Виды, устройство и принцип работы задвижек
СОДЕРЖАНИЕ
Введение………………………………………………………………………...
|
| 1 Литературный обзор…………………………………………………………..
|
| 1.1 Подготовка к ремонту основного технологического оборудования блока ректификации фракций Н.К. 80 0С (ДИП) абсорбционно-газофракционирующей установки (АГФУ)…………………………………
|
| 1.2 Ремонт основного технологического оборудования блока ректификации фракций Н.К. 80 0С (ДИП) абсорбционно-газофракционирующей установки…………………………………………………………………….
|
| 1.3 Виды, устройство и принцип работы задвижек………………………..
|
| 2 Технологический раздел……………………………………………………….
|
| 2.1 Технические и технологические характеристики основного оборудования блока ректификации фракций Н.К. 80 0С (ДИП) абсорбционно-газофракционирующей установки (АГФУ)………………
|
| 3 Монтаж технологических трубопроводов…………………………………..
|
| Заключение……………………………………………………………………….
|
| Список использованных источников…………………………………………..
|
|
ВВЕДЕНИЕ
Анализ работы газофракционирующих установок нефтехимических предприятий еще в 70-х годах прошлого века показал, что наиболее эффективным техническим решением является применение ректификационных процессов разделения. В частности, такие установки сейчас работают на Нижнекамском и Тобольском НХК.
На НПЗ для разделения нефтезаводских газов применяются преимущественно два типа газофракционирующих установок, в каждый из которых входят блоки компрессии и конденсации: ректификационный ‒ сокращенно ГФУ и абсорбционно–ректификационный ‒ АГФУ.
Абсорбционно‒газофракционирующая установка (АГФУ‒1) ‒ предназначена для сбора, компремирования жирных газов, стабилизации рефлюксов и бензинов термических крекингов, бензинов, факельных конденсатов, конденсата прямогонного газа.
В состав установки входят следующие блоки:
‒ блок сбора и компремирования жирных газов;
‒ блок ректификации бензинов термических крекингов, бензинов с установок 21‒10, ЛЧ‒24‒7, рефлюксов с установок ТК‒2,3, 22‒4, Л‒35‒11/1000, «Жекса», ОАО «УНПЗ», факельных конденсатов, конденсата прямогонного газа;
‒ блок теплоносителя – дизельное топливо;
‒ блок сбора и компремирования прямогонного и углеводородных газов;
‒ блок фракционирования фракции НК‒80°с (ДИП);
‒ блок деизогексанизации (ДИГ);
‒ блок теплоносителя АМТ‒300.
Для проведения химико-технологических процессов (нагрев, охлаждение, ректификация, абсорбция, химическое превращение) на предприятиях нефтегазопереработки и нефтехимии используется разнообразное оборудование установок при различных рабочих условиях (температура, среда, давление), что во многом предопределяет характер износа оборудования при его эксплуатации и специфику выполняемых в последующем ремонтных работ.
Нарушение работы аппаратуры может происходить в результате коррозионного износа (химическое или электрохимическое воздействие агрессивной среды на материал), эрозионного износа (истирание материала под действием сил трения и удара со стороны жидкой или содержащей твердые частицы рабочей среды), термического износа (снижение прочности и нарушение плотности элементов и соединений в результате воздействия высоких температур, высоких температурных напряжений, явлений ползучести, релаксации и нарушения стабильности структуры сталей), механического износа (пластические деформации и нарушение целостности деталей), а также в результате загрязнения рабочих поверхностей отложениями.
Литературный обзор
Многие аппараты (колонны, реакторы, трубчатые печи) имеют значительные габаритные размеры, массу, стоимость и их относят к основному оборудованию. Основное оборудование, как правило, не дублируется и остановка его для проведения профилактического (предупредительного) ремонта или же его отказ в результате аварии требуют остановки всей технологической линии (установки, блока, предприятия). Ремонт основного оборудования без остановки технологической линии возможен лишь в случае периодически действующих аппаратов и машин, которые можно ремонтировать в нерабочую для них смену [1].
