (экран), который разделяет зону резания и зону нахождения оператора, т.е. обеспечивает его защиту от возможных выбросов инструмента и заготовки, их осколков, стружки. Обязательность
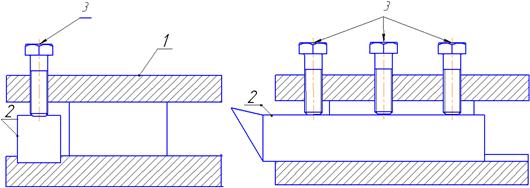
Рис. 3. Модернизированный вариант крепления резца:
1 – резцедержатель; 2 – резец; 3 – крепежные болты.
применения защитного щитка обеспечивается схемой блокировки (в соответствии с требованиями [2, раздел 2, пункт 2.4.8]), рис. 4, которая исключает включение станка, если защитный щиток (экран) находится в положении, не обеспечивающем защиту.
Рисунок 4. Схема блокировки защитного щитка:
S1 – контактор блокировки.
В положении, обеспечивающем защиту, контактор блокировки S замкнут, что позволяет оператору с помощью электромеханического пускателя включить станок. В случае отказа контактора блокировки S (отказ может быть либо в виде разрушения контактной группы – что не приводит к повышению опасности, станок просто не включится, либо в «залипании» контактов – что существенно повышает опасность травмирования оператора, поскольку станок можно включить в положении защитного щитка, не обеспечивающем защиту) вероятность происшествия резко возрастает.
Несложная модернизация схемы блокировки, рис. 5, может существенно повысить ее надежность, а индикация, введенная в схему блокировки, позволяет поддерживать высокую надежность во времени.

Рис. 5. Модернизированная схема блокировки защитного щитка:
S1 – контактор блокировки; S2 – дополнительный контактор блокировки;
R1, R2, H1, H2 – элементы схемы индикации исправности контакторов.
Последовательное включение в схему двух контакторов S1 и S2, имеющих вероятности отказов P1 и P2 приводит к тому, что отказ блокировки произойдет при одновременном отказе S1 и S2 (отказы P1, P2 не зависят друг от друга и объединены логическим объединением «ИЛИ») вероятность отказа блокировки PБ в целом составит
PБ = P1 P2.
Поскольку P1 , P2 <1 то PБ < P1 , P2. Если один из контакторов S1 или S2 откажет (отказ в «залипании» контактов), то система блокировки возвращается к исходной более низкой надежности. Для исключения этого параллельно каждому из контакторов включается элемент индикации Н1 и Н2. При отказе одного из контакторов («залипании» его контактов) в положении защитного щитка, не обеспечивающем защиту, соответствующий индикатор не загорится, так как оказывается замкнутым накоротко «залипшими» контактами контактора. Это позволит своевременно определить и заменить отказавший контактор.
Требования безопасности к конкретным видам технологического оборудования регламентируются соответствующими стандартами ССБТ. Смотри, например [9, 10, 11, 12 и др.].
Не нашли, что искали? Воспользуйтесь поиском по сайту:
©2015 - 2024 stydopedia.ru Все материалы защищены законодательством РФ.
|