Ремонт оборудования нефтегазоперерабатывающих и нефтехимических предприятий производится в соответствии с системой планово-предупредительных ремонтов (система ППР).
Система ППР включает в себя:
‒ межремонтное техническое обслуживание;
‒ плановые осмотры оборудования;
‒ также ремонты малые (текущие), средние (для аппаратов не обязательны) и капитальные.
Виды ремонтов отличаются один от другого объемом выполняемых работ. Капитальный ремонт оборудования позволяет практически полностью восстановить его первоначальное состояние и рабочие параметры при его эксплуатации.
1.1 Подготовка к ремонту основного технологического оборудования блока ректификации фракций Н.К. 80 0С (ДИП) абсорбционно-газофракционирующей установки (АГФУ)
При подготовке к ремонту колонного оборудования аппарат отключают от коммуникаций, для чего закрывают задвижки, затем снижают в аппарате давление до атмосферного (или устраняют вакуум), после чего удаляют из аппарата оставшийся в нем продукт и на подводящих и отводящих трубопроводах устанавливают заглушки [1].
В сливных карманах тарелок для стока флегмы при остановке аппарата предусмотрены дренажные отверстия диаметром 8 ‒10 мм. Если конструкция полотна не обеспечивает сток флегмы с тарелки на тарелку (колпачковые тарелки), то сливные отверстия выполнены в полотне тарелки.
После слива продукта для удаления остатков взрывопожароопасных и токсичных веществ аппарат пропаривают и промывают водой. В некоторых случаях пропарку и промывку аппарата повторяют несколько раз. Продолжительность пропарки и промывки зависит от рабочих условий в аппарате, вида ремонтных работ и ее указывают в технологической карте.
При пропарке и промывке аппарата снимают основную часть шпилек с люков, оставляя для сокращения времени его ремонта на каждом люке по 6‒8 шпилек. По окончании пропарки и промывки люки вскрывают последовательно в направлении сверху вниз. Запрещается вскрытие верхних и нижних люков одновременно или в направлении снизу вверх, т.к. это может привести к образованию внутри аппарата взрывоопасной смеси углеводородов с воздухом.
Для охлаждения колонны и снижения содержания в ней вредных веществ аппарат за счет естественной конвекции проветривают при открытых люках в течение 4‒6 ч. Отбирая переносны ми газоанализаторами пробы воздуха из разных по высоте колонны мест, определяют концентрацию вредных веществ в аппарате (предельно допустимое содержание углеводородов 300 мг/м3, сероводорода ‒ 10 мг/м3). При достижении концентраций ниже предельных допускаемых значений выдается разрешение на проведение в аппарате очистных и ремонтных работ. Прежде чем приступить к ремонтным работам внутрь аппарата подводится переносное электроосвещение напряжением 12 В во взрывобезопасном исполнении.
1.2 Ремонт основного технологического оборудования блока ректификации фракций Н.К. 80 0С (ДИП) абсорбционно-газофракционирующей установки
В процессе эксплуатации в результате проходящих химических превращений внутренняя поверхность корпуса колонного аппарата и внутренние устройства загрязняются отложениями смол, кокса, продуктов коррозии, что приводит к снижению эффективности работы аппарата. Кроме того, в результате коррозионноэрозионного износа снижается толщина стенок корпуса и повреждаются внутренние устройства [1, 2, 3].
Очистные и ремонтные работы внутри аппарата должны одновременно выполнять не менее двух рабочих: один находится внутри аппарата, другой снаружи наблюдает за работающим внутри, после чего они меняются местами. Работающий внутри аппарата должен обязательно надевать предохранительный пояс с веревкой, противоположный конец которой через люк выводится наружу и надежно закрепляется. При проведении сварочных работ место сварки в аппарате ограждается металлическими листами или пропитанными водой деревянными щитами.
Для осуществления чистки и ремонта колонн требуется разборка их внутренних устройств. Так как крепежные элементы тарелок (гайки, клинья) доступны только сверху, тарелки разбирают в последовательности сверху вниз. Для облегчения работ по разборке внутренних устройств внутри аппарата подвешивают цепную таль. Демонтированные секции тарелок через люки извлекают наружу и с помощью поворотного или неподвижного крана-укосины, который крепится к верху аппарата, опускают на землю. Трос, перекинутый через блок крана-укосины, направляют вниз на пневмолебедку или электролебедку во взрывобезопасном исполнении. Кран-укосину также используют для подъема секций тарелок на обслуживающие площадки к люкам аппарата при последующем монтаже внутренних устройств, после чего их вручную подают внутрь и производят сборку.
При ремонте насадочных колонн производят замену разрушенных и закоксованных насадочных тел. Выгрузку и загрузку насадки осуществляют через люки, используя для этого бадьи с открывающимся днищем, а также сменные переносные или стационарные лотки для транспортировки насадочных тел. В конце лотка устанавливается бункер с затвором-шибером, который гасит скорость падающих насадочных тел и регулирует поступление их в воронку передвижного контейнера.
Для разборки царговых колонн используют монорельс, к которому подвешивается таль. Демонтируемые царги и внутренние устройства (тарелки закрепляют между фланцами царг) приподнимаются и транспортируются по монорельсу.
Внутренний осмотр, чистку и ремонт корпусов высоких пустотелых аппаратов проще производить не путем сооружения в них внутренних лесов, а с использованием подвесных платформ, что позволяет сократить трудовые и материальные затраты, а также продолжительность ремонта. Платформа по частям через люк вводится внутрь аппарата, собирается и соединяется тросом с лебедкой.
Очистку внутренней поверхности корпуса аппарата и внутренних устройств от отложений выполняют механическим, гидромеханическим (водоструйная, пескоструйная чистка) или физико-химическими способами. Выбор способа чистки определяется природой отложений. Время, необходимое для очистки внутренних устройств, можно сократить, заменяя загрязненные детали и узлы тарелок ранее очищенными или новыми из запасного комплекта.
При проведении очистных работ возрастает концентрация вредных веществ в воздухе, в связи с чем необходимо работать в противогазах.
Механическая чистка внутренних поверхностей аппарата ‒ трудоемкая и вредная по условиям труда операция. Механическую чистку выполняют вручную или с механическим приводом (пневматические молотки, турбинки) лопатками, скребками или щетками из цветного металла.
При физико-химическом способе чистки на отложения воздействуют органическими углеводородными растворителями, ингибированными кислотами (соляной, сульфаминовой, лимонной, муравьиной или смесью этих кислот), щелочью, водой. При очистке деталей тарелок их погружают в ванну с растворителем или реагентом. В некоторых случаях физико-химическую чистку можно выполнять без разборки аппаратов, что сокращает время простоя оборудования на ремонте.
При комплексной очистке аппаратуры от отложений ее последовательно промывают легкими углеводородами, кислотой, водой, щелочью и снова водой, после чего производят пассивирование для предотвращения коррозии металла.
По завершении очистных работ проводят дефектацию корпуса и внутренних устройств аппарата. С помощью ультразвукового толщиномера определяют толщину стенки корпуса в местах наибольшего коррозионно-эрозионного износа, которая не должна быть меньше допускаемой толщины стенки корпуса, определяемой механическим расчетом. Толщину стенок деталей тарелок определяют с помощью обычного мерительного инструмента. Дефектные детали и узлы подлежат замене.
Сборку тарелок ведут в направлении снизу вверх. Перед сборкой детали тарелок проверяют на соответствие их размеров проекту и техническим условиям, при необходимости правят, прогоняют резьбу болтов и шпилек, заготавливают прокладки.
Для каждого типа тарелок предусмотрены определенные допуски на прогиб секций, размеры и положение контактных элементов, а также расстояние между ними, например:
Тарелки из S-образных элементов:
‒ кромки зубцов S-образного элемента и колпачка должны быть ровными, без заусенцев; продольное отклонение по высоте зуба ±1 мм;
‒ прогиб S-образного элемента, колпачка и желоба не более 3 мм на всю длину;
‒ концы вертикальных полок S-образного элемента должны находиться в прорезях паровых заглушек соседних элементов. Тарелки решетчатые:
‒ прогиб установленных секций не более 2 мм/м секции и не более 3 мм на всю секцию, допускаются отдельные выпучины до 6 мм;
‒ предельные отклонения расстояния между щелями, а также длина и ширина щелей принимаются по 8-му классу точности;
‒ смежные тарелки должны быть повернуты в горизонтальных плоскостях относительно друг друга на 90°.
Тарелки ситчатые:
‒ прогиб секций полотна не более 2 мм/м диаметра и не более 5 мм на весь диаметр; допускаются местные выпучины в приварных секциях высотой до 8 мм на площади до 15%;
‒ неперпендикулярность сторон сегментов и карманов не более 2 мм по наибольшей стороне.
Тарелки клапанные:
‒ прогиб секций не более 3 мм; допускаются местные выпучины высотой не более 2 мм;
‒ расстояние между отверстиями под клапаны выполняется с допуском ±1 мм;
‒ клапаны, установленные в отверстия секций, должны свободно перемещаться до упора;
‒ масса клапанов может различаться не более чем на ± 2 г. При сборке тарелок необходимо выдерживать требуемые допуски на горизонтальность, т.к. отклонения от горизонтальности полотен приводят к неравномерному барботажу пара по площади тарелки и снижению эффективности ее работы. Допускаемые отклонения от горизонтальности полотна для большинства тарелок составляют: Ah <0,001Z)B, но не более 5 мм, где De ‒ внутренний диаметр аппарата. Допуск на расстояние между тарелками составляет ±3 мм.
Горизонтальность полотен тарелок контролируется с помощью уровней (гидроуровней) и достигается изменением толщины прокладок между секциями полотна и опорными элементами тарелки (опорные кольцо, балки). Контроль горизонтальности колпачковых тарелок можно производить путем налива воды при закрытых сточных отверстиях.
В отдельных случаях тарелки проверяют на барботаж. При пробе тарелки на барботаж часть колонны, находящуюся ниже испытуемой тарелки, плотно закрывают и подключают к ней временный воздухопровод от воздуходувки или магистрали сжатого воздуха. Воду на тарелку подают по стояку паротуше-ния или специально проложенному для этой цели временномуводопроводу. При качественной сборке пузырьки барботируемого воздуха равномерно распределяются по площади тарелки.
При недопустимом местном или общем износе стенок корпуса аппарата заменяют его отдельные части или корпус в целом. При замене верхних изношенных поясов корпуса верхнюю часть аппарата отрезают, демонтируют и заменяют новой. Замена средних поясов корпуса значительно сложней: сначала отрезают и демонтируют верхнюю неповрежденную часть корпуса, затем ‒ среднюю поврежденную часть, после чего поднимают заранее подготовленную новую часть корпуса и стыкуют ее с нижней неповрежденной частью. После этого устанавливают на место верхнюю, ранее демонтированную часть корпуса. Грузоподъемные средства (мачты или краны) освобождают после заварки стыков. Однако, учитывая высокую трудоемкость подобных замен, часто более целесообразно проводить замену всего корпуса аппарата.
При местном износе корпуса, например, зоны питания аппарата, замену дефектных поясов производят, поддерживая верхнюю часть колонны с помощью временных стоек (рисунок 1) [1].
Временные стойки изготавливают из труб, швеллеров, двутавров и устанавливают снаружи или внутри корпуса. Расчет на прочность проводят по условию равенства сопротивления вырезанного сечения обечайки сопротивлению временных стоек.

а ‒ внутренними стойками; б ‒ наружными стойками; в ‒ схема крепления стойки: 1 ‒ опорная лапа; 2 ‒ стойка
Рисунок 1 ‒ Усиление корпуса аппарата в месте вырезаемых поясов
При замене обечаек корпуса и днищ аппарата руководствуются следующими требованиями:
‒ все швы должны быть только стыковыми;
‒ кромки свариваемых листов необходимо зачищать до чистого металла на ширину не менее 10 мм;
‒ продольные швы стыкуемых обечаек, а также меридиональные швы днищ должны быть смещены один по отношению к другому на величину трехкратной толщины более толстого листа, но не менее чем на 100 мм между осями швов;
‒ если разница в толщине стыкуемых листов превышает 5 мм или более 30% толщины тонкого листа, то необходимо предусмотреть плавное утонение толстого листа под углом не более 15°;
‒ ширина листов обечайки между продольными швами должна быть не менее 800 мм, а ширина замыкающей вставки ‒ не менее 400 мм; обечайки диаметром до 500 мм выполняют с одним продольным швом;
‒ смещение кромок на должно превышать в продольных швах 10% толщины тонкого листа, но не более 3 мм; в кольцевых швах при толщине листов до 20 мм ‒ 10% плюс 1 мм, а при толщине более 20 мм ‒ 15%, но не более 5 мм; в соединениях из биметалла ‒ 10%, но не более 3 мм стороны основного слоя и не более 50% толщины плакирующего слоя;
‒ совместный увод кромок (угловатость) в швах должен быть не более 10% толщины листа плюс 3 мм , но не более 5 мм. После сварки аппараты и их элементы подвергают термообработке в случаях, если:
‒ толщина стенки корпуса 5 > 36 мм или S> 0,009 (DB + 1200) мм, где DB ‒ внутренний диаметр корпуса, мм;
‒ корпус изготовлен из хромистой, хромомолибденовой или хромованадиевольфрамовой стали или из биметалла с основным слоем из этих сталей;
‒ среда в аппарате вызывает коррозионное растрескивание металла (раствор едкого натра, едкого кали и др.);
‒ днища или иные штампованные элементы из сталей 09Г2С или 10Г2С1 работают при температурах от минус 41 до минус 70°С;
‒ корпуса, изготовленные из хромоникелевых аустенитных сталей (12Х18Н10Т и др.) и работающие при температурах выше 350°С в средах, вызывающих межкристаллитную коррозию, необходимо подвергать стабилизирующему отжигу.
Термообработку проводят с помощью индукторов (токами промышленной и высокой частоты), электронагревателей, газовых горелок. На рисунке 2 представлено нагревательное устройство с беспламенными панельными горелками, которое можно также использовать для предварительного и сопутствующего подогрева при проведении сварочных работ.
Беспламенные панельные горелки 4 располагают на расстоянии 100 ‒ 150 мм от корпуса аппарата 1, закрепляют в разъемном кольцевом каркасе 2, который состоит из трех сегментов, собираемых на корпусе аппарата на фланцевых соединениях 5. Кольцевой газовый коллектор 7 собирается из трех секций на муфтах 9.
В завершение ремонтных работ люки аппарата закрывают, проводят испытание на прочность и плотность и восстанавливают теплоизоляцию аппарата.

1 ‒ корпус аппарата; 2 ‒ каркас нагревателя; 3 ‒ теплоотражательный
щиток; 4 ‒ беспламенная панельная горелка; 5‒ фланцевое соединение каркаса; 6 ‒ шланг подачи газа к горелке; 7 ‒ газовый коллектор; 8 ‒ шланг
подачи газа к коллектору; 9 ‒ соединительная муфта коллектора
Рисунок 2 ‒ Нагревательное устройство для местной термообработки
Повышение внутреннего давления при пуске аппаратов рекомендуется производить поэтапно, увеличивая его на 0,25 от рабочего давления с выдержками по пятнадцать минут. Рекомендуемая скорость повышения или снижения температуры не более 30 0С/ч. При пуске аппаратов в зимних условиях рекомендуется предварительно прогреть их паром и только после прогрева поднимать в них давление. Если предварительный прогрев аппарата не представляется возможным, то пуск выполняют в соответствии с «Регламентом проведения в зимнее время пуска, остановки и испытания на плотность аппаратуры», который устанавливает для данной марки стали наименьшую температуру и соответствующее ей давление, допускаемые при пуске.
Виды, устройство и принцип работы задвижек
Основное назначение запорной арматуры ‒ перекрывать поток рабочей среды по трубопроводу и снова пускать среду в зависимости от требований технологического процесса, обслуживаемого данным трубопроводом.
Задвижками называются запорные устройства, в которых проходное сечение перекрывается поступательным перемещением затвора в направлении, перпендикулярном направлению движения транспортируемой среды [4, 5].
В сравнении с другими видами арматуры задвижки имеют следующие преимущества: незначительное гидравлическое сопротивление при полностью открытом проходе, отсутствие поворотов потока перекачиваемой жидкости, простота обслуживания, относительно небольшая строительная длина. Задвижки с диаметром условного прохода более 300.. .400 мм имеют габаритные размеры, массу и стоимость меньше, чем краны.
Конструктивно (рисунок 3) задвижка представляет собой цельный литой или сварной корпус, снабженный двумя патрубками для присоединения к трубопроводу (с помощью фланцев или сварки) и шпиндель соединительный с запорным элементом и управляемый с помощью маховика или специального привода. Место выхода шпинделя из корпуса герметизируется с помощью сальникового уплотнения.

1 ‒ корпус; 2 ‒ седло; 3 ‒ направляющая движения клина; 4 ‒ клин;
5 ‒ шпиндель; 6 ‒ верхняя крышка; 7‒ шпилька; 8 ‒ уплотнительная
прокладка; 9 ‒ направляющая втулка; 10 ‒ сальник; 11 ‒натяжной фланец;
12 ‒ бугель; 13 ‒ гайка; 14 ‒ маховик
Рисунок 3 ‒ Полнопроходная задвижка с цельным клином
По конструкции уплотнительного затвора задвижки делятся на клиновые и параллельные.
По площади прохода задвижки могут быть полнопроходными (диаметры прохода задвижки и трубопровода равны) и с суженным проходом.
Различают также задвижки с выдвижным шпинделем (ходовая гайка расположена вне рабочей полости задвижки, а шпиндель совершает поступательное движение) и с невыдвижным шпинделем (ходовая гайка расположена непосредственно на затворе, в результате чего шпиндель совершает только вращательное движение).
К клиновым (рисунок 4) относятся задвижки, затвор которых имеет вид плоского клина. При закрытии задвижки этот клин опускается и плотно прилегает к уплотнительным поверхностям седел, расположенных под тем же углом, что и плоскости клина. Клиновые задвижки относительно легко закрываются и открываются. Однако для них характерен повышенный износ уплотнительных поверхностей затвора. Кроме того, имеются технологические трудности получения герметичности в затворе.
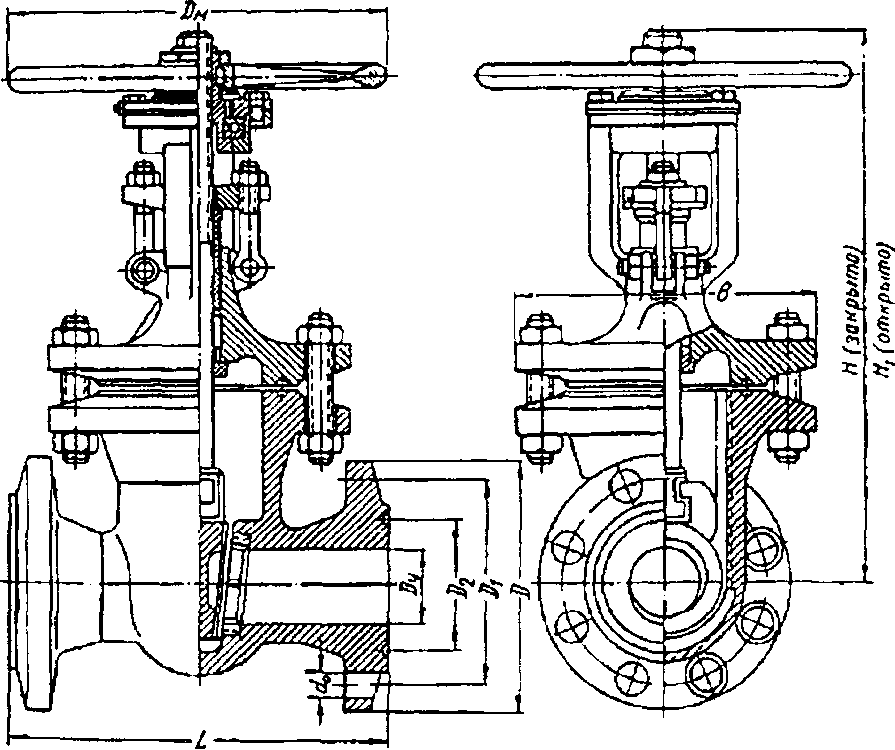
Рисунок 4 ‒ Задвижка клиновая стальная фланцевая серии ЗКЛ2
В параллельных задвижках уплотнительные поверхности седел параллельны друг другу и расположены перпендикулярно к направлению потока перекачивающей жидкости. Затвор в параллельных задвижках обычно называют диском, шибером или ножом.
Достоинствами параллельных задвижек являются простота изготовления затвора, легкость сборки и ремонта, отсутствие заедания затвора в полностью закрытом положении.
Недостаток задвижек данной конструкции заключается в большом расходе энергии на закрывание и открывание, что обусловлено трением между уплотнительными поверхностями седел затвора на всем пути движения.
Технологический раздел
2.1 Технические и технологические характеристики основного оборудования блока ректификации фракций Н.К. 80 0С (ДИП) абсорбционно-газофракционирующей установки (АГФУ)
К основным аппаратам газофракционирующих установок следует отнести ректификационные колонны и абсорберы с необходимым дополнительным оборудованием: конденсаторами, емкостями, подогревателями и холодильниками. И те и другие в конструктивном оформлении имеют много общего [1].
Для разделения смеси газов, рефлюксов, бензинов на составляющие компоненты на установке АГФУ‒1 используется процесс ректификации – многократного испарения и конденсации компонентов смеси в колоннах непрерывного действия тарелочного типа.
В зависимости от числа получаемых продуктов при разделении многокомпонентных смесей на АГФУ‒1 используются колонны К‒6,К‒7, ‒8, К‒40, К‒41 с получением двух нефтепродуктов и ректификационная колонна К‒10 с получением трех нефтепродуктов.
В каждой колонне имеется отпарная секция, расположенная ниже ввода сырья – тарелки питания. Целевым продуктом отпарной секции является жидкий кубовый остаток. Концентрационная секция расположена в колоннах над тарелкой питания.
Целевым продуктом концентрационной секции К‒10 являются пары ректификата – верхний нефтепродукт.
Для обеспечения нормальной работы ректификационных колонн обязательна подача орошения наверх колонны с выводом и конденсацией верхнего нефтепродукта. В низ колонн подводится тепло через рибойлеры у К‒6, К‒7, К‒8, К‒40, К‒41 или посредством «горячей струи кубового продукта через печи П‒2, П‒3 у К‒10.
Тарельчатая ректификационная колонна представлена на рисунке 5 [5].

1 – опорная обечайка; 2 – днище; 3 – вертикальный корпус;
4 – крышка; 5 – отбойное устройство; 6 – тарелки; 7 – устройство для ввода сырья
Рисунок 5 – Тарельчатая ректификационная колонна
Тарельчатые колонны состоят, как правило, из вертикального корпуса 3, сферической или эллиптической крышки 4, днища 2 и жестко скрепленной с корпусом опорной обечайки 1 цилиндрической или конической формы. Использование конических опор для высоких колонн небольшого диаметра способствует повышению их устойчивости и уменьшению нагрузки на опорную поверхность фундаментного кольца. Внутри корпуса колонны смонтированы тарелки 6, устройство 7 для ввода сырья, отбойное устройство 5 и штуцеры для жидкости и пара [4, 5].
Известно, что затраты при ректификации определяются преимущественно флегмовым числом и числом тарелок в колонне. Для близкокипящих компонентов с малой относительной летучестью эти параметры особенно велики. Поэтому из общих капитальных и эксплуатационных затрат на газофракционирование существенная часть приходится на разделение фракций i–С4–н–С4 и i–C5–н–С5. В этой связи на НПЗ часто ограничиваются фракционированием предельных газов без разделения фракций С4 и выше.
Технические характеристики колонны деизобутанизатор К‒8 представлены в таблице 1.
Таблица 1 ‒ Технические характеристики колонны деизобутанизатора К‒8
Наименование оборудования (тип, наименование аппарата, назначение и т.д.)
|
Номер
позиции по
схеме,
индекс
|
Коли‒чество, шт.
|
Материал
| Методы
защиты
металла
обору‒дования от коррозии
|
Технологическая
характеристика
|
Колонна
|
К‒8
|
|
Корпус: 09Г2С‒15
Днище:
09Г2С‒15
|
наружная грунтовка и покраска
| Н = 67396 мм
Д = 2800 мм
V = 750,5 м3
110 трапецевидно‒клапанных тарелок
Ррасч. = 9,9 кгс/см2
Трасч. стенки =100 0С
| | | | | | | | | | |
Одним из основных факторов, определяющих качество получаемых продуктов на ГФУ, является правильный выбор способа контакта и его конструктивного оформления. В промышленности применяют различные виды ректификационных тарелок, что объясняется многообразием технологических задач и индивидуальностью химических процессов. Контактные устройства должны обеспечивать интенсивный тепло– и массообмен паровой и жидкой фаз, иметь невысокие и одинаковые по площади гидравлические сопротивления. В технологии газоразделения получили распространение колпачковые тарелки с круглыми колпачками, желобчатые и с S–образными элементами, клапанные, ситчатые, струйные и решетчатые провального типа и др.
В зависимости от внутреннего устройства, обеспечивающего контакт между восходящими парами и нисходящей жидкостью, на установке АГФУ‒1 используются ректификационные колонны с трапециевидно‒клапанными и центробежными тарелками – в К‒6,трапециевидно‒клапанными тарелками – в К‒7, клапанными тарелками в К‒8, К‒40, К‒41 и трапециевидно‒ клапанными тарелками – в К‒10.
Клапанные тарелки широко применяют в нефтехимической промышленности. Основные их преимущества – способность обеспечить эффективный массообмен в большом интервале рабочих нагрузок, несложность конструкции, низкая металлоемкость и невысокая стоимость [5, 6].
Клапанные тарелки изготовляют с дисковыми и прямоугольными клапанами, тарелки работают в режиме прямоточного или перекрестного движения фаз. В отечественной промышленности наиболее распространены клапанные прямоточные тарелки с дисковыми клапанами. На клапанной прямоточной тарелке в шахматном порядке расположены отверстия, в которых установлены саморегулирующиеся дисковые клапаны диаметром 50 мм, способные подниматься при движении пара (газа) на высоту до 6 – 8 мм.
Дисковый клапан снабжен тремя направляющими, расположенными в плане под углом 45°, две из этих направляющих имеют большую длину. На диске клапана штамповкой выполнены специальные упоры, обеспечивающие начальный зазор между диском и тарелкой, что исключает возможность прилипания клапана к тарелке (рисунок 6, положение I).
При небольшой производительности по пару поднимается легкая часть клапана (рисунок 6, положение II) и пар выходит через щель между клапаном и полотном тарелки в направлении, противоположном направлению движения жидкости по тарелке. С увеличением скорости пара клапан поднимается и зависает над тарелкой (рисунок 6, положение III), a пар барботирует в жидкость через кольцевую щель под клапаном. При дальнейшем росте производительности по пару клапан занимает положение, при котором пар выходит в направлении движения жидкости, уменьшая разность уровней жидкости на тарелке (рисунок 6, положение IV). При этом короткая направляющая фиксируется в специальном вырезе на кромке отверстия, обеспечивая заданное положение клапана при его подъеме.

Рисунок 6 – Клапанно – прямоточная тарелка
Эффективность клапанных прямоточных тарелок (КПД) составляет 0,70 – 0,85, F < 2,5 (м/с)(кг/м3)‒0,5, диапазон устойчивой работы 3,5. В области саморегулируемой работы тарелки обладают относительно небольшим гидравлическим сопротивлением.
Не нашли, что искали? Воспользуйтесь поиском по сайту:
©2015 - 2024 stydopedia.ru Все материалы защищены законодательством РФ.
|